《高分子合成工藝》簡答題答案
第一章1、單體儲存過程中應注意什么問題,儲存設備應考慮哪些問題,為什么? 答:單體儲存過程應該注意: (1)為了防止單體自聚,在單體中添加少量的阻聚劑,如在1,3-丁二烯中加人防老劑對叔丁基鄰苯二酚。 (2)為防止著火事故的發(fā)生,單體儲罐要遠離反應裝置,儲罐區(qū)嚴禁明火以減少著火的危險。(3)防止爆炸事故的發(fā)生,首先要防止單體泄漏,因單體泄漏后與空氣接觸產(chǎn)生易爆炸的混合物或過氧化物;儲存氣態(tài)單體(乙烯)或經(jīng)壓縮冷卻后液化的單體(丙烯、氯乙烯、丁二烯等)的儲罐應是耐壓的儲罐;高沸點的單體儲罐應用氮氣保護,防止空氣進入。 2、引發(fā)劑儲存是應注意什么問題? 答:多數(shù)引發(fā)劑受熱后有分解和爆炸的危險,干燥純粹的過氧化物最易分解。 因此,工業(yè)上過氧化物引發(fā)劑采用小包裝,儲存在陰暗、低溫條件下,防火、防撞擊。 3、聚合反應產(chǎn)物的特點是什么? 答:聚合物的分子量具有多分散性;聚合物的形態(tài)有堅韌的固體、粉狀、粒狀和高粘度的溶液;聚合物不能用一般產(chǎn)品精制的方法如蒸餾、重結晶和萃取等方法進行精制和提純。 4、選擇聚合方法的原則是什么? 答:聚合方法的選擇原則是根據(jù)產(chǎn)品的用途所要求的產(chǎn)品形態(tài)和產(chǎn)品成本選擇適當?shù)木酆戏椒ā?自由基聚合可以采用本體、溶液、乳液和懸浮聚合等方法;離子聚合只能采用本體和溶液聚合。 聚合操作可以是連續(xù)法或者間歇法;聚合反應器有不同的類別、排熱方式和攪拌裝置等。 5、如何選用聚合反應器? 答:根據(jù)聚合反應器的操作特性、聚合反應及聚合過程的特征、聚合反應器操作特性和經(jīng)濟效益等聚合反應的特性以及過程控制的重點,按下列原則選擇聚合反應器: (1)重點在于目標產(chǎn)物的生成時,在原料配方一定的情況下,當反應物濃度高對于目標聚合物生成有利時,可選用管式聚合反應器或間歇操作的釜式聚合反
應器,當反應物濃度低對目標聚合物生成有利時,可選用連續(xù)操作的釜式聚合反應器或多級串聯(lián)釜式聚合反應器
(2)重點在于確保反應時間的場合可選用塔式或管式聚合反應器
(3)重點在于除去聚合熱的場合可以選用攪拌釜式聚合反應器
(4)重點在于除去平衡過程中產(chǎn)生的低分子物的場合,可選用攪拌釜式聚合反應器,薄膜型聚合反應器或表面更新型聚合反應器
(5)對于高粘度體系,應盡量選擇相應的特殊型式的聚合反應器。
6、常見的聚合反應器有哪些?簡述釜式聚合反應器結構。
答:常見的聚合反應器有:釜式反應器、管式反應器、塔式反應器、流化床式反應器、特殊形式聚合反應器。
釜式反應器包括:容器部分、換熱裝置、攪拌裝置、密封裝置、其它結構
7、高分子合成工藝路線選擇原則?
答:高分子合成工藝路線的選擇原則為:滿足產(chǎn)品的性能指標要求;生產(chǎn)的可靠性;技術上的先進性;經(jīng)濟上的合理性;生產(chǎn)裝置大型化;清潔生產(chǎn)、注重可持續(xù)發(fā)展。
第二章
1、生產(chǎn)單體的原料路線有幾條?比較它們的優(yōu)缺點?
答:石油化工路線、煤炭路線和其它(農(nóng)副產(chǎn)品)路線。
對原料來源要求:來源豐富、成本低 、生產(chǎn)工藝簡單、環(huán)境污染小、各種原料能綜合利用、經(jīng)濟合理,可以從著幾方面簡單分析。
2、簡述由最基本的原料(石油、天然氣和煤炭)制造高分子材料的過程。
從高分子合成的六個步驟結合具體的例子描述。
3、從乙炔開始可以制備哪些單體?從而制備那些高聚物?
參考教材。
第三章
1、什么是本體聚合?其主要組分是什么?本體聚合有什么特點?
