《Nat. Commun.》:多相結(jié)構(gòu)鋁箔負(fù)極
一、研究背景
為了滿足長程電動汽車和電動飛行的需求,下一代電池必須具有更高的能量密度和更高的安全性。固態(tài)電池(SSBs)可以使用新型高容量電極材料,同時(shí)避免使用易燃的液態(tài)電解質(zhì)。鋰金屬負(fù)極因其電極電勢低、理論容量高(3861 mAh g-1)而被廣泛研究用于固態(tài)電池。然而,與界面不穩(wěn)定性和鋰絲穿透導(dǎo)致短路有關(guān)的挑戰(zhàn)已被證明極難解決。
在低電位下與鋰合金化的材料("合金負(fù)極")因其高鋰存儲容量和減緩細(xì)絲生長而成為鋰金屬的一種有吸引力的替代品。數(shù)十年來,人們一直在研究硅等合金負(fù)電極在鋰離子電池中的應(yīng)用,目前,人們正在將少量的硅用于提高石墨基鋰離子電池負(fù)電極的容量。然而,合金負(fù)極在與鋰反應(yīng)的過程中會發(fā)生顯著的體積和結(jié)構(gòu)變化,從而導(dǎo)致固體電解質(zhì)界面(SEI)過度生長,并由于表面尺寸的持續(xù)變化而加速電池在液態(tài)電解質(zhì)中的失效。
雖然硅是迄今為止最受關(guān)注的材料,但其他合金負(fù)極材料也能顯著提高性能。20 世紀(jì) 70 年代,人們首次將鋁作為鋰存儲電極進(jìn)行研究。鋁鋰化后形成的 β-LiAl 相的理論比容量為 990 mAh g-1,體積變化率為 96%,低于硅 310% 的體積變化率。最重要的是,鋁是一種豐富的商品金屬,以鋁箔的形式制造具有成本效益;直接使用鋁箔負(fù)極可提高電池的能量密度,同時(shí)還可消除與傳統(tǒng)石墨漿鑄造和溶劑回收相關(guān)的成本。鋁箔還可同時(shí)充當(dāng)活性鋰存儲介質(zhì)和集電器,進(jìn)一步提高比能量/能量密度。然而,在使用非水性電解質(zhì)溶液的電池中,鋁基箔在實(shí)際條件下的性能較差。鋁電極的降解被認(rèn)為是由于液態(tài)電解質(zhì)中孔隙的形成和 SEI 的生長、鋰的擴(kuò)散捕集以及機(jī)械斷裂造成的。
