高品質(zhì)的背后,你不知道的BMW質(zhì)量細(xì)節(jié) | 汽勢(shì)焦點(diǎn)
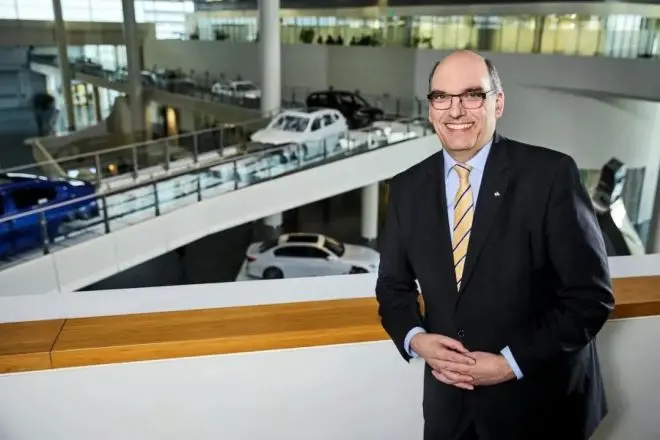
汽勢(shì)Auto-First|柴小娜
“質(zhì)量是維護(hù)顧客忠誠(chéng)最好的保證?!睂汃R深諳此道。
與此同時(shí),二十大“建設(shè)質(zhì)量強(qiáng)國(guó)”戰(zhàn)略提出,要深入實(shí)施質(zhì)量強(qiáng)國(guó)、制造強(qiáng)國(guó)戰(zhàn)略,堅(jiān)持推動(dòng)高質(zhì)量發(fā)展,制造業(yè)要實(shí)現(xiàn)智能化升級(jí)與綠色化轉(zhuǎn)型。由此可見,寶馬一直以來的高質(zhì)量發(fā)展之路,不僅契合了客戶需求,更在積極響應(yīng)國(guó)家高質(zhì)量發(fā)展號(hào)召中,始終與國(guó)家戰(zhàn)略高度契合。
正如華晨寶馬總裁兼首席執(zhí)行官戴鶴軒博士所言“ 作為一家以客戶為中心的企業(yè),我們致力于生產(chǎn)質(zhì)量卓越的產(chǎn)品以滿足中國(guó)消費(fèi)者的需求,而高質(zhì)量的生產(chǎn)制造體系是制造高質(zhì)量產(chǎn)品的前提。自2003年成立以來,華晨寶馬始終堅(jiān)持高質(zhì)量發(fā)展,在沈陽(yáng)建成了行業(yè)領(lǐng)先的智能制造生產(chǎn)基地,并將繼續(xù)致力于引領(lǐng)中國(guó)汽車行業(yè)的產(chǎn)業(yè)升級(jí)和綠色轉(zhuǎn)型?!?/p>
接下來,我們就深入到寶馬的研發(fā)、采購(gòu)、生產(chǎn)等各個(gè)環(huán)節(jié),看看寶馬如何生產(chǎn)出一臺(tái)讓用戶滿意,并與國(guó)家高質(zhì)量戰(zhàn)略高度契合的寶馬汽車。
數(shù)字化技術(shù)帶來“革命性”質(zhì)量改變
質(zhì)量代表了豪華,更代表安全,一輛車是否安全和可靠,都藏在細(xì)節(jié)里。數(shù)字化帶來的”革命性“質(zhì)量改變讓寶馬汽車受益無窮。比如寶馬100項(xiàng)AI技術(shù),尤其是AI視覺檢測(cè)技術(shù)的運(yùn)用,讓所有細(xì)微的瑕疵都無處遁形。
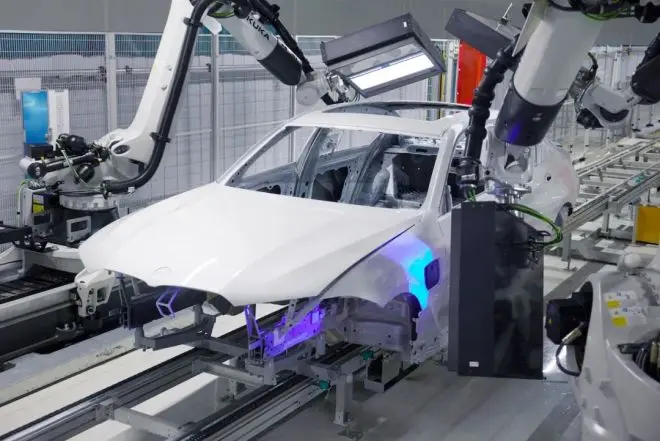
AI視覺檢測(cè)系統(tǒng)更是在整個(gè)生產(chǎn)、研發(fā)過程中大顯身手。沈陽(yáng)的研發(fā)中心擁有超過70個(gè)測(cè)試臺(tái)架,在開始量產(chǎn)前,將完成100多個(gè)涉及排放、安全、NEV檢測(cè)的檢查實(shí)驗(yàn)。
