生產(chǎn)效率提高20%,奧迪怎么做到的?
一個多世紀(jì)以來,流水線生產(chǎn)是汽車產(chǎn)業(yè)制造的主要生產(chǎn)模式。但如今隨著產(chǎn)品多樣化、個性化的用戶需求日益增加,汽車組裝的流程和部件越來越復(fù)雜,嚴(yán)格遵循生產(chǎn)步驟的流水線方式面臨窘境。
為此,奧迪推出全球首個汽車行業(yè)模塊化組裝系統(tǒng)。
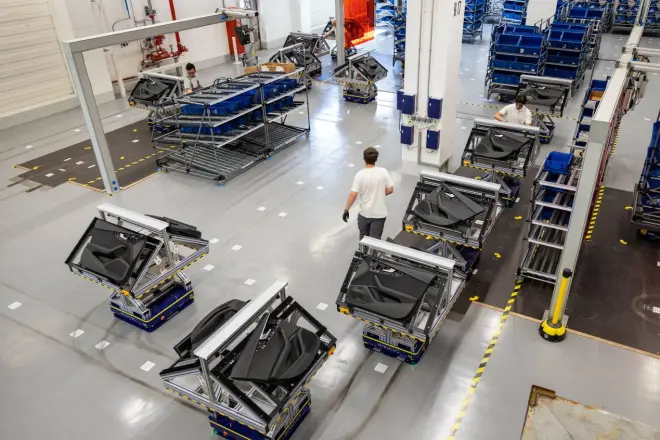
作為一種新的生產(chǎn)線補充形式,工人將在“生產(chǎn)島”組裝配件,不受周期時長的限制。此外,鑒于零部件種類的多樣,奧迪還應(yīng)用自動導(dǎo)引車(AGV),遵循“貨到人”的原則,為工作站點提供所需材料。
日益復(fù)雜的產(chǎn)品與用戶需求正在改變現(xiàn)代化生產(chǎn)。汽車廠商必須不斷提高生產(chǎn)的靈活性,以適應(yīng)特定的用戶需求、應(yīng)對短期市場變化,以及解決可持續(xù)性問題。
由于在傳統(tǒng)的裝配流水線中,每個產(chǎn)品在每個站點都有統(tǒng)一的加工時間,嚴(yán)格的生產(chǎn)流程難以滿足定制化的生產(chǎn)需求。相比之下,模塊化組裝不設(shè)流水線和固定的生產(chǎn)速度,可更加高效運作。
取代傳統(tǒng)流水線的全新動態(tài)組裝流程,將隨站點次序和站點不同加工時間的變化而變化。
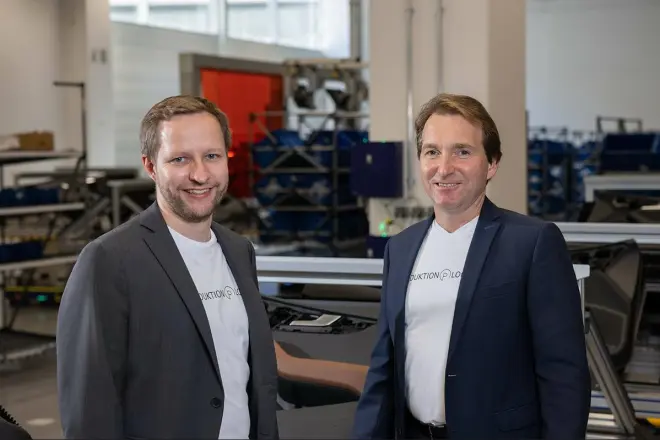
在奧迪英戈爾施塔特工廠,奧迪生產(chǎn)實驗室項目經(jīng)理Wolfgang Kern的團(tuán)隊正將這種模塊化組裝理念(虛擬流水線)應(yīng)用于內(nèi)飾門板預(yù)裝環(huán)節(jié),為后續(xù)推廣打下基礎(chǔ)。
“模塊化組裝是我們針對未來生產(chǎn)需求的有效解決方案之一。為減輕員工工作負(fù)擔(dān)、提升工作效率,我們還引入了先進(jìn)的數(shù)字技術(shù),進(jìn)一步提高靈活性?!眾W迪汽車股份公司管理董事會生產(chǎn)和物流董事葛惟柯(Gerd Walker)表示,“與此同時,這一項目也是彰顯奧迪開放創(chuàng)新文化的典型案例。憑借敏捷的團(tuán)隊合作,我們正積極開創(chuàng)智慧互聯(lián)的先進(jìn)生產(chǎn)模式?!?/p>