與鋰離子電池相比,固態(tài)電池具有完全不同的化學(xué)機(jī)械環(huán)境。例如,固態(tài)電解質(zhì)(SSE)不會流動以潤濕體積變化的負(fù)極顆粒表面,這可能會穩(wěn)定 SEI 的形成。事實(shí)上,與使用非水性電解質(zhì)溶液的電池相比,使用硅基負(fù)極的固態(tài)電池最近顯示出更好的循環(huán)穩(wěn)定性。此外,采用各種合金負(fù)極(包括硅和鋁)的固態(tài)電池可以獲得更高的能量密度和比能量(圖 1a、b),甚至接近過量鋰金屬固態(tài)電池的能量密度和比能量。然而,最近大多數(shù)合金負(fù)極固態(tài)電池都采用了鑄造顆?;驈?fù)合電極,在概念上與傳統(tǒng)的鋰離子電池電極相似??紤]到 SSB 不同的化學(xué)機(jī)械環(huán)境,其他電極概念可能對長期耐久性也是可行的,包括開發(fā)致密箔電極。與鋰金屬進(jìn)行物理合金化的厚(>100μm)銦或鋁箔已被用作 SSB 負(fù)極,以充當(dāng)鋰匯,但這些厚箔有顯著過量的材料,導(dǎo)致能量密度低,無法實(shí)際使用。此外,避免使用鋰金屬進(jìn)行預(yù)鋰化有利于電池的規(guī)?;a(chǎn)。
二、研究成果
在此,美國喬治亞理工學(xué)院Matthew T. McDowell團(tuán)隊(duì)證明了采用致密鋁基負(fù)極的固態(tài)電池能夠在不預(yù)鋰化的情況下,以商業(yè)相關(guān)的面積容量(2-5 mAh cm-2)和箔厚度(30 μm)進(jìn)行穩(wěn)定的電化學(xué)循環(huán)。鋁電極和Al94.5In5.5電極與全電池 SSB 及 Argyrodite 硫化銀電解質(zhì)(Li6PS5Cl)結(jié)合在一起,這些電池在 25 °C、電流密度高達(dá) 6.5 mA cm-2?的條件下實(shí)現(xiàn)了數(shù)百次穩(wěn)定循環(huán)。盡管在循環(huán)過程中體積發(fā)生了變化,但鋁基電極仍能保持機(jī)械完整性,沒有形成明顯的內(nèi)部孔隙,其中由于內(nèi)部孔隙表面的過度SEI生長,在約70次循環(huán)中發(fā)生故障,這與使用非水電解質(zhì)溶液的電池的表現(xiàn)形成了鮮明對比。添加約5at.%的銦以形成分層多相微結(jié)構(gòu),可改善速率行為、初始庫侖效率和達(dá)到的容量。