基于MLT模型的鋪層復(fù)合材料漸進失效分析
一.復(fù)合材料漸進損傷與MLT模型長久以來,對于復(fù)合材料層板結(jié)構(gòu)的剛強度分析通常都采用經(jīng)典層合板理論,這種被長期廣泛使用的理論在預(yù)報典型層合薄板結(jié)構(gòu)的剛度問題時,具有較好的精度,但由于典型層合板結(jié)構(gòu)的失效模式多種多樣,同時具有不同失效模式相互耦合的特點,因此在極限強度的預(yù)報方面存在一定的局限性。為了克服這一問題,有多種損傷理論模型被提出,而這其中漸進損傷模型是研究最多,最容易工程應(yīng)用的一種損傷模型。復(fù)合材料的漸進損傷模型屬于連續(xù)介質(zhì)損傷機理范疇,與研究復(fù)合材料內(nèi)部單一宏觀裂紋擴展演化的損傷模型(如VCCT)不同,這類模型重點研究的是微觀損傷對材料性能造成的影響(Talrija,1985)。一般來說,對于UD鋪層復(fù)合材料,不同的微觀缺陷類型對宏觀材料性能的影響也不同。
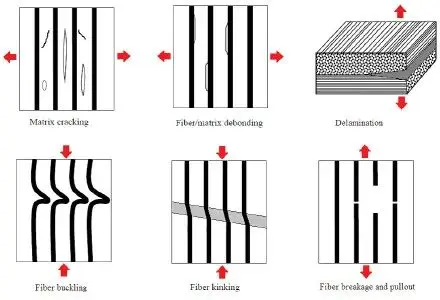
?圖1?復(fù)合材料失效模式(Guangyan, 2007)
微觀開裂或微觀空隙:出現(xiàn)在基體相中,主要影響材料橫向拉伸和剪切方面的宏觀性能。
纖維脫粘:出現(xiàn)在纖維和基體界面上,主要影響材料的軸向和橫向拉伸性能。
纖維微觀屈曲或彎曲:出現(xiàn)在纖維上,發(fā)生時通常伴隨有纖維脫粘,主要影響材料的軸向壓縮性能。
纖維斷裂:出現(xiàn)在纖維上,主要影響材料的軸向拉伸性能。
層間開裂:出現(xiàn)在相鄰鋪層之間,主要導(dǎo)致面內(nèi)和法向性能下降。
根據(jù)連續(xù)介質(zhì)損傷力學,微觀損傷對材料的影響可以被看作材料中存在微小孔隙,這些孔隙會導(dǎo)致材料內(nèi)部的實際應(yīng)力高于外部測量得到的表征應(yīng)力,也可以表現(xiàn)為帶有缺陷的材料的剛度低于無損傷材料的剛度。一維的表征應(yīng)力與真實應(yīng)力
的關(guān)系可以簡單的表征為:

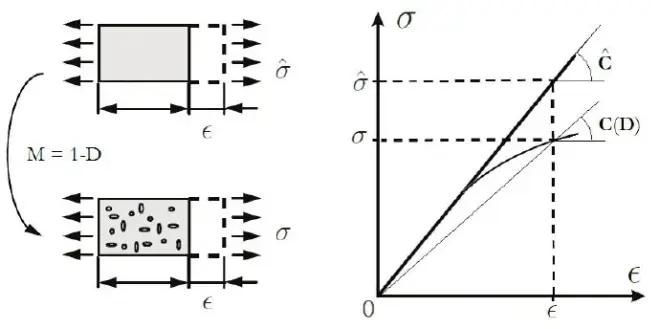
?圖2?損傷力學基本模型其中D為損傷系數(shù)。根據(jù)這一模型,三維表征應(yīng)力的本構(gòu)關(guān)系可以表征為:
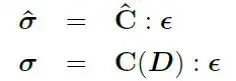

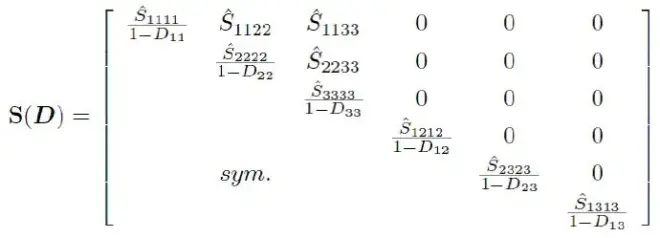
其中,

為無損傷條件下的材料剛度,S為有損傷的表征剛度,損傷因子D包含六個分量。表征泊松比可以通過下式計算得到:

