化工企業(yè)高濃度氯代烴有機廢氣治理工程
安徽某化工新材料企業(yè),實際投產(chǎn)生產(chǎn)中其有機廢氣中主要成分由二氯甲烷、二氯乙烷、乙酸、乙醇、庚烷、甲醇、碳酸二甲酯、二甲胺、甲苯等組成。對于車間中不含上述二氯甲烷、二氯乙烷等氯代烴類有機廢氣,采用反應釜排口處設置集氣罩進行收集,對排口處設置全覆蓋集氣罩,利用末端風機保持罩口的微負壓,經(jīng)計算其風量為25000Nm3/h,采用蓄熱焚燒裝置(RTO)進行焚燒處理。
對于從傅克釜、脫溶釜、精餾釜排出的高濃度二氯甲烷、二氯乙烷,該類有機廢氣特點是濃度高、風量小,如直接進入RTO系統(tǒng)焚燒將生成次級污染物氯化氫、二噁英。氯化氫的生成將大大加劇RTO設備的腐蝕,同時也需要消耗大量的堿液中和處理以確保氯化氫排放達標;二噁英不但具有很強的毒性,而且具有致癌性、致突變性、生物富集性以及在環(huán)境介質(zhì)中的長期穩(wěn)定性,且該項目執(zhí)行的排放標準《大氣污染物綜合排放標準》(DB31/933-2015)中對二噁英的要求為0.1ng-TEQ/m3,對氯代烴進行深冷預處理將大大減少二噁英的生成。因此,擬采用深度冷凝方式對高濃度氯代烴廢氣進行預處理,經(jīng)過深冷后的氯代烴不凝氣再進入RTO焚燒實現(xiàn)達標排放。
1、廢氣濃度及風量
根據(jù)企業(yè)提供的數(shù)據(jù),當從傅克釜、脫溶釜、精餾釜等排氯代烴廢氣操作時,其主要排放的廢氣成分分別為二氯甲烷、二氯乙烷,可根據(jù)物料不同進行單獨分類收集,排放時其夾帶有少量氯化氫和氯苯等。分類單獨收集后,主要含二氯甲烷廢氣風量為160Nm3/h,主要含二氯乙烷廢氣風量為240Nm3/h。具體工況參數(shù)如下表1所示:
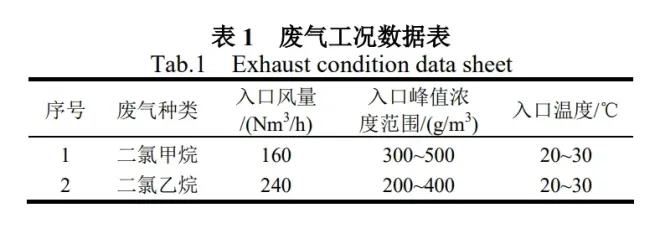
2、工藝流程及工藝設計
2.1整體工藝選擇
根據(jù)廢氣排放工況,二氯甲烷、二氯乙烷有機廢氣可分別收集后進行單獨處理,故設計兩套深冷回收裝置分別回收處理,冷凝回收后的回收液還可回用于生產(chǎn)工段中,實現(xiàn)廢氣資源化。因廢氣中夾帶氯化氫廢氣,故需堿洗預處理后再進入冷凝回收系統(tǒng),可減輕氯化氫對冷凝系統(tǒng)的腐蝕,經(jīng)深冷后的氯代烴不凝氣再進入RTO焚燒系統(tǒng)焚燒后再實現(xiàn)達標排放,故整體工藝流程如圖1所示。
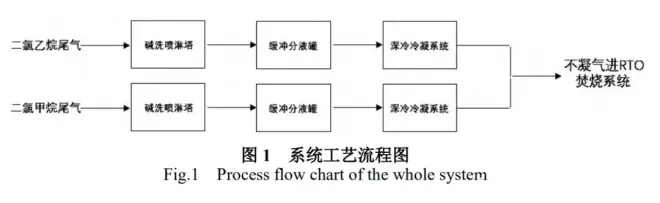
2.2機械制冷基本原理
