GH4133B合金航空發(fā)動機渦輪盤的疲勞斷裂與組織研究
摘?要:研究了不同應(yīng)力幅值下航空發(fā)動機渦輪盤用GH4133B合金的疲勞性能,并觀察了疲勞斷口形貌。結(jié)果表明, GH4133B合金的理論疲勞極限均值為239.5MPa; 應(yīng)力幅值為432MPa時, 疲勞斷口無明顯塑性變形, 斷口整體較
為平整;疲勞源位于試樣表面夾雜物處,在應(yīng)力作用下向心部擴展,后斷區(qū)位于外側(cè)邊緣,可見小面積剪切唇;合金中第二相顆粒在一定程度上會抑制疲勞裂紋的擴展,并減緩裂紋擴展速率。
眾所周知,航空飛行器的動力來源是發(fā)動機,發(fā)動機的性能直接決定了航空飛行器的續(xù)航能力和整體性能。渦輪盤作為整個發(fā)動機動力渦輪部分的核心部件,其在燃燒室內(nèi)受到高溫燃?xì)獾耐苿?,將燃?xì)獾臒崮苻D(zhuǎn)化為機械能,驅(qū)動發(fā)動機的運轉(zhuǎn)。因此,其制備工藝規(guī)范非常嚴(yán)格,可靠性主要取決于其坯件的冶金質(zhì)量,渦輪盤的完整性、均勻性和性能水平"。對于工程構(gòu)件,常見的是由于疲勞引起的
斷裂失效,約占斷裂事故的75%左右。尤其是隨著現(xiàn)代航空發(fā)動機的快速發(fā)展,發(fā)動機的轉(zhuǎn)速和渦輪泵溫度在不斷提高,發(fā)動機構(gòu)件中的工作應(yīng)力也在不斷發(fā)生變化,其面臨的疲勞失效問題愈發(fā)突出P3。因此,本文對航空發(fā)動機渦輪盤的疲勞性能及其微觀組織演變進行研究,以期為航空發(fā)動機渦輪盤疲勞斷裂機理研究提供參考。
1 試驗材料與方法
本文選用的材料為航空發(fā)動機渦輪盤用GH4133B合金,化學(xué)成分如表1。試樣取自渦輪盤件,所采用的熱處理工藝為:1075℃x8h空冷+745℃x15h空冷。
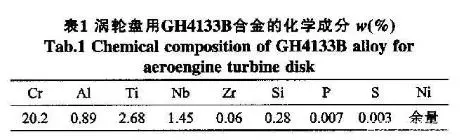
對航空發(fā)動機渦輪盤用GH4133B合金在ZWICK-ROELL疲勞試驗機上進行了高周疲勞試驗,疲勞試樣如圖1所示。波形為正弦波,頻率30Hz,應(yīng)力比為-1,參照航標(biāo)HB5287-1996閘,應(yīng)力幅為256-538MPa。采用S-4800型掃描電子顯微鏡觀察斷裂斷口。
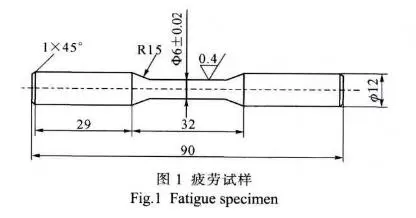
2 試驗結(jié)果及討論
表2為GH4133B合金不同應(yīng)力幅值的疲勞試驗結(jié)果及疲勞壽命的平均值和方差。采用三參數(shù)冥函數(shù)疲勞S-N表達式問:
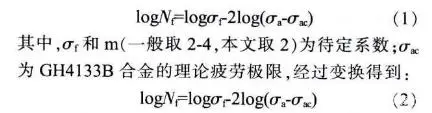
logN=logor2log(o, 0)其中,0,和m(一般取2-4,本文取2)為待定系數(shù):0為GH4133B合金的理論疲勞極限,經(jīng)過變換得到:ogN=logo-2log(a-0, )對不同應(yīng)力幅下的疲勞斷裂周次進行回歸處