答:不加其它介質(zhì),只有單體本身、引發(fā)劑或催化劑在熱、光、輻射作用下進行的聚合稱為本體聚合,其主要組分是單體和引發(fā)劑(催化劑)。
優(yōu)點:工藝過程簡單,通常本體聚合的轉(zhuǎn)化率很高,所需回收的單體很少,可省去分離回收工序;聚合體系簡單:只需單體和引發(fā)劑;產(chǎn)品因為無雜質(zhì)引入,品質(zhì)純凈,絕緣性能和透明性好;因無溶劑回收和洗滌產(chǎn)物的過程,廢水少,有利于環(huán)境保護。
缺點:烯烴聚合為放熱反應,無傳熱介質(zhì)、反應熱難于消除;體系粘度大,分子擴散困難,所形成的合物的分子量分布加 寬,產(chǎn)品易產(chǎn)生氣泡;存在自加速效應。
2、甲基丙烯酸甲酯澆鑄本體聚合工藝中,為什么要分兩段進行?
答:MMA在聚合過程中,當單體轉(zhuǎn)化率達到20%左右時,粘度上升很快,聚合速率顯著提高,以致發(fā)生局部過熱,甚至產(chǎn)生爆聚,這種現(xiàn)象稱為“凝膠效應"。在聚合過程中,當反應物漸漸增稠而變成膠質(zhì)狀態(tài)后,熱的對流作用受到限制,使反應體系積蓄大量的熱,局部溫度上升,導致聚合速率加快,以致產(chǎn)生大量的熱量,這種惡性循環(huán)的結果先是局部,然后擴大至全部達到沸騰狀態(tài),這就是所謂爆聚。在MMA轉(zhuǎn)化成聚合物的反應過程中,反應物的體積有著顯著的收縮。采用兩段聚合可以:
(1)縮短聚合時間,提高生產(chǎn)率,保證產(chǎn)品質(zhì)量;
(2)使一部分單體進行聚合,減少在模型中聚合時的收縮率;
(3)增加粘度,從而減小模內(nèi)漏漿現(xiàn)象;
(4)克服溶解于單體中的氧分子的阻聚效應。
3、乙烯氣相本體自由基聚合的聚合熱很高,為生產(chǎn)正常進行,工藝上需采取哪些措施?
答:乙烯氣相本體聚合時聚合強烈放熱,一般轉(zhuǎn)化率提高1%,反應物料溫度提高12~13°C。如果聚合熱不及時排出,溫度會迅速升高,而乙烯在350°C以上不穩(wěn)定,會發(fā)生爆炸性分解。因此乙烯聚合應防止局部過熱,控制低的轉(zhuǎn)化率(通常在20%~30%),大量的乙烯必須循環(huán)使用,以保證傳熱。同時,聚合釜中采用高速攪拌,保證釜內(nèi)物料與引發(fā)劑充分混合,不產(chǎn)生局部過熱。
4、乙烯高壓聚合產(chǎn)生長支鏈和短支鏈的原因是什么?
答:活性鏈向其它聚合物大分子鏈轉(zhuǎn)移,生成新的游離基。如果乙烯與這種新的活性游離基繼續(xù)結合,便形成大分子內(nèi)的長鏈支化。
活性增長鏈中氫原子為同一鏈所奪?。从坞x基在分子內(nèi)部轉(zhuǎn)移),如果乙烯分子與這種活性的游離基繼續(xù)結合即發(fā)生分子內(nèi)的短鏈支化。
第四章
1、何謂懸浮聚合?懸浮聚合的種類有哪兩種?與本體聚合相比較其優(yōu)缺點是什么?
