熱電廠汽輪機油系統(tǒng)集中檢查技術(shù)規(guī)范
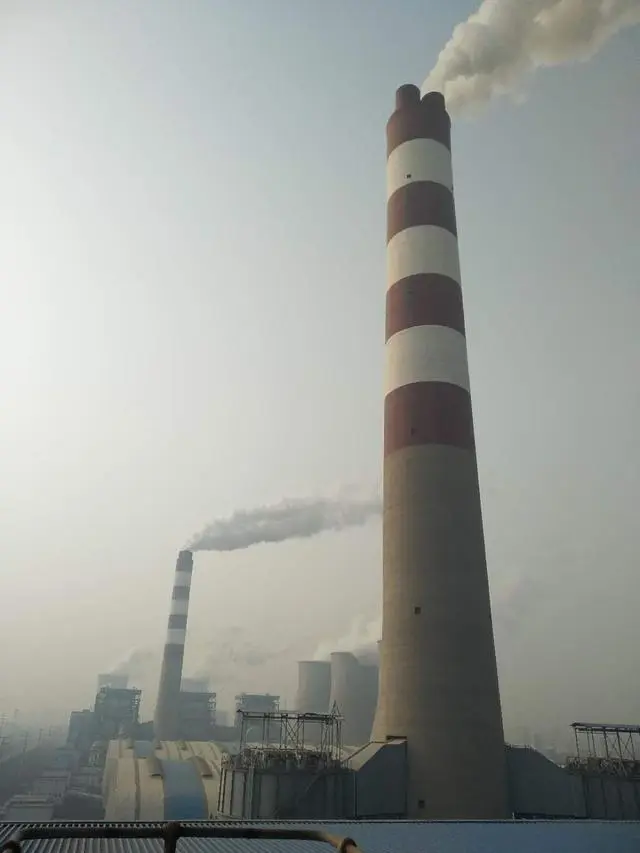
一、油系統(tǒng)管道安裝要求:
1.油系統(tǒng)管道的管件要求:
1.1變徑管應(yīng)采用鍛制式,大管徑可采用鋼板焊制。
1.2油管的法蘭應(yīng)盡量使用對焊短管法蘭,使法蘭焊接時不產(chǎn)生變形,用于公稱壓力低于PN10的法蘭,一般應(yīng)比其工作壓力相應(yīng)的等級提高一級。
1.3壓力油系統(tǒng)管道應(yīng)使用鋼質(zhì)閥門,壓力油管應(yīng)使用無縫碳素鋼管。
1.4除與設(shè)備連接必需外,一般不采用活接頭連接。
1.5油管道應(yīng)盡量減少法蘭接口和中間焊口,DN50 及以下油管應(yīng)采用全氬弧焊接,其他油管焊接時應(yīng)采用氬弧焊打底,并進行無損探傷。油管道焊縫的坡口類型、焊口間隙及焊接檢驗應(yīng)按DL/T 869《火力發(fā)電廠焊接技術(shù)規(guī)程》
1.6管子和閥門的荷重應(yīng)由支吊架承受,不得承受在設(shè)備上或油管接頭上。
1.7對汽輪發(fā)電機需隔絕軸電流的各部位與油管連接時,應(yīng)注意加裝必要的絕緣件,組裝前應(yīng)檢查絕緣件完好無損,并應(yīng)安裝正確。為便于測量絕緣,可裝設(shè)雙道絕緣法蘭。
1.8管道上的兩個成型件相互焊接時,應(yīng)按設(shè)計加接短管。
1.9高壓合金鋼管道表面上不得引弧試電流或焊接臨時支撐物。
1.10油管與基礎(chǔ)、設(shè)備、管道或其他設(shè)施應(yīng)留有膨脹間距,保證運行時不妨礙汽輪機和油管自身的熱膨脹,與存在脹縮位移的設(shè)備部件、管道連接的小油管應(yīng)符合膨脹補償規(guī)定。
1.11油管外壁與蒸汽管道保溫層外表面應(yīng)有不小于150mm 的凈距,距離不能滿足時應(yīng)加隔熱板。運行中存有靜止油的油管應(yīng)有不小200mm 的凈距,在主蒸汽管道及閥門附近的油管不宜設(shè)置法蘭、活接頭。
2.管子對接焊縫位置應(yīng)符合設(shè)計規(guī)定。否則,應(yīng)符合下列要求:
2.1焊縫位置距離彎管的彎曲起點不得小于管子外徑或不小于100mm。
2.2管子兩個對接焊縫間的距離不宜小于管子外徑,且不小于150mm。
2.3支吊架管部位置不得與管子焊縫重合,焊縫距離支吊架邊緣不小于50mm。
2.4焊后需作熱處理的接口,該距離不小于焊縫寬度的5倍且不小于100mm。
2.5管子接口應(yīng)避開疏、放水及儀表管的開孔位置,距開孔邊緣不應(yīng)小于50mm,且不應(yīng)小于孔徑。