本系統(tǒng)采用機械壓縮制冷,其基本工作原理是熱力學第二定律,即它是通過壓縮機消耗機械能改變制冷劑的狀態(tài),在制冷劑循環(huán)狀態(tài)變化過程,將熱量從溫度低的環(huán)境(或物體)傳遞(轉(zhuǎn)換)給溫度高的物體(或物質(zhì)),從而使溫度高的物質(zhì)(如有機氣體)減低溫度,相態(tài)發(fā)生變化(從氣態(tài)變?yōu)橐簯B(tài)),通過將氯代烴廢氣冷凝變?yōu)橐簯B(tài),實現(xiàn)凈化或回收的目的。
2.3冷凝終點溫度設計
為將上述高濃度氯代烴廢氣深冷預處理后降低其排氣濃度,冷凝點溫度按照安托萬方程模擬計算出不同溫度下的飽和蒸汽濃度參考值,依照其飽和蒸汽濃度值作為選擇最終冷凝終點溫度的重要參考,二氯甲烷、二氯乙烷在不同冷凝溫度和飽和蒸汽濃度對照表如表2所示。
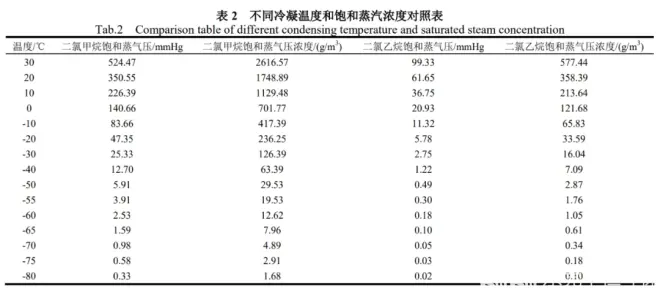
可見,在廢氣冷凝終點為-70~-75℃間,將有不低于90%的二氯甲烷、二氯乙烷廢氣將被冷凝液化,不凝氣將進入設計處理量為25000Nm3/h的RTO系統(tǒng)中先被稀釋后焚燒處理,大大降低了RTO對氯代烴的處置負荷,可進一步保證因焚燒氯代烴而產(chǎn)生的氯化氫、二噁英等次級污染物的大量形成。且將冷凝終點溫度設置再低無法再增加二氯甲烷的冷凝液化效果,因此,將冷凝終點溫度定為-70~-75℃間。
2.4深冷冷凝系統(tǒng)設計要點
深冷冷凝裝置采取“堿液吸收+雙通道冷凝”的集成工藝。系統(tǒng)組成含“廢氣輸送模塊”、“堿液吸收模塊”、“雙通道冷凝模塊”、“冷凝液輸送模塊”、“PLC控制模塊”。
2.4.1廢氣輸送模塊
二氯甲烷、二氯乙烷廢氣深冷冷凝裝置入口均分別設置阻火器,確保安全。氣相總管分別配裝一臺壓力變送器,廢氣主管路管道上阻火器兩端設置壓差變送器,如發(fā)生堵塞現(xiàn)象導致壓差超過設置值,系統(tǒng)自動發(fā)出報警信號。廢氣通過管道連接進行收集,當有氣體呼出產(chǎn)生有微正壓時,裝置內(nèi)的防爆變頻引風機開始連鎖起動,并根據(jù)進氣管內(nèi)的壓力反饋值進行PID變頻調(diào)節(jié),確保氣相管道內(nèi)工作壓力穩(wěn)定在一定范圍內(nèi),為克服撬內(nèi)冷凝模塊阻力提供動力。系統(tǒng)設有“開風機正壓(50~500Pa)”、“運行壓力(-200Pa)”、“停風機負壓(-500Pa)”、“超壓排空(2000Pa)”等參數(shù),以上參數(shù)均可現(xiàn)場進行調(diào)整,當管道內(nèi)氣體壓力達到“開風機正壓”值,引風機啟動,低于“停風機負壓”值,引風機停止,PLC通過變頻器控制引風機的轉(zhuǎn)速,使管道內(nèi)壓力按“運行壓力”值,上下微量波動,從而順利將油氣引入裝置進行處理,超過“超壓排空”設置值,則報警且打開緊急排空閥,將超壓氣體安全排出,確保安全;該模塊內(nèi)還設置進氣溫度檢測及進氣流量檢測,系統(tǒng)引風機安裝于尾氣出口管道,保證整套裝置內(nèi)的過流管道均處于微負壓狀態(tài),減少了廢氣外漏的風險,同時也避免了易液化組分堵塞風機進氣通道,造成引氣故障。
