優(yōu)思學(xué)院|六西格瑪案例分析 - 降低焊接缺陷率
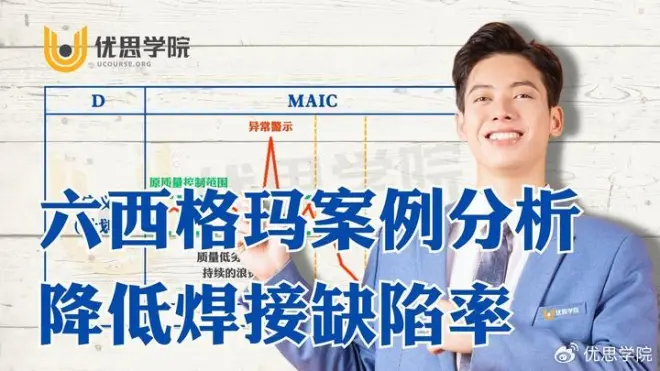
?
大家有留意優(yōu)思學(xué)院的文章和視頻的,都知道六西格瑪方法中的控制圖有助于監(jiān)測(cè)流程的穩(wěn)定性和識(shí)別特有原因的發(fā)生。對(duì)流程周期性地采樣,當(dāng)測(cè)量結(jié)果在控制上限和下限內(nèi),而且圍繞著一條中心線時(shí),我們就說(shuō)流程是受控的。注意上述控制上限和下限有別于規(guī)范限。
?
我們來(lái)看看一家工廠中對(duì)一個(gè)印刷電路板生產(chǎn)線的最后檢驗(yàn)。假設(shè)在工廠中使用了流程控制圖P圖(即,部分不符合控制圖),如下圖所顯示(如果一個(gè)圖表沒(méi)有了控制限,而只有一個(gè)運(yùn)行圖,那就會(huì)導(dǎo)致公司把圖上每個(gè)上下波動(dòng)的點(diǎn)都視為特有原因)。在該圖中,樣本總量的平均缺陷率是0.244。
?
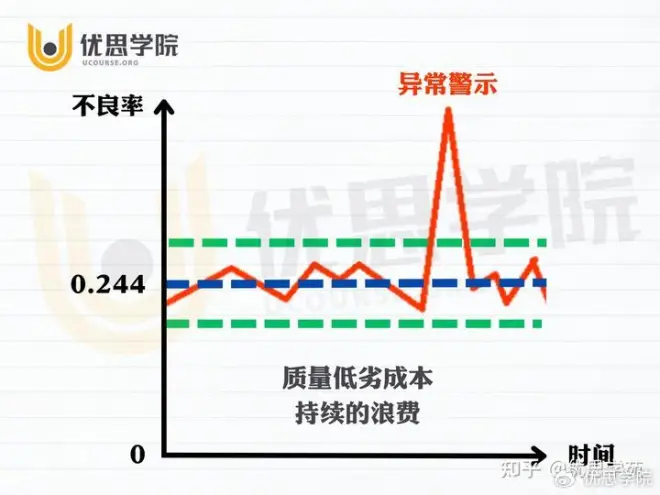
如果控制圖中沒(méi)有發(fā)現(xiàn)異常的情況,這一流程就是所謂受控的(即,沒(méi)有觀察到特有原因,如果有異常,就要找出這個(gè)特有的原是什么,然后設(shè)法令制程穩(wěn)定受控)。這是在DMAIC中的M階段所要做的事情。
?
過(guò)程穩(wěn)定之后,我們就需要降低缺陷率以減少返工率和廢品率(即,減少共有原因的影響),進(jìn)入分析的階段。
?
團(tuán)隊(duì)從3200次印刷電路的生產(chǎn)中觀察到以下各類(lèi)缺陷:
?
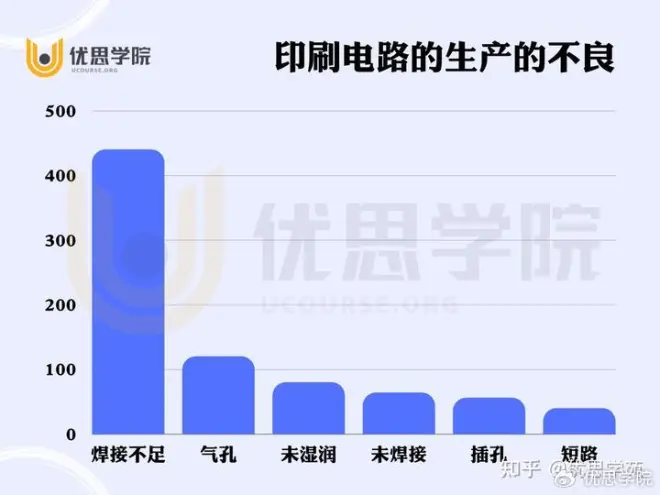
如上表中的焊接缺陷帕累托圖所示,很明顯應(yīng)當(dāng)“首攻”焊接不足。接下來(lái)通過(guò)一個(gè)由各領(lǐng)域?qū)I(yè)人員(例如,工程師、技師、制造工人、化學(xué)家、管理層等)參與的頭腦風(fēng)暴來(lái)生成因果圖,目的是識(shí)別最有可能產(chǎn)生缺陷的根源。
?
