GH4708鎳基高溫合金抗高溫耐磨涂層的防護方法
一種GH4708鎳基高溫合金抗高溫耐磨涂層的防護方法(57)摘要本技術(shù)屬于熱處理領(lǐng)域,特別是涉及一種GH4708鎳基高溫合金抗高溫耐磨涂層的防護方法。按照以下步驟進行:滲劑焙燒→滲劑配置→零件清洗→裝包→滲鋁→出爐→拆包→零件清理→檢驗;其中,滲鋁前GH4708鎳基高溫合金經(jīng)1140℃±20℃×0.5~2h,空冷固溶,然后加工成零件滲鋁,滲鋁后再經(jīng)800℃±20℃×10~20h,空冷時效。本發(fā)明方法能夠滿足發(fā)動機低壓渦輪嵌入件、軸的設(shè)計制造要求,滲鋁層深度為0.03mm~0.08mm,表層生成了富鋁的NiAl相,表面硬度顯微硬度大于700HV,大大提高了GH4708鎳基高溫合金的抗氧化性能和耐磨性能。
一種GH4708鎳基高溫合金抗高溫耐磨涂層的防護方法,其特征在于,按照以下步驟進行:滲劑焙燒→滲劑配置→零件清洗→裝包→滲鋁→出爐→拆包→零件清理→檢驗;其中,滲鋁前GH4708鎳基高溫合金經(jīng)1140℃±20℃×0.5~2h,空冷固溶,然后加工成零件滲鋁,滲鋁后再經(jīng)800℃±20℃×10~20h,空冷時效。
2.按照權(quán)利要求1所述的GH4708鎳基高溫合金抗高溫耐磨涂層的防護方法,其特征在于,滲劑由含鐵量42wt%~50wt%的鋁鐵粉和氯化銨粉末配置而成,其中:按重量百分比計,鋁鐵合金粉末占98.5~99.0%,氯化銨粉末占1.0~1.5%。
3.按照權(quán)利要求1所述的GH4708鎳基高溫合金抗高溫耐磨涂層的防護方法,其特征在于,在GH4708鎳基高溫合金表面制備出符合設(shè)計要求滲鋁層0.03mm~0.08mm的抗高溫耐磨防護涂層;抗高溫耐磨防護涂層為外層和擴散層組成,其中:外層0.025mm~0.50mm,擴散層0.010mm~0.030mm。
4.按照權(quán)利要求1所述的GH4708鎳基高溫合金抗高溫耐磨涂層的防護方法,其特征在于,滲劑焙燒時,將鋁鐵合金粉末與氯化銨粉末混合均勻,將混合物裝入滲鋁包中于950℃±20℃保溫5h~10h。
5.按照權(quán)利要求1所述的GH4708鎳基高溫合金抗高溫耐磨涂層的防護方法,其特征在于,滲鋁時,將裝有零件的滲鋁包在450℃±20℃的溫度下保溫2h~4h,隨爐升溫到900℃~950℃溫度保溫5~10h滲鋁;滲鋁保溫結(jié)束后,將滲鋁包取出于空氣中冷卻。
GH4708鎳基高溫合金抗高溫耐磨涂層的防護方法技術(shù)領(lǐng)域
[0001]本技術(shù)屬于熱處理領(lǐng)域,特別是涉及一種GH4708鎳基高溫合金抗高溫耐磨涂層的防護方法。背景技術(shù)