這里需要注意的是,表征剛度矩陣S并不是對角陣,因此在單向應(yīng)力條件下,當橫向表征應(yīng)力為0時,橫向真實應(yīng)力未必為0。

漸進損傷模型的關(guān)鍵在于描述損傷因子D的產(chǎn)生和演化過程。損傷因子D可以表征為真實應(yīng)力的函數(shù),也可以表征為某失效準則系數(shù)的函數(shù)。數(shù)學上對D的基本要求包括:

Matzenmiller-Lubliner-Taylor損傷模型,或稱Hashin損傷模型是一種用于UD復(fù)合材料的漸進損傷模型(Matzenmiller et al. 1995).該模型將損傷因子D描述為關(guān)于Hashin失效準則系數(shù)的函數(shù)。3D的MLT模型將損傷因子描述為:



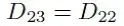
其中Hashin 3D失效準則系數(shù)可以表征為:





在Digimat中,損傷因子D與Hashin失效因子之間的函數(shù)關(guān)系?可以定義為多種函數(shù)形式,從而可以較靈活的描述損傷的發(fā)生和演化過程。Digimat支持的損傷演化函數(shù)包括:階躍函數(shù)損傷演化模型:
圖3階躍函數(shù)損傷演化模型冪函數(shù)損傷演化模型:
圖4?冪函數(shù)損傷演化模型指數(shù)函數(shù)損傷演化模型:
圖5?指數(shù)函數(shù)損傷演化模型線性軟化損傷演化模型:
圖6?線性軟化函數(shù)損傷演化模型二.3D復(fù)合材料孔板漸進失效分析采用三維實體單元分析復(fù)合材料孔板的拉伸失效過程。為了準確描述各層剛度的損傷退化過程,對每一層劃分獨立的實體單元。對于實體單元,不能通過層合板模型來定義鋪層方向,因此需要根據(jù)鋪層信息,對每一層單元定義獨立的材料坐標系。
圖7?復(fù)合材料孔板的有限元模型
孔板的鋪層定義為(45/0/0/-45/90)2s,共計20層,每層0.125mm,共計2.5mm厚。
在Digimat-MF中創(chuàng)建UD材料模型,材料的工程常數(shù)參見下表,UD的纖維體積含量為65%。
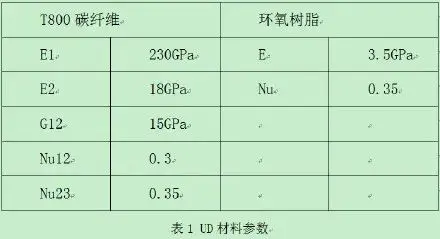
