天行健咨詢:巧用六西格瑪,解決現(xiàn)場(chǎng)缸蓋螺栓擰緊問題!
G公司基于六西格瑪DMAIC方法對(duì)其發(fā)動(dòng)機(jī)缸蓋螺栓擰緊一次性合格率不高進(jìn)行改進(jìn)研究。其中使用測(cè)量系統(tǒng)分析、過程能力分析、Minitab等軟件工具,強(qiáng)調(diào)了DMAIC在質(zhì)量管理中的應(yīng)用和效果。
1、定義階段
在實(shí)際生產(chǎn)過程中,根據(jù)G公司2020年8月份停線問題統(tǒng)計(jì),STN350工位累計(jì)報(bào)警停線288min,屬于裝配線停線TOP3的問題。根據(jù)擰緊曲線分析報(bào)警曲線最終扭矩偏低,低于70Nm(最終扭矩控制范圍是70-160Nm)。而且一次性合格率僅為98.03%。
利用高階流程圖(SIPOC)梳理流程,S供應(yīng)商是某螺栓供應(yīng)商及ATLAS公司。I輸入包括螺栓、半成品發(fā)動(dòng)機(jī)、操作工、擰緊程序等。P過程是放置螺栓,設(shè)備自動(dòng)擰緊。O輸出將螺栓擰緊至最終扭矩。C客戶是生產(chǎn)基地。
VOC轉(zhuǎn)化為CTQ,就是工位擰緊報(bào)警,原因是擰緊最終扭矩低于70Nm。先制定目標(biāo),現(xiàn)階段終擰緊一次性合格率為98.03%,目標(biāo)為終擰緊一次合格率為99.5%,考慮停線工時(shí)費(fèi)、電費(fèi)、螺栓成本的浪費(fèi),按照年產(chǎn)量20萬臺(tái)發(fā)動(dòng)機(jī)計(jì)算,預(yù)估節(jié)省收益為27.6萬元,項(xiàng)目計(jì)劃半年完成改善。
2、測(cè)量階段
公司會(huì)對(duì)擰緊設(shè)備進(jìn)行定期標(biāo)定,擰緊傳感器讀數(shù)與擰緊機(jī)讀數(shù)可靠,滿足擰緊軸擰緊精度≤3%的要求,因此設(shè)備測(cè)量系統(tǒng)滿足要求。
3、分析階段
通過整理現(xiàn)場(chǎng)缸蓋螺栓擰緊過程,從人機(jī)料法環(huán)測(cè)六個(gè)方面分析確認(rèn)問題的影響因子,如圖1所示。
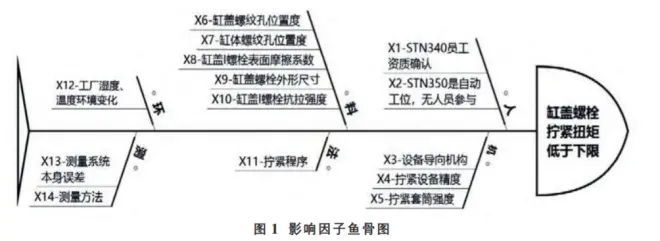
首先可以進(jìn)行快速排查如下:
X1-STN340員工資質(zhì),從現(xiàn)場(chǎng)人員技能矩陣可以看出,該崗位的員工均滿足三級(jí)上崗資質(zhì),X2-STN350工位是自動(dòng)工位,無人員參與。因此人為非關(guān)鍵因子。
X3-設(shè)備導(dǎo)向機(jī)構(gòu)確認(rèn),通過檢查設(shè)備日常點(diǎn)檢表,確認(rèn)導(dǎo)向定位工裝,缸體上導(dǎo)向銷限位工裝尺寸滿足使用要求,因此,此為非關(guān)鍵因子。