[0002]GH4708鎳基高溫合金在950℃以下可以長期使用,是航空發(fā)動機的常用材料,用于制造壓氣機、燃燒室、渦輪、可調(diào)噴口內(nèi)的易產(chǎn)生磨損的承力件,如低壓渦輪嵌入件、軸等。這些承力件工作溫度為700℃~850℃,工作環(huán)境惡劣,易磨損,所以要求這些零件不僅有良好抗高溫氧化性能,而且還要有良好的耐磨性能。
[0003]耐磨涂層的制備方法有很多,如:氣體滲碳、氮化、熱噴涂碳化鎢、電鍍鉻等。滲碳是將低碳鋼工件放在增碳的活性介質(zhì)中,加熱、保溫,使碳原子滲入鋼件表面,并向內(nèi)部擴散形成一定碳濃度梯度的滲層。
氮化是一種以氮原子滲入鋼件表面,形成一層以氮化物為主的滲層方法。氮化、滲碳主要用于鋼件,氮化工藝長,使用溫度低。
熱噴涂涂層是熱噴涂材料經(jīng)熱源加熱至熔化或半熔化態(tài),用高壓氣流令其霧化并噴射于工件上,從而形成涂層的一種表面加工方法。
涂層與基體是物理結(jié)合,使用過程中易產(chǎn)生掉塊現(xiàn)象,不適用合噴涂大批量的小零件。
電鍍是一種電化學(xué)過程,也是一種氧化還原過程,將金屬制件作為陰極、所鍍金屬或合金作為陽極,分別掛于銅或黃銅制的極棒上而浸入含有鍍層成分的電解液中,并通入直流,在零件上就會沉積出金屬鍍鎳層。
電鍍鉻層后續(xù)需要加工,工序復(fù)雜,且也為物理結(jié)合。
[0004]為了找到一種能夠在鎳基高溫合金表面制備抗高溫耐磨涂層的防護方法,本發(fā)明的目的在于提供一種GH4708鎳基高溫合金抗高溫耐磨涂層的防護方法,采用粉末包埋法在GH4708鎳基高溫合金上制備鋁化物滲層的方法,滿足發(fā)動機零件使用要求。
[0005]本發(fā)明的技術(shù)方案是:
[0006]一種GH4708鎳基高溫合金抗高溫耐磨涂層的防護方法,按照以下步驟進行:滲劑焙燒→滲劑配置→零件清洗→裝包→滲鋁→出爐→拆包→零件清理→檢驗;其中,滲鋁前GH4708鎳基高溫合金經(jīng)1140℃±20℃×0.5~2h,空冷固溶,然后加工成零件滲鋁,滲鋁后再經(jīng)800℃±20℃×10~20h,空冷時效。
[0007]所述的GH4708鎳基高溫合金抗高溫耐磨涂層的防護方法,滲劑由含鐵量42wt%~50wt%的鋁鐵粉和氯化銨粉末配置而成,其中:按重量百分比計,鋁鐵合金粉末占98.5~99.0%,氯化銨粉末占1.0~1.5%。
[0008]所述的GH4708鎳基高溫合金抗高溫耐磨涂層的防護方法,在GH4708鎳基高溫合金表面制備出符合設(shè)計要求滲鋁層0.03mm~0.08mm的抗高溫耐磨防護涂層;抗高溫耐磨防護涂層為外層和擴散層組成,其中:外層0.025mm~0.50mm,擴散層0.010mm~0.030mm。