這些性能的提高得益于分布式鋰化銦相以最小的過電位促進(jìn)了鋁的(脫)鋰化反應(yīng),以及高鋰離子擴(kuò)散率的銦鋰相減輕了鋰捕獲。這些結(jié)果表明,鋁基負(fù)極可以在固態(tài)結(jié)構(gòu)中實(shí)現(xiàn),并為提高性能提供了微結(jié)構(gòu)設(shè)計(jì)指南,從而有可能實(shí)現(xiàn)高能量密度電池,避免與鋰金屬負(fù)極相關(guān)的退化難題。相關(guān)研究工作以“Aluminum foil negative electrodes with multiphase microstructure for all-solid-state Li-ion batteries”為題發(fā)表在國際頂級期刊《Nature Communications》上。祝賀
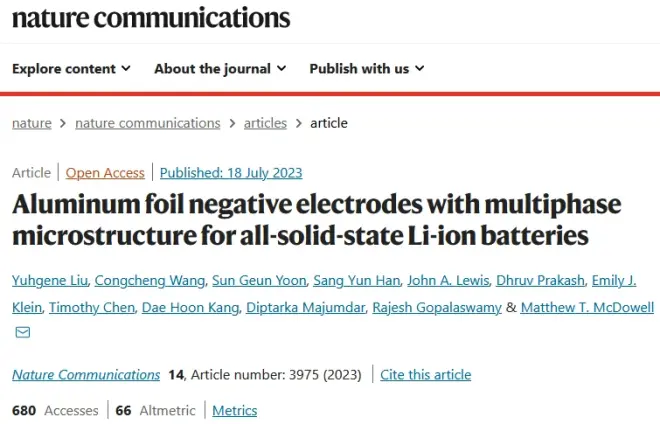
三、圖文速遞
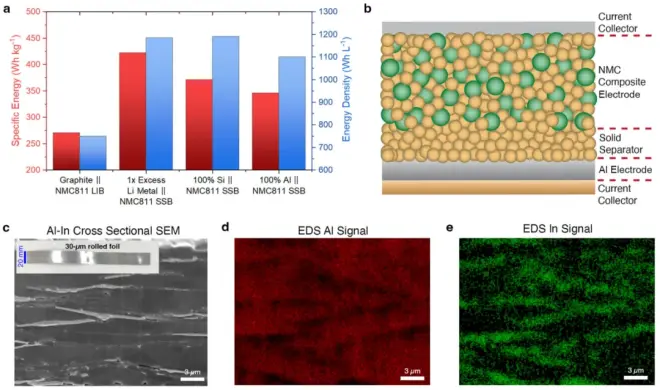
在惰性環(huán)境中熔化適當(dāng)比例的鋁銦合金負(fù)極,然后冷卻并軋制到所需厚度(圖 1c,插圖)。X 射線衍射 (XRD) 顯示,合金由獨(dú)立的鋁相和銦相組成,這與 Al-In 相圖中單晶冷卻時(shí)的固相不混溶性一致。圖1c顯示的是厚度為30μm的原始 Al94.5In5.5箔的低溫聚焦離子束(cryoFIB)掃描電子顯微鏡(SEM)圖像,圖1d和1e顯示的是 X 射線能量色散光譜(EDS)分析,揭示了材料中的元素分布,其中銦與鋁的質(zhì)量比為1:4。Al94.5In5.5鋁箔呈現(xiàn)出獨(dú)特的層狀微觀結(jié)構(gòu),銦層分布在整個(gè)鋁基體中。純鋁箔也是致密的,沒有橫截面形態(tài)特征。
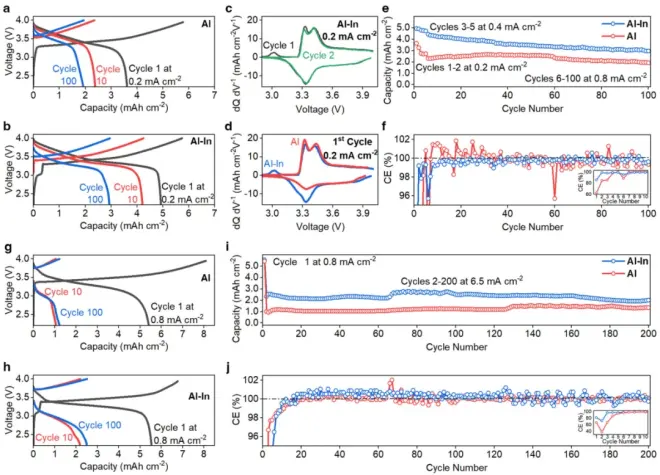
圖2a和2b顯示了鋁| LPSC | NMC622 和 Al94.5In5.5?| LPSC | NMC622 電池的恒電流循環(huán)結(jié)果。這些電池的正極負(fù)載量為5.8 mAh cm-2,在25 °C下循環(huán)過程中,電池保持在24 MPa的疊加壓力下。