GH3030高溫合金材質(zhì)密度化學(xué)成分
GH3030概述:GH3030固溶強化型高溫合金是早期發(fā)展的80Ni-20Cr固溶強化型高溫合金,化學(xué)成分簡單,GH3030在800℃以下具好的熱強性和高的塑性,并具有良好的耐氧化、冷沖壓和焊接工藝性能。GH3030合金經(jīng)固溶處理后為單相奧氏體,使用過程中組織穩(wěn)定。用于800℃以下工作的渦輪發(fā)動機燃燒室部件和在1100℃以下要求耐氧化但承受載荷小的其他高溫部件。GH3030具有強熱加工及冷加工性能,用于制作化工設(shè)備及配套配件。

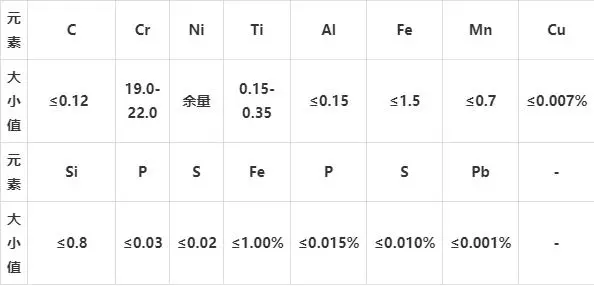
GH3030化學(xué)成分:
應(yīng)用概況與特殊要求:
主要用于燃燒室和加力燃燒室零部件以及機匣安裝邊等零部件。
物理及化學(xué)性能
熱性能
熔化溫度范圍:1374~1420℃
金相組織結(jié)構(gòu):
該合金在1000攝氏度固溶處理后為單相奧氏體組織,間有少量TiC和Ti(CN)。
工藝性能與要求:
1.該合金具有良好的可鍛性能,鍛造加熱溫度1180℃,終鍛900℃。
2.該合金的晶粒度平均尺寸與鍛件的變形程度、終鍛溫度密切相關(guān)。
3.熱處理后,零件表面氧化皮可用吹砂或酸洗方法清除。
摘? 要? 分析了?GH3030 合金鍛坯產(chǎn)生表面裂紋和內(nèi)部裂紋的原因 ,提出了減少裂 紋的有效措施。
1 前 言
GH3030 合金屬于固溶強化型鎳基耐熱高溫 合金 ,主要用于發(fā)動機 650~800 ℃的火焰筒、襯 套及其它高溫部件。冶鋼主要生產(chǎn)棒材和餅材。 多年來 ,GH3030 合金生產(chǎn)中的主要問題是鍛造開 坯過程容易產(chǎn)生角裂和魚鱗狀表面裂紋 ,降低了 成材率。鎳基高溫合金價格昂貴 ,提高成材率是 降低成本的關(guān)鍵。通過技術(shù)攻關(guān) ,使成材率大幅 度提高 ,創(chuàng)造了較大的經(jīng)濟效益 ,樹立了冶鋼的品 牌。
2 GH3030 合金的化學(xué)成分
GH3030 合金的化學(xué)成分見表 1。

3 工藝流程
GH3030 采用電弧爐或非真空感應(yīng)爐 + 電渣 冶煉 ,可以得到純潔度高、組織均勻致密、偏析度 較小和表面良好的電渣錠。電渣錠為 1. 2 t 或 1. 5 t ,用 5 t 蒸汽錘開坯。
4 裂紋形成過程及裂紋特征
GH3030 合金電渣錠在鍛造開坯從方園斷面
至方斷面就開始出現(xiàn)輕角裂?,繼續(xù)變形后角裂加 深 ,挖掉角裂時繼續(xù)鍛打表面無裂紋。對于個別 嚴重的鍛坯在角裂加深擴大后平面部分出現(xiàn)魚鱗 狀裂紋。