理◎, 得到logos, 并由此計算得到理論疲勞極限o。從表2中可以看出,GH4133B合金的理論疲勞極限均值為239.5MPa, 方差為13.6MPa。應(yīng)力幅值為432MPa時, logN, 為5.06時第一組試樣斷裂, 遠低于其它幾組試樣以及平均值。圖1為應(yīng)力幅值為432MPa時疲勞斷口宏觀形貌。低倍形貌中可見,GH4133B合金斷口沒有發(fā)生明顯塑性變形,斷口較為平整,表現(xiàn)出脆性斷裂特征;疲勞源區(qū)主要分布在試樣表面,在外加應(yīng)力下逐漸向心部擴展,后斷區(qū)
位于外側(cè)邊緣處,同時可見小面積的剪切唇,如圖1(a)所示。裂源區(qū)可以發(fā)現(xiàn),在疲勞斷口源區(qū)中可見尺寸約為80um的凹坑,凹坑處原始夾雜物已經(jīng)發(fā)生了脫落,且源區(qū)較為粗糙,并有很多二次裂紋,源區(qū)附近可見疲勞擴展弧線,如圖1(b)。圖3為不同應(yīng)力幅值GH4133B合金疲勞斷口過渡區(qū)的SEM形貌。當(dāng)應(yīng)力幅值為462MPa時, 低倍下可見明顯的疲勞條帶,且在裂紋擴展過程中出現(xiàn)了“疲勞亮痕”,這種“疲勞亮痕”多出現(xiàn)在第二相顆粒的相界面處,是第二相顆粒在反復(fù)拉壓應(yīng)力作用下形成的,局部區(qū)域還可見少量韌窩和撕裂棱的存在, 如圖3(a) ; 高倍SEM形貌中可見河流狀花樣的存在, 如圖3(b) ; 當(dāng)應(yīng)力幅值為400MPa和256MPa時, 疲勞斷口過渡區(qū)中仍然可見撕裂棱和疲勞弧線,第二相顆粒上的疲勞條帶的寬度小于基體疲勞條帶寬度, 這與462MPa的斷口類似, 這主要是由于第二相起到了強化合金的作用,從而降低了裂紋的擴展速率。
圖4為應(yīng)力幅值為462MPa下渦輪盤用GH4133B合金疲勞斷口擴展區(qū)的SEM顯微形貌。可以看出,疲勞裂紋擴展區(qū)的疲勞弧線緊密,疲勞源位于疲勞弧線凹的一方,疲勞弧線的間距小于1jm;當(dāng)疲勞條帶在擴展過程中遇到第二相顆粒時,將在界面處形成微缺口,進而產(chǎn)生局部應(yīng)力集中,當(dāng)應(yīng)力足夠大時,在應(yīng)力集中處撕裂并形成二次裂紋,如圖4(b)所示。從這一角度出發(fā),第二相顆粒在一定程度上將抑制疲勞裂紋的擴展,起到減緩裂紋擴展速率的效果。
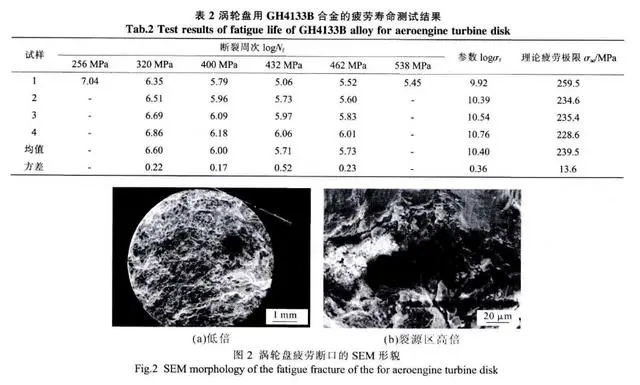

圖5為應(yīng)力幅值分別為256, 400和462MPa時GH4133B合金疲勞斷口瞬斷區(qū)的SEM顯微形貌。可以看出, 當(dāng)應(yīng)力幅值為256MPa時, 疲勞斷口瞬斷區(qū)中可見細(xì)小韌窩和撕裂棱,表現(xiàn)為韌性斷裂特征,在韌窩底部還可見細(xì)小第二相顆粒的存在, 整體表現(xiàn)為塑性變形特點; 400MPa時, 瞬斷區(qū)韌窩尺寸變小、變淺,同時還可見解理斷口形貌, 此時的斷裂方式為混合斷裂; 462MPa時,
