Flow-3D AM 模擬液態(tài)金屬 3D 打印狀態(tài)-馬路科技
按需噴墨打印是一種有效的商業(yè)和消費圖像復制方法。這項技術的原理也可以應用于功能印刷和增材制造領域。傳統(tǒng)的噴墨技術已用于通過沉積和圖案化從聚合物到活細胞的材料來打印各種功能性介質(zhì)、組織和設備。這項工作的重點是將基于噴墨的技術擴展到 3D 實體金屬結構的打印。目前,大多數(shù) 3D 金屬打印應用涉及沉積金屬粉末在激光或電子束等外部定向能源的影響下燒結或熔化以形成固體物體的情況。然而,此類方法在成本和工藝復雜性方面存在缺點,例如,需要時間和能源密集型技術在 3D 打印工藝之前制造粉末。
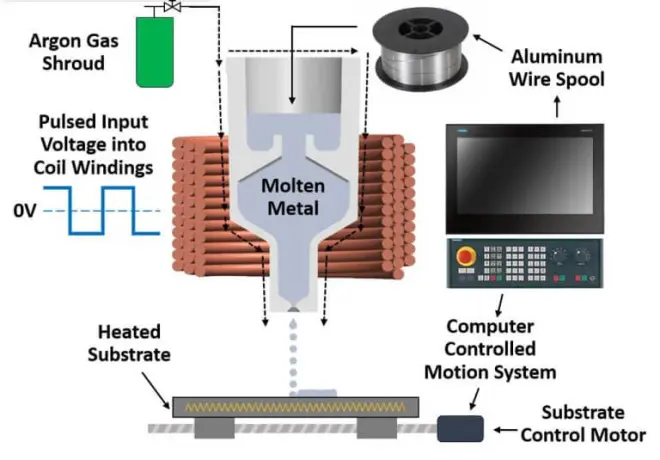
在本文中,我們將討論一種基于磁流體動力學 (MHD) 按需噴射和液滴沉積在移動基板上的 3D 金屬結構增材制造的新方法。為簡單起見,該研究分為兩部分:在第一部分中,使用 MHD 分析估計打印頭內(nèi)部的洛倫茲力密度產(chǎn)生的壓力,然后將其用作?FLOW-3D AM?模型的邊界條件用于研究液滴噴射動力學。在第二部分,F(xiàn)LOW-3D AM進行參數(shù)分析以確定理想的液滴沉積條件。
建模工作的結果用于指導設備的設計,如圖 1 所示。一個線圈圍繞著噴射室,并被電脈沖產(chǎn)生一個瞬態(tài)磁場,該磁場滲透到液態(tài)金屬中并感應出內(nèi)部閉環(huán)的瞬變電場。電場產(chǎn)生循環(huán)電流密度,它與瞬態(tài)場反向耦合并在腔室內(nèi)產(chǎn)生磁流體動力洛倫茲力密度。力的徑向分量產(chǎn)生壓力,用于將液態(tài)金屬液滴從孔口噴出。噴出的液滴行進到基板上,在那里它們聚結并凝固形成延伸的固體結構??梢允褂靡苿踊逯饘哟蛴∪我庑螤畹娜S結構,從而實現(xiàn)入射液滴的精確圖案沉積。該技術已獲得專利并由 Vader Systems 商業(yè)化,商品名為 MagnetoJet。
原型設備開發(fā)
Vader Systems 的 3D 打印系統(tǒng)的關鍵部件是打印頭組件,該組件由一個兩部分噴嘴和一個螺線管線圈組成。液化發(fā)生在噴嘴的頂部。下部包含一個亞毫米孔,其直徑范圍為 100μm 至 500μm。如圖 1a 所示,水冷螺線管線圈圍繞著孔腔(冷卻系統(tǒng)未顯示)。許多打印頭設計的迭代開發(fā)一直在探索噴射室?guī)缀涡螤顚σ簯B(tài)金屬填充行為以及液滴噴射動力學的影響。這些原型系統(tǒng)已成功打印出由普通鋁合金制成的實體 3D 結構(圖 2)。液滴的直徑范圍為 50 μm 至 500 μm,具體取決于孔口直徑、幾何形狀、噴射頻率和其他參數(shù)。
計算模型
