寶馬BMW工廠的管理精髓
所有國家里面,德資企業(yè)應該是最看重“過程”的,在對過程要求幾近苛刻的汽車行業(yè),更是如此。
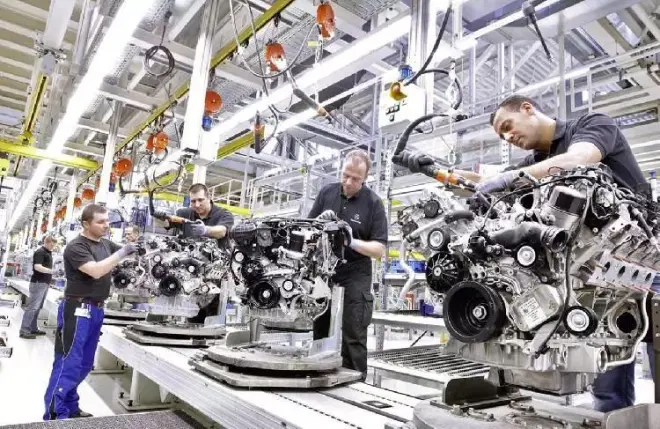
德國也因此誕生了眾多叱咤風云的汽車品牌。BMW(寶馬),便是其中血緣純正的代表。今天,通過BMW在“過程”方面的要求,讓我們一起領略德系過程管理的精髓。
VPSVPS(增值生產(chǎn)系統(tǒng)),是BMW多年前提出的一個概念,這幾年在國內(nèi)開展的如火如荼。
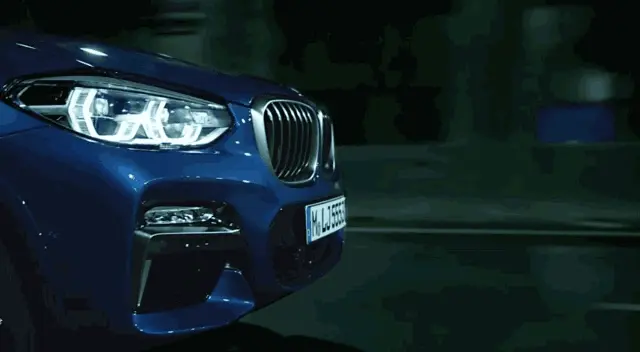
VPS,要求在寶馬集團的全部生產(chǎn)過程中,要最大限度地創(chuàng)造價值,從供銷商到經(jīng)銷商,在有利的環(huán)境規(guī)劃中,在生產(chǎn)和以顧客為目標的銷售和生產(chǎn)的流程中,要把浪費減少到最低限度。價值什么樣的過程創(chuàng)造價值呢?即適合于用戶準備好付款的過程,所有不創(chuàng)造價值的過程均為浪費。創(chuàng)造價值的過程即客戶愿意掏錢買單的過程。