答:懸浮聚合是通過強烈的機械攪拌作用使不溶于水的單體或者多種單體的混合物成為液滴狀分散于懸浮介質(zhì)中進行聚合反應的方法,分為均相和非均相懸浮聚合。
特點:體系粘度低,聚合熱容易經(jīng)水介質(zhì)與夾套換熱,散熱和溫度控制比本體聚合,溶液聚合容易得多;懸浮聚合一般采用間歇分批方式進行。這主要是懸浮聚合中,隨著聚合反應的進行,產(chǎn)生的聚合物易粘附于聚合器壁上,從而影響樹脂質(zhì)量的均一性和設備的使用性能,使懸浮聚合的連續(xù)化難于實現(xiàn);產(chǎn)品分子量比溶液聚合高,比本體聚合分布窄;后處理工序比本體聚合復雜,生產(chǎn)成本高。
2、懸浮劑的種類及其懸浮機理
答:懸浮劑主要是一些溶于水的高分子物質(zhì)和一些難溶于水的微粉末無機化合物。
水溶性高分子化合物包括天然高分子化合物和合成高分子化合物兩類,屬于非離子型的表面活性極弱的物質(zhì),溶于水后,一部分分散于水相中,一部分被吸附于單體液滴的表面,從以下三個方面起到保護作用:降低體系的表面張力、形成珠滴保護層、增加介質(zhì)水的粘度。
無機化合物以機械的隔離作用阻止單體液滴相互碰撞和聚集。當固體粉未被水潤濕并均勻分散懸浮于水相中時,它們就象組成一個間歇尺寸一定的“篩網(wǎng)”,當單體液滴的尺寸小于這個“篩網(wǎng)”的尺寸時,液滴可以在粉未之間作曲折運動,碰撞合并成尺寸較大的液滴。大于“篩網(wǎng)”尺寸的液滴則不能穿過,故能防止發(fā)生聚集現(xiàn)象。
3、簡述懸浮聚合中工藝條件(水油比,溫度,時間,聚合裝置等)的控制并簡要說明原因。
水與單體用量之比為水油比,水油比大,傳熱效果好,聚合物顆粒粒度均一,相對分子量分布窄,生產(chǎn)一控制,但設備利用率低。水油比小,不利于傳熱,生產(chǎn)較難控制。
聚合溫度影響聚合速率,也影響聚合物的分子量。聚合溫度越高,聚合速率越快。較高溫度下反應可縮短懸浮聚合的危險期,減少聚合物粒子凝聚結塊向。但隨溫度升高,放熱峰提前出現(xiàn),放熱劇烈,在這種情況下防止爆聚極為重要。反應溫度對聚合物分子量有一定影響,如鏈引發(fā)速率大于增長速率,或因鏈增長活性增加導致鏈轉(zhuǎn)移活性增加時,聚合物分子量下降。
從延長反應時間來增加轉(zhuǎn)化率,將使生產(chǎn)周期延長,降低聚合設備的利用率,是不經(jīng)濟的。通常在達到90%轉(zhuǎn)化率以上時就終止反應。
懸浮聚合一般為間歇生產(chǎn),故大多數(shù)在聚合釜中進行。釜的傳熱和攪拌、粘釜和清釜均對聚合有影響。
4、簡述影響PVC樹脂顆粒形態(tài)和大小以及粒度分布的主要原因。
答:影響PVC樹脂顆粒形態(tài)和粒度分布的因素主要是懸浮劑的種類和機械攪拌,其次是單體純度、聚合用水和聚合物的后處理等。
1)懸浮劑種類:懸浮劑明膠對單體的保護作用太強,對樹脂的壓迫力太大,容易形成緊密型樹脂。PVA對單體的保護作用適中,形成疏松型樹脂。PVA的分子量越大,PVC樹脂的顆粒越小。PVA的分子量分布越寬,PVC樹脂的粒度分布也越寬。
2)機械攪拌:一般而言,機械攪拌速度越快,樹脂顆粒越小,攪拌速度均勻,樹脂顆粒分布較窄。
3)其它因素:單體或水中含有氯離子、氯化物等對PVC樹脂有一定的溶解能力,會導致形成緊密型樹脂。
第五章
1、什么是乳液聚合?其主要組分和各組分的作用是什么?乳液聚合有什么特點?
答:乳液聚合是由單體和水在乳化劑作用下配制成的乳液中進行的聚合。主要組分有油溶性單體、水溶性引發(fā)劑、水溶性乳化劑和介質(zhì)水。
乳化劑在乳液聚合中的作用可以概括為:
降低界面張力,便于油相單體和聚合物膠乳乳化和分散得很細;
增溶作用,使油溶性單體溶解在液滴之中,形成乳液體系;
形成保護膠膜,便乳液體系穩(wěn)定。
乳液聚合的特點:以水為反應介質(zhì),粘度低,成本低,同時,分散體系穩(wěn)定性優(yōu)良,反應平穩(wěn)安全,便于管道輸送,容易實現(xiàn)連續(xù)化操作。產(chǎn)品可直接作涂料和粘合劑,減少了引起火災和污染環(huán)境的可能;聚合速度快同時分子量高;可以利用各種單體進行聚合和共聚合,有利于乳液聚合物的改性和新產(chǎn)品的開發(fā);需得到固形物時,后處理復雜,成本高,聚合物產(chǎn)品中雜質(zhì)含量高。
2、什么是乳化劑?乳化劑的作用是什么?乳化劑有哪幾類?它們使用的場合有什么不同?用哪些指標來表征乳化劑的性能?
