事后100%檢驗不如事前50%防錯!
導(dǎo)?讀
某供應(yīng)商,工人在裝配這樣一個零件時,經(jīng)常出現(xiàn)位置安裝反的情況。車間主管對工人反復(fù)進行質(zhì)量意識教育,甚至對操作者進行了考核,但裝反的問題依然時有發(fā)生。
一日,其公司領(lǐng)導(dǎo)先將五個零件放在了會議桌上,然后問道:“員工為什么出現(xiàn)操作錯誤?”
有人立刻回答:“因為員工的質(zhì)量意識薄弱,不遵守操作規(guī)程,所以出現(xiàn)了錯誤?!?br>領(lǐng)導(dǎo)繼續(xù)發(fā)問:“那我們采取了什么措施呢?”
有人回答:“加大了考核力度和后續(xù)檢驗?!?br>領(lǐng)導(dǎo)沉默了一會,一字一頓的說道:“如果由在座的諸位,去現(xiàn)場裝配這個零件,連續(xù)干上10天,你們能否保證不安裝反?你們能保證檢查出來這個故障?”一邊說著,一邊指向桌面上隨意放置的五個零件。
會場一片沉默,誰都沒有絕對的把握。
“看來人無完人,誰都沒有把握做到,那么,憑什么要求員工做到?”
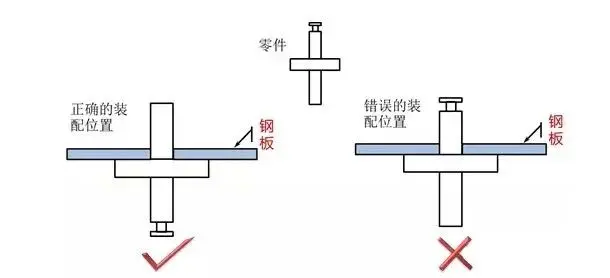
在產(chǎn)品實際的生產(chǎn)過程中,因零件相似而錯裝、因零件又小又多而漏裝等現(xiàn)象時有發(fā)生,需要防止或盡可能避免錯誤發(fā)生。
試想,一個操作人員每天進行同樣的裝配工作上百次千次甚至上萬次,如果產(chǎn)品設(shè)計和過程設(shè)計開發(fā)不能防止提前預(yù)防裝配錯誤的發(fā)生,就算是萬分之一的概率,操作人員稍微不留神,錯誤就發(fā)生了。
因此,必須在產(chǎn)品制造之前,產(chǎn)品及過程設(shè)計階段就要采取防錯,進行防錯的設(shè)計,提前預(yù)防裝配過程中可能發(fā)生的錯誤,要求為可制造性/可裝配性而進行的防錯。
防錯(Poka-yoke)是發(fā)明防錯設(shè)計結(jié)構(gòu)、防錯裝置,利用過程措施來杜絕或減少錯誤動作,將人為差錯預(yù)防性地消滅、降低。
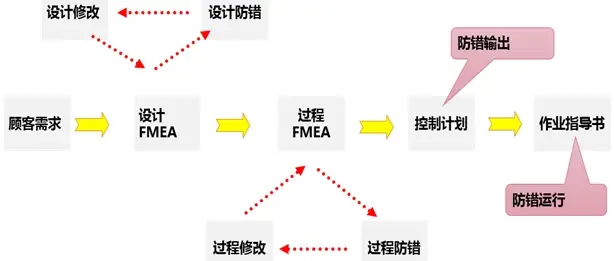
防錯管理,是由防錯設(shè)計、防錯的實施、防錯驗證和防錯經(jīng)驗教訓(xùn)的沉淀四個環(huán)節(jié)共同組成的“P-D-C-A”閉環(huán)過程。
其中,防錯設(shè)計又包括:錯誤識別、方案設(shè)計、方案評估,防錯流程的執(zhí)行過程中需要一系列的工具進行支撐;
在防錯設(shè)計階段,會使用到DFMEA和PFMEA分析,可利用以往成功的防錯經(jīng)驗、可使用頭腦風(fēng)暴的靈感,還可以使用5Why、魚骨圖等質(zhì)量分析工具;