對出現(xiàn)角裂時進行挖角后不再出現(xiàn)角裂?的?,可鍛成方坯 ,局部清理后再成材。挖角的鍛 坯 ,在鍛制 90 mm 方試料時容易出現(xiàn)表面裂紋 ,低 倍組織見圖 1。對 90 mm 方試料進行低倍檢驗和 對棒材進行超聲波探傷發(fā)現(xiàn)的內(nèi)部裂紋 ,有的距 表面有一定深度 ,沿弦向呈彎曲狀 ,也有的接近棒材的中心。
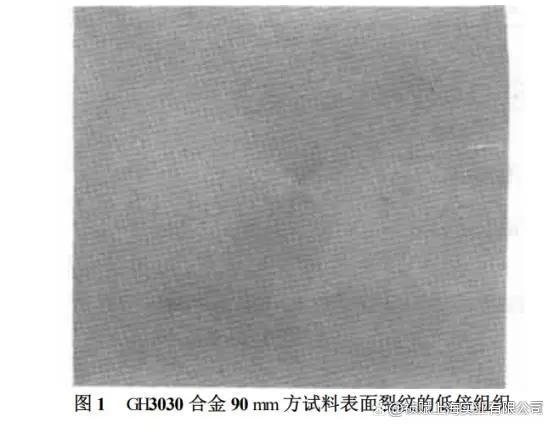
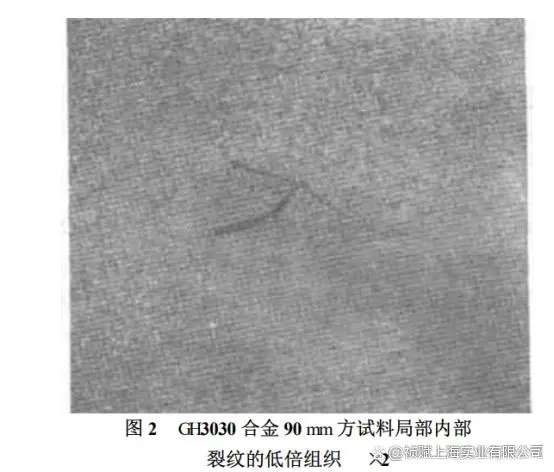
5 產(chǎn)生裂紋的原因及預(yù)防措施 鍛造的主要目的在于破壞鑄態(tài)組織 ,得到均 勻致密的鍛態(tài)顯微組織 ,并獲得一定的外形???制好加熱溫度 ,使鋼錠溫度均勻 ,內(nèi)外燒透 ,防止 過燒。內(nèi)部裂紋 ,除鋼錠本身由于原材料雜質(zhì)元 素、氫氧含量高、電渣錠氣孔和殘留 Ca 量不同等 影響熱加工塑性而產(chǎn)生外 ,大多與過熱和局部過 燒有關(guān)。
高溫合金導(dǎo)熱性較差?,熱加工溫度范圍 窄 ,熱加工塑性較低 ,鎳基高溫合金的熱加工塑性 約在 40 %~50 %左右 [1 ] 。
5.?1 原材料的影響 原材料的雜質(zhì)元素含量較高 ,尤其是五害元 素、氣體等超標(biāo)準(zhǔn)。如冶煉所用鎳板質(zhì)量不好 ,而 且鎳板用量非常大 ,占原材料的 70 %以上。
6.?鎳板?有氣泡夾層?,五害元素含量較高 ,表面留有電解液 ,且退火不徹底 ,氣體含量較高。五害元素、氣 體等雖然平均含量很小 ,甚至只有十萬分之幾 ,但 是由于偏析 ,使晶界區(qū)的局部濃度較高 ,其結(jié)果導(dǎo) 致晶界有效強化或嚴重弱化 [2 ] ,在高溫加熱條件 下 ,容易在晶界產(chǎn)生裂紋。因此 ,要確保原材料質(zhì) 量 ,加強鎳板退火。當(dāng)鎳板 wH ≤5. 9 ×10 - 6時 ,方 可用于冶煉。
7.?原材料的?wP 、wS 較高。P、S 易形成低熔點共 晶 ,降低熱加工性 ,增加脆性 ,晶界偏析造成脆化。
8.?硫與鎳形成硫化物?Ni3S2 ,它可與 Ni 組成易熔的 共晶體(Ni + Ni3S2 ) ,沿鎳的晶界分布 ,引起鎳的熱 脆。因此 ,煉鋼時選用低 wS 的金屬鉻 ,石灰選用 木炭燒制的。
9.?同時在電渣錠加熱過程中避免火焰?直接噴到電渣錠表面?,以減少鋼錠增硫。
5.?2 冶煉因素的影響 由于 GH3030 為含低 Al、Ti 的鎳鉻基高溫合 金 ,電弧爐或感應(yīng)爐冶煉時脫氧不良 ,因此應(yīng)適當(dāng) 提高 Mn 含量和控制合適的殘留 wCa 。
6.?由于?Mn 可以脫氧和脫硫 ,生產(chǎn)中將 Mn 由 0. 30 %提高到
0. 55 % ,同時增加脫氧劑 Ca - Si 塊用量 ,由原 1. 3 ~2. 2 kgΠt 提高到 2. 8~3. 4 kgΠt ,使脫氧良好。 電渣冶煉時采用提純渣 ,加強對渣料、石棉板 和護錠鎳板的烘烤 ,以降低氣體和夾雜含量 ,消除 電渣錠氣孔 ,減少內(nèi)部裂紋。
