材料|引線框架材料C19400
相比于Cu-Ni-Si和Cu-Cr-Zr系引線框架用銅合金,Cu-Fe-P系合金在開發(fā)成熟度、綜合性價比、應(yīng)用廣泛性等方面都具有顯著的優(yōu)勢,因而占據(jù)了整個引線框架材料用量的65%以上,其中,析出強化型C19400合金又是Cu-Fe-P系中最具代表性的合金品牌[1]。
過去的30年,國產(chǎn)C19400銅合金精密帶材不僅產(chǎn)能小,而且產(chǎn)品表面質(zhì)量、力學(xué)性能等較難滿足市場要求,因而國內(nèi)消費主要依靠進口。自2008年大卷重、高控制精度、工藝功能較為完備的國產(chǎn)現(xiàn)代化銅板帶熱軋機組研制成功以來(解決了在線高溫固溶處理技術(shù)難題)
C19400合金成分及性能
C19400合金是在銅中加入Fe、Zn、P等低固溶度元素,屬典型的析出強化型合金。根據(jù)合金元素及第二相在基體中的溶解度隨溫度的降低而減少的基本條件,利用熱加工終了溫度進行固溶處理,在隨后的變形過程中將消除加工硬化退火和時效析出處理結(jié)合起來,使第二相盡可能得以充分的析出,進而提高合金的強度與導(dǎo)電率。
由Cu-Fe相圖可知,在835℃時,面心立方的-Fe轉(zhuǎn)變?yōu)轶w心立方的-Fe,此時最大的固溶度達到4.0%。室溫下,F(xiàn)e幾乎不溶于Cu中,以-Fe形式析出,如果有P存在,可以生成細小的Fe2P或Fe3P,從銅基體中析出,能夠?qū)辖鹌鸬郊毦娀淖饔肹2]。
微量合金元素的添加,能有效改善C19400的性能,但加入量要進行合理控制[3]。C19400合金化學(xué)成分及力學(xué)性能見表1。
表1 C19400合金化學(xué)成分及力學(xué)性能
Table 1 Chemical composition and mechanical properties of C19400 alloy
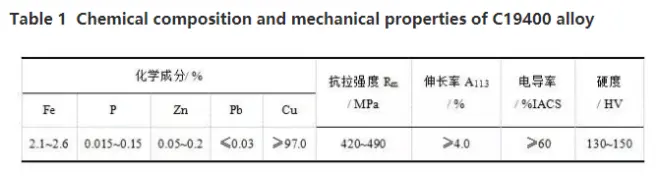
C19400熱軋工藝特點
2.1 工藝流程
相比于紫銅、黃銅等銅及銅合金,C19400比較顯著的特征是需要熱軋后進行高溫固溶處理。利用現(xiàn)代化銅板帶熱軋機組生產(chǎn)C19400的工藝流程為:鑄錠再加熱→鑄錠出爐→熱錠傳送→鑄錠對中→氧化皮吹掃→軋邊輥軋邊→多道次熱軋→高溫固溶處理→頭尾矯直→帶材冷卻降溫→空氣吹掃→液壓剪切頭尾→帶材卷取→料卷運輸。
2.2 熔煉鑄造
含F(xiàn)e2.1~2.6%的C19400銅合金熔點為1090℃,固相線為1084℃,因而其液-固相區(qū)域較窄。一般銅液溫度控制在1150~1190℃為宜,同時應(yīng)采用較低的鑄造速度。鑄造時,隨溫度的降低,會析出一定量的二相粒子(-Fe、Fe2P、Fe3P混合物)。二相粒子能夠阻礙位錯的運動,并對晶界起釘扎作用,使晶粒不會明顯長大,但應(yīng)對二相粒子的大小、形狀、分布進行控制,以使合金的高溫性能好,利于熱軋開坯。若鑄錠冷卻速度快,析出的第二相聚集長大,呈粗大的樹枝狀和針狀分布,使材料各向異性,造成高溫時材料的橫向性能差,變形時合金易產(chǎn)生沿晶斷裂尤其是熱軋開裂現(xiàn)象。
2.3 鑄錠再加熱
