車身一體化壓鑄產(chǎn)業(yè)研究報(bào)告
當(dāng)今,汽車制造業(yè)正朝著更輕、更高效、更可持續(xù)的方向發(fā)展。在這一輕量化的趨勢中,車身一體化壓鑄技術(shù)成為了一項(xiàng)引人注目的創(chuàng)新。通過將多個(gè)鋁合金零部件整合為一個(gè)無縫結(jié)構(gòu),一體化壓鑄技術(shù)不僅減輕了整車重量,還提高了結(jié)構(gòu)強(qiáng)度和安全性能。它不僅在汽車行業(yè)取得了顯著的進(jìn)展,而且正在改變著整個(gè)行業(yè)的制造方式和設(shè)計(jì)理念。
當(dāng)下汽車輕量化的發(fā)展推動(dòng)鋁合金材料需求提升,但連接工藝及結(jié)構(gòu)件性能制約鋁合金材料在汽車中的應(yīng)用。真空高壓鑄造技術(shù)是鋁合金車身結(jié)構(gòu)件生產(chǎn)最優(yōu)選,采用超高真空高壓壓鑄工藝的一體化壓鑄,能夠?qū)崿F(xiàn)多個(gè)鋁合金零件的一體化成型;
一體化壓鑄由于高度集成,免去了“沖焊”環(huán)節(jié),與傳統(tǒng)制造相比,一體化壓鑄在制造成本、人工成本等方面更低,同時(shí)縮短了車型的開發(fā)周期,提升了生產(chǎn)效率和原材料回收利用率,應(yīng)用范圍也從傳統(tǒng)結(jié)構(gòu)件(減震塔、前后縱梁)發(fā)展到下車體(后底板、前機(jī)艙、前底板),最后到白車身;
一體化壓鑄的產(chǎn)業(yè)鏈上游包含材料、設(shè)備、模具供應(yīng)商,中游包括各類壓鑄件零部件廠商(第三方和主機(jī)廠自研),下游應(yīng)用包括國內(nèi)外的主機(jī)廠,上游技術(shù)壁壘主要包括以下幾點(diǎn):
1)材料:免熱處理合金是一體化壓鑄的基礎(chǔ),有助于提高一體化壓鑄的良品率,從而降低成本,免熱處理合金主要分為鋁硅及鋁鎂兩大系列,鋁硅系列是當(dāng)前主流。
2)設(shè)備:大噸位壓鑄機(jī)有助于壓鑄件結(jié)構(gòu)和尺寸的進(jìn)一步突破,是行業(yè)未來的發(fā)展方向。小鵬G6前后一體式鋁壓鑄是目前行業(yè)內(nèi)最先進(jìn)的車身技術(shù),最大壓鑄力可達(dá)12,000噸。