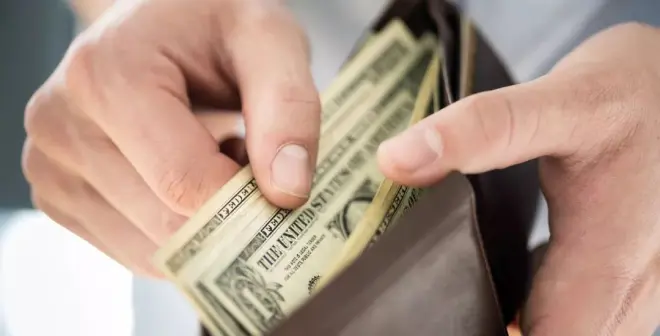
這樣的過程多嗎?BMW分析了一個的常見工位。
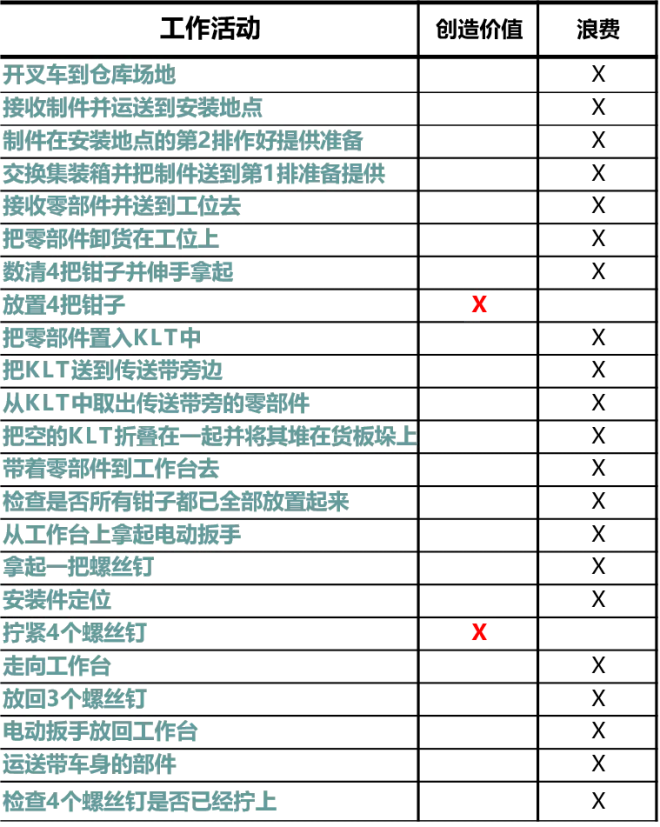
20多個"過程",客戶真正愿意買單的只有兩個,其他的都是浪費。
浪費一看浪費這么多,BMW覺得得歸個類,于是有了公開的和隱蔽的浪費概念。
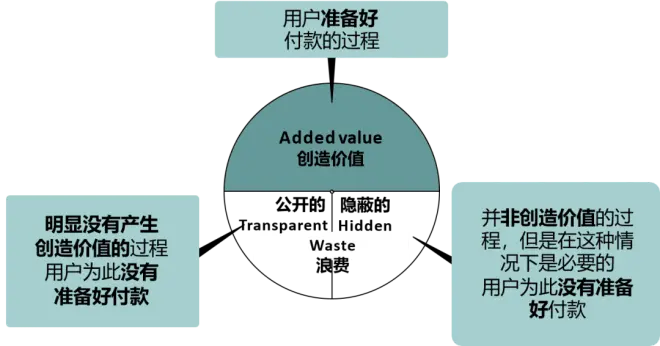
其中,隱蔽的浪費即哪怕是浪費,可不得不浪費。在此基礎上,又分析了上面提到的工位。
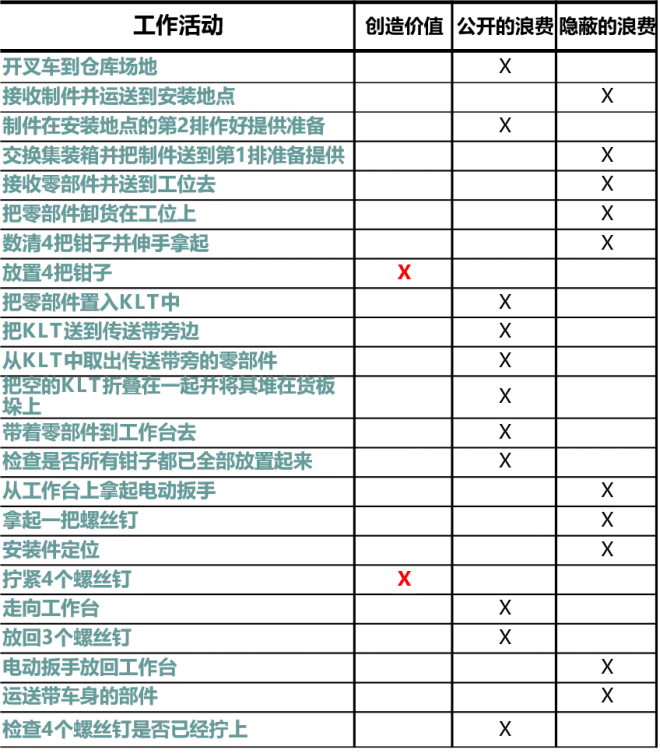
解決思路既然,隱藏的浪費是必須的,那我們降低浪費的對象只能在公開的浪費方面。
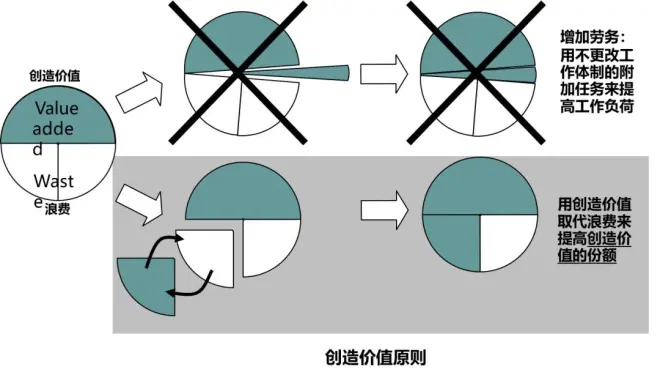
如何減低呢?
