A100鋼是國外Aermet100鋼具有超高強(qiáng)度
A100鋼
A100鋼是國外Aermet100鋼,屬于Co-Ni超高強(qiáng)度鋼,具有超高強(qiáng)度(σb≈1970MPa)、優(yōu)良的斷裂韌度、抗應(yīng)力腐蝕開裂能力、良好的焊接性。是飛機(jī)重要承力構(gòu)件最具競爭力的候選材料,比如起落架外筒及活塞桿、傳動(dòng)筒機(jī)活塞桿等。
100鋼是由C、Cr、Mo強(qiáng)化的Fe-Co-Ni系合金,合金化元素高達(dá)30%,且該鋼采用真空熔煉加真空自耗重熔的雙真空熔煉工藝,材料制造成本較高。目前起落架外筒及活塞桿等筒狀構(gòu)件,均采用傳統(tǒng)鍛造配合機(jī)加工的制造方法,而筒內(nèi)實(shí)心的構(gòu)件則在整體模鍛件的基礎(chǔ)上進(jìn)行深膛切削去除。傳統(tǒng)的起落架制造方法存在制造難度高、周期長,材料利用率低等缺點(diǎn),無法飛機(jī)型號(hào)快速試制的要求。
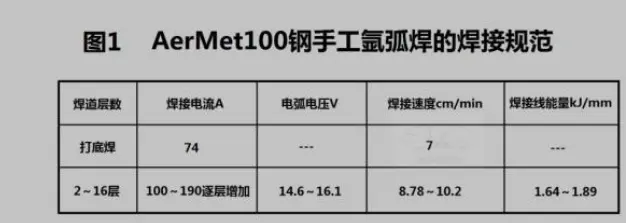
為克服上述現(xiàn)有技術(shù)的不足,本發(fā)明的目的是提供一種二次硬化高強(qiáng)度A100合金鋼粉末制備方法,
相比之下,國內(nèi)對該鋼研究起步晚,投入少,目前我國的飛機(jī)起落架主要用300M鋼和AF1410鋼。隨著航空事業(yè)的發(fā)展,北京航空材料研究院成功研制出了Aermet100鋼的焊材和焊接工藝。不久將來,新型飛機(jī)會(huì)用上A100起落架。
現(xiàn)在焊接A100鋼的方法主要是氬弧焊,焊材采用同質(zhì)剪條宜采用V形坡口,間隙1mm左右。在焊接過程中,焊接參數(shù)根據(jù)焊道在坡口中的具體位置應(yīng)適當(dāng)調(diào)整。如打底焊時(shí),為了避免焊漏應(yīng)采用較大的焊接速度和較小的焊接電流,填絲速度和電弧電壓也要相應(yīng)降低。隨焊道層數(shù)增加,坡口內(nèi)焊縫寬度增大,為保證焊縫容寬并避免未熔合,應(yīng)增大焊接電流和電弧電壓。一般焊后先進(jìn)行正火+高溫回火的預(yù)備熱處理,再進(jìn)行淬火-冰冷-時(shí)效的最終熱處理。對于厚16mm,V形坡口的焊接參數(shù)見圖1。