[0009]所述的GH4708鎳基高溫合金抗高溫耐磨涂層的防護方法,滲劑焙燒時,將鋁鐵合金粉末與氯化銨粉末混合均勻,將混合物裝入滲鋁包中于950℃±20℃保溫5h~10h。
[0010]所述的GH4708鎳基高溫合金抗高溫耐磨涂層的防護方法,滲鋁時,將裝有零件的滲鋁包在450℃±20℃的溫度下保溫2h~4h,隨爐升溫到900℃~950℃溫度保溫5~10h滲鋁;滲鋁保溫結(jié)束后,將滲鋁包取出于空氣中冷卻。
[0011]本發(fā)明的優(yōu)點及有益效果是:
[0012]1、航空發(fā)動機的壓氣機、燃燒室、渦輪、可調(diào)噴口等不同部位的零件根據(jù)結(jié)構(gòu)特點和工作環(huán)境要求,零件表面不僅要有一定的耐磨性,而且零件還要耐高溫氧化,所以為了提高零件表面的抗氧化和抗腐蝕性能及耐磨性能,通常在表面施加防護涂層,即在零件表面制備與基體冶金結(jié)合的滲鋁層,這樣不僅可以提高零件的抗氧化、抗腐蝕性能,同時能夠起到一定的耐磨作用,從而提升零件的可靠性和延長使用壽命。
[0013]2、本發(fā)明方法能夠顯著提高GH4708鎳基高溫合金的抗氧化、抗腐蝕性能和增加耐磨性能,特別適用于長期工作在高溫、耐腐蝕環(huán)境下有磨擦產(chǎn)生的零件。該方法已經(jīng)成功應(yīng)用于航空發(fā)動機球形接頭、軸、低壓渦輪嵌入件的研制、生產(chǎn),也可推廣到航空發(fā)動機其他部件和其他燃氣渦輪發(fā)動機的零件上,具有廣泛的應(yīng)用價值。
[0014]3、本發(fā)明方法能夠滿足發(fā)動機低壓渦輪嵌入件、軸的設(shè)計制造要求,滲鋁層深度為0.03mm~0.08mm,表層生成了富鋁的NiAl相,表面硬度顯微硬度大于700HV,大大提高了GH4708鎳基高溫合金的抗氧化性能和耐磨性能。
[0015]圖1為920℃滲鋁滲層組織圖。
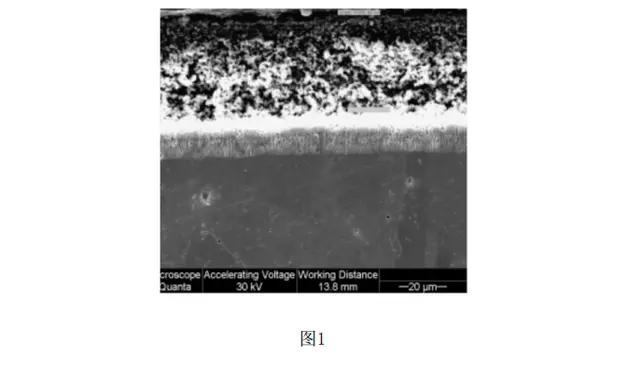
[0016]圖2為920℃滲鋁滲層成分分布圖;其中,(a)滲鋁滲層組織;(b)Ni;(c)Cr;(d)Al;(e)Ti;(f)Mo;(g)W;(h)O。
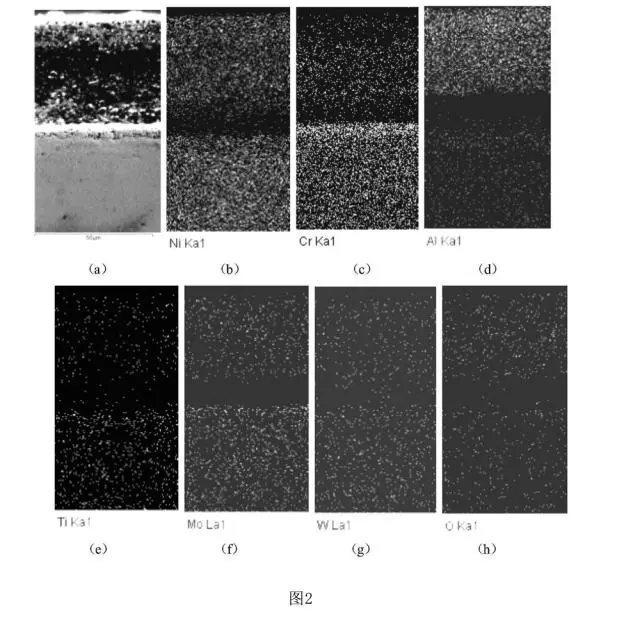
[0017]圖3(a)-圖3(b)為GH4708合金標準熱處理的基體晶粒組織圖;其中,圖3(b)是圖3(a)的放大圖。
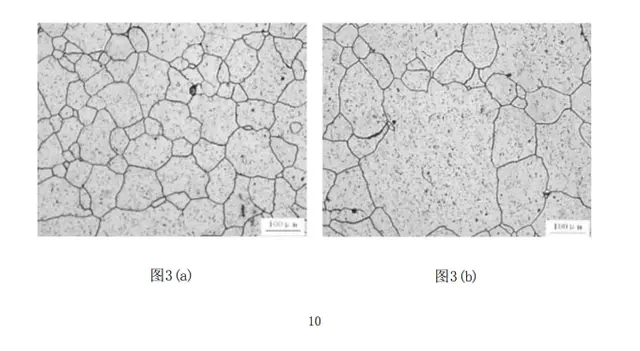
[0018]圖4為GH4708合金920℃滲鋁后的基體晶粒組織圖。
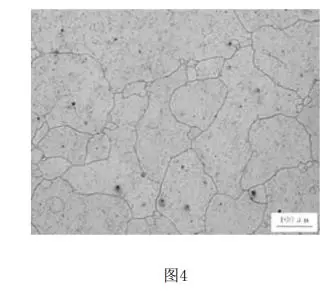
[0019]圖5為GH4708合金標準熱處理后的基體顯微組織圖。
