煉鐵廠高爐礦槽除塵器結構特點
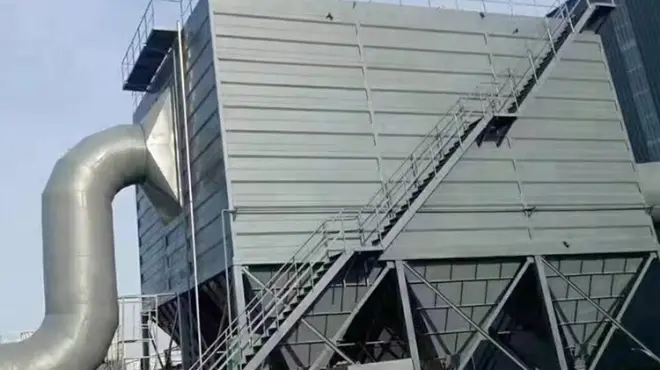
煉鐵廠高爐礦槽除塵器結構特點:
1、設計合理的灰斗導流技術解決了一般布袋除塵器常產生的各室分風不均勻現(xiàn)象;
2、離線清灰技術的應用,解決了在線清灰不徹底及灰塵形成二次吸附的現(xiàn)象;
3、灰斗進風及導流板的設置,避免了大顆粒粉塵直接對布袋的沖刷,延長了濾袋的使用壽命,降低了運行成本;
4、單室分風管道設有手動蝶閥,若同時將一室的離線閥與分風管道手動碟閥關閉,即可對此室實現(xiàn)不停機換袋與在線檢修,減少了停機的次數(shù),降低了因停機換袋或檢修為生產帶來的損失;
5、設計了特殊大儲量的脈沖閥貯氣包,既可滿足用戶提供的高壓氣源的使用,亦可滿足低壓氣源的使用;
6、濾袋上端采用彈簧漲圈型式,不但密封性能好,而且在維修更換布袋時快捷簡單,實現(xiàn)機外換袋;
7、在袋籠上端的結構設計上可按不同工況有多種結構型式(八角形、圓形等)的選擇,對袋籠的制造有嚴格的要求,本公司的袋籠是自動化生產線上加工的,其各項指標較標準提高50%左右。
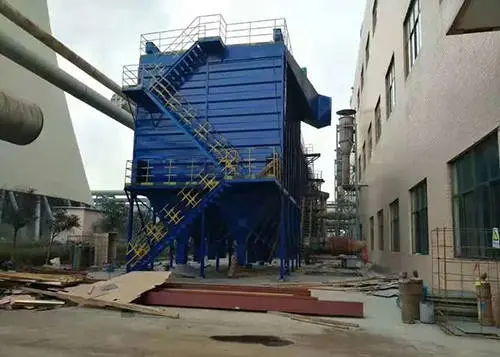
鋼鐵廠除塵器主體結構:
1、除塵器劃分為24個倉室,布置成兩列,中間為進風和出風總風道。倉室之間有隔板嚴密分隔,以實現(xiàn)離線清灰。
2、各倉室進風口與濾袋之間設擋風板,在箱體內部取上進風方式。
3、各倉室進口設手動蝶閥,出口設氣動停風閥??蓪崿F(xiàn)離線清灰以及除塵器在不停機狀態(tài)下實現(xiàn)單個倉室的檢修和每個倉室的風量分配。
4、每個倉室設216條濾袋,濾袋尺寸為120mm×6000mm。24個倉室共計5184條,總過濾面積為11716m2。
5、濾袋框架采用八角星形斷面,與圓形斷面相比,可增強清灰效果,減少濾袋與框架之間的磨損,有助于延長濾袋壽命,便于濾袋框架的抽出與插入。
6、濾袋材質選用滌綸針刺氈。