我們需要關注過程的10原則。
VPS過程10原則
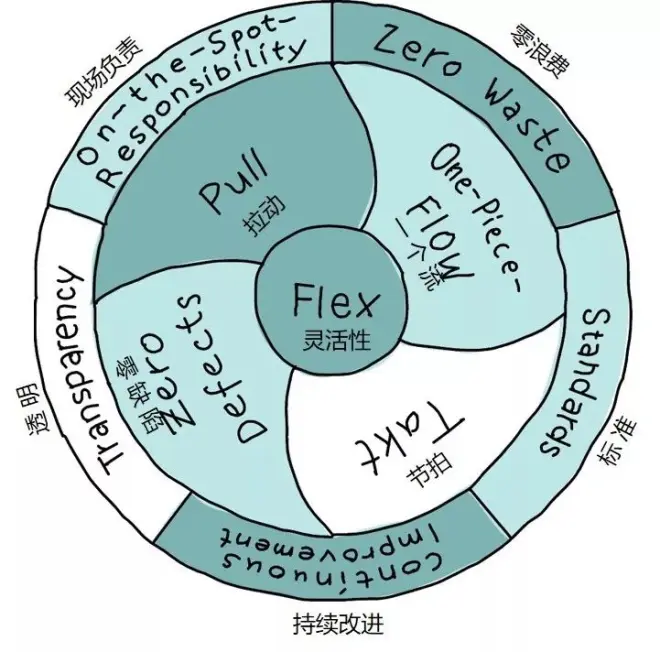
VPS的核心是提高靈活性。內(nèi)圈描述了我們產(chǎn)品設計和運行的強制性要素。外圈代表了VPS保證的基礎,同時又保證了可持續(xù)性。
01 |?靈活性靈活性是核心優(yōu)勢。—能迅速而容易地使改型車一體化。—通過作業(yè)時間平衡總數(shù)波動。—暫短的準備階段有可能改變訂單。—生產(chǎn)用簡單手段進行自控。—所有產(chǎn)品都能隨時在沒有額外花費 情況下制作。
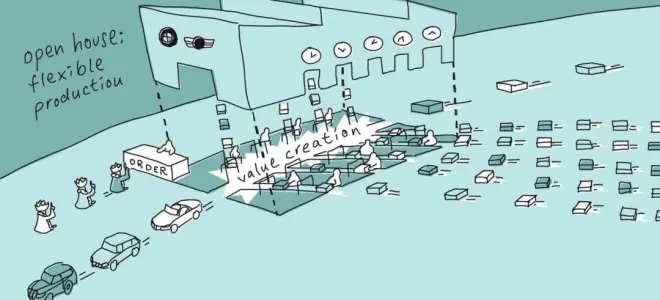
周轉(zhuǎn)時間是靈活性的關鍵。降低周轉(zhuǎn)時間,減少存貨水平和緩沖量可提高過程高度靈活性和高度的用戶為導向。
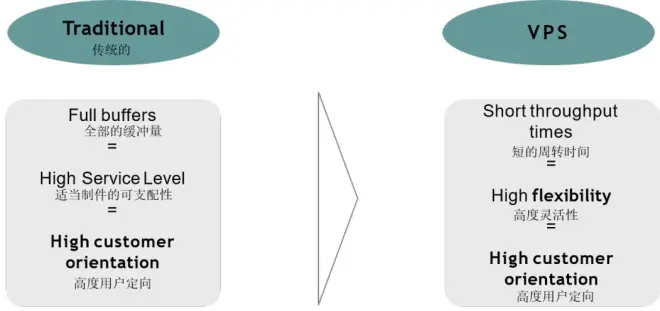
實例:
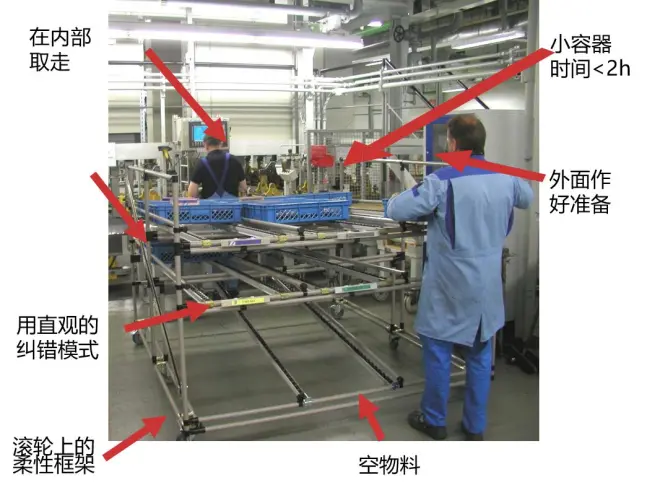
02?|?一物流物料以“勻速”流動。生產(chǎn)從一個加工步階到另一個加工步階無堆裝階段(緩沖)地流動著。預裝件無延遲地流入主流水線。