在華晨寶馬動(dòng)力總成工廠,AI視覺檢測(cè)系統(tǒng)被應(yīng)用于發(fā)動(dòng)機(jī)缸蓋質(zhì)量檢測(cè),據(jù)寶馬官方介紹,準(zhǔn)確率達(dá)到99.7%,該技術(shù)能自動(dòng)識(shí)別缸蓋表面微小瑕疵,將任何潛在瑕疵直接傳輸至檢測(cè)員,生產(chǎn)效率和檢測(cè)精度得到前所未有的提升。
里達(dá)工廠是寶馬集團(tuán)BMW iFACTORY生產(chǎn)戰(zhàn)略的最佳范例,它是一座真正的數(shù)字化汽車工廠,是“工業(yè)元宇宙”的先驅(qū)。里達(dá)工廠的車身車間用工業(yè)物聯(lián)網(wǎng)(IIoT)連接起每一件產(chǎn)品、每一個(gè)流程和每一位員工,從而實(shí)現(xiàn)高質(zhì)量、高效率的數(shù)字化生產(chǎn)。而人工智能、數(shù)據(jù)分析和算法的廣泛使用,將決策從“經(jīng)驗(yàn)驅(qū)動(dòng)”轉(zhuǎn)換為“數(shù)據(jù)驅(qū)動(dòng)”。
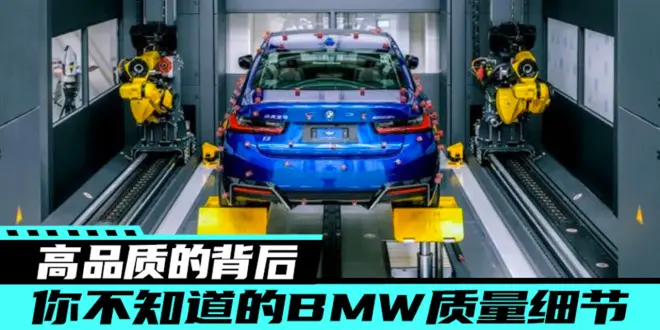
在里達(dá)工廠車身車間, 4個(gè)機(jī)器人自動(dòng)拍照,對(duì)比檢測(cè)每一道縫隙的寬窄,其精確度達(dá)到正負(fù)0.03毫米,相當(dāng)于一根頭發(fā)絲的五分之一。在涂裝車間,人工智能計(jì)算機(jī)視覺系統(tǒng)猶如孫悟空“火眼金睛”,在100秒內(nèi)可拍攝10萬張照片, 以確保部件和涂漆車身沒有任何微小瑕疵。
類似的細(xì)節(jié)和數(shù)字非常多,不必一一列舉。目前,沈陽(yáng)生產(chǎn)基地大約實(shí)現(xiàn)了約100項(xiàng)AI技術(shù)的應(yīng)用,任何一個(gè)微小的瑕疵都不放過,體現(xiàn)了這個(gè)豪華品牌的自我修養(yǎng)。
紀(jì)錄片《你不知道的BMW電動(dòng)車故事》中寶馬研發(fā)工程師連說“質(zhì)量第一,質(zhì)量第一,質(zhì)量第一,強(qiáng)調(diào)“永遠(yuǎn)在努力把每一臺(tái)車做到100分,用質(zhì)量去保證產(chǎn)品的一致性。”
精益確保高質(zhì)量生產(chǎn)平穩(wěn)運(yùn)行
如今,電動(dòng)化已成為汽車產(chǎn)業(yè)發(fā)展的主流賽道,寶馬也在持續(xù)加速電動(dòng)化轉(zhuǎn)型。數(shù)據(jù)顯示,今年前9個(gè)月,寶馬集團(tuán)在中國(guó)純電動(dòng)車型銷量同比增長(zhǎng)65%,保持強(qiáng)勁勢(shì)頭。到2025年年底,寶馬集團(tuán)計(jì)劃在全球交付200萬輛純電動(dòng)車。預(yù)計(jì)到2030年,集團(tuán)全球銷量至少50%將來自于純電動(dòng)車型。
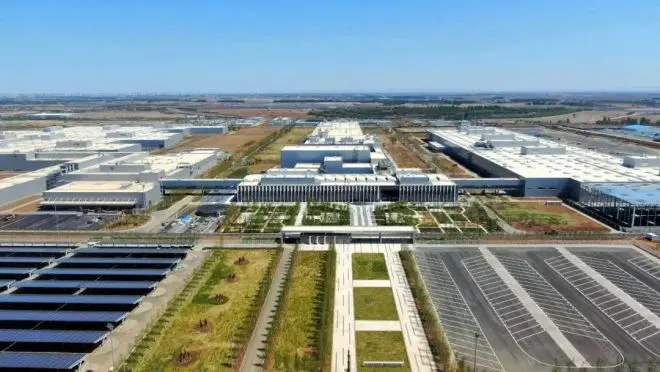
實(shí)現(xiàn)如此大規(guī)模的電動(dòng)化生產(chǎn),質(zhì)量到底是如何保障的?
