888脫硫催化劑 東獅牌888脫硫催化劑
一、888脫硫催化劑的應(yīng)用
1. “888”脫硫催化劑有降低懸浮硫和降低化工原材料消耗的能力(已在該公司得到驗證)
1.1 懸浮硫
由于“888”脫硫催化劑是酞菁鈷磺酸鹽系金屬高分子有機化合物,析出的單質(zhì)硫,比重較大,再生槽硫泡沫易分離,并且相當(dāng)穩(wěn)定,懸浮硫很容易就控制在0.3g/L以下。不像栲膠法脫硫工藝,再生槽析出的單質(zhì)硫疏松,顆粒大(須狀顆粒較多),不能夠完全分離,控制在0.5g/L以下較為困難。我們自投用“888”脫硫催化劑以來,,貧液中懸浮硫的工藝指標(biāo)一直控制在0.3g/L以下。
1.2 化工原料和化學(xué)品消耗
脫硫工藝化工原材料的消耗,主要是看純堿的消耗,它是一個重點控制指標(biāo)。在煤氣入口硫含量不高時,通過堿耗高低就能判斷和反映出脫硫工藝的管理、設(shè)備設(shè)計和工藝運行的好壞。堿耗的高低主要取決于處理煤氣量和入口硫化氫的含量,除選擇質(zhì)量好的催化劑、配備合理的設(shè)備以外,硫酸鹽高是導(dǎo)致其消耗高的主要原因。若副鹽控制不好,會導(dǎo)致堿耗成倍增加,應(yīng)如何控制呢?我們應(yīng)加強對脫硫液指標(biāo)的管理,例如溶液溫度高、貧液懸浮硫高、再生電位偏離、溶液在再生槽的停留時間過長、熔硫釜產(chǎn)生殘液處理不當(dāng)?shù)鹊龋寄軐?dǎo)致副鹽升高,對此我們應(yīng)加強控制和重視。再則,“888”本身就有脫硫功能強和降消耗的功效顯著,我公司自投用該產(chǎn)品后,化工原材料和化學(xué)品消耗指標(biāo),在全國同類型企業(yè)中,已連續(xù)多年處于先進(jìn)水平,也是我們建脫硫工序以來最好水平,詳見下表。
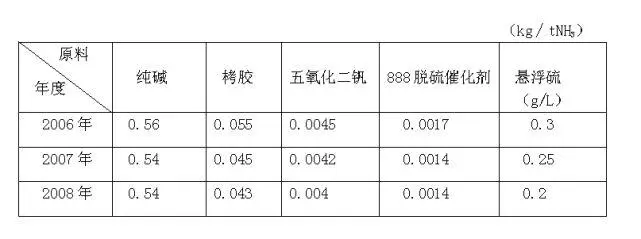
來百度APP暢享高清圖片
2.“888”脫硫催化劑有溶瀉硫的作用
“888”脫硫催化劑在我公司使用以來,脫硫塔阻力一直保持在450mmH2O柱以下,十分穩(wěn)定,避免了過去每次系統(tǒng)停車都要清塔現(xiàn)象,實現(xiàn)了連續(xù)多年穩(wěn)定運行的良好局面,為降低生產(chǎn)成本節(jié)約了大量的人力、物力和財力。
3. 有脫有機硫的功效
我們脫硫工序除脫合成氨半水煤氣硫化氫外,還負(fù)責(zé)甲醇水煤氣的脫硫任務(wù)。2003年由于煤種發(fā)生變化,甲醇凈化工序總硫迅速上漲,經(jīng)分析有機硫含量占95%,為了防止觸媒中毒,在無可奈何的情況下,只好減機減負(fù)荷生產(chǎn)。事后接到集團公司安排,該項任務(wù)必須由我們工序想辦法處理。按照我們栲膠法脫硫,只脫無機硫、不脫有機硫的工藝,對于我們來說是個新問題。經(jīng)我們研究決定,利用“888”脫硫催化劑來解決該問題,經(jīng)過幾天運轉(zhuǎn),問題得到了解決,現(xiàn)已連續(xù)多年運行,甲醇系統(tǒng)總硫一直保持在150 mg/m3--300mg/m3,其中COS保持在100mg/m3左右。利用“888”脫硫催化劑,確保了甲醇催化劑的使用壽命和甲醇生產(chǎn)的高負(fù)荷穩(wěn)定運行,為降低甲醇生產(chǎn)成本做出了巨大貢獻(xiàn)。