作為原型設備開發(fā)的一部分,計算模擬在原型制造之前進行,以篩選設計概念的性能,即液滴噴射動力學、液滴-空氣和液滴-基板相互作用。為了簡化分析,開發(fā)了兩種不同的互補模型,它們使用計算電磁 (CE) 和 CFD 分析。在第一個模型中,使用兩步 CE 和 CFD 分析來研究基于 MHD 的液滴噴射行為和有效壓力生成。在第二個模型中,采用熱流體 CFD 分析來研究基板上液滴的圖案化、聚結和凝固。
在 MHD 分析之后,從第一個模型中提取了等效壓力分布,并將其用作?FLOW-3D AM模型的輸入,旨在探索液滴噴射和液滴-基板相互作用的瞬態(tài)動力學。執(zhí)行FLOW-3D AM模擬以了解孔口內(nèi)部和周圍的潤濕對液滴噴射的影響。通過改變孔口內(nèi)外的流體初始化水平,并允許脈沖之間有一個由脈沖頻率決定的時間段,我們能夠識別噴射液滴的特征差異,包括大小和速度。
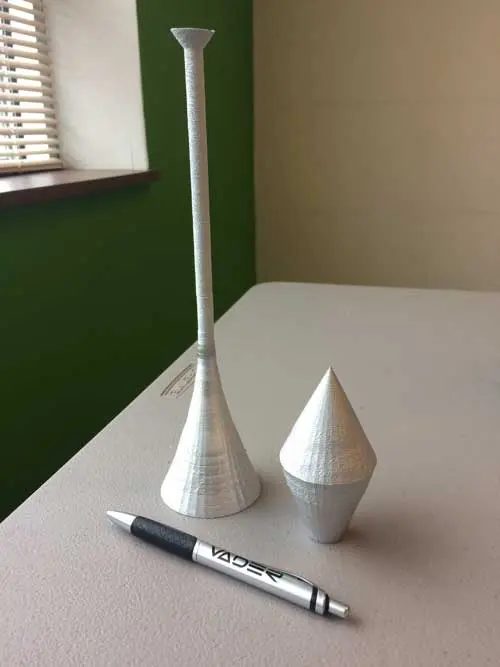
液滴生成
在 MagnetoJet 打印過程中,液滴以通常在 1-10 m/s 范圍內(nèi)的速度噴射,具體取決于電壓脈沖參數(shù),并在撞擊基板之前在飛行過程中稍微冷卻。控制基板上液滴的圖案化和凝固的能力對于精確 3D 實體結構的形成至關重要。使用高分辨率 3D 運動底座可實現(xiàn)用于圖案化的精確液滴放置。然而,控制凝固以創(chuàng)建具有低孔隙率且沒有不需要的分層偽影的良好成型 3D 結構是一項挑戰(zhàn),因為它涉及控制:
當液滴冷卻時,從液滴到周圍材料的熱擴散,
噴出液滴的大小,
液滴噴射頻率和
來自已經(jīng)形成的 3D 物體的熱擴散。
通過優(yōu)化這些參數(shù),液滴將足夠小以提供印刷特征的高空間分辨率,并且它們將保留足夠的熱能以促進與相鄰液滴和層之間更平滑的聚結。應對熱管理挑戰(zhàn)的一種方法是將加熱基板的溫度保持在低于但相對接近熔點的溫度。這降低了液滴與其周圍環(huán)境之間的溫度梯度,從而減緩了液滴的熱量擴散,從而促進聚結和凝固,形成光滑的固體 3D 質(zhì)量。
使用?FLOW-3D AM進行參數(shù)化 CFD 分析以探索該方法的可行性。我們對保持在較低溫度下的基板運用Flow-3D AM進行了類似的分析,例如 600 K、700 K 等 據(jù)觀察,雖然 3D 結構可以打印在較冷的基板上,但它們顯示出不良的偽影,例如后續(xù)沉積金屬層之間缺乏強聚結。這是由于沉積液滴中熱能損失率增加所致?;鍦囟鹊淖罱K選擇可以基于給定應用的物體可接受的打印質(zhì)量來確定。隨著打印過程中部件變大,這甚至可以動態(tài)地進行調(diào)整以適應更高的熱擴散。
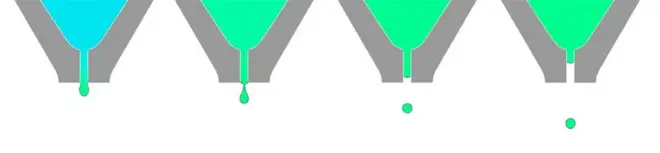
液滴聚結和凝固