2.4.2堿液吸收模塊
在引風機作用下,氯代烴廢氣從堿洗塔下部進入,與弱堿吸收液進行氣液兩相充分接觸吸收,將廢氣中的氯化氫吸收,為避免氯代烴對塔身的腐蝕,塔身及循環(huán)管路材質(zhì)選擇316L。堿液在塔底經(jīng)水泵增壓后從塔頂噴淋而下,最后回流至塔底循環(huán)使用。
塔內(nèi)填料設計方面,堿洗塔內(nèi)填料層作為氣液兩相間接觸構(gòu)件的傳質(zhì)設備,填料塔底部裝有填料支承板,填料(同樣為避免氯代烴腐蝕有機塑料填料,填料材質(zhì)選擇316L)以亂堆方式放置在支承板上。填料的上方安裝填料壓板,以防被上升氣流吹動。
噴淋液從塔頂經(jīng)液體分布器噴淋到填料上,并沿填料表面流下。氣體從塔底送入,經(jīng)氣體分布裝置分布后,與液體呈逆流連續(xù)通過填料層的空隙,在填料表面上,氣液兩相密切接觸進行傳質(zhì)??账俾士刂撇怀^1m/s,確保吸收效率并有效控制廢氣的揮發(fā)損耗。當吸收一定量氣體,導致液位達到高液位,或吸收液中的pH值達到中和值,失去吸收能力,則自動補充堿液及排放廢液,氣體出口同樣設置尾氣pH在線檢測,確??刂扑嵝詺怏w有效去除。
2.4.3雙通道冷凝模塊
在引風機作用下,待處理二氯甲烷、二氯乙烷氣體依次再進入預冷箱、一級淺冷箱(雙通道)、二級中冷箱(雙通道)、三級深冷箱(雙通道),一級冷凝溫度設計為0~5℃(可調(diào)),二級冷凝溫度設計為-25~-35℃(可調(diào)),三級冷凝溫度設計為-70~-80℃(可調(diào))。在此梯度低溫條件下,高濃度氯代烴廢氣冷凝液化,回收液匯集流入回收裝置內(nèi)的暫存罐中,不凝氣進入RTO系統(tǒng)進行焚燒。設置雙通道主要考慮冰堵因素,當一個通道通過差壓計顯示壓力過高,將油氣自動切換到另一個通道進行冷凝。雙通道冷凝模塊是深冷冷凝系統(tǒng)的核心,還有如下特殊設計考慮:
(1)采用R404A、R23及R14環(huán)保型制冷劑,同等工況(蒸發(fā)、冷凝溫度)、同等換熱制冷量的情況下,能耗最低,更容易達到-70~-80℃或更低的低溫,保證冷凝回收效果,且所用制冷劑均為市場易購的標準消耗品。
(2)由于傳統(tǒng)的板翅式換熱器板片距小(僅幾毫米),板片薄(約0.4毫米),在低溫工況下,很短時間(1小時左右)便可能發(fā)生“結(jié)霜”而“冰堵”,傳熱效果惡化,加之結(jié)霜又使混合氣難以通過,風阻又降低換熱效果,且結(jié)霜嚴重時存在脹破的風險,一旦內(nèi)漏將混合可燃氣吸入制冷系統(tǒng)被壓縮機壓縮有引起爆炸的危險,即便為雙通道設計,也會導致切換過于頻繁,對運行可靠性及平穩(wěn)性造成影響。本項目設計使用高效、緊湊、低阻管翅式集成雙通道蒸發(fā)器,其殼層通道大,耐冰堵,翅片管壁厚達1.5亳米,強度高,運行安全性佳。