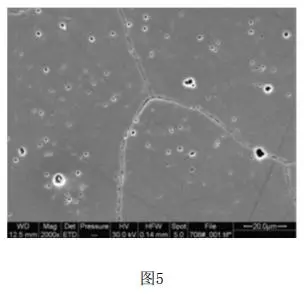
[0020]圖6為GH4708合金920℃滲鋁后的基體顯微組織圖。
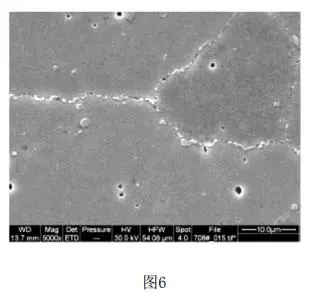
[0021]圖7為950℃滲鋁滲層組織圖。
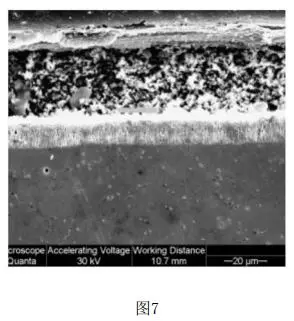
[0022]圖8為950℃滲鋁滲層成分分布圖;其中,(a)滲鋁滲層組織;(b)Ni;(c)Cr;(d)Al;(e)Ti;(f)Mo;(g)W;(h)O。
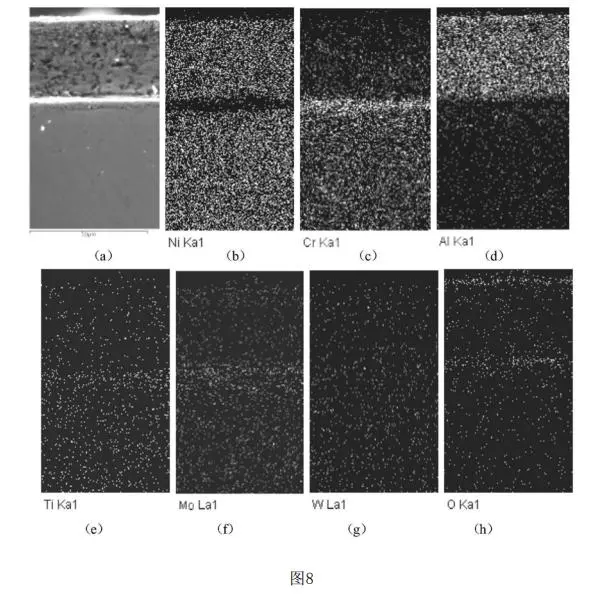
[0023]圖9為GH4708合金滲鋁后的基體晶粒組織圖。
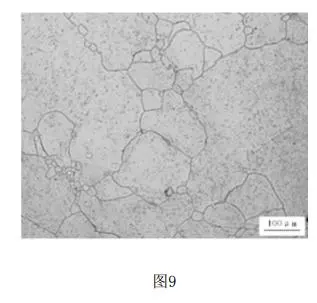
[0024]圖10為GH4708合金滲鋁后的基體顯微組織圖。具體實施方式
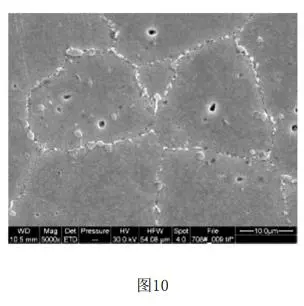
[0025]在具體實施過程中,本發(fā)明GH4708鎳基高溫合金滲鋁的工藝方法,按照以下步驟進行:滲劑焙燒→滲劑配置→零件清洗→裝包→滲鋁→出爐→拆包→零件清理→檢驗。
[0026]所述材料為GH4708鎳基高溫合金棒材,滲鋁前經(jīng)1140℃±20℃×0.5~2h,空冷固溶,然后加工成零件滲鋁,滲鋁后再經(jīng)800℃±20℃×10~20h,空冷時效。滲劑由含鐵量42wt%~50wt%的鋁鐵粉和符合GB658-1988的氯化銨粉末配置而成,其中:按重量百分比計,鋁鐵合金粉末占98.5~99.0%,氯化銨粉末占1.0~1.5%。采用高溫滑底爐制備滲鋁層,用掃描電鏡、拉力試驗機等設(shè)備進行組織、性能分析測試。
[0027]為了摸索滲鋁層對基體組織性能的影響,及滲鋁溫度、滲鋁時間對滲鋁層深度和組織的影響,制定了6種不同的工藝試驗方案,950℃×3h、5h、8h,920℃×8h、10h、12h。滲鋁后對所有滲鋁方案金相試片的滲鋁層進行組織形貌與深度分析,最終從兩種溫度中各取一組符合滲鋁層要求的兩組試棒,分別加工成室溫拉伸試樣、高溫瞬時試樣、高溫持久試樣,進行力學(xué)性能試驗。利用拉力試驗機分析滲鋁前后試棒的室溫力學(xué)性能、高溫瞬時和持久性能進行測試。最終在GH4708鎳基高溫合金表面制備出符合設(shè)計要求滲鋁層0.03mm~0.08mm的抗高溫耐磨防護涂層,其中外層0.025mm~0.50mm,擴散層0.010mm~0.030mm。
[0028]下面,通過實施例對本發(fā)明進一步詳細闡述。
[0029]實施例1:
[0030]本實施例中,GH4708鎳基高溫合金抗高溫耐磨涂層的防護方法,具體步驟如下:
[0031](1)材料:GH4708,成分見表1,滲鋁前經(jīng)1140℃×1h,空冷固溶,滲鋁后再經(jīng)800℃×15h,空冷時效。
[0032]表1 GH4708化學(xué)成分(wt%)

[0034](2)滲鋁
[0035]滲劑配置:滲鋁劑由含鐵量42wt%的鋁鐵合金粉末與GB658-1988的氯化銨粉末混合配成。其中,按重量百分比計,鋁鐵合金粉末占99.0%,氯化銨粉末占1.0%。[0036]滲劑焙燒:焙燒鋁鐵合金粉末時,加入干燥的氯化銨粉末,混合均勻。將混合物裝入滲鋁包中于950℃±20℃保溫5h~10h。
[0037]滲鋁:將裝有零件的滲鋁包在450℃±20℃的溫度下保溫2h~4h,隨爐升溫到920℃溫度保溫8h滲鋁。滲鋁保溫結(jié)束后,將滲鋁包取出于空氣中冷卻。
[0038](3)滲鋁工藝對滲鋁層深度和組織的影響
[0039]滲鋁工藝實施滲鋁工藝后,對試樣進行研磨、拋光和腐蝕后,在金相顯微鏡下觀察滲鋁層深度,滲鋁層深度0.057mm~0.059mm。滲層截面形貌如圖1所示,從圖1可以看出滲層分布連續(xù),分為兩層,即約0.041mm的外層和約0.017mm的擴散層,靠近滲層的影響區(qū)內(nèi)晶界上碳化物很少。
[0040]在掃描電子顯微鏡下采用背散射對未經(jīng)腐蝕的滲層形貌進行觀察,并采用二次電子及元素面掃描對兩種方案得到的滲層及附近區(qū)域合金成分分布進行分析,如圖2所示。對滲層進行合金元素面掃描發(fā)現(xiàn),兩種工藝所得滲層成分分布基本相同,即由表面向基體內(nèi),成分變化比較明顯的是Al、Cr與Ni元素。
[0041]滲鋁時,滲劑分解形成Al原子,吸附在試片表面,通過擴散進入試片基體表面,由 于試片表面Al原子濃度增高,Al原子由外向內(nèi)擴散,所以最外層Al含量較高,隨滲層厚度的增加,Al含量逐漸降低,直到與基體中的Al含量相同。另外,因為試片表面Ni原子與Al原子形成了NiAl相,原基體中的Cr、W等元素在NiAl中溶解度較低,在擴散層中可能以α-Cr、α-W相等形式存在,而過渡層中的Cr、W、Ti等碳化物形成元素可能形成碳化物存在于過渡層中。因此,滲層組織由表及里分別為:表層主要為富鋁的NiAl相,向內(nèi)的過渡層和擴散層為富Cr相、碳化物、NiAl相和Ni3Al相等。
[0042](4)滲鋁工藝對基體組織和性能的影響
[0043]經(jīng)過標準熱處理后的GH4708合金基體,其晶粒組織很不均勻,大晶粒達到了ASTM No.3級,小晶粒為ASTM No.5-6級,且大小晶粒的分布沒有規(guī)律,在大晶粒區(qū),大晶粒的周圍存在一些細晶,見圖3(a)、(b)。滲Al工藝處理后的基體晶粒組織見圖4??梢钥闯觯c標準熱處理后的基體組織相比,滲Al工藝處理后合金的晶粒有所長大,晶粒大小也是很不均勻,平均在ASTM No.2-3級。