X4-擰緊軸精度,通過擰緊軸標(biāo)定記錄,精度滿足3%要求,此為非關(guān)鍵因子。X5-套筒精度,通過設(shè)備日常點(diǎn)檢表,確認(rèn)滿足檢測(cè)要求,因此X4和X5為非關(guān)鍵因子。
X6-缸蓋螺紋孔位置度排查,通過隨機(jī)抓取24組螺栓孔位置度的變量數(shù)據(jù)(標(biāo)準(zhǔn)為Φ0.6),利用mintab,計(jì)算的位置度Cpk=1.93>1.33,即缸蓋螺栓孔位置度非關(guān)鍵因子。
X7-缸體螺紋孔位置度,數(shù)據(jù)通過線上三坐標(biāo)測(cè)量?jī)x進(jìn)行測(cè)量并記錄在QDAS數(shù)據(jù)庫(kù)中,從QDAS中抓取數(shù)據(jù)讀取其Pok,滿足1.33的能力要求,因此缸體螺紋孔位置度為非關(guān)鍵因子。
X8-螺栓摩擦系數(shù),采用雙樣本T檢驗(yàn),從ATLAS系統(tǒng)中對(duì)兩種不同摩擦系數(shù)1、2,隨機(jī)抓取48組變量數(shù)據(jù),通過Mintab計(jì)算,得出P-value<0.05,表明缸蓋螺栓表面摩擦系數(shù)是顯著影響因子。如圖2所示。
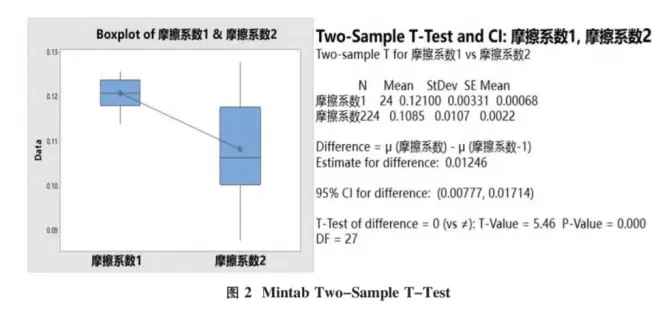
X9-缸蓋螺栓外觀尺寸,螺栓入廠會(huì)使用螺栓直線度檢具進(jìn)行檢測(cè)(標(biāo)準(zhǔn)為覬0.3),隨機(jī)抽取24組樣本,并利用minitab軟件計(jì)算其過程能力,Cpk=11.3,滿足過程能力要求,此為非關(guān)鍵因子。
X10-缸蓋螺栓抗拉強(qiáng)度,外檢會(huì)對(duì)各批次螺栓檢測(cè)器抗拉強(qiáng)度(標(biāo)準(zhǔn)為≥940MPa),隨機(jī)抽取144組數(shù)據(jù),使用Minitab進(jìn)行過程能力計(jì)算,得出Cp=1.54,Cpk=1.12,雖然過程能力不高,但出于可接受范圍,后續(xù)根據(jù)改進(jìn)效果考慮是否進(jìn)一步進(jìn)行提升。
X11-擰緊程序,缸蓋螺栓采用扭矩+轉(zhuǎn)角的擰緊工藝分為預(yù)擰緊和終擰緊兩部分如圖3,擰緊工藝所示。根據(jù)程序變更記錄,從2018年SOP開始,程序就沒有發(fā)生變化,而問題是8月發(fā)生,故此為非關(guān)鍵因子。從是否產(chǎn)生變化的角度,確認(rèn)X12工廠環(huán)境的溫度濕度,X13測(cè)量系統(tǒng)本身誤差,X14測(cè)量方法。此三項(xiàng)影響因子均未發(fā)生變化,因此暫時(shí)斷定為非關(guān)鍵因子。