(3)冷凝末級溫度低至-70℃或更低溫度,為充分回收此冷量,在蒸發(fā)器前級設置一級預冷器,使出口低溫氣體與高溫進氣進行冷量交換,既回收末級冷量,又對高溫進氣進行預制冷,節(jié)能降耗的同時,又可預凝結(jié)油氣中所含的水分,從而遲緩后續(xù)冷凝箱中蒸發(fā)器表面結(jié)霜速度,進一步延長化霜周期,并保持良好的換熱效率。
(4)系統(tǒng)采用防爆風冷冷凝器,避免冬季低溫造成水冷冷凝器內(nèi)部結(jié)冰脹破、導致壓縮機燒毀的風險,該冷凝器采用親水藍膜高防腐性翅片,不易積灰,維護量極少。
(5)特別設計的氣液分離結(jié)構(gòu),有效解決冷凝出口帶液問題,將對后級處理模塊的影響降至最低。
(6)設置壓差變送器,實時監(jiān)測冷箱進、出口壓差,根據(jù)冰堵情況自動進行雙通道的切換,三級蒸發(fā)器均為雙通道并聯(lián)結(jié)構(gòu),可交替進行制冷及化霜,較好地解決了氯代烴熔點高易結(jié)晶堵塞冷凝通道導致液化回收難題,確保裝置連續(xù)制冷運行。系統(tǒng)化霜快速且不因化霜影響氣體的冷凝處理,且化霜是利用制冷壓縮機排出的高溫制冷劑蒸汽來進行,一套壓縮機同時給2套并聯(lián)蒸發(fā)器供熱與供冷,還減輕了原有冷凝器的負荷,整機經(jīng)濟節(jié)能。
在此梯度低溫及設計條件下,90%左右的高濃度氯代烴廢氣冷凝液化,回收液匯集流入回收裝置內(nèi)的暫存罐中。
2.4.4冷凝后廢液輸送模塊
冷凝下來的回收液從各個蒸發(fā)器流出,依靠重力匯集流入回收裝置內(nèi)的儲液罐中,儲液罐外配置磁翻板一體化液位計,液位高低信號直觀顯示并反饋給PLC,系統(tǒng)按用戶預設參數(shù)通過輸油泵輸送回收液到用相關(guān)存儲設備中后后續(xù)處理。
2.4.5PLC控制模塊
本項目深冷冷凝回收處理裝置控制軟件采用西門子公司S7系列編程平臺編制而成,程序采用模塊化結(jié)構(gòu)編寫??刂瞥绦蚰K有:主控制程序、數(shù)字量采集子程序、模擬量采集子程序、吸收控制子程序、一級機控制子程序、二級機控制子程序、三級機控制子程序、油液位控制子程序、保護子程序、報警子程序及相關(guān)運算模塊等??刂葡到y(tǒng)功能主要構(gòu)成如下:
(1)一鍵操作全自動運行:裝置按照設定的程序自動運行,無需人工干預。吸收模塊自動進行液位控制。制冷溫度到達工況控制點要求時,冷凝模塊自動停止運行進入待機狀態(tài)。當溫度回升后,重新自動運行。