在項目試點的過程中,專家們在驗證模塊化組裝系統(tǒng)的可行性、挖掘其未來應(yīng)用潛力的同時,個人能力也得到了提升。
這種靈活系統(tǒng)的另一個重要優(yōu)勢是,奧迪可以雇用因身體條件限制不能在生產(chǎn)線上工作的殘障人士?!拔覀兡軌蚋鶕?jù)他們的自身情況設(shè)計工作環(huán)境,而這在流水線生產(chǎn)模式中是不能全面體現(xiàn)的,”Wolfgang Kern 說,“我們在生產(chǎn)過程中使用了更高靈活度的自動化技術(shù),來減輕員工們的工作負(fù)擔(dān)。”得益于任務(wù)處理的多樣化,員工不再具有統(tǒng)一的工作時間,所有人的工作量也得到減輕,這一點也符合人體工程學(xué)推崇的“以人為本”的理念。
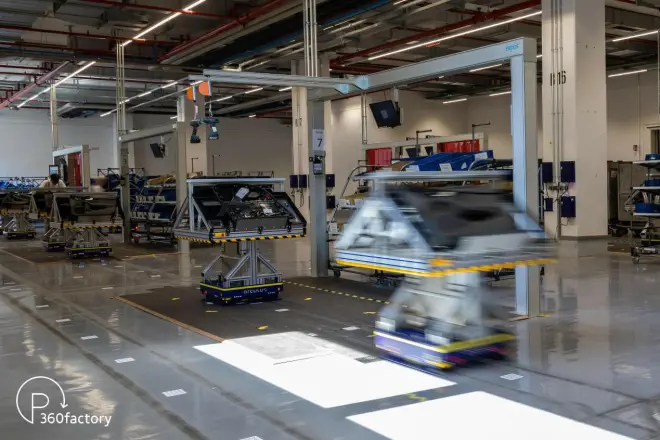
智能化的自動導(dǎo)引車確保生產(chǎn)靈活性
在試點項目中,工作任務(wù)不再遵循統(tǒng)一的順序。相反,它們的順序被靈活安排,以滿足特定需求。門板將被自動導(dǎo)引車直接運送到所需部件的各個站點。
例如,一個站點負(fù)責(zé)車燈所需的電纜和照明元件組裝,無需安裝車燈的門板便會繞過該站。而另一個負(fù)責(zé)組裝后門遮陽板的站點則可能成為其下一站。由于流水線預(yù)先設(shè)定了節(jié)奏,此前這項任務(wù)必須由兩到三個人分擔(dān),這讓工作效率低下,并可能影響質(zhì)量。
此外,當(dāng)某項任務(wù)在同一站點排隊時,自動導(dǎo)引車會自動將產(chǎn)品送至下一個等待時間較短的站點。整個“生產(chǎn)島”的工作站點布置會進(jìn)行周期性檢查和調(diào)整?!芭c現(xiàn)有的組織方式相比,這種由智能自動引導(dǎo)帶來的靈活性是一個重要進(jìn)步?!盬olfgang Kern強調(diào)。與傳統(tǒng)流水線不同,獨立的工作站點和模塊化組裝系統(tǒng)并非為滿足固定生產(chǎn)需求,而是確保在一定生產(chǎn)能力區(qū)間內(nèi)更加靈活、更加高效地運營。