3)模具:一體化壓鑄技術(shù)對模具的尺寸、密封性等都有著較高的要求,同時(shí)開發(fā)周期長、開發(fā)成本高,行業(yè)競爭格局集中,主要包括廣州型腔、寧波賽維達(dá)等公司。
特斯拉在2020年率先應(yīng)用一體化壓鑄后底板,國內(nèi)蔚來、小鵬、吉利等車企率先實(shí)現(xiàn)了一體化壓鑄的量產(chǎn),國外車企將在2025年實(shí)現(xiàn)量產(chǎn)。一體化壓鑄工藝作為未來重要的發(fā)展趨勢,企業(yè)正在加速進(jìn)行布局,預(yù)計(jì)2025年國內(nèi)一體化壓鑄件市場規(guī)模將接近300億元,年均復(fù)合增長率達(dá)176%。
在雙碳背景下,輕量化是汽車行業(yè)的發(fā)展趨勢。根據(jù)相關(guān)數(shù)據(jù)顯示,汽車整備質(zhì)量每減少 100kg,百公里油耗可降低0.3-0.6L?!豆?jié)能與新能源汽車技術(shù)路線圖2.0》的發(fā)布也對汽車油耗及輕量化系數(shù)提出了嚴(yán)格要求。2035年對于傳統(tǒng)能源乘用車和純電動(dòng)乘用車的輕量化系數(shù)分別相比2019年的基數(shù)下降25%和35%。
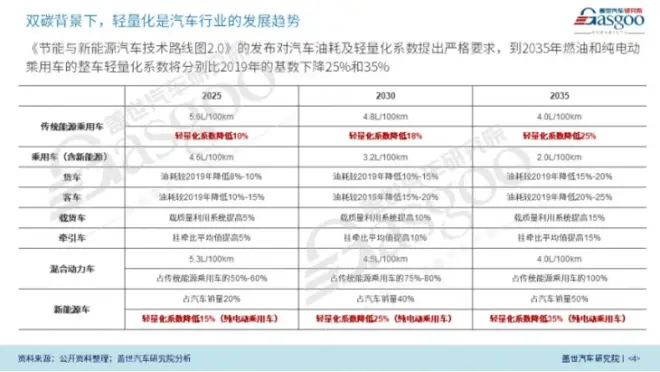
目前汽車輕量化的技術(shù)路徑主要包括零部件輕量化、電器輕量化和車身輕量化。其中,車身輕量化主要從材料、結(jié)構(gòu)、工藝三方面改進(jìn),當(dāng)前的主要輕量化措施是采用輕質(zhì)材料。鋁合金材料具有輕質(zhì)、抗拉強(qiáng)度高、回收性好、耐腐蝕、可塑性強(qiáng)、工藝相對成熟等特點(diǎn),材料密度顯著低于高強(qiáng)度鋼,成本及工藝難度優(yōu)于鎂合金和碳纖維,是當(dāng)前技術(shù)工藝下最具性價(jià)比及可行性的輕量化材料。
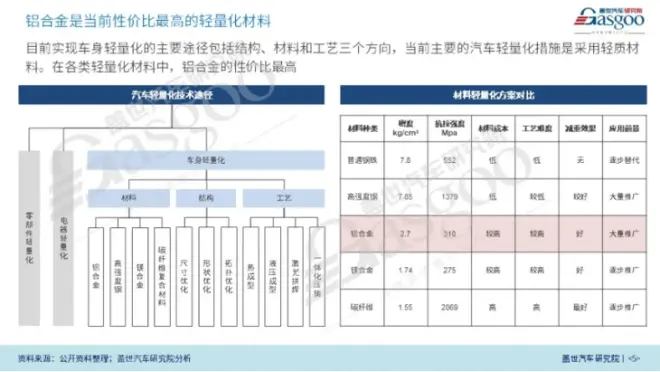