UD的失效描述選擇Hashin 3D失效模型,強度參數(shù)如下所示:
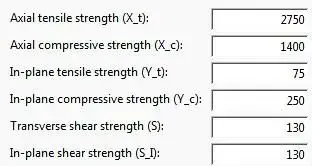
圖8 Hashin 3D失效強度漸進失效過程選擇階躍函數(shù)的MLT 3D模型來描述脆性的材料剛度退化過程,定義當Hashin失效準則達到1時,損傷發(fā)生并達到最大值,損傷后的殘余剛度為原始剛度的1%。
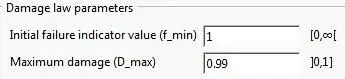
在Digimat-MF中定義1方向的單向拉伸載荷,可以看到材料在應(yīng)變1.8%處發(fā)生損傷,損傷后材料剛度下降至初始剛度的1%。
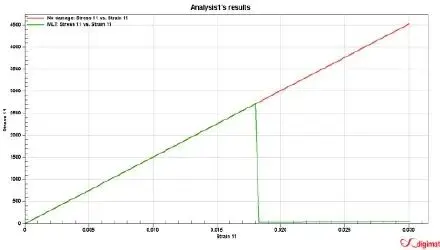
圖10 UD的脆性漸進損傷通過Digimat-CAE將Digimat的材料模型插入Marc的有限元模型中,提交計算。在后處理結(jié)果中可以觀察到損傷因子D11和D22的演化過程,分別代表纖維的損傷和樹脂的損傷。
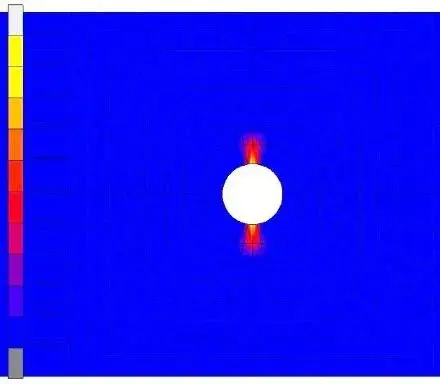
A:90度層率先出現(xiàn)樹脂損傷(1.2mm處);
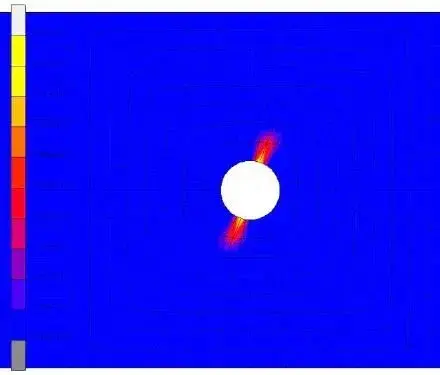
B:90度層的樹脂損傷引發(fā)纖維損傷(1.32mm處);
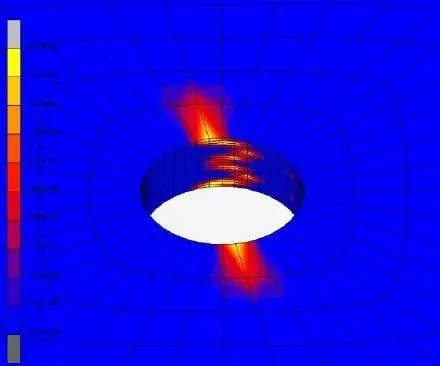
C:纖維損傷蔓延至孔邊所有層(2.28mm處);
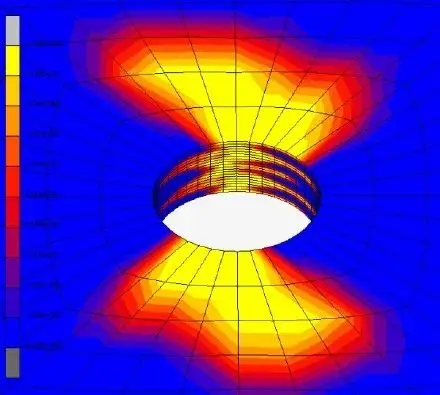
D:樹脂損傷擴展到孔邊所有層(2.34mm處)圖11?損傷演化過程:復(fù)合材料孔板當拉伸至1.2mm時,孔邊0度鋪層率先出現(xiàn)損傷,基體的破壞導(dǎo)致纖維在1.32mm處也發(fā)生了損傷。隨著90度鋪層的損傷,表層的45度鋪層也在1.32mm處發(fā)生樹脂損傷,并在1.68mm處損傷蔓延至芯層45度鋪層的基體上,但僅限于孔邊,未發(fā)生進一步擴展。拉伸至2.22mm處,0度鋪層出現(xiàn)纖維損傷,進而引起正負45度鋪層發(fā)生纖維損傷(2.28mm)和0度鋪層出現(xiàn)基體損傷(2.34mm),從而導(dǎo)致?lián)p傷大面積擴展和孔板剛度大幅度下降,最終導(dǎo)致孔板斷裂。????