2.6管道需穿過隔墻、樓板時,位于隔墻、樓板內(nèi)的管段不得有接口。穿墻及過樓板的管道所加套管應(yīng)符合設(shè)計規(guī)定。當(dāng)設(shè)計無要求時,穿墻套管長度不應(yīng)小于墻厚,穿樓板套管宜高出樓面或地面25-30mm。管道與套管的空隙應(yīng)按設(shè)計要求填塞。當(dāng)設(shè)計沒有明確給出要求時,應(yīng)用不燃燒軟質(zhì)材料填塞。
3.抗燃油系統(tǒng)管道還應(yīng)符合下列要求:
3.1抗燃油系統(tǒng)的管路、接頭、油箱等材質(zhì)均為不銹鋼,不得采用銅質(zhì)材料。
3.2抗燃油管路及部件的清洗不得使用氯化物溶劑.管路安裝前用蒸汽沖洗干凈,并用無油壓縮空氣吹干。
3.3所有小口徑不銹鋼管路優(yōu)先使用管子割刀下料,不得使用砂輪切割機或火焰切割,管端必須光潔無毛刺。
3.4螺紋接頭處用聚四氟乙烯帶做密封料,包纏時螺紋端部前兩扣不包。
3.5抗燃油系統(tǒng)密封圈采用氟橡膠圈。
4.頂軸油管的安裝還應(yīng)符合下列要求:
4.1油泵進出口與油管的連接應(yīng)正確。
4.2安裝前管子、接頭和軸瓦孔道均應(yīng)吹掃干凈。
4.3盡量減少管子接頭并應(yīng)采用套管焊接,由高壓合格焊工施焊。
4.4接至軸瓦上的頂軸油管均應(yīng)考慮膨脹補償;每根管子上的閥門與單向閥均應(yīng)嚴密不漏。
4.5頂軸油泵的安裝位置應(yīng)使油泵入口保持一定壓力,并在入口加設(shè)濾網(wǎng)。
4.6通向每一軸承的頂軸油管上應(yīng)裝設(shè)頂軸油壓表,并應(yīng)裝有單向節(jié)流閥。油壓表應(yīng)經(jīng)校驗合格,表管應(yīng)有阻力圈。
4.7頂軸油泵體上部的漏油口應(yīng)接管至回油容器,該管應(yīng)盡量減小阻力。
4.8頂軸油管與發(fā)電機后軸承座連接時應(yīng)絕緣,絕緣接頭應(yīng)有足夠的強度
4.9頂軸油管接頭不得承受管道、閥門的荷重。
5.用活接頭連接的油管還應(yīng)符合下列要求:
5.1活接頭不得使用焊接的鎖母接頭:鎖母接頭必須用整塊金屬制成,不得使用焊接的鎖母接頭,配制時凸肩處應(yīng)有倒角,一般不宜采用管螺紋接頭,如需使用時宜采用聚四氟乙烯帶作墊料。
5.2球形鎖母接頭須涂色檢查,接觸應(yīng)嚴密。
5.3平口鎖母接頭應(yīng)加裝經(jīng)過退火的紫銅墊,厚度宜為lmm。
5.4管子接頭處應(yīng)呈自由狀態(tài),無強制連接情況,在對口嚴密緊的情況下,鎖母接頭應(yīng)有富裕的螺紋。
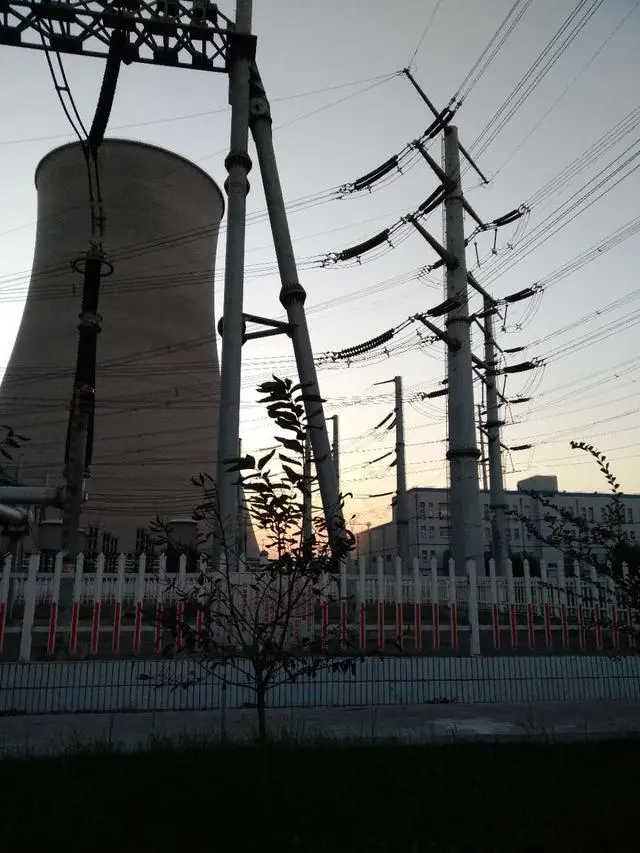
二、油系統(tǒng)管道附件安裝要求:
1.油系統(tǒng)應(yīng)盡量避免使用法蘭連接,禁止使用鑄鐵閥門。