兩種電池在0.2 mA cm-2的首次充電時(shí)幾乎都利用了正極的全部容量,但與純鋁電池(85% 對 64%)相比,使用 Al-In 合金的電池顯示出更高的初始庫侖效率(CE)。鋁銦負(fù)極電池在充電過程中顯示出與銦的鋰化有關(guān)的初始肩峰(圖 2b)。在第一個(gè)循環(huán)之后,圖2b中的電壓曲線和圖2c中的差分容量(dQ/dV)曲線幾乎沒有顯示銦進(jìn)一步鋰化的跡象,這表明即使在放電之后,鋁箔中的銦仍然保持鋰化狀態(tài)。比較兩個(gè)具有不同負(fù)極的電池的第一個(gè)循環(huán)的差分容量曲線(圖 2d)凸顯了鋁銦電池的可逆性得到了改善。
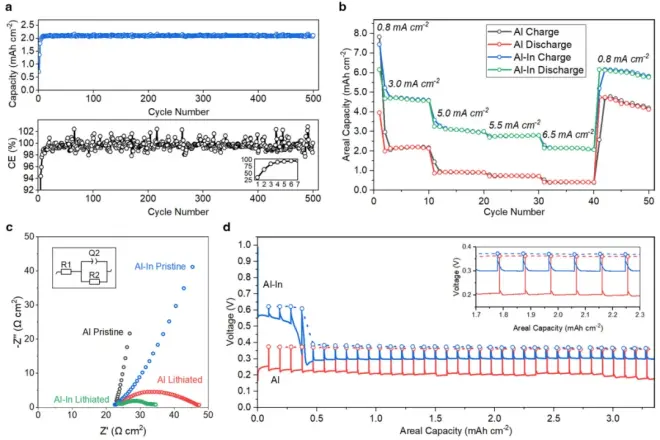
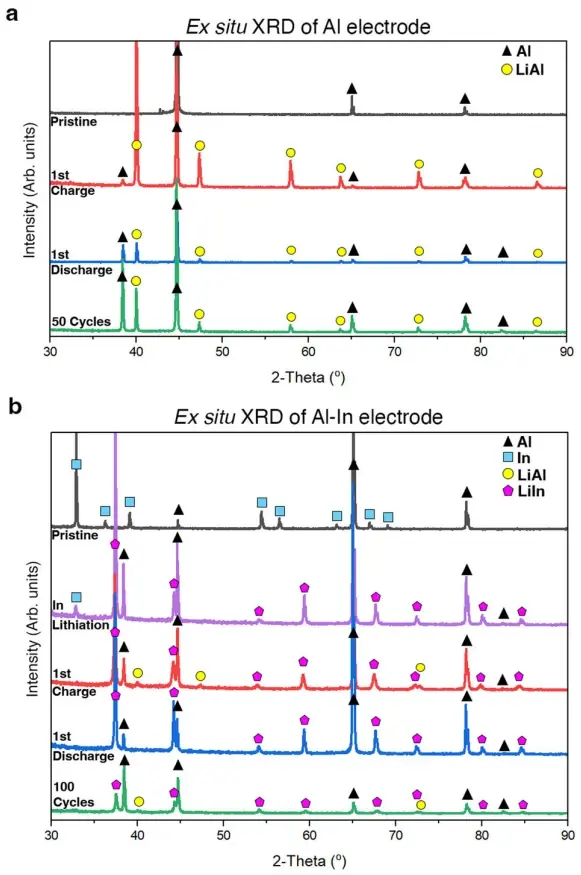
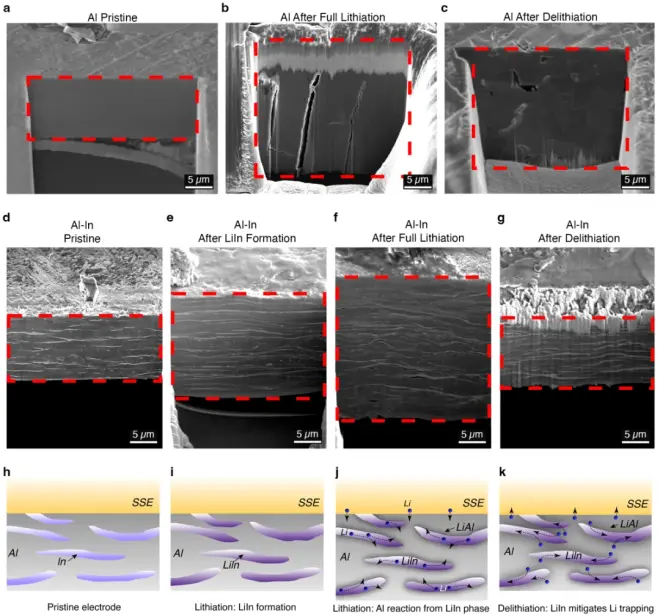
?圖5顯示了Al94.5In5.5和純鋁電極在不同循環(huán)階段的低溫 FIB-SEM 成像結(jié)果。低溫有助于確保將樣品損傷和與Ga+銑削束的相互作用降至最低。圖5a顯示的是原始鋁電極。圖5b顯示的是完全鋰化后的鋁電極,其厚度明顯增加,并出現(xiàn)明顯裂紋。圖5c顯示的是脫鋰后的鋁電極,其中含有一些孔隙。圖5d顯示了原始Al94.5In5.5箔的低溫 FIB 圖像,對比度較低的銦相在整個(gè)鋁基體中呈層狀可見。圖5e顯示了僅對銦進(jìn)行光鋰處理后的Al94.5In5.5箔電極。鋁箔完全鋰化后(圖5f),材料的厚度擴(kuò)大了約100%,而鋁脫鋰后(圖5g),鋁箔的厚度縮小了。重要的是,在整個(gè)鋰化/脫鋰過程中,銦鋰層保持完整可見。20個(gè)循環(huán)后的 FIB-SEM 圖像也顯示出完整且相互連接的鋰銦層,這表明箔在整個(gè)循環(huán)過程中都保持著密集的相互連接的鋰銦層。經(jīng)過100次充電/放電循環(huán)后,箔仍然保持機(jī)械完好。