輸出加載點的位移和反作用力可以得到孔板的力-位移曲線,根據(jù)曲線可知,孔板的極限拉伸位移約為2.5mm,最大強度約出現(xiàn)在2.35mm處,根據(jù)損傷結(jié)果可知,此后孔板所有層的纖維和基體都發(fā)生了損傷,孔邊剛度極具下降引起損傷的快速擴展,從而導(dǎo)致孔板整體拉伸剛度的顯著下降。
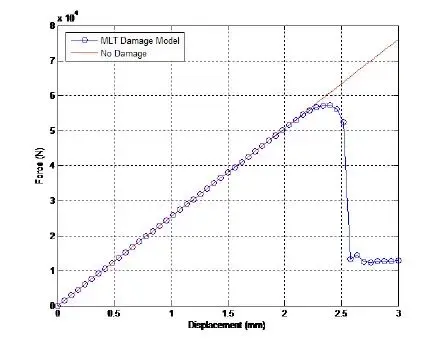
圖12?孔板力-位移曲線比較考慮損傷和不考慮損傷情況下,損傷導(dǎo)致的剛度下降比例,可以了解損傷對孔板整體剛度影響的演化過程。可以看出在加載到1.9mm后,孔板出現(xiàn)了可觀察到的剛度衰減。此時損傷開始在孔邊90度和45度鋪層中擴展,相同角度鋪層,外側(cè)鋪層損傷較內(nèi)側(cè)鋪層嚴重。
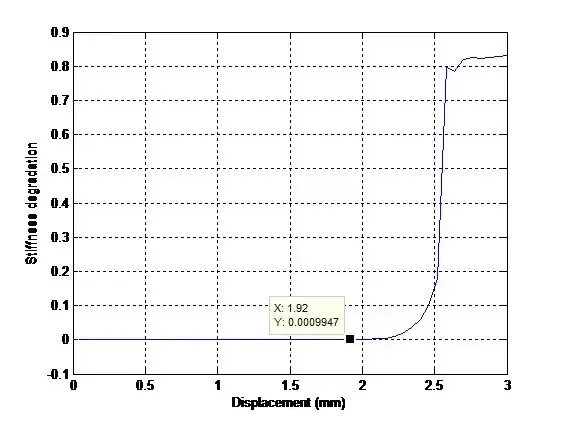
圖13?孔板整體剛度衰減過程
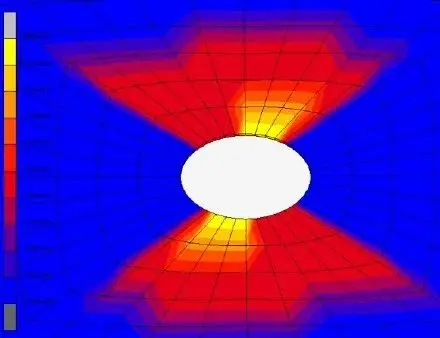
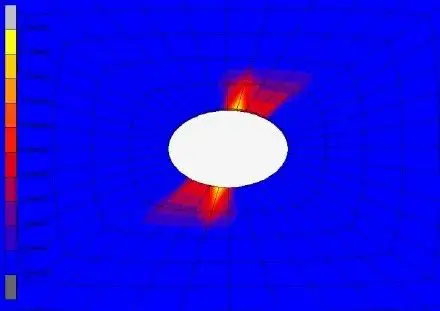
圖14?外側(cè)90度鋪層(左)與內(nèi)測90度鋪層(右)的基體損傷情況通過計算剛度衰減率的增量可以了解剛度衰減速率的變化情況。由下圖可以發(fā)現(xiàn),在加載2.28mm之前,雖然可以觀察到剛度衰減,但衰減速率降低,結(jié)構(gòu)上表現(xiàn)為孔邊鋪層雖然發(fā)生損傷,但損傷并未迅速擴展。2.28mm之后,孔邊所有層的纖維都發(fā)生了損傷,導(dǎo)致孔邊剛度極具下降,損傷開始向內(nèi)部擴展,整體剛度衰減速率明顯加快。
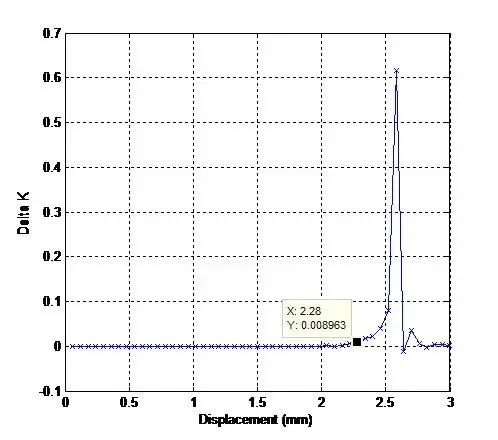
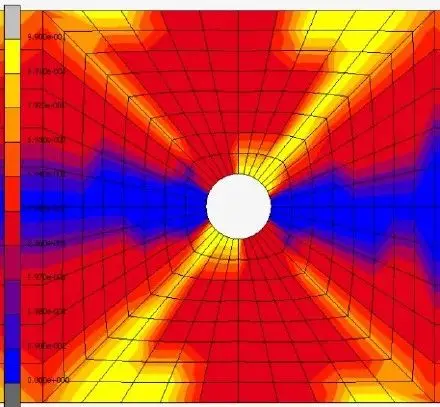
圖15?孔板整體剛度衰減速率變化及90度鋪層樹脂損傷向板內(nèi)部蔓延
cr:MSC軟件的博客。版權(quán)歸原作者所有,僅用于學習等,對文中觀點判斷均保持中立,若您認為文中來源標注與事實不符,若有涉及版權(quán)等請告知,將及時修訂刪除,謝謝大家的關(guān)注!