Inconel718鎳基高溫合金GH4169鎳基合金
鎳基高溫合金哈氏合金系列材料生產(chǎn)供應(yīng)商廠家-禎賦(上海)實業(yè)
Inconel 718概要:
Inconel 718是沉淀強化的鎳基高溫高強合金
Inconel 718在-253~700℃溫度范圍內(nèi)具有良好的綜合性能,650℃以下的屈服強度居變形高溫合金的首位,并具有良好的抗疲勞、抗輻射、抗氧化、耐腐蝕性能,以及良好的加工性能、焊接性能和長期組織穩(wěn)定性,能夠制造各種形狀復(fù)雜的零部件,在宇航、核能、石油工業(yè)中,在上述溫度范圍內(nèi)獲得了極為廣泛的應(yīng)用。
該合金的另一特點是合金的組織對熱加工工藝特別敏感,掌握合金中相析出和溶解規(guī)律及組織與工藝、性能間的相互關(guān)系,可針對不同的使用要求制定合理、可行的工藝規(guī)程,就能獲得可滿足不同強度級別和使用要求的各種零件。
對應(yīng)牌號

供貨規(guī)格:
圓鋼、棒材、板材、帶材、管材、線材蘭宇活動低價供應(yīng)
化學(xué)成分:
C≤0.08 Mn≤0.35 Si≤0.015 P≤0.35 S≤0.015 Cr17~21 Ni50~55 Mo2.8~3.3 Cu≤0.3 Ti0.65~1.15 Al0.2~0.8 Fe余量 Nb4.75~5.5 B≤0.006
物理性能:
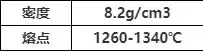
常溫下合金的機械性能的MIX:

特性:
1.易加工性
2.在700℃時具有高的抗拉強度、疲勞強度、抗蠕變強度和斷裂強度
3.在1000℃時具有高抗氧化性
4.在低溫下具有穩(wěn)定的化學(xué)性能
5
.良好的焊接性能
金相結(jié)構(gòu)
718合金為奧氏體結(jié)構(gòu),沉淀硬化后生成的γ”相使之具有了優(yōu)秀的機械性能。在熱處理過程中于晶界處生成的δ相使之具有了較好的塑性。
耐腐蝕性
不管在高溫還是低溫環(huán)境,718合金都具有極好的耐應(yīng)力腐蝕開裂和點蝕的能力。718合金在高溫下的抗氧化性尤其出色。
工藝性能與要求
熱加工
合適的熱加工溫度為1120-900℃,冷卻方式可以是水淬或其他快速冷卻方式,熱加工后應(yīng)及時退火以保證得到優(yōu)良的性能。熱加工時材料應(yīng)加熱到加工溫度的上限,為了保證加工時的塑性,變形量達到20%時的終加工溫度不應(yīng)低于960℃。
冷加工
冷加工應(yīng)在固溶處理后進行,加工硬化率大于奧氏體不銹鋼,因此加工設(shè)備應(yīng)作相應(yīng)調(diào)整,并且在冷加工過程中應(yīng)有中間退火過程。
焊接工藝
合金具有滿意的焊接性能,可用氬弧焊、電子束焊、縫焊、點焊等方法進行焊接。
