天行健咨詢:運(yùn)用六西格瑪降低制造系統(tǒng)造成的停線時(shí)間
停線是制約工廠制造能力的關(guān)鍵瓶頸之一,本例中我們運(yùn)用六西格瑪工具分析了制造系統(tǒng)停線比例,樣本數(shù)據(jù)取處2009年到2013年,通過計(jì)算得到制造系統(tǒng)停線比例的平均值為67.75%(圖1),從數(shù)據(jù)層面驗(yàn)證了運(yùn)營業(yè)務(wù)對(duì)制造系統(tǒng)停線的諸多抱怨。
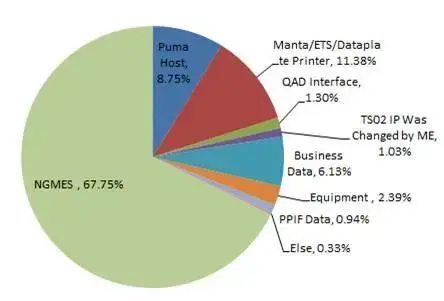
一、分析和改進(jìn)過程
項(xiàng)目團(tuán)隊(duì)結(jié)合數(shù)據(jù)分析結(jié)果和運(yùn)營管理的實(shí)際情況,起草了用戶訪談問題清單,并訪談了十幾位來自不同工廠的業(yè)務(wù)負(fù)責(zé)人,利用六西格瑪工具對(duì)訪談結(jié)果和樣本數(shù)據(jù)進(jìn)行了詳盡的分析和討論(圖2),識(shí)別出停線的主要原因是系統(tǒng)支持流程不完善,進(jìn)而對(duì)系統(tǒng)支持流程做了價(jià)值鏈分析,最終確定改進(jìn)點(diǎn)為建立并系統(tǒng)支持快速相應(yīng)機(jī)制,以及完善快速響應(yīng)機(jī)制下的工具和報(bào)表,并責(zé)成相關(guān)責(zé)任人對(duì)改進(jìn)任務(wù)清單進(jìn)行跟蹤、匯報(bào),直至改進(jìn)任務(wù)全部完成(圖3)。
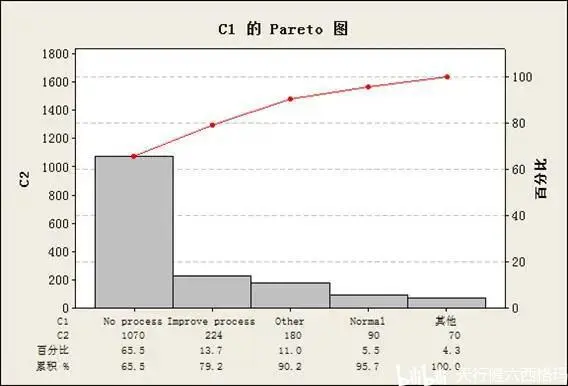
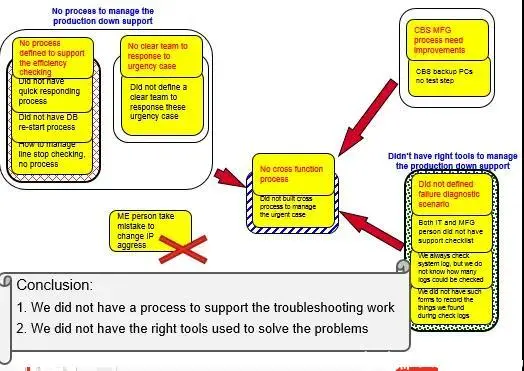
圖2 停線時(shí)間原因分析
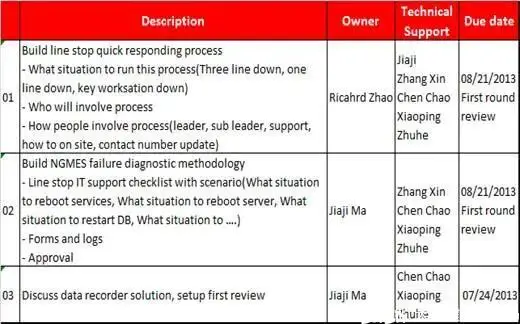
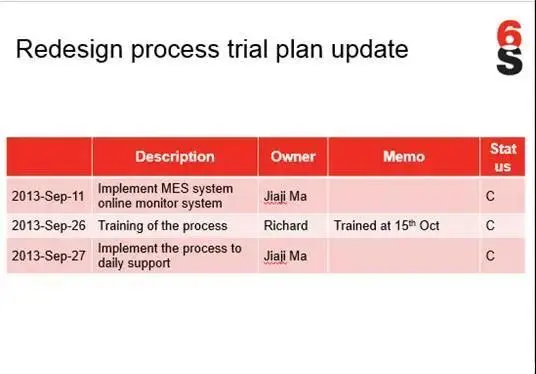
圖3 流程改善任務(wù)跟蹤圖片
二、改進(jìn)措施落實(shí)和監(jiān)控
整體改變計(jì)劃于九月底全部落實(shí)到位,十二月底,項(xiàng)目團(tuán)隊(duì)抽取改進(jìn)后三個(gè)月的數(shù)據(jù)(10-12月)等閑時(shí)進(jìn)行分析,得到制造系統(tǒng)停線比例為44%(圖4),雖然距離業(yè)務(wù)要求還有差距,但改進(jìn)措施明顯已經(jīng)發(fā)揮了作用,停線比例減少了23%,接下來就是持續(xù)加大對(duì)流程的培訓(xùn)和執(zhí)行效率的管理,力爭達(dá)到停線比例降低27%的總體要求。
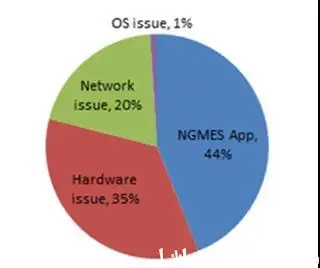
圖4 改善后結(jié)果跟蹤
三、經(jīng)驗(yàn)分享
從商業(yè)機(jī)密方面考慮,該項(xiàng)目沒有直接計(jì)算由停線引起的經(jīng)濟(jì)損失,但仍然有相當(dāng)?shù)慕梃b意義,六西格瑪理論看似復(fù)雜、繁瑣,大家在使用過程中最大的困惑之上就是改進(jìn)難以落實(shí)到具體數(shù)據(jù)指標(biāo)上來。其實(shí),只要堅(jiān)持運(yùn)用六西格瑪工具,數(shù)據(jù)指標(biāo)就會(huì)自然而然地計(jì)算出來,因?yàn)閹缀跛辛鞲瘳敼ぞ叨际腔跀?shù)據(jù)分析的,比如在本例中,改進(jìn)目標(biāo)事實(shí)上是業(yè)務(wù)流程,但最終的改進(jìn)依據(jù)卻是停線比例。