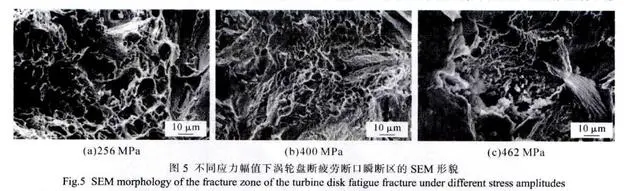
韌
窩數(shù)量進一步減小,且韌窩較淺,斷裂方式為準(zhǔn)解理斷裂。
3 結(jié)論
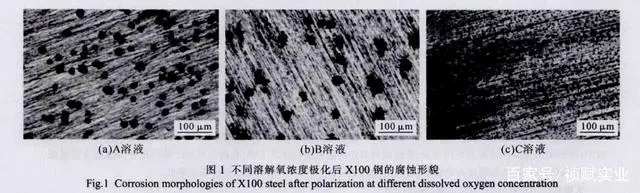
(1)航空發(fā)動機渦輪盤用GH4133B合金的理黑色腐蝕坑,大小不一;在B溶液中,黑色的腐蝕坑明顯減少;在C溶液中,基本上看不到腐蝕坑,只有一些深度很淺的坑分布在表面,腐蝕程度明顯依次降低。圖2給出了三種不同溶液下的動電位極化曲線??梢钥闯?,隨著溶液中氧含量的減少,曲線明顯的向上向左偏移,腐蝕電流密度明顯減小,通過分析其腐蝕電流密度分別為39.23、26.56、19.66pA/cm。從而其耐腐蝕性越來越好。圖3給出的是試樣在A、B、C溶液中腐蝕后的交流阻抗圖譜??梢钥闯?,整個阻抗圖譜是由低頻區(qū)域的收縮電容弧和高頻區(qū)域的壓扁容抗弧兩部分組成,低頻區(qū)域的收縮電容弧表明此時有腐蝕產(chǎn)
物覆蓋在電極上。并且隨著溶解氧含量的降低,高頻區(qū)域的容抗弧越大,這是因為在腐蝕過程中有腐蝕產(chǎn)物開始阻止腐蝕的進行。通過模擬的等效電路圖,得到的擬合結(jié)果列于表2,可以看到隨著溶液中氧含量的減少,n值由0.6468增加至0.7963,說明試樣也越來越耐腐蝕,表面質(zhì)量也越來越好。極化電阻的增加說明隨著氧含量的降低,試樣受到來自于腐蝕產(chǎn)物膜的阻力越來越大,這與極化曲線的分析結(jié)果是一致的。通過X射線衍射儀測得A、B、C三種不同氧含量的腐蝕產(chǎn)物圖譜如圖4所示,可以看出,氧含量不同,腐蝕產(chǎn)物及其含量是有很大的差別。A溶液中的腐蝕產(chǎn)物主要為Fe,O.,夾雜著一些Fe(OH)z;在B溶液中主要為Fe OOH和少量的F eCO, ; 在C溶液中的產(chǎn)物主要為F eCO, 和少量的Fe(HCO) 。分析可知,對于A溶液,氧含量較充足,陰極發(fā)生吸氧反應(yīng),生成OH,陽極生成Fe",從而得到Fe(OH)a,F(xiàn)e(OH),繼續(xù)和O,發(fā)生反應(yīng)得到Fe(OH)s,F(xiàn)e(OH) , 分解為Fe OOH, Fe OOH繼續(xù)和Fe*得到了Fe,O.,并且氧含量越高,F(xiàn)e,O,越多。所得的Fe(OH);產(chǎn)物是非常疏松多孔的組織,對于電極的保護是有限的,所以腐蝕速率較高。對于B溶液,氧含量較低,陰極的吸氧反應(yīng)受到抑制,F(xiàn)e(OH),也不能完全
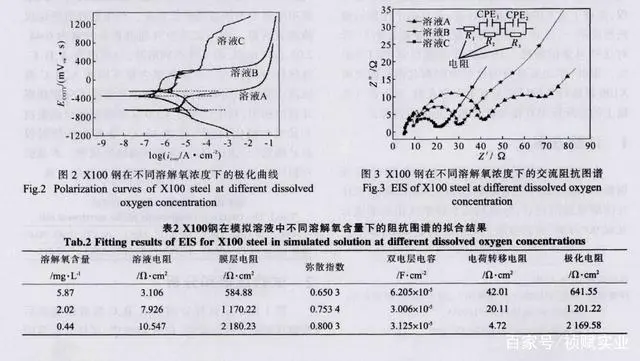