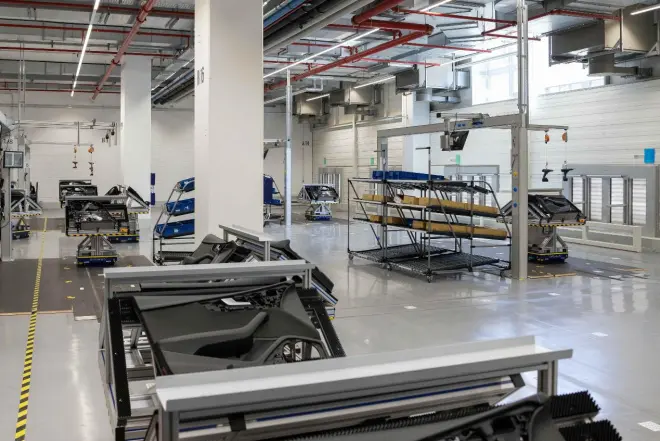
物流和質(zhì)量管理流程的高效整合
在零部件組合變化豐富的情況下,“貨到人”原則是最佳解決方案。例如,自動導(dǎo)引車會將分類正確的門板電纜線零部件運送到工人面前,在他們?nèi)∽咚璨考?,剩余部件則回到備用位置等待下一次組裝,因為通常情況下不同的門板會使用不同的零部件組合。
自動導(dǎo)引車提供分類好的零部件,取代了原本上游的分揀工作。由中央計算機控制的自動導(dǎo)引車借助無線電網(wǎng)絡(luò)能夠精準(zhǔn)定位到厘米。相機檢測也可以整合到質(zhì)量管理流程中,與傳統(tǒng)的流水線相比,這種方式能夠更快速、更容易地檢測異常,從而減少不可預(yù)見的額外工作。
“我們正以精益生產(chǎn)為原則,將傳統(tǒng)流水線的高度分工性與集成管理的系統(tǒng)性相結(jié)合,不斷探索如何借由物聯(lián)網(wǎng)驅(qū)動的數(shù)字生產(chǎn)系統(tǒng),實現(xiàn)更加高效的運營?!盬olfgang Kern解釋道。
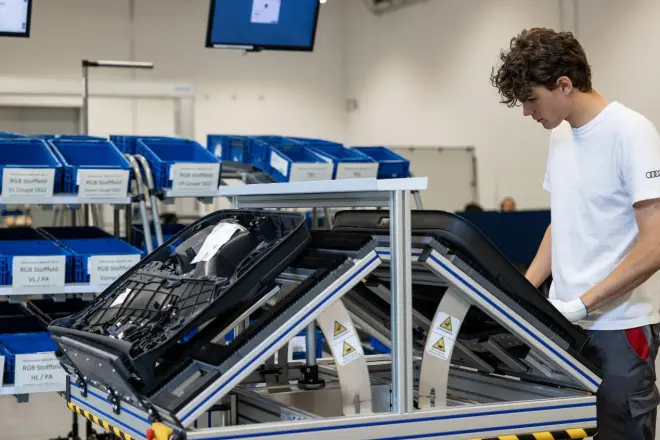
生產(chǎn)效率提高約20%
該試點項目提供了十分有價值的成果,將幫助奧迪工程師進(jìn)一步開發(fā)衍生應(yīng)用程序?!耙詣?chuàng)造價值和靈活自動化為導(dǎo)向,我們的生產(chǎn)時間大幅減少,生產(chǎn)效率提高了約20%。”Wolfgang Kern表示。
團(tuán)隊的下一步工作是將模塊化組裝系統(tǒng)更大規(guī)模地應(yīng)用到預(yù)裝環(huán)節(jié)中,實現(xiàn)更大范圍的靈活高效生產(chǎn)?!叭∠潭魉€,設(shè)立獨立工作站點,讓產(chǎn)線重組更加容易?!钡靡嬗陟`活的硬件和自動導(dǎo)引車,工人們通常只需要調(diào)整相應(yīng)軟件便可。與前后互聯(lián)的流水線相比,可變動的工作站可以更輕松地滿足不同產(chǎn)品的獨特生產(chǎn)需求。