(2)引風自動控制:根據(jù)進氣總管道壓力參數(shù)的變化,PLC對防爆引風機進行PID變頻控制,使管道內(nèi)的進氣壓力穩(wěn)定在一定區(qū)間內(nèi),確保安全。
(3)一、二、三壓縮機自動控制:根據(jù)程序的設定和制冷溫度的變化,自動開停壓縮機,在開停過程中有多重保護機制。
(4)制冷、化霜及節(jié)能模式:當連續(xù)制冷時間到達設定周期后,雙通道冷箱自動交替進行制冷與化霜。三級壓縮機退出運行:當回收油品發(fā)生變化,不需要深冷(-70℃)運行時,可以操作防爆箱面板“二級投入”旋鈕,則可使三級壓縮機處于待機狀態(tài),不參與制冷,僅一、二級壓縮機運行,此時最低冷凝溫度為-30℃。
(5)油位自動控制:儲油罐在正常油位時,凝液依靠重力流入罐內(nèi);當高油位時油泵起動自動泵油;泵至低油位時自動停止。
(6)保護與報警功能:當壓縮機綜合保護、壓縮機溫度保護、電動機過電流保護、電源相序保護、儲油罐液位達到100%、可燃氣體超過設置值等報警發(fā)生時,裝置自動停止運行并報警,直到問題排除并清除報警方可開機。
2.5深冷系統(tǒng)主要配置參數(shù)
綜上,本項目設計使用二套深冷冷凝機組分別對高濃度二氯甲烷、二氯乙烷進行深冷冷凝,冷凝液化后的二氯甲烷、二氯乙烷回收液可根據(jù)生產(chǎn)的實際要求回用至生產(chǎn)工段中。其配置的主要參數(shù)如下表3所示。
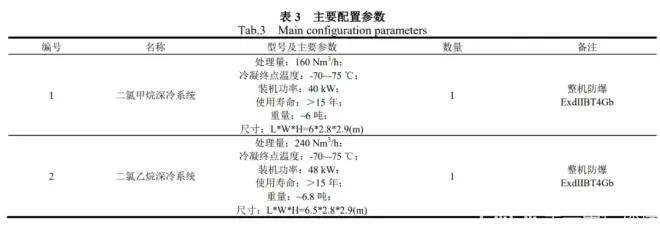
3、運行效果
本工程2020年11月投入使用,經(jīng)過1個月的調(diào)試,冷凝系統(tǒng)運行效果穩(wěn)定,最低冷凝終點溫度可達-76℃,二氯甲烷、二氯乙烷去除率可達90%左右,達到設計要求。經(jīng)冷凝后的不凝氣接入已投用且有機廢氣處理量為25000Nm3/h的RTO焚燒系統(tǒng)中經(jīng)稀釋后焚燒處理,進入RTO焚燒系統(tǒng)的二氯甲烷入口濃度為6.28mg/m3。最終,經(jīng)RTO焚燒處理后二氯甲烷、非甲烷總烴排放指標均符合排放標準要求,如表3所示:
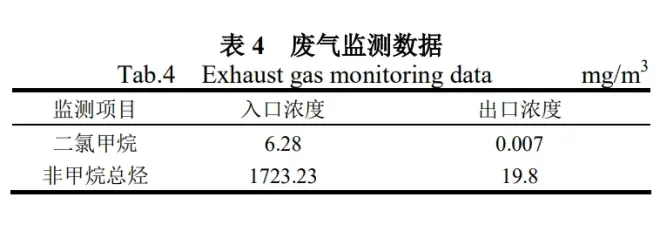
4、總結(jié)
本工程采用深冷冷凝工藝對化工新材料企業(yè)生產(chǎn)裝置中排放的高濃度、小風量氯代烴進行深冷預處理,冷凝回收處理率可達90%左右,大大減少進入RTO裝置的氯代烴,減輕了次級污染物氯化氫等的生成。經(jīng)RTO焚燒爐處理后的廢氣達到排放標準要求。該工程的成功運行對類似化工企業(yè)排放高濃度、低風量氯代烴廢氣處置設計具有借鑒作用和參考意義。