答:工業(yè)上乳液聚合采用的乳化劑全部是表面活性劑。 乳化劑在乳液聚合中的作用可以概括為:降低界面張力,便于油相單體和聚合物膠乳乳化和分散得很細;增溶作用,使油溶性單體溶解在液滴之中,形成乳液體系;形成保護膠膜,便乳液體系穩(wěn)定。
按照乳化劑溶于水時,其親水基是否電離可分成:離子型和非離子型乳化劑。
臨界膠束濃度CMC和親水親油平衡值HLB。
3、乳液聚合中,乳化劑并不參與反應,但是對聚合反應速率和聚合物分子量有很大影響,為什么?
答:對于在合理的乳化劑濃度范圍內(nèi)進行的正常乳液聚合來說,[E]越大膠束數(shù)目Nm越多,按膠束機理生成的乳膠粒數(shù)目也就越多,即Np就越大,Dp就越小。當自由基生成速率一定時,Np越大,自由基在乳膠粒中的平均壽命就越長,自由基就有充足的時間進行鏈增長,故可達到很大的分子量Mn;同時,NP大,說明反應活性中心數(shù)目多,故Rp也越大。
4、什么是種子乳液聚合?
答:種子乳液聚合是指在乳液聚合體系中如果已經(jīng)有乳膠粒子存在,當物料配比和反應條件控制適當時,新加入盼單體原則上僅在已生成的微粒上聚合,而不生成新的乳膠粒,即僅增大原來微粒的體積,而不增加乳膠粒的數(shù)目,這種乳液聚合稱做種子乳液聚合。簡言之,原來的乳膠粒好似種子,以原來的乳膠粒作為種子,再加單體繼續(xù)聚合,稱做種子乳液聚合。
第六章
1、什么是溶液聚合?簡述溶液聚合的優(yōu)缺點。
答:將單體溶解于溶劑中進行聚合的方法稱為溶液聚合。
優(yōu)點:溶劑作為傳熱介質(zhì)使體系具有較低的粘度,便于聚合熱的消散和溫度控制,局部過熱的危險減小。同時溶劑的回流和局部沸騰也有利于溫度的控制;易于控制產(chǎn)品的分子量,并減少交聯(lián)作用;便于除去聚合體系中殘留的催化劑,調(diào)節(jié)劑以及殘余單體;可不經(jīng)干燥直接用作油漆,涂料,粘合劑和紡絲液。
缺點:反應速度緩慢,聚合度不高;設備利用率低;溶劑回收既費時又增加成本,并造成環(huán)境污染。
2、什么是均相溶液聚合?什么是非均相溶液聚合?
答:生成的聚合物溶于溶劑中的溶液聚合為均相溶液聚合。生成的聚合物不溶于溶劑中的溶液聚合為非均相溶液聚合。
3、溶液聚合中溶劑的作用?選擇溶劑的原則是什么?
答:溶劑作用:(1)誘導分解 使引發(fā)效率降低,引發(fā)速率增高。(2)鏈轉(zhuǎn)移作用 (3)溶劑對聚合物分子形態(tài)的影響: 增加分子量、 減少聚合物的支化、交聯(lián)。
溶劑的選擇:
(1)對于聚合反應無阻聚或緩聚作用。
(2)鏈轉(zhuǎn)移常數(shù)不能很大,否則不能得到所要求的平均分子量和高分子量的聚合物。
(3)根據(jù)應用要求決定采用均相溶液聚合還是非均相溶液聚合。
(4)溶劑的毒性,安全及生產(chǎn)成本等因素。
第七章
1、溶液丁苯聚合中如何控制產(chǎn)品的無規(guī)度?并說明每種方法的原理。
(1)添加極性物質(zhì)—無規(guī)試劑法
添加少量極性物質(zhì)如醚類、硫醚、叔胺和磷的化合物等到溶聚丁苯的共聚體系中,通過這些極性物質(zhì)與活性增長中心的離子對絡合,可以改變兩種單體聚合時的相對活性,使苯乙烯聚合活性提高,在反應初期就能與丁二烯共聚得到無規(guī)共聚物,并使反應速度加快。
(2)控制加料速度法