零件熱處理工藝
航空零件的熱處理通常按標(biāo)準(zhǔn)熱處理制度和直接時效熱處理制度進行。
應(yīng)用范圍領(lǐng)域
由于在700℃時具有高溫強度和優(yōu)秀的耐腐蝕性能、易加工性,718可廣泛應(yīng)用于各種高要求的場合。
1.汽輪機
2.液體燃料火箭
3.低溫工程
4.酸性環(huán)境
5.核工程
Inconel718高溫度合金,具有良好的加工和焊接性能,在航空航天等尖端領(lǐng)域中得到廣泛應(yīng)用。電渣重熔法主要是通過爐渣對非金屬夾雜物進行吸附和溶解將金屬提純凈化[1]。電渣重熔共分為3個階段:自熔電極端部金屬液滴的形成、金屬液滴在渣池中下落、金屬熔池中雜質(zhì)的上浮。這3個階段中,最為重要的是熔滴形成以及滴落階段,此階段直接影響夾雜物去除的程度
[2-3]。由于技術(shù)限制,無法透過結(jié)晶器對電渣重熔的熔滴行為進行觀察,因此,采用數(shù)值模擬方法研究電渣重熔的凈化機制具有重要意義。由于熔滴的直徑和滴落速度直接影響著模擬的計算,學(xué)者們將熔滴形成和滴落過程作為源項加入動量方程
[4-5],將熔滴在穩(wěn)恒磁場下可視化
[6],采用多相流模型、熔滴表面張力模型、焓-多孔模型及MHD電磁模型
[7]等多種方法,在不同工藝參數(shù)下對電渣重熔熔滴行為展開研究。陶然等研究了熔滴滴落的過程中雜質(zhì)去除率與熔滴滴落的各階段尺寸大小及比接觸面積之間的關(guān)系[8-10]Campbell
[11]等人采用物理模型模擬電渣重熔過程中的金屬液滴生成及下落現(xiàn)象,結(jié)果顯示自耗電極熔化過程有兩種基本形式:熔化速率較低時,電極的端部會生成離散的金屬液滴;熔化速率較高時,電極端部離散的金屬液滴會消失變成連續(xù)的金屬流股,它在離電極末端一定距離處碎裂成小顆粒金屬液滴。埋在爐渣池中的電極的末端形狀呈現(xiàn)凸球形,并且電極尺寸與金屬液滴的大小有密切關(guān)系
[12]。范金席對主要工藝參數(shù)如電壓,填充率和鋼渣界面張力對液滴行為的影響以及熔池形狀與不同電極熔化速率的關(guān)系
[12]。但目前缺少對高溫合金的電渣重熔過程熔滴行為的研究,因此本文對高溫合金的熔滴行為進行了模擬研究,希望為實際工藝生產(chǎn)提供指導(dǎo)借鑒依據(jù)。
1數(shù)學(xué)模型和邊界條件1.1控制方程電渣重熔數(shù)值模擬過程耦合了多種場,控制方程包括能量守恒方程、質(zhì)量守恒方程、Maxwell電磁場方程、動量守恒方程。
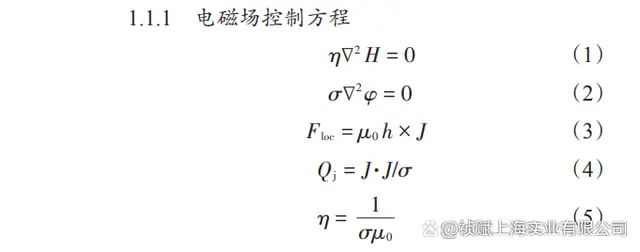
式中:H為磁場強度,A/m;σ為電導(dǎo)率,S/m;φ為電位,V;J為電流密度,A/m2;Floc為洛侖茲力,N/m3;μ0為真空磁導(dǎo)率,H/m;Qj為焦耳熱,W/m3;h為磁場擴散系數(shù),m2/s。