為實(shí)現(xiàn)上述目的,本發(fā)明采用的技術(shù)方案是:一種二次硬化高強(qiáng)度A100合金鋼粉末制備方法,包括以下步驟:
步驟1,A100母合金棒的熔煉,合金成分按照AMS6532(A)進(jìn)行合金配比:按質(zhì)量分?jǐn)?shù)計(jì),鐵余量,碳0.21~0.25,鉻2.9~3.3,鎳11~12,鈷13~14,鉬1.1~1.3,錳≤0.1,鈦≤0.015,鋁≤0.015,硅≤0.1,磷≤0.008,硫≤0.005,氧≤0.002,氮≤0.0015,磷+硫≤0.01;
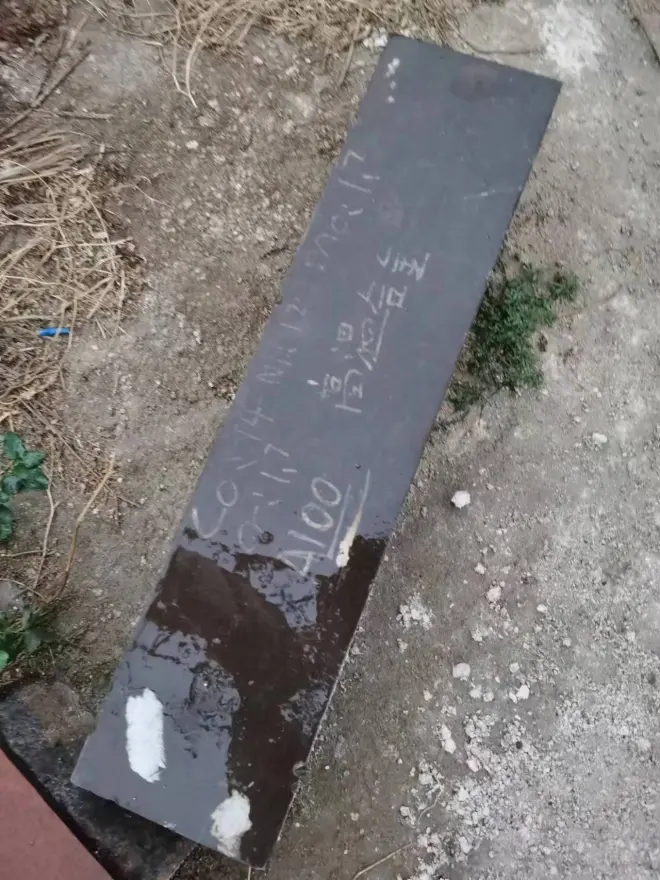
步驟2,將A100合金母合金棒坯進(jìn)行機(jī)加,加工后電極棒直徑為20-100mm,長度為100-1000mm,電極棒直線度偏差控制在≤0.2mm/m,獲得A100合金電極棒;
步驟3,將A100合金電極棒置于惰性氣體密閉反應(yīng)室內(nèi)并高速旋轉(zhuǎn),采用等離子槍加熱電極棒端部,使其融化;
步驟4,步驟3的A100合金電極棒熔融金屬霧化后在離心力作用下飛出,形成細(xì)小液滴,液滴在保護(hù)氣體中快冷后形成球形顆粒,落入霧化室底部收集容器內(nèi),得到A100合金球形粉末。
所述的A100合金球形粉末比表面積低,僅有0.01~0.08m2/g。
步驟4所述的A100合金球形粉末球形度大于95%。
所述的電極棒的轉(zhuǎn)速為5000~35000rpm。
所述的惰性氣體為氦氣或氬氣或二者的混合氣體。
A100鋼本發(fā)明的有益效果是:
與現(xiàn)有技術(shù)相比,本發(fā)明A100合金球形粉末的制備方法,通過高速旋轉(zhuǎn)離心霧化的方法制備A100合金球形粉末,大限度地減少合金成分偏析,消除組織粗大及不均勻組織。同時(shí)可實(shí)現(xiàn)近凈成形和自動(dòng)化批量生產(chǎn),有效降低金屬的損耗。因其生產(chǎn)過程中不與坩堝和脫氧劑等混合,不怕混入雜質(zhì),所以制取成粉末具有高純度,球形度良好,低價(jià)雜物含量等性能指標(biāo),保證了材料成分配比的正確性和均勻性。
采用PREP制粉工藝可以制備球形度很高的A100合金鋼粉末,粉末中無衛(wèi)星粉?,F(xiàn)有技術(shù)A100合金鋼粉末比表面積大于0.1 m2/g。因此,采用本方法制備高球形度的A100粉末。采用PREP法制備A100合金鋼粉末具有良好的應(yīng)用前景。