二、888脫硫催化劑在半水煤氣脫硫中的應(yīng)用
浙江某公司現(xiàn)有一條50kt/a噸雙氧水生產(chǎn)線,該生產(chǎn)線消耗氫氣約10.50km3/a,約需17.50KNm3/a半水煤氣,該半水氣中含硫化氫1.5g/Nm3左右,如不經(jīng)處理排放會對環(huán)境造成很大的影響。為此,公司于2008年初投資興建了一套半水煤氣栲膠脫硫裝置,但脫硫效果一直沒達(dá)到預(yù)期的效果,因此于2009年8月份改造為888脫硫裝置,采用長春東獅科技(集團)有限責(zé)任公司的888脫硫催化劑,取得了明顯的效果。
采用888脫硫催化劑法脫硫情況
⑴由于公司采用栲膠法脫硫工藝一年多來運行一直不穩(wěn)定,脫硫效果達(dá)不到要求,為此,2009年10月將栲膠法脫硫工藝改為888脫硫工藝。采用長春東獅科技(集團)有限責(zé)任公司生產(chǎn)的888脫硫催化劑,并在東獅公司人員的指導(dǎo)下對工藝進(jìn)行了調(diào)整,脫硫設(shè)備在原栲膠脫硫設(shè)備的基礎(chǔ)上進(jìn)行了一定的改進(jìn),增加了888活化槽等設(shè)備,各工藝指標(biāo)迅速達(dá)到要求,化學(xué)品消耗大幅降低,工藝運行情況,詳見表3。
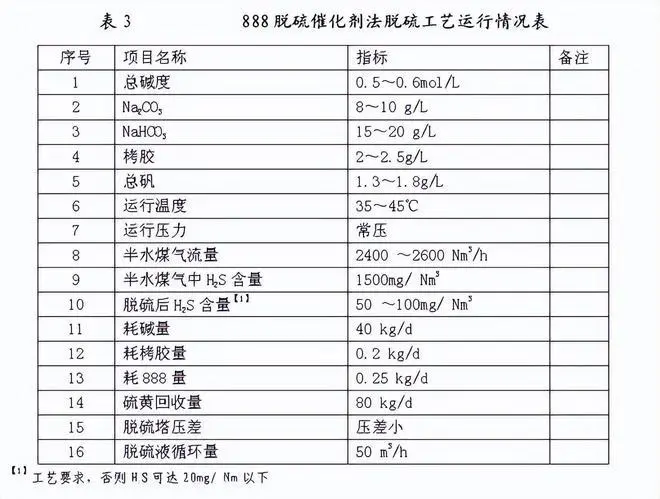
⑵由以上數(shù)據(jù)可知,采用東獅888脫硫催化劑并經(jīng)東獅公司人員的現(xiàn)場指導(dǎo)改進(jìn),我公司的半水煤氣脫硫迅速達(dá)到了預(yù)期的效果,其優(yōu)越性主要表現(xiàn)在以下幾個方面:
①脫硫效率高,可達(dá)95%以上,而且運行穩(wěn)定,出口硫化氫含量可達(dá)20mg/ Nm3以下(但因后續(xù)工序低變催化劑對硫的要求,人為控制在50~100mg/ Nm3)。
②消耗低,每天堿耗只有栲膠法時的一半,催化劑用量也很低,化學(xué)品總消耗量只有原來的一半。
③不易堵塔,脫硫塔壓差上升慢。
④脫硫液循環(huán)量小,只有栲膠時的50%左右,電耗低(循環(huán)泵由原來的22kw改為7.5kw)。
通過以上分析可知,用888脫硫催化劑代替栲膠脫硫工藝更加穩(wěn)定,硫容高,脫除硫化氫的能力完全能夠符合工藝要求,出硫率高,能耗低,脫硫劑消耗低。同時栲膠法改用888脫硫催化劑法,對半水煤氣進(jìn)行硫化氫脫除,各種設(shè)備基本不需調(diào)整,只需要增加888活化罐等小設(shè)備就行。
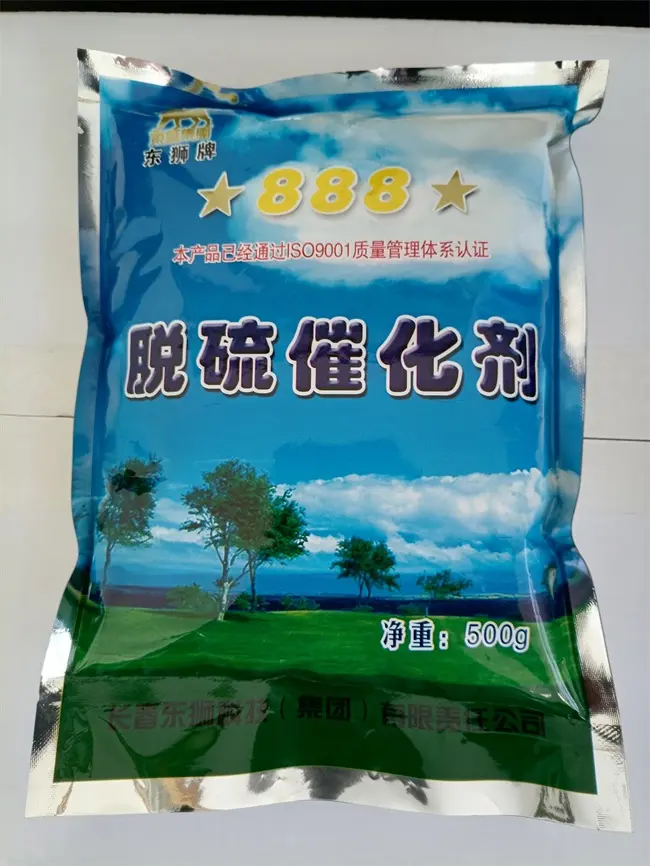