Fiber Reinforced Concrete
Plain concrete possesses a very low tensile strength, limited ductility and little resistance to cracking.?Due to its poor tensile?strength, internal micro cracks are present in concrete which leads to brittle fracture. In order to reduce the micro cracks, addition of small, closely spaced and uniformly dispersed fibers are used. This type of concrete is known as?fiber reinforced concrete (FRC).
In recent years a great deal of interest has been shown in fiber reinforced concrete. Various experiments have shown that the addition of fibers (normally up to about 1% or 2% by volume) to conventional concretes can appreciably improve their characteristics.
A number of different types of fibers are used to produce?FRCs?of various kinds. The most common ones are steel, asbestos, organic polymers (?primarily polypropylene) , glass and carbon. These fibers vary considerably in geometry, properties, effectiveness, and cost.
The first generation of steel fibers were smooth, but it was soon found that, as a result, they did not develop sufficient bond with the cement matrix; modern steel fibers are generally either deformed along their lengths or at their ends (Fig. 10. 1) to enhance the cement-fiber bond.
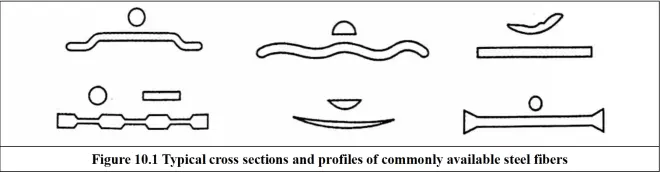
Naturally occurring asbestos fibers have been used with cement and water in the manufacture of asbestos cement pipe and other building components since about 1900. Asbestos fibers are particularly compatible with the cement matrix, which makes it easy to disperse relatively large volumes of fibers?in the matrix and enhances the fiber-matrix bond in the hardened concrete. The resulting asbestos cements have high corrosion and abrasion resistance. However, there are significant health hazards associated with the production and handling of asbestos fibers, leading to lung cancer. It should be noted that health risks are minimal during the use of asbestos cement components, as long as they do not begin to disintegrate due to mechanical abuse. Thus, as a result of the health risks and increasingly strict environmental regulations, asbestos fibers have largely been replaced with other types of fibers.
Synthetic fibers?have become increasingly common in recent years. Most synthetic fibers have lower elastic moduli than concrete.?At the relatively low fiber volumes currently used in industrial practice (<0.5% ) , they are most effective in reducing the amount of plastic shrinkage cracking, though they also provide some toughening and impact resistance. Carbon fibers are high-modulus synthetic fibers that also have high tensile strengths. They are very effective in FRC, but their high cost has limited their use.
It must be emphasized that, in general, fiber reinforcement is not a substitute for conventional steel reinforcement. Fibers and steel reinforcement play different roles in concrete: Reinforcing bars are used to increase the load-bearing capacity of structural concrete members, while fibers are more effective for crack control. There are many applications in which fibers?can be used effectively in conjunction with conventional reinforcement to improve the behavior of?structural components, for instance when the concrete is to be subjected to blast or impact loading, or in seismic applications.
Some properties of fiber reinforced concrete are described below.
1. Strength
The strengths of fiber-reinforced concretes are not?significantly greater than they would be if the same mixes were used without the fibers. The role of the fibers is not to increase strength, though modest strength increases may occur.
2. Toughness?
Cracks develop in concrete as it is loaded (or as it dries). If the fibers have sufficient strength, and if they can achieve sufficient bond with the matrix, they will tend to keep the crack widths small. Fiber reinforced concretes are substantially tougher and have greater resistance to cracking. However, some fibers are more effective than others in this regard. For instance, deformed fibers, which have a better bond with the matrix, will be more effective than smooth fibers of the same material, which pull out of the matrix more easily. The use of fibers has increased the versatility of concrete by reducing its brittleness.
3. Impact Resistance?
The impact resistance of plain concrete, which is quite low, can be increased dramatically ( by more than an order of magnitude) by the addition of fibers. Steel and carbon fibers?are more effective in this regard than synthetic fibers, but all types of fibers increase both the fracture energy and generally the peak loads under impact. At the higher loading rates associated with impact tests, in which failure occurs in a few milliseconds rather than in a few minutes as in static tests, a higher number of fibers appear to break rather than to pull out. This is related to the bond characteristics of the fibers; a great deal of research is currently underway to try to optimize fiber geometry for the case of impact loading.
4. Creep and Shrinkage
Up to fiber volumes of about 1%?fiber additions have little or no effect on either the creep characteristics or the drying shrinkage of concrete, though they tend to reduce the crack widths significantly during shrinkage. However, fibers can be very effective in reducing the plastic shrinkage. Indeed, this is one of the principal uses of polypropylene fibers in modern FRO technology
5. Durability
Synthetic fibers are not subject to corrosion.?Steel fibers may, of course, rust. However, it has been found that for good quality FRC, this rusting is confined to the "skin" of the concrete; fibers in the interior of the concrete are protected by the alkaline environment. Thus, even with steel fibers, corrosion leads only to cosmetic effects. In some cases, such as high-temperature refractory applications, stainless steel fibers may be used ( though at a considerable increase in cost).