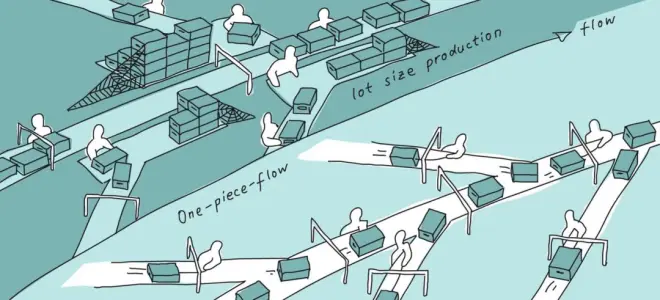
—物料和信息的流動是可以覺察到的。
—過程勻速地運行,無停頓或匆忙。—人們可以對各種要求作出迅速反應。?—工廠平面圖按物料流動來布置,物料流動決定工廠的設計參數(shù)。—沒有一個過程需要“安全網(wǎng)”,緩存系統(tǒng)被撤銷。
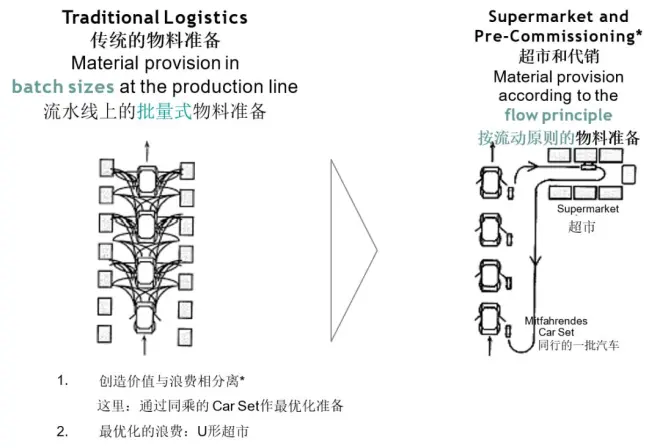
實例:
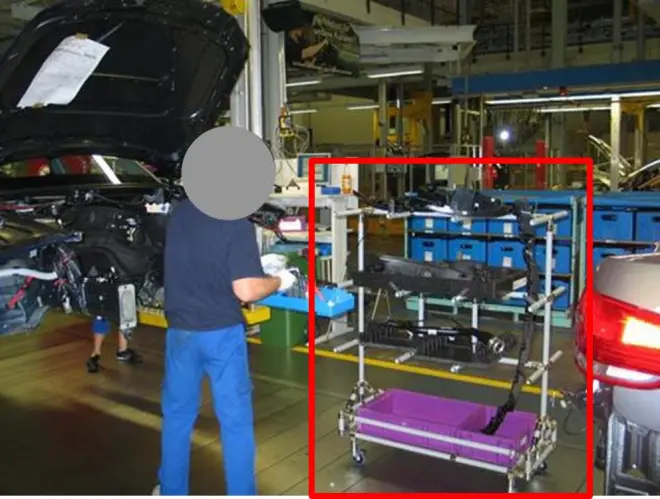
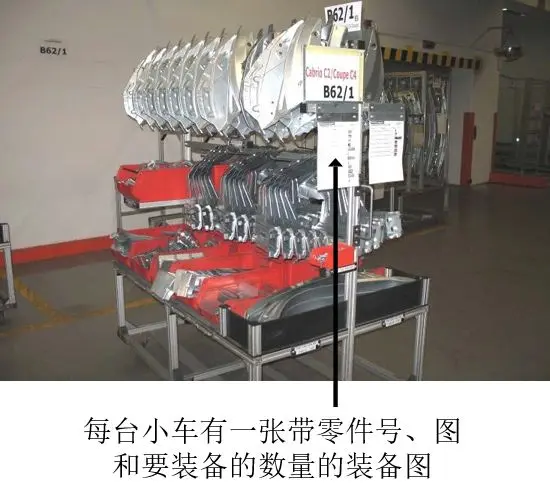
03?|?節(jié)拍—生產(chǎn)系統(tǒng)在協(xié)調(diào)中進行。—物料按生產(chǎn)節(jié)奏進行供應。—組裝(作為與客戶的接口)決定了步伐。—包括廠外供應商在內(nèi)的全體過程伙伴均受節(jié)拍影響。—拉平的生產(chǎn)導致均勻的節(jié)拍。—所有過程均將在節(jié)拍時間內(nèi)結(jié)束。
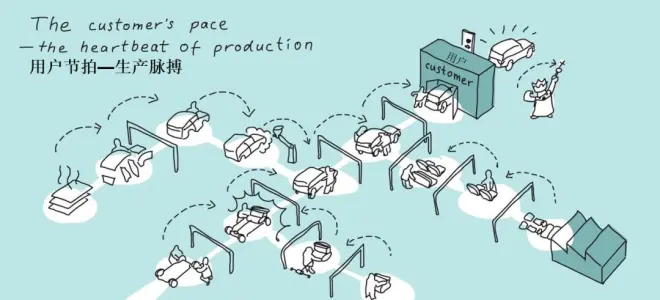
節(jié)拍使生產(chǎn)流程同步。