眾所周知,“電”的控制與應(yīng)用,比起燃油來講要苛刻得多,這意味著電車的裝配工藝對(duì)于結(jié)構(gòu)化的要求更高,比如動(dòng)力電池的安裝,車輛各項(xiàng)功能的檢測(cè)也更為嚴(yán)格,這些都離不開iFACTORY身后“精益”的支持。好在生產(chǎn)的靈活性是寶馬集團(tuán)在制造領(lǐng)域最大的優(yōu)勢(shì)之一,特別是能夠在短時(shí)間內(nèi)根據(jù)需求調(diào)配資源并調(diào)整生產(chǎn)的能力,提升生產(chǎn)效率。
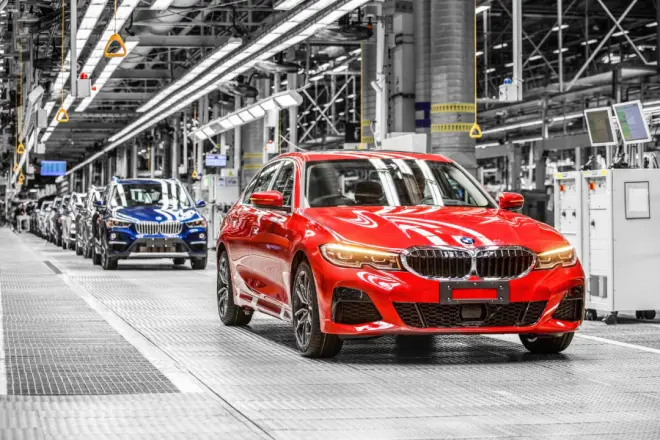
此外,“精益”的另一個(gè)特點(diǎn)就是其通過流程的標(biāo)準(zhǔn)化提升生產(chǎn)精確性,確保產(chǎn)品質(zhì)量。我們以車身強(qiáng)度舉例,車身在使用中承受著各種載荷,寶馬在車身強(qiáng)度方面有超過100年的技術(shù)積累,通過大量的實(shí)地極限測(cè)試,確保車身的強(qiáng)度、耐久性和剛度,保證駕乘人員的絕對(duì)安全。
據(jù)數(shù)據(jù)統(tǒng)計(jì),傳統(tǒng)白車身生產(chǎn)線投資4.6億美元,涂裝車間投資需要1億美元,這也是傳統(tǒng)制造車廠門檻高的原因之一。以里達(dá)工廠正在生產(chǎn)的i3為例,今天我們所能看到的白車身早已經(jīng)不再是簡(jiǎn)單的焊裝。它的白車身是由鋁、鋼等近30種材料組成的,同時(shí)根據(jù)不同部位、不同材質(zhì),為了提高車身強(qiáng)度,一共應(yīng)用了11種連接技術(shù)。
全新BMW i3是寶馬首款純電動(dòng)中型運(yùn)動(dòng)轎車,已經(jīng)正式在里達(dá)工廠投產(chǎn)。寶馬i3的設(shè)計(jì)理念是最大程度地運(yùn)用輕量化技術(shù)降低車身重量,從而增大電池容量。因此,寶馬i3前車身部分用了鑄鋁和鋁型材作為發(fā)動(dòng)機(jī)的支撐,據(jù)寶馬官方介紹,一是因?yàn)檐嚿磉\(yùn)動(dòng)過程中的剛性要求;二是因?yàn)檐囕v碰撞過程中產(chǎn)生的塑性變形。
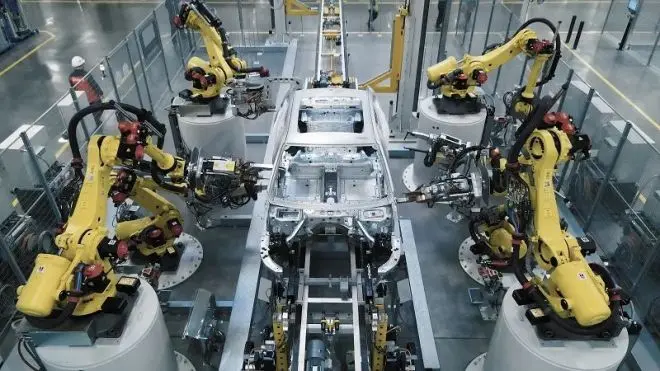
在碰撞過程中,彈性變形的能量需求和塑性變形的能量需求是不一樣的,當(dāng)材料產(chǎn)生塑性變形,它會(huì)吸收巨大的能量,這樣會(huì)保證乘客的安全?;诖隧?xiàng)考量,在i3后車身的部分,為了減輕重量并提升鋼性,也采用了這種鑄鋁材料,這樣在車的運(yùn)動(dòng)過程中,可以形象地感覺到寶馬車像一根扁擔(dān)挑了兩個(gè)板凳一樣。