我們研究了加熱基板上的層內(nèi)液滴聚結和凝固作為液滴之間的中心間距以及液滴噴射頻率的函數(shù)。在此分析中,液態(tài)鋁的球形液滴從 3 毫米的高度撞擊加熱的不銹鋼基板。液滴的初始溫度為 973 K,基板保持在 900 K,略低于凝固溫度 943 K。圖 3 顯示了當液滴分離距離從 100 變化到實線時,液滴聚結和凝固 μm 至 400 μm,步長為 50 μm,噴射頻率保持恒定在 500 Hz。當液滴分離超過 250 μm 時,沿線出現(xiàn)帶有尖點的固化段。在 350 μm 或更大的分離距離處,線段變得離散并且線具有未填充的間隙,這對于形成光滑的固體結構是不理想的。
我們對保持在較低溫度下的基板運用Flow-3D AM進行了類似的分析,例如 600 K、700 K 等 據(jù)觀察,雖然 3D 結構可以打印在較冷的基板上,但它們顯示出不良的偽影,例如后續(xù)沉積金屬層之間缺乏強聚結。這是由于沉積液滴中熱能損失率增加所致?;鍦囟鹊淖罱K選擇可以基于給定應用的物體可接受的打印質(zhì)量來確定。隨著打印過程中部件變大,這甚至可以動態(tài)地進行調(diào)整以適應更高的熱擴散。
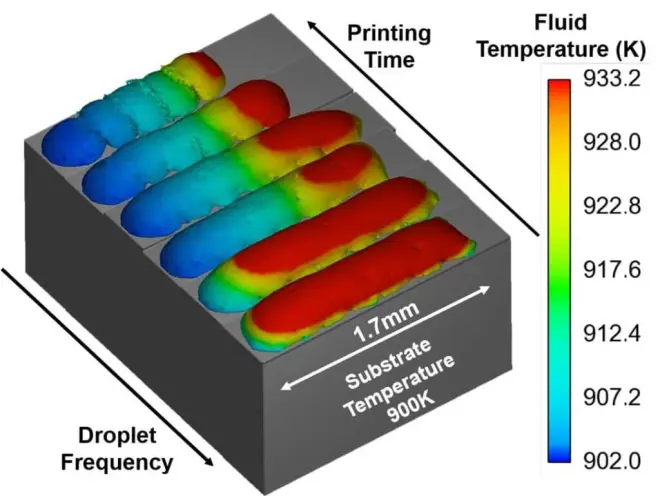
FLOW-3D 結果的驗證
圖 4 顯示了印在加熱基板上的杯狀結構。在打印過程中,加熱基板的溫度根據(jù)打印部分的瞬時高度實時從 733K(430°C)逐漸升高到 833K(580°C)。這樣做是為了克服隨著物體表面積的增加而增加的局部熱擴散。鋁的高導熱性使得這特別困難,因為必須快速調(diào)整局部熱梯度,否則溫度會迅速下降并降低層內(nèi)聚結。
結論
根據(jù)Flow-3D AM的仿真結果,Vader System 的原型磁流體動力液態(tài)金屬按需滴落 3D 打印機原型能夠打印任意形狀的 3D 固體鋁結構。這些結構是使用亞毫米液滴的逐層圖案沉積成功印刷的。僅使用一個噴嘴就實現(xiàn)了每小時超過 540 克的材料沉積速率。這項技術的商業(yè)化正在順利進行,但在吞吐量、效率、分辨率和材料選擇方面實現(xiàn)最佳印刷性能仍然存在挑戰(zhàn)。新的建模工作將側重于量化打印過程中的瞬態(tài)熱效應、彎液面行為以及評估打印部件的質(zhì)量展開。
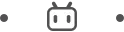
馬路科技(RATC)成立于1996年,為FLOW-3D中國公司授權總經(jīng)銷商,是以三維測量、三維掃描、逆向工程以及三維打印等先進技術為導向的科技公司,客戶主要來自汽車、航空航天以及消費品等產(chǎn)業(yè)。馬路科技在國內(nèi)共有八個服務點,位于:北京、青島、上海、昆山、寧波、東莞、成都、臺北、臺中、臺南,有超過200名專家提供在地專業(yè)技術支持及服務。?