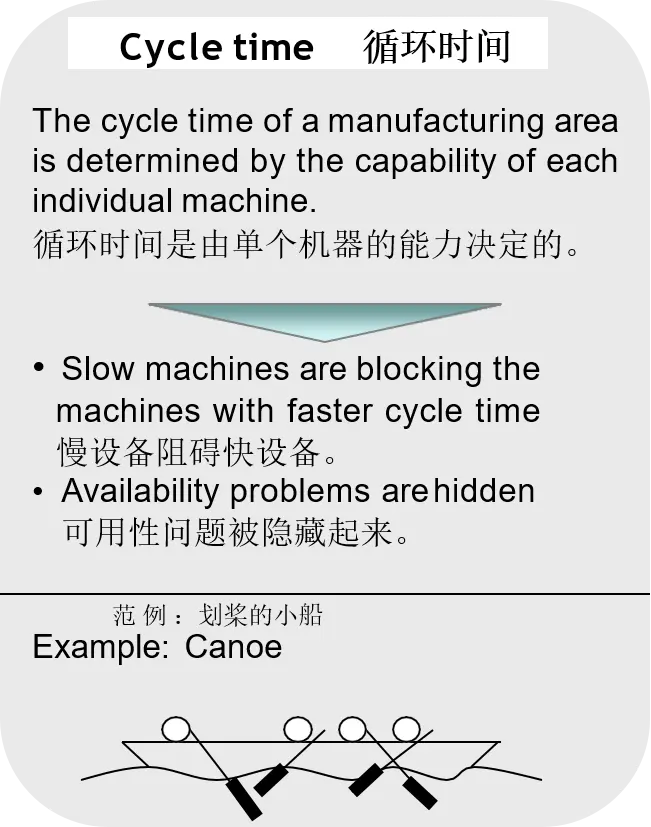
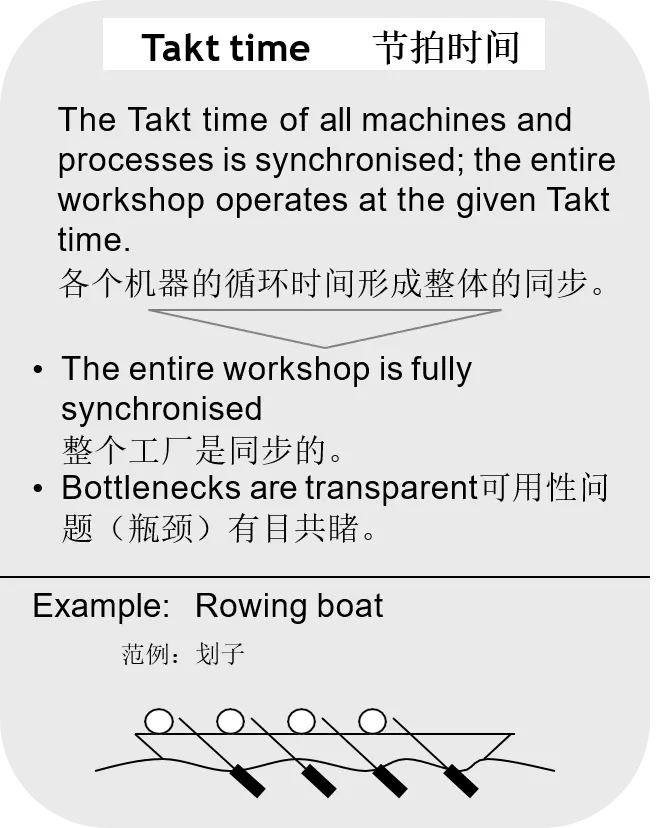
節(jié)拍的目的是工廠的同步。所有過程(物流也在內(nèi))將用用戶節(jié)拍 — 工廠的脈搏來操控。根據(jù)魚骨原理的同步過程。
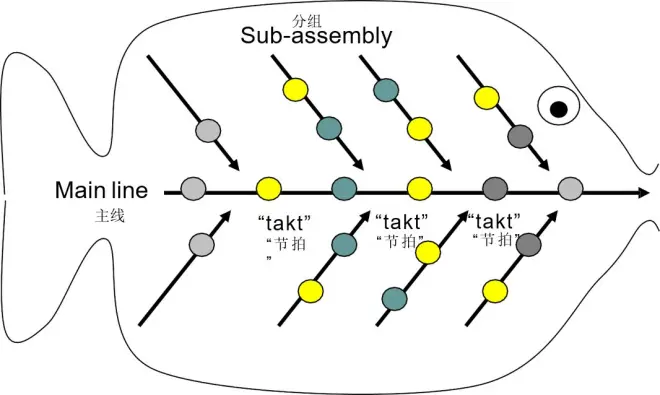
(精益管理咨詢公司www.kaizenjit.com精益生產(chǎn)管理咨詢培訓)
實例:
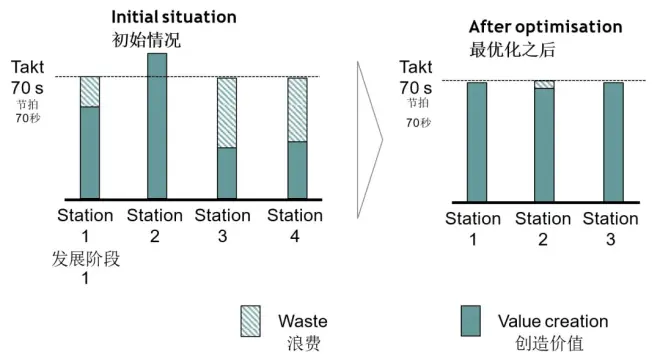
04?|?拉動原則—只有缺少什么,才須向那里補給什么。—短的反應時間比高機械負荷還重要。—信息流動簡單,明了和快捷。—物料流動被設計成“向上游”流動。—存貨降到最少量。—1個批次規(guī)模是目標。
兩種邏輯:
按拉動原則,只有當用戶消費什么時,生產(chǎn)或物流才發(fā)生。
實例:
05?|?零缺陷認清問題越晚,浪費就越大。因此對所有過程都要預先調(diào)查可能出現(xiàn)的問題。有缺陷的就不要轉(zhuǎn)送,要揭示缺陷的成因并當場排除。每個缺陷都是改進的動機。