在C19400鑄錠熱軋前,應(yīng)進行再加熱,使內(nèi)部元素擴散,降低鑄造應(yīng)力,利于熱軋開坯。再加熱溫度一般低于固相線溫度約100~200℃,但應(yīng)能保證最難溶二相粒子的完全固溶。根據(jù)Cu-Fe 合金相圖,C19400鑄錠加熱溫度一般控制在930~980℃范圍內(nèi),加熱與保溫時間正比于鑄錠厚度而控制在3~5個小時內(nèi)。
爐生一次氧化皮是C19400鑄錠加熱后表面最主要的氧化層。對C19400鑄錠的加熱溫度、加熱與保溫時間、爐內(nèi)氣氛尤其是含氧量等進行有效控制可以減少鑄錠表面的氧化皮厚度。生產(chǎn)時,現(xiàn)場采用表2中的工藝參數(shù),有效保證了C19400的開軋、終軋溫度,并減少了爐生一次氧化皮的厚度。
圖1 C19400銅合金帶材熱軋
Fig. 1 Hot rolling of C194 00alloy strip
C19400特殊的工藝需求給熱軋機組提出了較高的要求,因此,在設(shè)備細節(jié)設(shè)計上考慮較為周到:
(1)C19400鑄錠出爐后熱輻射溫降約0.8~1.1℃/s,如要保證30℃以內(nèi)的溫降,鑄錠出爐后的運輸時間應(yīng)保證在30s以內(nèi)。通過減少加熱爐到軋機的距離、改進鑄錠出爐的方式,以及提高運輸輥道速度等方法都有效滿足了C19400開軋溫度的需求;
(2)在軋邊輥設(shè)置上,改變以往線外大立輥的模式,在軋機內(nèi)機前機后都設(shè)置了C型結(jié)構(gòu)的軋邊輥。在對邊部質(zhì)量進行控制、限制寬展的同時,參與軋制過程使帶材形成后張力,進而有效改善了帶材的板形;
(3)為了減少帶材溫降,軋輥采用盒式冷卻,減少了濺落到帶材表面的乳液,同時也提高了帶材的表面質(zhì)量。
C19400鑄錠熱軋后要進行在線高溫固溶處理,帶材終軋溫度最低不能低于710℃,而固溶處理后的溫度應(yīng)控制在300℃以下。所以,在熱軋機組最高軋制速度在150~180m/min的前提下,如何保證C19400高于710℃的終軋溫度就顯得非常關(guān)鍵。其解決途徑有:(1)提高熱軋開軋溫度;(2)減少軋制道次;(3)在線加熱或保溫。但加熱溫度的提高不能是無限制的,或者會導(dǎo)致過熱、過燒,嚴(yán)重時無法熱軋;而在線加熱保溫一般為爐卷軋機所使用的工藝。因而,銅板帶熱軋機組在實際應(yīng)用時,只能在保證開軋溫度的情況下,通過減少軋制道次,盡量提高軋制速度(會增大軋制力)的方式來進行C19400的控軋控溫。
為了提高生產(chǎn)效率、減少帶材溫降、大壓下充分破碎再結(jié)晶晶粒,機組在前期11道次試軋、9道次試軋基礎(chǔ)上能夠?qū)崿F(xiàn)對210×620×8000mm規(guī)格的C19400大鑄錠進行7道次大壓下高速軋制,這在大鑄錠銅板帶生產(chǎn)工藝領(lǐng)域具有極其重要的意義:
(1)體現(xiàn)了機組的較高控制能力;
(2)突破了鑄錠咬入工藝技術(shù)難題;
(3)大壓下能充分破碎再結(jié)晶晶粒,進而達到細化晶粒的目的;
(4)減少了軋制時間,能夠降低鑄錠及帶材表面的氧化層厚度;
(5)單個鑄錠實際生產(chǎn)時間可以節(jié)省5min左右,提高了生產(chǎn)效率;
(6)節(jié)能降耗并減少人工時,有效降低產(chǎn)品的生產(chǎn)成本。
經(jīng)過優(yōu)化后的C19400大鑄錠7道次軋制規(guī)程見表3。