在防錯實施階段,會利用控制計劃、標(biāo)準(zhǔn)化作業(yè)等將防錯的要求納入標(biāo)準(zhǔn)化作業(yè)和跟蹤監(jiān)控范圍;
在防錯驗證階段,需要利用產(chǎn)品試錯、產(chǎn)線試錯、OK/NG樣件等方式對防錯裝置的有效性進行驗證,對于防錯裝置可能出現(xiàn)的防錯裝置失效,應(yīng)建立應(yīng)急計劃,并根據(jù)防錯驗證的結(jié)果,作為制定對防錯裝置實施的預(yù)防性維護計劃。
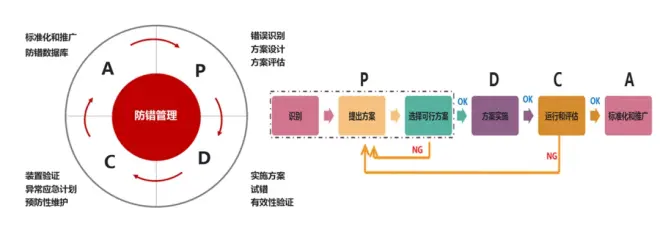
如何推行防錯?
我們圍繞上面的PDCA四個環(huán)節(jié),進行展開說明。
1
第一步,成立防錯小組
俗話說“聞道有先后,術(shù)業(yè)有專攻”,專業(yè)的事要交給專業(yè)的人做,用擅長于防錯的人做,小組成員應(yīng)包含設(shè)計、工藝、生產(chǎn)、品質(zhì)等相關(guān)人員。
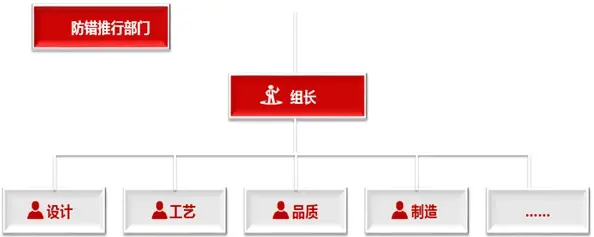
2
第二步,發(fā)現(xiàn)問題
來源于:
a . 以往產(chǎn)品或類似設(shè)計缺陷導(dǎo)致防錯失效;b . 零部件供應(yīng)商、總裝生產(chǎn)、服務(wù)店、用戶反饋等反饋的問題;c . 產(chǎn)品設(shè)計標(biāo)準(zhǔn);d . 產(chǎn)品/設(shè)計FMEA;e . 分析SPC數(shù)據(jù);
3
第三步,分析錯誤原因
對已經(jīng)存在的人為錯誤進行分析,找出錯誤原因所在,以及這些錯誤可能造成的后果進行預(yù)測分析。
確定根本原因是對應(yīng)用防錯技術(shù)以消除缺陷至關(guān)重要的。找出缺陷發(fā)生的源頭,用質(zhì)量管理七工具和5Why方法找出根本原因。
4
第四步,制定解決問題的基本方案
頭腦風(fēng)暴是一種可以激發(fā)產(chǎn)生大量的有創(chuàng)意的點子方法。也可利用工廠相似的防錯裝置。
錯誤預(yù)防是通過產(chǎn)品設(shè)計、裝配輔助措施等只允許以正確的方式進行生產(chǎn)活動的方法,實際生產(chǎn)要確保在產(chǎn)生錯誤的環(huán)節(jié)(缺陷來源)就直接將錯誤探測出來。
5
第五步,評估選擇正確的解決方案
防錯方案的評估和選擇,應(yīng)當(dāng)遵循“簡單、高效、低成本”的原則,對于防錯的投入產(chǎn)出分析,對方案進行成本/效益分析,評審行動方案,選擇最優(yōu)方案,在此基礎(chǔ)上提出實施計劃。