—沒有缺陷轉(zhuǎn)達給下一個過程。—要使缺陷和薄弱處透明。—識別缺陷之前就避免缺陷。—立刻就地解決問題。—要根除每個缺陷的原因。—每個缺陷都為改進提供了空間。
實例:復合產(chǎn)品來自簡單設備
零缺陷:停歇的打磨線
06?|?透明目前的產(chǎn)量多高?為什么會出現(xiàn)未預料的問題?干脆把標準和企業(yè)狀況展示出來并直接告知 有關人員,使每個人都能最快地對變化作出 反應。
—標準和企業(yè)狀態(tài)目視化。—每次目視化顯示都有一個定義的發(fā)送 者和接收者。—信息用簡單的手段表達。—明確的描述會導致過程可靠地實施。
實例:目視化管理顯示
07?|?持續(xù)改進每個人在他的崗位上都要愉快地為改革出一份力。每個過程都能夠作改進并且每項改進都注入某個標準中。做一點改進是我們日常工作的出發(fā)點。
—每個過程都是能夠改進的。—每項改進都終結(jié)在某個標準中。—每個標準又是繼續(xù)改進的出發(fā)點。—努力爭取改進對于每個人都是理所當 然的事情。—給改進過程打上的印記是創(chuàng)造價值。—每個人都愉快地參與其中。
只有與持續(xù)改進相聯(lián)合的規(guī)劃才能帶來持久的效率提升。
實例:放水閥的安裝,你有何改進建議?