為了確定哪些因素對(duì)缺陷率影響最大,我們可以進(jìn)行回歸分析,然后再進(jìn)行實(shí)驗(yàn)設(shè)計(jì),這可能是最為恰當(dāng)?shù)姆椒?。這些技術(shù)人員或許還可以決定將考察對(duì)象用連續(xù)響應(yīng)來(lái)代替此前使用的描述性響應(yīng)??梢灶A(yù)期,連續(xù)響應(yīng)輸出對(duì)樣本量的要求要小得多。
?
在對(duì)流程進(jìn)行改變并且在控制圖上顯示出確實(shí)實(shí)現(xiàn)了改善之后,可以再生成新的帕累托圖?;蛟S對(duì)于焊接不足的改善已經(jīng)足夠大,而氣孔此時(shí)成為下一個(gè)首要改善的目標(biāo)。我們還可以用流程控制圖來(lái)單獨(dú)跟蹤焊接不足的現(xiàn)象,以迅速識(shí)別出流程從“修正水平”可能發(fā)生的退化。
?
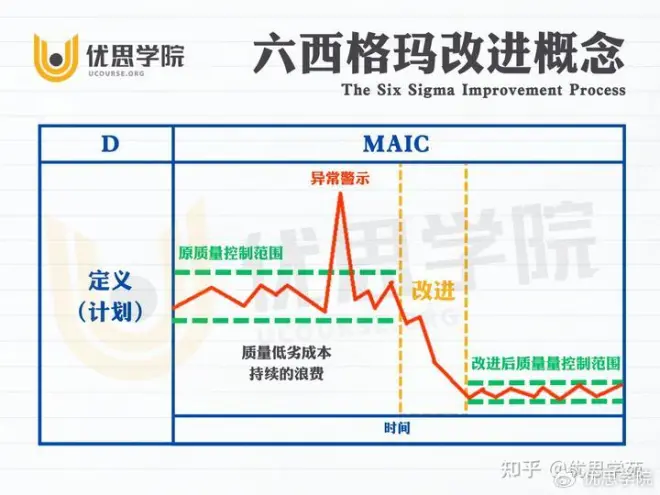
在通過(guò)確認(rèn)實(shí)驗(yàn)核實(shí)改變的效果之后,就可以對(duì)制造流程實(shí)施改變了。由于這些改變,現(xiàn)在P圖中的數(shù)據(jù)的模式應(yīng)當(dāng)向下平移,到達(dá)另外一個(gè)穩(wěn)定的區(qū)域。作為持續(xù)流程改善的一部分,重復(fù)上述所有步驟,以便識(shí)別其他需要改善的領(lǐng)域。
?
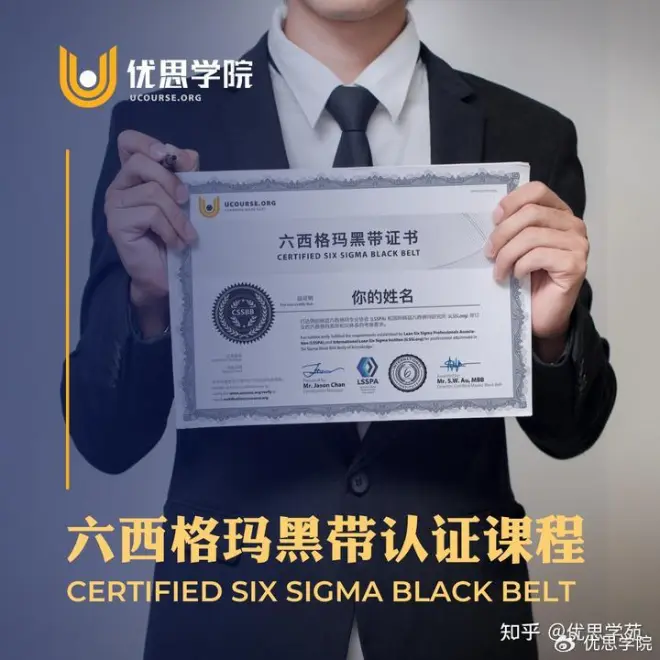
?