1.1.2流場控制方程因為熔渣池流動為湍流,將體積分數(shù)方程與動量方程都采用時均值處理,寫成矢量形式

式中:ρ為流體的密度,kg/m3;τ為單位時間,s;v為流動速度矢量,m/s;P為壓力,Pa;μeff為流體有效粘度,Pa·s;g為重力加速度,m/s2;s為源項,N/m3。
1.1.3多相流VOF控制方程用建立在固定的歐拉網(wǎng)格下的VOF模型求解控制方程,處理兩種或者多種互不相融流體的流動現(xiàn)象;利用不同流體的體積分數(shù)追蹤單元相界面。VOF模型中對于第q相的體積分數(shù)控制方程
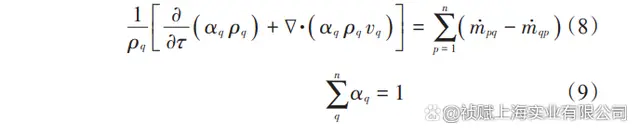
式中:ρq為第q相密度,kg/m3;αq為第q相體積分數(shù);vq為第q相的速度矢量,m/s;mpq為第p相向第q相轉(zhuǎn)移的質(zhì)量,kg;mqp為第q相向p相轉(zhuǎn)移的質(zhì)量,kg。對于一個控制體積,若αq=1,則代表q相充滿了控制體積。
若0<αq<1,則代表在控制體積中存在q相與其它相的交界面。若αq=0,則代表控制體積中不存在第q相。在VOF模型中,每相之間的相互作用力作為動量方程的源項。相互作用力為

式中:σij為i相j相之間的界面張力,N/m;αj為第j相的體積分數(shù);ρi為第i相的密度,kg/m3;κj為第j相的界面曲率。
1.2邊界條件為了方便計算及模型簡化,將出口設(shè)為零電勢位,分別將進口條件、出口條件設(shè)定為質(zhì)量入口和流量入口。設(shè)定壁面為無滑移邊界條件,將零剪切力邊界條件應(yīng)用于渣池和空氣的接觸面。對流換熱和輻射換熱為主要換熱方式。1.3工藝參數(shù)和物性參數(shù)電渣重熔過程中影響熔滴行為的因素很多,為了方便計算,本文做出如下假設(shè):
(1)液態(tài)熔渣和熔融金屬均為不可壓縮流體。
(2)鋼渣的物性參數(shù)只與溫度有關(guān)。
(3)此模型只考慮液態(tài)渣池、自耗電極和金屬熔池。模型設(shè)定的各項工藝參數(shù)如下:渣池深度140、150mm,電極長度310mm,電極直徑60mm,插入深度20mm,鋼錠高度350mm,結(jié)晶器直徑120mm,電極電壓30、35、40V,電流7.450A。模擬所用鋼物性參數(shù)如下:密度8240kg/m3,熱容435J/(kg·℃),電阻率1.15μΩ·m,導(dǎo)熱系數(shù)31.9W/(m·K),池導(dǎo)熱系數(shù)15.1W/(m·K),金屬液相線1260K,金屬固相線1320K,金屬凝固潛熱247MJ/kg。模擬所用渣物性參數(shù):密度2400kg/m3,熱容1404J/(kg·℃),導(dǎo)熱系數(shù)10.45W/(m·K),粘度0.0052kg/(m·s),熔渣黑度0.92,體積膨脹系數(shù)0.0001K-1,鋼液粘度0.006kg/(m·s),熔渣電導(dǎo)率σ(S/m)