08?|?標準化好的過程以標準為依據(jù)。標準要盡量簡單并從而簡便工作。統(tǒng)一性將知識捆扎在一 起,使它能夠得以有意義地進一步發(fā)展。這使經(jīng)驗交流變得容易一些。
—優(yōu)異的過程、結(jié)構(gòu)、裝置均以標準為依據(jù)。—標準要盡量簡單并便于工作。—員工的創(chuàng)造力在不斷地提高標準。—標準不是聰明才智的對立面。—上級索取標準并自己應用這些標準。
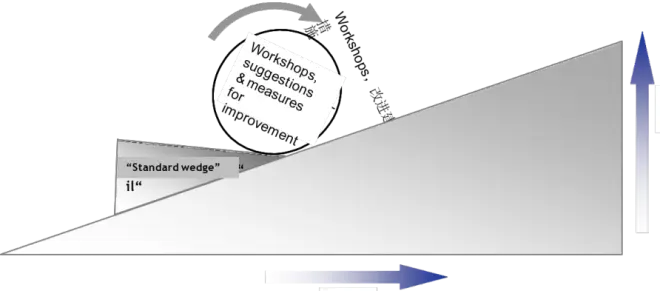
每個過程都遵循某個標準。標準應被證實有效。?每項改進都以一個新的標準結(jié)束,這個新標準又是繼續(xù)改進的出發(fā)點。
實例:標準化劃線
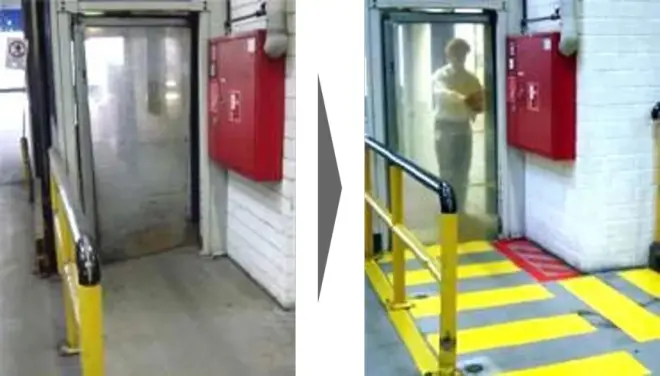
09?|?現(xiàn)場負責每個人都知道自己對企業(yè)成功應作出什么努力。凡是真正盡職盡責的人,就會在現(xiàn)場找到要共同參與設計的工作。
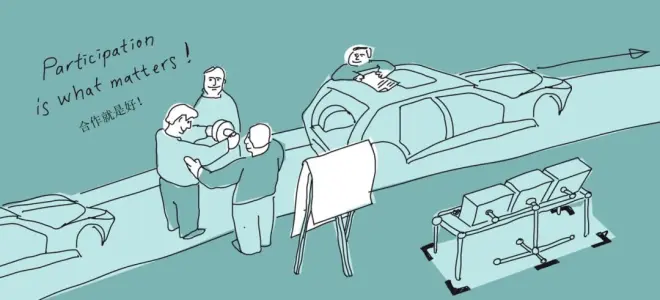
—在距創(chuàng)造價值盡量近的地方負起責任。—每個人都知道自己的目標并正在個人負責地致力于目標的實現(xiàn)。—每個人都了解他對企業(yè)成功應作的貢 獻。—必要的指標由小組現(xiàn)場記錄。—每個問題都將在其出現(xiàn)地得到解決。—要在過程現(xiàn)場進行管理。