綜上所述,這些發(fā)現(xiàn)證明了鋁基體中分布的銦鋰相對于提高鋁銦電極的可逆性、速率行為和性能非常重要。如前所述,銦相首先發(fā)生鋰化,即使在Al-In | | NMC622電池放電后也會保持鋰化,如圖5h, i中的示意圖所示。這種銦鋰相可以支持相對較快的鋰擴(kuò)散,可能通過以下方式影響電池的行為。首先,由于銦鋰相作為層狀三維網(wǎng)絡(luò)分布在整個(gè)鋁基體中,因此鋁與銦鋰相中的鋰發(fā)生反應(yīng)的界面面積更大。這使得鋰能從銦鋰網(wǎng)絡(luò)中傳輸出來,與鋁發(fā)生反應(yīng),以較低的過電位形成鋰鋁(圖5j)。
四、結(jié)論與展望
長期以來,人們一直在為使用非水性電解質(zhì)溶液的電池尋找合金基負(fù)極,但在實(shí)際相關(guān)的面積容量和電極厚度條件下,這種負(fù)極卻無法實(shí)現(xiàn)穩(wěn)定的循環(huán)。他們的研究結(jié)果表明,固態(tài)結(jié)構(gòu)以及負(fù)極微結(jié)構(gòu)工程對于實(shí)現(xiàn)穩(wěn)定的全固態(tài)二次鋰電池具有明顯的優(yōu)勢。他們發(fā)現(xiàn),致密的鋁基負(fù)極在固態(tài)電池的鋰化和脫鋰過程中保持緊湊,避免了在使用非水電解質(zhì)溶液的電池中形成大量的 SEI,從而限制了電池的性能。出現(xiàn)這種情況的原因可能是全固態(tài)堆疊產(chǎn)生的機(jī)械約束,以及負(fù)極和 SSE 之間相對穩(wěn)定的平面界面接觸(而使用非水電解質(zhì)溶液的電池中,界面面積會逐漸增大)。SSB 循環(huán)性能可通過添加少量合金元素得到改善;5.5 at% 的銦可提高可逆性并改善速率行為。這是因?yàn)榉植际礁邤U(kuò)散性銦鋰相能夠使鋰與鋁在較大的界面面積上發(fā)生反應(yīng),從而提高速率性能,同時(shí)還能最大限度地減少鋰去除過程中的鋰捕獲。這些研究結(jié)果表明,有可能在全固態(tài)鋰電池中使用箔合金金屬電極,從而避免了漿料涂層的需要,而漿料涂層在電池制造中占據(jù)了相對較大的成本和能耗要求。此外,箔合金金屬電極還提供了將一種結(jié)構(gòu)同時(shí)用作離子存儲電極和電流收集器的可能性。預(yù)計(jì)未來在優(yōu)化合金成分和微觀結(jié)構(gòu)、確定銦以外的其他元素添加效果以及了解材料演變方面的努力將進(jìn)一步提高性能。
文獻(xiàn)鏈接:https://www.nature.com/articles/s41467-023-39685-x