這意味什么呢,只有在足夠的車身強(qiáng)度和駕駛技能足夠好的基礎(chǔ)上,才能夠保證駕駛者在時(shí)速70公里以上時(shí)有信心拐硬彎。
如果說成就一款經(jīng)典產(chǎn)品的關(guān)鍵是細(xì)節(jié),那壓死駱駝的最后一根稻草同樣來自被忽視的細(xì)節(jié)。從一串串?dāng)?shù)據(jù)來看寶馬電動(dòng)汽車的質(zhì)量生產(chǎn)細(xì)節(jié),明顯安心可靠,環(huán)節(jié)透明,流程清晰,每一輛寶馬電動(dòng)汽車其豪華和安全就隱藏在一個(gè)個(gè)細(xì)節(jié)中。
全價(jià)值鏈的質(zhì)量管控“立大功”
隨著多年對(duì)質(zhì)量方面的不懈探索,寶馬已構(gòu)建了一套貫穿全價(jià)值鏈的質(zhì)量管理,在研發(fā)、供應(yīng)鏈、生產(chǎn)等環(huán)節(jié)都制定了明確的流程和方法。寶馬認(rèn)為,研發(fā)與采購(gòu)是確保高質(zhì)量生產(chǎn)的基礎(chǔ)。
正如華晨寶馬技術(shù)和生產(chǎn)高級(jí)副總裁昆碩先生說:“通過iFACTORY生產(chǎn)戰(zhàn)略,我們致力于發(fā)展員工‘質(zhì)量第一’的理念和目標(biāo)明確的質(zhì)量工作——這些都基于實(shí)時(shí)的車輛數(shù)據(jù)分析和直接的客戶反饋。為了實(shí)現(xiàn)最高的客戶滿意度,我們?cè)谘邪l(fā)、采購(gòu) / 供應(yīng)商管理、生產(chǎn)部門和合作伙伴的共同努力下,保障產(chǎn)品擁有最好的質(zhì)量?!?/p>
在研發(fā)過程中,寶馬通過全面、嚴(yán)格的測(cè)試避免質(zhì)量問題。在沈陽(yáng)的寶馬研發(fā)中心,有超過70個(gè)測(cè)試臺(tái)架,在開始量產(chǎn)前,將完成100多個(gè)涉及排放、安全、NEV檢測(cè)的檢查試驗(yàn)。
眾所周知,近些年,不時(shí)出現(xiàn)電動(dòng)車輛起火的新聞事件,部分原因來自電池安全。在電動(dòng)化浪潮下,電池不僅占到整車成本的40%左右,安全更是消費(fèi)者心頭一大隱患。對(duì)于新能源純電動(dòng)車,寶馬設(shè)置了從電芯,電池模組,電池包到整車各級(jí)的苛刻測(cè)試,在華晨寶馬研發(fā)中心里涵蓋了128次機(jī)械測(cè)試、994次軟件功能測(cè)試,通過一層層測(cè)試,確保每一環(huán)節(jié)質(zhì)量的“零缺陷”。
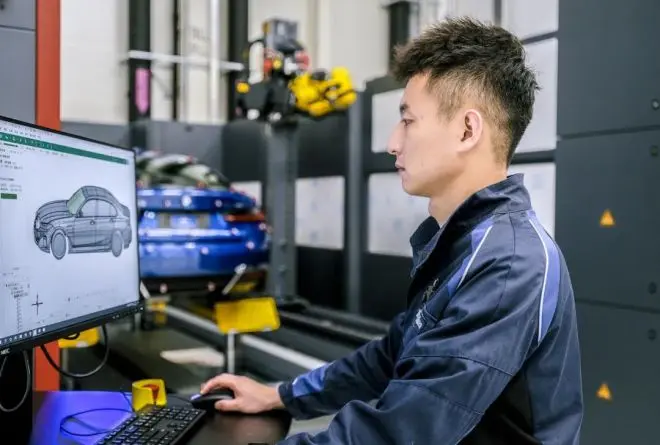