7、采用停風脈沖清灰方式,每倉室設一套噴吹裝置,噴吹管與脈沖閥出口采取插接方式便于拆裝。
8、電磁脈沖閥為DMF80型直通式快速脈沖閥,其壓力輸出口為雙扭線結構。
9、上箱體頂部設有落水坡度(20:1)和落水槽,以防止頂蓋積水。
10、每個倉室設一個灰斗,設有一臺倉壁振動器和一個人孔門。
11、灰斗下口設有手動插板閥和星形卸灰閥,前者供檢修星型卸料器時用。
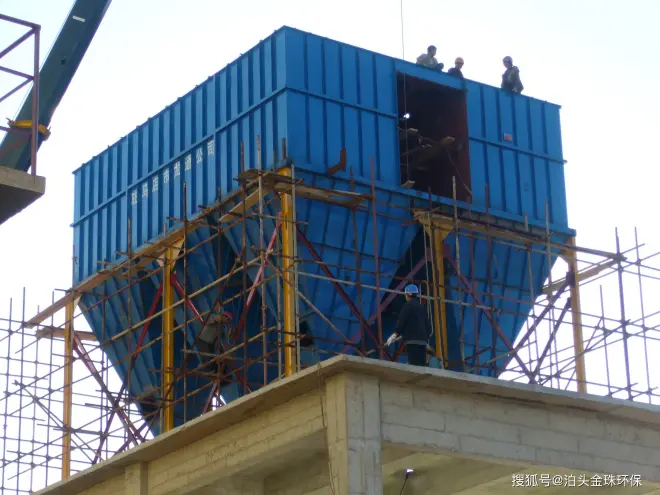
槽上捕集形式的特點
1)因為用移動通風槽,這樣吸風口可以不用閥門控制,減少閥門驅動裝置的維護和閥門的漏風問題。
2)在卸料小車的卸料口兩側開吸口,可以更加有效的進行煙塵捕集,提高捕集效果。
輸送、返礦(返焦)膠帶機受、落料捕集罩
為避免物料被吸入系統(tǒng)管道,而造成的管道內物料沉降及堵塞;膠帶轉運處設密閉罩。
鋼廠礦槽布袋除塵器結構及工作原理
本方案中含塵氣流由矩形風管進入各灰斗,再進入箱體的濾袋過濾區(qū),氣流穿過濾袋粉塵被阻留在濾袋外表面,凈化后的氣體經濾袋口進入清潔室,由風口排出。
除塵系統(tǒng)運行一段時間后,由于濾袋阻留粉塵的增多,氣體過濾阻力將增大,此時除塵器對濾袋進行清灰。本除塵器采用離線脈沖清灰方式,由自動控制系統(tǒng)按照設定的(時間)控制程序(或壓差控制程序),逐室逐排執(zhí)行自動脈沖噴吹,清落的粉塵集于灰斗,由卸灰閥卸入下級輸灰系統(tǒng)。該長袋低壓離線脈沖除塵器在運行過程中按自動重復控制程序控制除塵器運行清灰全過程,保證含塵氣體達標后排放。
為減少除塵器在清灰過程中過濾室的二次污染及二次吸附,采用分室離線清灰,并能實現(xiàn)維修與設備保養(yǎng),使除塵器阻損下降,真正做到設備高效、低阻、長壽命、可靠、低耗運行,是所有企業(yè)追求的目標。該除塵器在進風管上設有進風口拆流板,使各過濾室的進風量相對保持平衡,延長濾袋使用壽命。
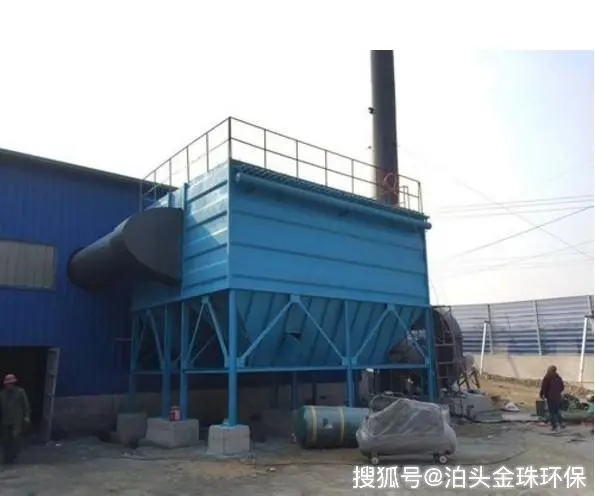