2模擬結(jié)果分析2.1熔滴下落對溫度場和流場的影響圖1為各時間點熔滴滴落模擬圖。從圖2第一滴熔滴開始滴落到第二滴熔滴完成滴落的整個過程中區(qū)域溫度的變化,可以發(fā)現(xiàn),熔滴下落對溫度場影響不大。渣池溫度約為1800℃,熔滴溫度約為1600℃。
熔滴持續(xù)滴落時,對渣金界面產(chǎn)生擾動,流場出現(xiàn)并伴隨著對流換熱。從圖3第一滴熔滴開始滴落到第二滴熔滴完成滴落的整個過程中區(qū)域流場的變化,得到渣池流場的變化主要在熔滴附近,近似成對稱分布;隨著熔滴滴落,擾動也逐漸向渣池下方擴展。
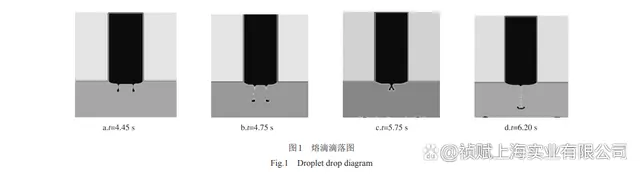
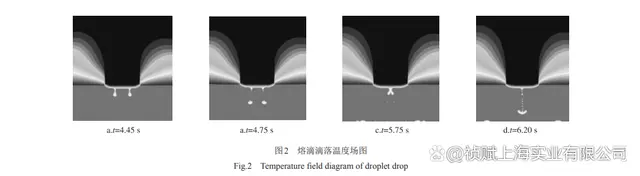
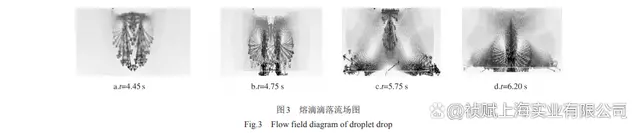
2.2填充比對熔滴滴落的影響填充比即電極直徑與結(jié)晶器直徑之比,它的大小影響到電渣重熔過程中熔煉速率、供電功率和鋼錠的凝固質(zhì)量,選取合適的填充比對提高熔煉的效果有著顯著影響。圖4至圖6表示不同填充比下的電極熔化情況。隨著填充比的增大,自耗電極端部熔滴的數(shù)量逐漸增多。當(dāng)在電壓為35V,其他條件不變的情況下,填充比為0.4時,電極與熔池接觸面積較小,只形成了一個熔滴源,當(dāng)填充比達到0.5以上時,電極最初熔化時會有兩個熔滴源生成,隨著熔煉平穩(wěn)的進行,兩個熔滴源逐漸靠近,最終融合成為一個較大的熔滴源。電極端頭形狀會有一定的變化,平直形貌逐漸消失成為弧形,且填充比的大小直接影響著弧度的大小,填充比的增加會使弧度減小。
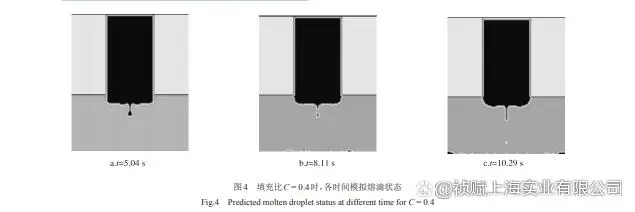
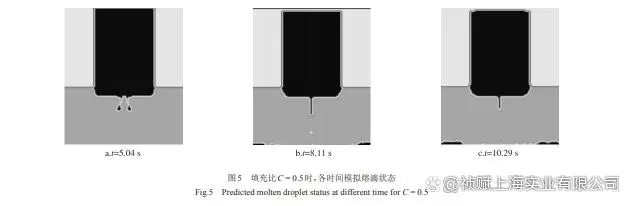
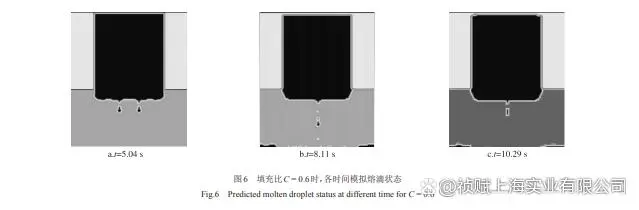
2.3電壓對熔滴行為的影響從圖7至圖9中可以看出,在電壓分別為30V、35V、40V條件下,電極在熔化開始階段,均會有兩個熔滴源生成,在短時間熔煉后,會形成一個熔滴源。其原因是熔煉初期電極端頭平直無錐度,液膜滴落位置不確定,未運動到電極中心便會滴落。隨熔化過程進行,電極端頭形成一定錐度,液膜移動到電極的中心,兩個液滴源合并成一。單位時間內(nèi)熔化的鋼液隨電壓的增大而增多,并且熔滴下落的平均直徑也增大。
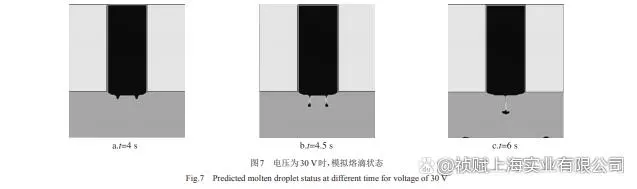