在供應(yīng)商質(zhì)量保障方面,寶馬更是獨(dú)樹一幟,樹立行業(yè)標(biāo)桿,將質(zhì)量從供應(yīng)商源頭抓起。目前,寶馬在中國(guó)有超過460 家本土供應(yīng)商,每家供應(yīng)商均需通過“質(zhì)量和零缺陷理念、次級(jí)供應(yīng)商管理、可持續(xù)發(fā)展、柔性生產(chǎn)系統(tǒng)、社會(huì)責(zé)任和成本效率”六大項(xiàng)考核。目前,“零缺陷”理念已成功滲透到整個(gè)供應(yīng)鏈體系,深入影響供應(yīng)商生產(chǎn)過程。與此同時(shí),寶馬注重增強(qiáng)員工質(zhì)量意識(shí)的培養(yǎng),每一個(gè)人都是質(zhì)量的責(zé)任主體。
同時(shí),在生產(chǎn)過程中,寶馬沈陽(yáng)生產(chǎn)基地形成了研發(fā)、采購(gòu)、生產(chǎn)一體化的獨(dú)特模式。這意味著,一方面,車輛在生產(chǎn)過程中一旦被監(jiān)測(cè)到潛在的質(zhì)量風(fēng)險(xiǎn),整車質(zhì)量管控部門第一時(shí)間響應(yīng),實(shí)施預(yù)防性管控;另一方面,迅速根據(jù)風(fēng)險(xiǎn)評(píng)估,確保不合格的零件或車輛不會(huì)繼續(xù)投入生產(chǎn)或抵達(dá)經(jīng)銷商。
至此,寶馬為質(zhì)量管控和保障設(shè)置了一個(gè)科學(xué)閉環(huán),每個(gè)環(huán)節(jié)從供應(yīng)商、原材料、生產(chǎn)、研發(fā)、測(cè)試、檢測(cè)等各司其職,最終實(shí)現(xiàn)“零缺陷”的高質(zhì)量汽車。
汽勢(shì)觀:至此,寶馬為質(zhì)量管控和保障設(shè)置了一個(gè)科學(xué)閉環(huán),每個(gè)環(huán)節(jié)從供應(yīng)商、原材料、生產(chǎn)、研發(fā)、測(cè)試、檢測(cè)等各司其職,最終實(shí)現(xiàn)“零缺陷”的高質(zhì)量汽車入華20年,作為國(guó)內(nèi)最早的汽車合資企業(yè)之一和最受中國(guó)市場(chǎng)和消費(fèi)者歡迎的豪華品牌,寶馬將“豪華”與“安全”刻在自己的DNA里,“質(zhì)量第一”理念是寶馬全面質(zhì)量文化的核心。一個(gè)個(gè)數(shù)字的背后,是寶馬在扎根中國(guó)的第20年里,繼續(xù)實(shí)現(xiàn)高質(zhì)量發(fā)展的有力表現(xiàn),也是在iFactory生產(chǎn)理念的支撐下,精益求精的不斷努力。