5. 3 電渣錠殘留 wCa 的影響 經(jīng)大量的統(tǒng)計分析可知 ,當(dāng)電渣錠殘留 wCa 在 0. 001 5 %~0. 004 5 %之間 ,裂紋廢品最少 ,成 材率最高。
5.?4 鍛造工藝的影響 加熱溫度過高 ,保溫時間過長 ,引起過熱或過 燒 ,出現(xiàn)內(nèi)部裂紋。
6.?實踐證明?, 加熱溫度超過
1 180 ℃,保溫時間超過 5 h ,裂紋廢品明顯增加。
對錠型較大的鋼錠?,要特別注意加熱速度 ,加熱速 度要緩慢 ,保溫時間應(yīng)適當(dāng)長一些。
終鍛溫度偏低由熱加工溫度偏低引起裂?紋?,當(dāng)熱加工溫度太低 ,如終鍛溫度 ≤900 ℃時 , GH3030 合金的變形抗力增大 ,塑性降低 ,若繼續(xù) 進行變形 ,往往引起裂紋。
在實際生產(chǎn)中?,開鍛溫度 ≥1 050 ℃,終鍛溫 度 ≥900 ℃,出現(xiàn)角裂及時挖掉 ,可以有效地控制 裂紋的產(chǎn)生和擴展。同時 ,鍛造過程中 ,最初的錘 擊應(yīng)輕 ,錘擊面應(yīng)盡可能小 。由于鑄態(tài)組織塑性?經(jīng)?910 ℃淬火 + 610 ℃回火后鋼晶粒更細小、 更均勻 ,其組織為回火索氏體 (見圖 7) 。
這也就?是說?,經(jīng)過高溫回火消除了貝氏體對鋼性能的影 響??梢娫囍其摰慕M織完全達到了設(shè)計要求。
6 結(jié) 論
(1) 試制鋼的主要化學(xué)成分 C、Si、Mn、Cr、Mo、 B、Al 等的含量分別為 0. 17 %~0. 22 %、0. 26 % ~0. 35 %、1. 16 %~1. 4 %、0. 51 %~0. 56 %、 0. 25 %~0. 26 %、0. 001 2 %~0. 001 8 %、0. 015 %~0. 031 % ,都符合 DNV 和 ABS 對四級錨鏈鋼 的要求。
(2) 三相交流電弧爐冶煉鋼的屈服強度 (σs ) 、 抗拉強度(σb ) 、延伸率 (δ5 ) 、斷面收縮率 (Ψ) 和夏 比 V 型缺口沖擊值 ,Akv(0 ℃、- 20 ℃、- 40 ℃) 的 平均值分別為 866 MPa、930 MPa、13. 3 %、53 %和 118 J 、99 J 、88 J ,完全符合有關(guān)規(guī)范對四級錨鏈鋼 的要求。
(3) 試制鋼通過淬透性試驗、夾雜物分析和高低倍檢測表明其淬透性較好 ,組織基本為鐵素體 + 珠光體 ,夾雜物含量也相當(dāng)少。
(4) 對比試制鋼的 3 種冶煉方法(包括真空感 應(yīng)爐、真空爐重熔及電爐冶煉) 表明 ,用電弧爐冶 煉完全可以達到 DNV 和 ABS 對四級錨鏈鋼的要 求。
只要嚴格控制原材料成分、冶煉過程和熱處?理工藝?,在工業(yè)性試驗階段可以不采用真空進行 冶煉。