[0044]在高倍下進一步觀察,晶內(nèi)碳化物大體有兩種形貌,一種是不規(guī)則的大塊狀,數(shù)量較少;另一種是分布比較均勻的細小的球狀。在晶界上有細小碳化物呈鏈狀析出,標準熱處理如圖5所示。經(jīng)過滲Al工藝處理后,碳化物在晶界聚集長大并呈顆粒狀,見圖6。
[0045](5)滲鋁工藝對基體性能的影響
[0046]GH4708合金棒材標準熱處理后的基體力學(xué)性能和滲鋁后的力學(xué)性能試驗結(jié)果見表2。
[0047]表2 GH4708合金標準熱處理的基體和滲Al后棒材的拉伸和持久性能
[0048]
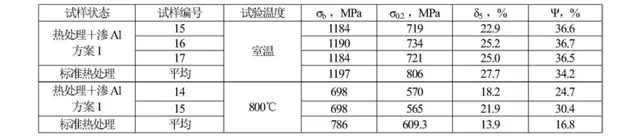
[0049]

[0050]滲Al后的室溫拉伸強度稍有下降,延伸率比滲Al前降低約12%,面縮率有所提高。滲Al后的800℃拉伸強度有所下降,延伸率和斷面收縮率都大幅度提高,分別提高約47%和65%。滲Al后的800℃持久壽命比滲前降低60%左右。
[0051]實施例2:
[0052]與實施例1不同之處在于,本實施例中,GH4708鎳基高溫合金抗高溫耐磨涂層的防護方法,具體步驟如下:
[0053](1)材料:GH4708,成分見表1,滲鋁前經(jīng)1140℃×1h,空冷固溶,滲鋁后再經(jīng)800℃×15h,空冷時效。
[0054](2)滲鋁
[0055]滲劑配置:滲鋁劑由含鐵量50wt%的鋁鐵合金粉末與GB658-1988的氯化銨粉末混合配成。其中,按重量百分比計,鋁鐵合金粉末占98.5%,氯化銨粉末占1.5%。
[0056]滲劑焙燒:焙燒鋁鐵合金粉末時,加入干燥的氯化銨粉末,混合均勻。將混合物裝入滲鋁包中于950℃±20℃保溫5h~10h。
[0057]滲鋁:將裝有零件的滲鋁包在450℃±20℃的溫度下保溫2h~4h,隨爐升溫到950℃溫度保溫5h滲鋁。滲鋁保溫結(jié)束后,將滲鋁包取出于空氣中冷卻。
[0058](3)滲鋁工藝對滲鋁層深度和組織的影響
[0059]滲鋁工藝實施滲鋁工藝后,對試樣進行研磨、拋光和腐蝕后,在金相顯微鏡下觀察滲鋁層深度,滲鋁層深度0.042mm~0.046mm。滲層截面形貌如圖7所示,從圖7可以看出滲層分布連續(xù),分為兩層,即約0.029mm的外層和約0.016mm的擴散層,靠近滲層的影響區(qū)內(nèi)晶界上碳化物很少。
[0060]在掃描電子顯微鏡下采用背散射對未經(jīng)腐蝕的滲層形貌進行觀察,并采用二次電子及元素面掃描對兩種方案得到的滲層及附近區(qū)域合金成分分布進行分析,如圖8所示。對滲層進行合金元素面掃描發(fā)現(xiàn),兩種工藝所得滲層成分分布基本相同,即由表面向基體內(nèi),成分變化比較明顯的是Al、Cr與Ni元素。