利用鋰系引發(fā)體系活性聚合的特點,控制加料速度,使其低于聚合反應速度。這樣,當加入的少量丁二烯被聚合后,反應活性較差的苯乙烯也得到完全聚合。當加人體系中的兩種單體都消耗完之后,再追加少量單體,使反應繼續(xù)下去,以此保證苯乙烯能夠較為均勻地分布在大分子鏈上,最終形成無規(guī)共聚物。
(3)控制單體濃度比率恒定法
人為地控制丁二烯和苯乙烯單體的濃度在這樣的比率,即丁二烯的濃度保持在一個較低的水平,而苯乙烯的濃度大得足以在反應初期就能進入共聚物中,促使 KBS[B-][S]~KBB[B-][B],并不斷補充消耗的丁二烯的量,保持丁二烯與苯乙烯單體濃度比率始終恒定,則可獲得無規(guī)聚合的丁苯橡膠。
(4)高溫聚合法
常溫下,鋰系引發(fā)劑引發(fā)丁二烯與苯乙烯的共聚體系中,反應速率常數(shù)KSB>>KBS,KBB>KBS。但是在130~160℃的高溫下共聚時,苯乙烯的相對活性增加,其共聚速率常數(shù)與丁二烯靠近,三個速率常數(shù)之間的差距顯著縮小,使它們彼此都具競爭能力,從而實現(xiàn)無規(guī)共聚。
2、試討論丁基橡膠陽離子聚合的生產(chǎn)工藝(聚合方法和聚合工藝條件)
答:丁基橡膠是異丁烯和少量異戊二烯(用量為異丁烯質(zhì)量的1.5%~4.5%,或者二者質(zhì)量之比為97:3),經(jīng)陽離子聚合反應而得。
加人異戊二烯的目的是為了在大分子主鏈上提供雙鍵,因為異丁烯的均聚物大分子鏈上無雙鍵,不易硫化為橡膠制品。加人少量異戊二烯與之共聚得到的共聚物經(jīng)硫化后成為性能優(yōu)良的丁基橡膠。 丁基橡膠的生產(chǎn)以淤漿法為主,其聚合機理是典型的陽離子聚合機理。
第八章
1、簡述氣相本體聚合生產(chǎn)HDPE的工藝流程。
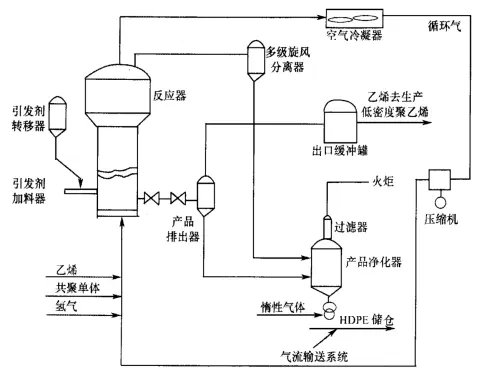
編輯
2、丙烯聚合的催化劑組成(第一到第四代)
見課件
3、丁二烯溶液聚合中產(chǎn)生掛膠的原理是什么?如何預防?
答:丁二烯在鎳催化體系中進行聚合是一個無終止的反應過程,在溶解良好的條件下體系是均相狀態(tài),未終止活性中心只能使單體聚合。如果溶解不好,有線性聚合物沉析出來,留在其中的活性中心會使線性分子中的2~3位置的π鍵打開而交聯(lián)形成凝膠,這種凝膠沉積于管壁、釜壁及其他死角就形成掛膠。 產(chǎn)生掛膠的原因很多,如溶劑類型、催化劑濃度、聚合溫度、原材料純度、聚合釜結構、攪拌器型式等。
為減輕掛膠,可采用以下措施:
(i)以苯、甲苯、甲苯和庚烷混合液代替溶解能力較差的抽余油。
(ii)提高催化劑活性,減少其用量。
(iii)穩(wěn)定操作,防止溫度起伏過大。
(iV)脫除三氯化硼乙醚絡合物中的水分,減少“黑油”產(chǎn)生。
(V)用預混釜使單體、溶劑和催化劑在入聚合釜前預混,使催化劑分散均勻。
(Vi)采用搪玻璃反應器或用不銹鋼制造,且用特殊的拋光技術進行加工也可減輕掛膠。
4、生產(chǎn)乙丙橡膠的物料組成及其作用
答:乙烯、丙烯二元共聚物,簡稱乙丙二元橡膠(EPM),引入少量非共軛二烯烴為第三單體得到的乙烯-丙烯-非共軛二烯共聚合物,簡稱乙丙三元橡膠(EPDM),兩者統(tǒng)稱已丙橡膠。 乙丙橡膠工業(yè)生產(chǎn)中,除乙烯、丙烯單體外,還需要第三單體、溶劑、分子量調(diào)節(jié)劑、活化劑等。 乙丙橡膠加入非共軛二烯烴作為第三單體,是為獲得用硫磺硫化所需的不飽和度。
5、比較丁二烯溶液聚合和氣相聚合工藝
從高分子合成的六個步驟分析比較,可以參考烯烴的氣相聚合。