2.油系統(tǒng)法蘭禁止使用塑料墊、橡皮墊(含耐油橡皮墊)和石棉紙墊。油系統(tǒng)法蘭全部墊片及密封膠圈,法蘭墊片厚度應(yīng)遵循調(diào)節(jié)控制油不超過0.5mm,潤滑油不超過1.5mm,其內(nèi)徑大于法蘭內(nèi)徑2-3mm,頂軸油系統(tǒng)、EH油系統(tǒng)密封圈應(yīng)使用氟橡膠和紫銅墊,禁止使用聚四氟乙烯、丁晴橡膠制品,使用紫銅墊時,應(yīng)進行回火處理。要求采用厚度小于1.5mm的隔電紙、青殼紙或其他耐油、耐熱墊料,以減少結(jié)合面縫隙。
3.油管道法蘭、閥門及可能漏油部位的周圍,必須對附近的熱力管道或其他熱體的保溫應(yīng)緊固完整,并包好鐵皮。油管外壁與蒸汽管道保溫層外表面距離不少于150mm,距離不足時,加裝隔熱板。
4.油管道法蘭、閥門及軸承、調(diào)速系統(tǒng)等應(yīng)保持嚴密不漏油,如有漏油應(yīng)及時消除,嚴禁漏油滲透至下部蒸汽管、閥門保溫層內(nèi)。
5.禁止在油管道上進行焊接工作。在拆下的油管上進行焊接時,必須事先將管子沖洗干凈。
6.事故排油閥應(yīng)設(shè)2個明桿鋼質(zhì)閥門,其操作手輪應(yīng)設(shè)在距油箱5m以外的地方,并有兩個以上的通道,操作手輪不允許加鎖,應(yīng)掛有明顯的“禁止操作”標(biāo)志牌。
7.油管道要保證機組在各種運行工況下自由膨脹。
8. 油管法蘭連接應(yīng)無偏斜,不得強力對口,法蘭螺栓必須對稱地均勻緊固。
9. 油管道伸縮節(jié)的安裝方向應(yīng)正確。管道上的閥門門桿應(yīng)平放或向下,防止運行中閥蝶脫落切斷油路。
10. 油管清掃封閉后,不得在上面鉆孔、氣割或焊接,否則必須重新清理。
11. 漏油后可能噴濺到高溫管道和設(shè)備上及沒有封閉設(shè)施的發(fā)電機引出線上的油管法蘭或接頭處,應(yīng)設(shè)上下對分的法蘭罩,罩殼最低點應(yīng)裝設(shè)疏油管。
12. 油管法蘭和其他容易漏油的連接件靠近高溫管道或處于高溫管道上方的油管密集處應(yīng)設(shè)防爆油箱。
13.防爆油箱底部應(yīng)有傾斜坡度,在最低位置應(yīng)接有足夠通流面積的疏油管,管子人口應(yīng)加蓖子。經(jīng)灌水試驗后應(yīng)無滲漏。
三、油系統(tǒng)管道支吊架安裝要求:
1.管道支吊架的形式、材質(zhì)、加工尺寸及精度應(yīng)符合設(shè)計圖紙的規(guī)定。
2.管道支吊架鋼結(jié)構(gòu)的組裝尺寸與焊接方式應(yīng)符合設(shè)計圖紙的規(guī)定。制作后應(yīng)對焊縫進行外觀檢查,不允許漏焊、欠焊,焊縫及熱影響區(qū)不允許有裂紋或嚴重咬邊等缺陷。焊接變形應(yīng)予矯正。合金鋼結(jié)構(gòu)的焊接應(yīng)符合DL5007《電力建設(shè)施工及驗收技術(shù)規(guī)范(火力發(fā)電廠焊接篇)》的規(guī)定。
3.滑動支架的工作面應(yīng)平滑靈活,無卡澀現(xiàn)象。