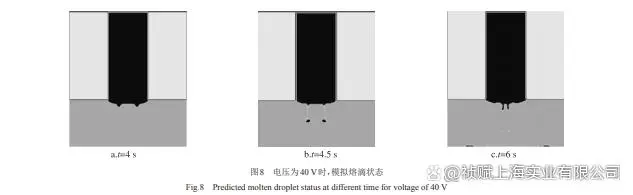
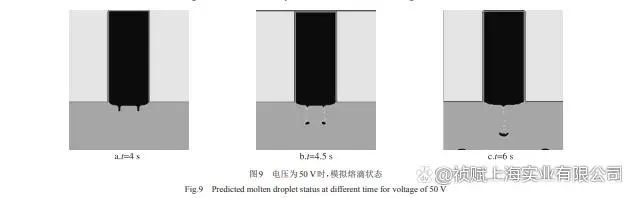
2.4界面張力對熔滴行為的影響圖10至圖12為兩相界面張力變化對熔滴的尺寸的影響情況,據(jù)模擬結(jié)果可以計算對應(yīng)界面張力下的熔滴尺寸。
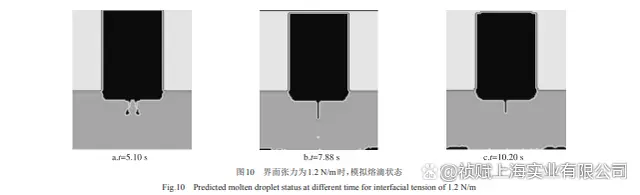
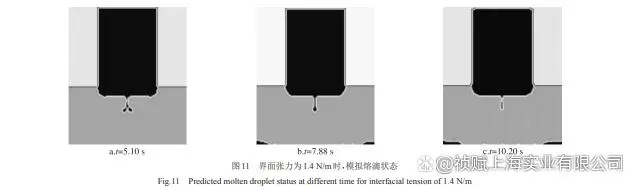
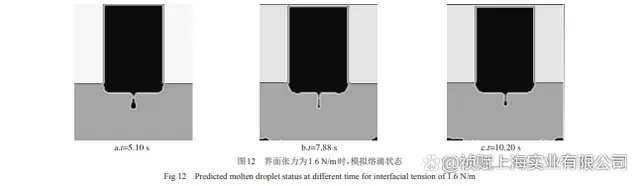
表面張力與熔滴直徑的理論公式
式中:M為熔滴質(zhì)量,kg;σ為鋼渣界面張力,N/m;r為電極半徑,m;g為重力加速度,m/s2;f為修正系數(shù)。熔滴直徑的模擬值與式
(12)的理論計算值如表1所示。模擬值和理論計算值都表明了熔滴直徑隨著表面張力的增加而增加,也證明了本文數(shù)值模擬的合理性與結(jié)果的可靠性。熔滴在重力、電磁力、熔渣浮力的合力與界面張力平衡。
界面張力比較大時,鋼液會在受到重力、電磁力、熔渣浮力合力小于最大界面張力的情況下逐漸聚集形成較大尺寸的熔滴,然后隨著熔滴重力的增加打破了原有的平衡進而滴落。在同一渣系下,界面張力越小,熔滴的直徑越小,熔滴的熱力學(xué)與動力學(xué)條件越充分,越有利于鋼錠的凈化。
2.5渣池深度對熔滴行為的影響不同渣池深度的熔滴形成過程如圖13和圖14所示。在其他參數(shù)條件一定的情況下,150mm渣池深度的熔滴形成時間略晚于140mm渣池深度,整個滴落過程的時間也略長。在t=4.86s的時候,140mm渣池深度的重熔過程的熔滴已經(jīng)在合力作用下與電極脫離,而渣池深度為150mm的熔化過程的熔滴還處在拉長狀態(tài);t=8.11s時,140mm渣池深度的熔滴形成一個熔滴源后進行滴落,而150mm渣池深度的熔滴源在還沒有完全形成一個熔滴源時便開始滴落。
3結(jié)論
(1)在熔滴下落過程中,整個渣池中溫度分布變化不大。熔池流場近似呈對稱分布,流動強度隨熔滴下落的頻率增大而增大。
(2)渣池深度越大,熔滴從形成到開始滴落所需時間越長,與渣接觸時間越長,越有利于凈化除雜。
(3)熔滴尺寸大小主要與填充比、界面張力和電極電壓有關(guān)。界面張力越大,熔滴形成的直徑孫夢茹,等:Inconel718高溫合金的電渣重熔過程熔滴滴落行為·425·遼寧科技大學(xué)學(xué)報第41卷越大。當(dāng)填充比在0.4~0.6時,電極與熔池接觸的面積越大,單位時間內(nèi)的熔化量越多,形成的熔滴直徑越大。電壓越大,電極溫度越高,單位時間內(nèi)熔化的鋼液越多,熔滴下落的平均直徑增大。