[0061]滲鋁時,滲劑分解形成Al原子,吸附在試片表面,通過擴散進入試片基體表面,由于試片表面Al原子濃度增高,Al原子由外向內(nèi)擴散,所以最外層Al含量較高,隨滲層厚度的增加,Al含量逐漸降低,直到與基體中的Al含量相同。另外,因為試片表面Ni原子與Al原子形成了NiAl相,原基體中的Cr、W等元素在NiAl中溶解度較低,在擴散層中可能以α-Cr、α-W相等形式存在,而過渡層中的Cr、W、Ti等碳化物形成元素可能形成碳化物存在于過渡層中。因此,滲層組織由表及里分別為:表層主要為富鋁的NiAl相,向內(nèi)的過渡層和擴散層為富Cr相、碳化物、NiAl相和Ni3Al相等。
[0062](4)滲鋁工藝對基體組織和性能的影響
[0063]經(jīng)過標準熱處理后的GH4708合金基體,其晶粒組織很不均勻,大晶粒達到了ASTM No.3級,小晶粒為ASTM No.5-6級,且大小晶粒的分布沒有規(guī)律,在大晶粒區(qū),大晶粒的周圍存在一些細晶,見圖3(a)、(b)。滲Al工藝處理后的基體晶粒組織見圖9。可以看出,與標準熱處理后的基體組織相比,滲Al工藝處理后合金的晶粒有所長大,晶粒大小也是很不均勻,平均在ASTM No.2-3級。
[0064]如圖10所示,經(jīng)過滲Al工藝處理后,碳化物在晶界聚集長大并呈顆粒狀。碳化物長大更加明顯,其部分在晶界上形成了塊狀。
[0065](5)滲鋁工藝對基體性能的影響
[0066]GH4708合金棒材標準熱處理后的基體力學(xué)性能和滲鋁后的力學(xué)性能試驗結(jié)果見表3。
[0067]表3 GH4708合金標準熱處理的基體和滲Al后棒材的拉伸和持久性能
[0068]
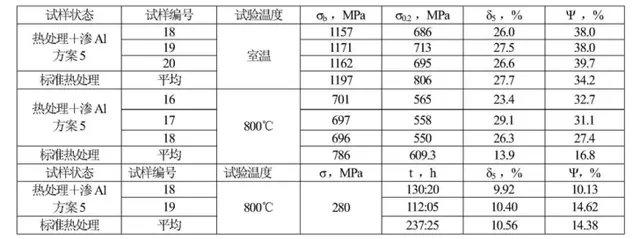
[0069]滲Al后的室溫拉伸強度稍有下降,屈服強度下降近14%,延伸率稍有所降低,面縮率提高約12%。滲Al后的800℃拉伸強度和屈服強度都有所下降,延伸率和斷面收縮率都不同程度的提高,分別提高89%和81%。滲Al后的800℃持久壽命大幅度降低。
[0070]實施例結(jié)果表明,本發(fā)明方法能夠滿足發(fā)動機壓氣機、燃燒室、渦輪、可調(diào)噴口等部分的小耐磨設(shè)計制造要求。粉末包埋法則是將需要涂覆的零件置于容器內(nèi),容器用粉狀混合物填充,在高溫下反應(yīng),方法簡單,涂層與基體冶金結(jié)合,主要是用以制取沒有剝落缺陷的高質(zhì)量均勻涂層。采用粉末包埋法滲鋁防護零件工藝方法簡單、表面效果顯著,單臺創(chuàng)造2萬的經(jīng)濟價值。