4.制作合格時支吊架應(yīng)進行防銹處理,并妥善分類保管。合金鋼支吊架應(yīng)按設(shè)計要求有材質(zhì)標(biāo)記。
5.支吊架生根結(jié)構(gòu)上的孔應(yīng)采用機械鉆孔。
6.所有活動支架的活動部分均應(yīng)裸露,不應(yīng)被水泥及保溫層覆蓋。
7.支吊架調(diào)整后,各連接件螺桿絲扣必須帶滿,鎖緊螺母應(yīng)鎖緊,防止松動。
8不銹鋼管道與支吊架之間應(yīng)墊入不銹鋼或氯離子含量不超過500ppm的非金屬墊片隔離。
四、其他要求:
1. 油系統(tǒng)管道間應(yīng)無摩擦,運行中油系統(tǒng)管道與其它管道或其它物體交叉、接觸磨擦?xí)r,應(yīng)加裝防磨墊并固定且滿足管道及軸承箱熱膨脹需求。機組運行中加強對油管道振動的監(jiān)督,定期對油系統(tǒng)管路的振動情況進行檢查測量,并做好記錄,油管異常振動時,立即分析原因并及時處理。
2.機組運行期間加強對前軸承箱處各壓力油管的監(jiān)督檢查,30MW、60MW機組重點加強對1#軸承箱油擋滲油情況的監(jiān)督,135MW、300MW機組加強#1、#2軸承箱油擋的監(jiān)督,油擋出現(xiàn)滲油情況時,立即設(shè)置收油盤,將漏油排放到安全的地方,汽缸保溫層不應(yīng)與軸承箱油擋接觸,防止油煙滲入保溫層內(nèi)引發(fā)不安全情況。
3.檢修人員和運行人員在巡檢過程中禁止踩踏油管道,運行人員每班要針對油管道所加膠皮墊的部位檢查,膠皮墊無脫落、不牢的情況,軸承進、回油管法蘭不應(yīng)覆于保溫層內(nèi),靠近汽輪機高溫部位的頂軸油管、潤滑油進、回油管的法蘭設(shè)置防護罩。
4.對油系統(tǒng)支吊架進行全面檢查,拆除油防護罩檢查油系統(tǒng)所有法蘭、閥門螺栓的緊固情況,并更換油系統(tǒng)中浸油的墊片,對前軸承箱內(nèi)壓力油管進行打壓試驗,解體檢查電磁閥、安全油切換閥、AST、OPC、伺服閥集成法蘭,密封圈應(yīng)完好,活接應(yīng)采用整塊金屬制成,球形接口應(yīng)嚴密,在對口嚴密壓緊情況下,鎖母接頭應(yīng)有富余的螺紋。
5.對小直徑壓力油管、表管要采取防震、防磨措施,加大薄弱部位(與箱體連接部位)的強度(如局部改用厚壁管),以防止振動疲勞或磨損斷裂引起高壓油噴出著火。
6.機組油系統(tǒng)的設(shè)備及管道損壞發(fā)生漏油,凡不能與系統(tǒng)隔絕處理的或熱力管道已滲入油的,應(yīng)立即停機處理。
7.壓力油管路附近和主油箱附近的照明應(yīng)盡可能選用防爆型燈具。
8.主油箱的濾油門、取樣門、底部放水門必須裝設(shè)兩道截門并應(yīng)上鎖.
9. 油管道要保證機組在各種運行工況下自由膨脹,油管道要有牢固的支吊架,油系統(tǒng)中的儀表管路應(yīng)盡量