目前鋁合金已廣泛應(yīng)用于轉(zhuǎn)向節(jié)、控制臂、副車架、電機(jī)殼、電池盒等部件,但鋁合金車身的制造工藝復(fù)雜度遠(yuǎn)超鋼制車身,需要多種連接技術(shù)進(jìn)行組合,大大提升了生產(chǎn)的難度和整車的制造成本。
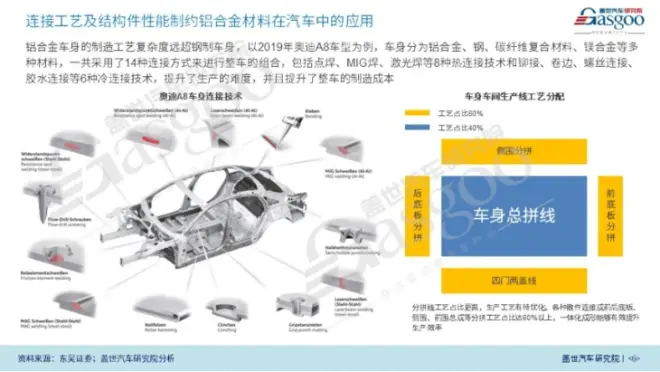
鋁合金零部件的主要成型工藝包含了鑄造、鍛造和擠壓。壓力鑄造主要分為高壓鑄造、低壓鑄造、差壓鑄造等。其中,低壓鑄造與差壓鑄造多用底盤區(qū)域,而高壓鑄造因加工效率高,加工零部件壁厚小等特點(diǎn),在車身中的運(yùn)用越來越多,是未來的發(fā)展方向。真空高壓鑄造能有效消除高壓鑄造工藝下的氣孔現(xiàn)象,同時(shí)塑形更為精準(zhǔn),是鋁合金車身結(jié)構(gòu)件生產(chǎn)最優(yōu)選,一體化壓鑄采用超高真空高壓壓鑄工藝,能夠?qū)崿F(xiàn)多個(gè)鋁合金零件的一體化成型。
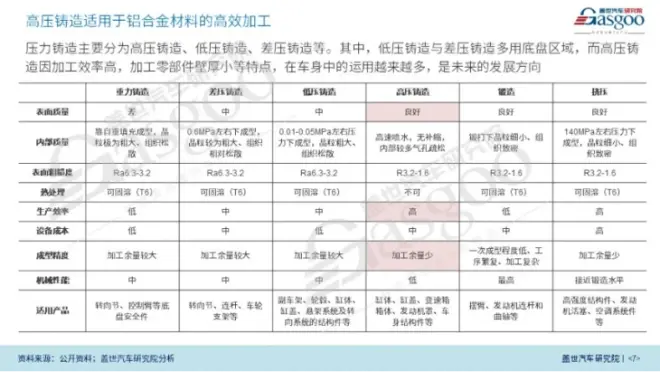
汽車傳統(tǒng)制造工藝主要由“沖壓、焊接、涂裝、總裝”四大環(huán)節(jié)組成,一體化壓鑄免去了“沖焊”環(huán)節(jié),彌補(bǔ)了鋁合金結(jié)構(gòu)件在傳統(tǒng)汽車生產(chǎn)工藝下的一些弊端,同時(shí)在成本、效率、精度、安全性及輕量化方面帶來了更多優(yōu)勢。
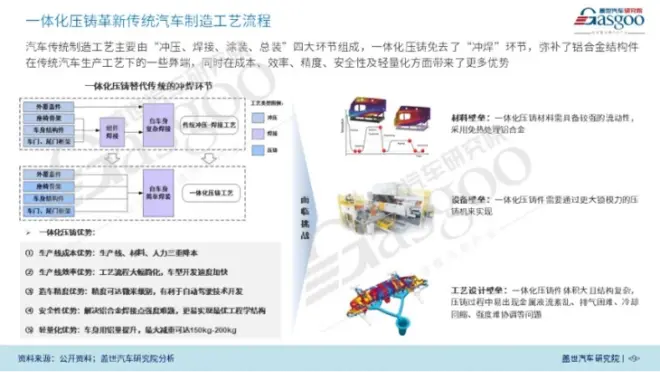
一體化壓鑄從傳統(tǒng)結(jié)構(gòu)件(減震塔、前后縱梁)發(fā)展到下車體(后底板、前機(jī)艙、前底板),最后到白車身,對應(yīng)單車價(jià)值量和壓鑄機(jī)的噸位也在持續(xù)提升。特斯拉于2016年開發(fā)出了用于一體式壓鑄技術(shù)的鋁合金配方,2019年提出“一體鑄造”技術(shù),2020年的特斯拉電池日發(fā)布會(huì)上,馬斯克稱特斯拉ModelY將采用一體壓鑄生產(chǎn)車身后底板總成。目前特斯拉的一體化壓鑄后底板與前機(jī)艙已實(shí)現(xiàn)量,一體化下車體即將量產(chǎn),未來向前后車身一體化+CTC方向發(fā)展。