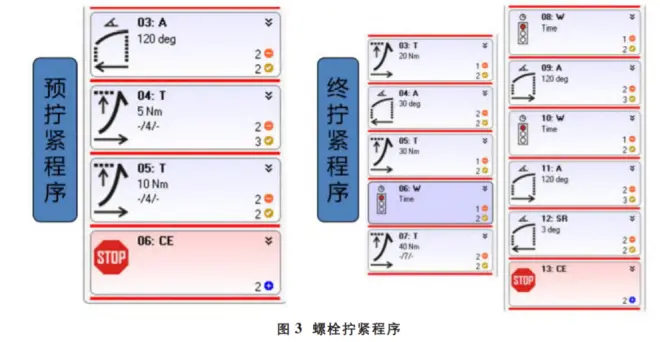
結(jié)論如下,X8缸蓋螺栓表面摩擦系數(shù)為關(guān)鍵因子,X10缸蓋螺栓抗拉強(qiáng)度為根據(jù)結(jié)果改善情況待判因子。下一步就缸蓋螺栓表面摩擦系數(shù)影響因子進(jìn)行分析。
根據(jù)物料追溯8月份問題較多的螺栓為供應(yīng)商4月份生產(chǎn),而其2月份生產(chǎn)的螺栓在工廠表現(xiàn)較好,針對(duì)這兩批次的螺栓進(jìn)行對(duì)比分析如表1。


分析對(duì)比兩種表面處理標(biāo)準(zhǔn)工藝,如表2,再分析兩種螺栓的過程能力差異,B50處理后螺栓摩擦系數(shù)Cpk=0.15,CP8000處理后螺栓摩擦系數(shù)Cpk=1.65如圖4。最后鎖定原因?yàn)楣?yīng)商表面工藝變更導(dǎo)致。
4、改進(jìn)階段
六西格瑪改進(jìn)階段就是優(yōu)化解決方案,確認(rèn)能夠滿足改進(jìn)目標(biāo)。供應(yīng)商將表面處理油劑從B50更換成CP8000,生產(chǎn)螺栓進(jìn)行現(xiàn)場(chǎng)驗(yàn)證?,F(xiàn)場(chǎng)驗(yàn)證結(jié)果如下,將改善的螺栓在現(xiàn)場(chǎng)進(jìn)行驗(yàn)證,隨機(jī)搜集2496份變量數(shù)據(jù),通過Minitab軟件進(jìn)行數(shù)據(jù)分析,樣本均值扭矩為101Nm,過程能力Cpk=2.26,如圖5。改善后,工廠持續(xù)生產(chǎn)2個(gè)月發(fā)動(dòng)機(jī)過程中,其終擰緊一次性合格率為99.7%,改善有效。
5、控制階段
控制階段是保證缸蓋螺栓終擰緊一次性合格率得到明顯改善。要求供應(yīng)商針對(duì)控制計(jì)劃進(jìn)行優(yōu)化,如表3所示;工廠內(nèi)部需保持實(shí)時(shí)監(jiān)控,要求外檢、工藝制定每周擰緊日?qǐng)?bào),匯報(bào)擰緊工位一次性合格率及原因分析,生產(chǎn)部門利用OEE日?qǐng)?bào),整理擰緊的主要問題。
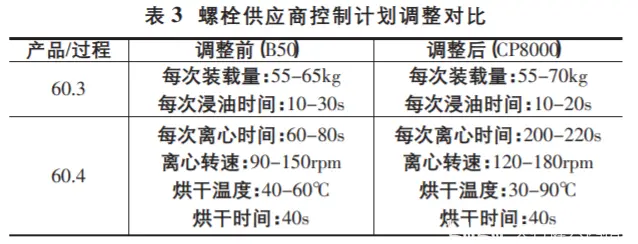
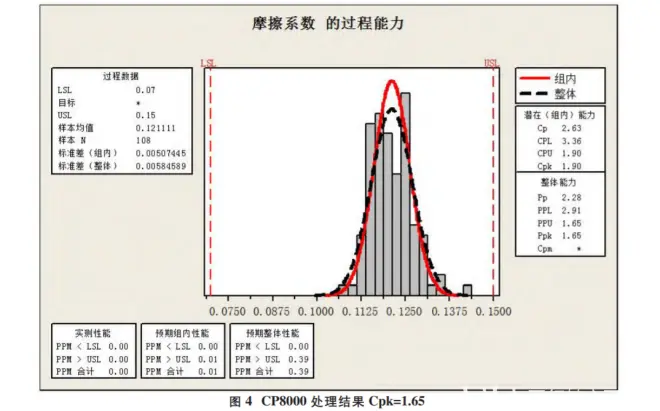
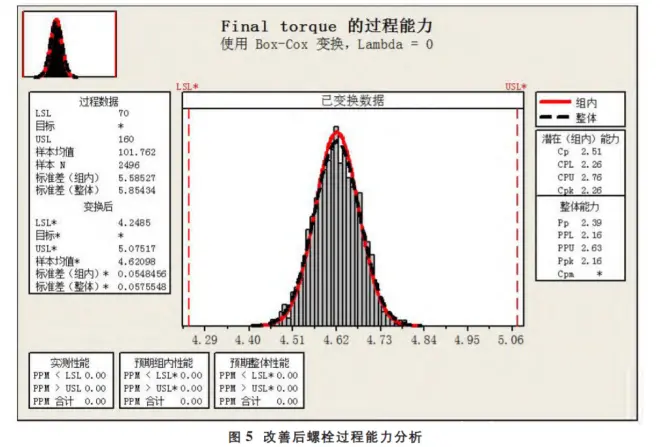
總結(jié)
針對(duì)裝配線缸蓋螺栓終擰緊一次性合格率偏低的問題,引入六西格瑪質(zhì)量管理工具,通過定義、測(cè)量、分析、改進(jìn)、控制的過程,挖掘根本原因,改進(jìn)優(yōu)化,達(dá)到精益求精的效果、消除了生產(chǎn)浪費(fèi),提高了生產(chǎn)效率。