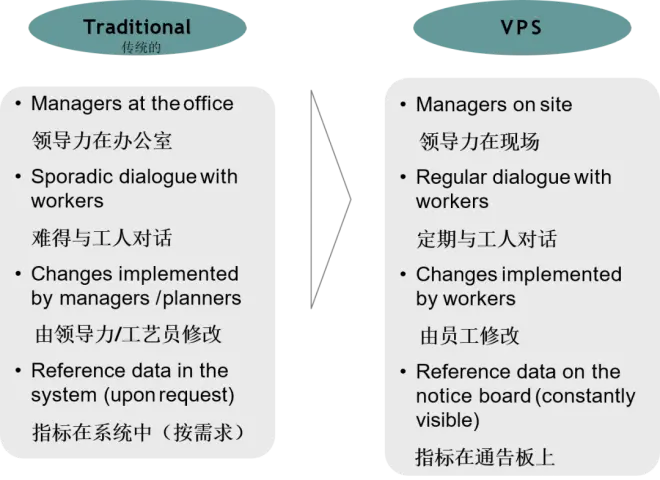
實例:指標在現(xiàn)場
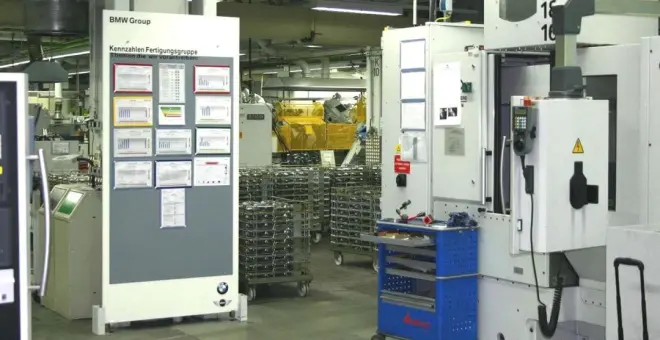
10?|?零缺陷每種勞務、每件工具、每種大量物料, 凡是超過絕對必需就都是浪費。我們從確實必要的、 不能再免除什么的每一過程確認是否是完美的過程。
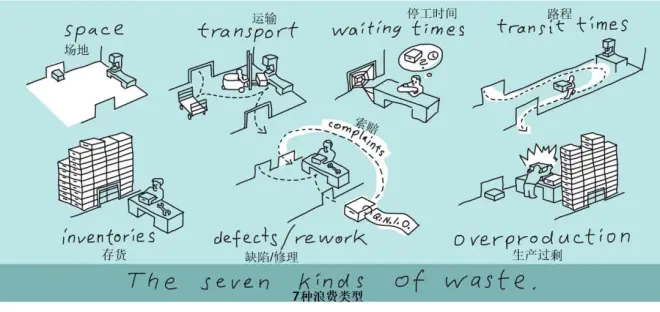
—企業(yè)的各個領域都將識別浪費。—領導力對浪費有一個正確的看法。—全體員工持續(xù)地減少浪費。—有計劃地揭示浪費并清除之。—如果是個完美的過程就不能再刪去什么。
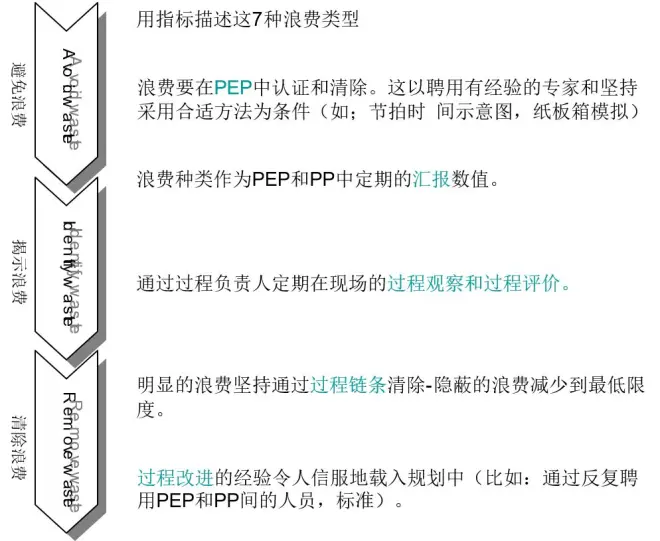
實例:車身制造中的紙板集裝箱模擬
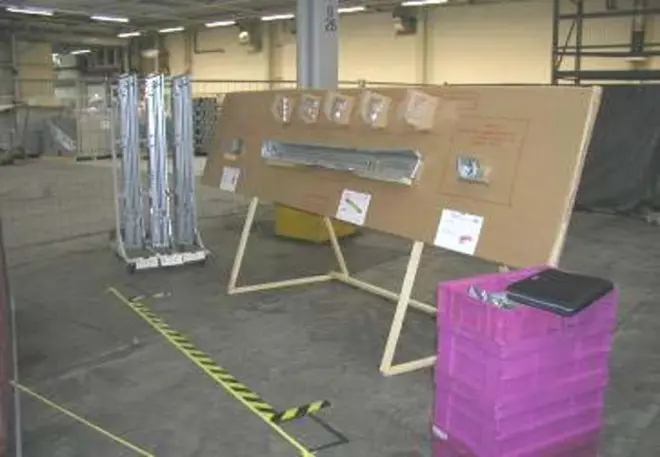
版權申明:精益爭霸尊重版權并感謝每一位作者的辛苦付出與創(chuàng)作;如文章視頻、圖片等涉及版權請第一時間聯(lián)系,我們將根據(jù)提供的證明材料確認版權并立即刪除!