然后確定工序上的更改,選擇合適的防錯裝置,制定責(zé)任及時間表,分配所需的資源。
要站在產(chǎn)品的生產(chǎn)周期的角度來評判,局部和靜態(tài)的思維會阻礙正確決策的形成。對于設(shè)計無法滿足防錯(成本、產(chǎn)品平臺化、復(fù)雜生產(chǎn)工藝)進行工藝控制防錯。
方案評估時應(yīng)考慮:
a . 產(chǎn)品功能、結(jié)構(gòu)設(shè)計增加防錯;b . 制造過程中工藝防錯。
6
第六步,實施方案
在實施方案過程中,要不斷根據(jù)實際的情況進行調(diào)整,并不斷地進行改進和完善,實現(xiàn)方案的利益最大化。
7
第七步,運行和評估
收集數(shù)據(jù)與實施前相比較。
8
第八步,標(biāo)準(zhǔn)化和推廣
對防錯過程進行評審,前面的過程和結(jié)果進行總結(jié),建立防錯案例數(shù)據(jù)庫,探討方案能否復(fù)制、推廣其他類似產(chǎn)品,特別要注意標(biāo)準(zhǔn)化,
建立防錯數(shù)據(jù)庫,為以后新項目/產(chǎn)品進行防錯。數(shù)據(jù)庫來源于:
a . 以往產(chǎn)品或類似設(shè)計缺陷導(dǎo)致防錯失效;b . 以往生產(chǎn)經(jīng)驗,總結(jié)出常見的人為錯誤;c . 零部件供應(yīng)商、總裝生產(chǎn)、服務(wù)店、用戶反饋等反饋的問題;d . 產(chǎn)品設(shè)計標(biāo)準(zhǔn);e . 產(chǎn)品/設(shè)計FMEA;
防錯對于零缺陷質(zhì)量管理來說是注重預(yù)防,能夠在過程中最大限度地避免不良的發(fā)生,事后100%檢驗不如事前50%的防錯,防錯這對于追求高質(zhì)量的產(chǎn)品非常有效。
防錯不僅是一項系統(tǒng)工程,而且是實現(xiàn)零缺陷的有效手段,更是以預(yù)防為主的零缺陷質(zhì)量管理體系中的核心組成部分,它幾乎已成為質(zhì)量源于制造的同義語。
在進行產(chǎn)品設(shè)計和生產(chǎn)線設(shè)計時,只有在正確評估各種失效模式的風(fēng)險程度和充分調(diào)查客戶需求的基礎(chǔ)上,準(zhǔn)確地對關(guān)鍵工序、關(guān)鍵步驟進行防錯設(shè)計,才能取得事半功倍的效果。
奇葩的故障五花八門,有用的防錯可防萬一。
分享一些防錯案例:
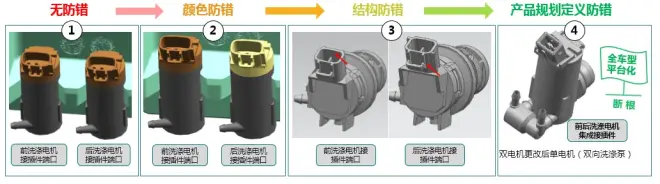
風(fēng)窗玻璃洗滌器防錯改善
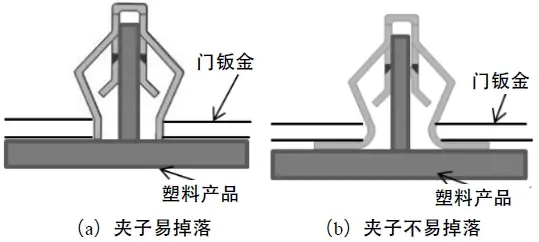
防掉落防錯改善