美國阿貢國家實驗室在鋰電池中研究進展
【研究背景】
目前鋰離子電池的研究主要集中在提高鋰電池性能,增加能量密度和延長電池壽命。高容量電極材料,如硅,可以顯著增加陽極的鋰存儲容量。然而,鋰離子電池用硅基電極的商業(yè)化一直受到(脫)鋰化過程中硅顆粒體積變化的嚴重阻礙。在(脫)鋰化過程中硅粒子的嚴重體積形變會導(dǎo)致電極的膨脹和收縮,隨著電解液的過度還原和固態(tài)電解液界面膜的形成,電池容量迅速衰減。許多研究人員曾報道過這種由鋰化誘導(dǎo)的硅顆粒形態(tài)轉(zhuǎn)變。理論計算表明,硅粒子的完全鋰化將產(chǎn)生約300%的體積膨脹。
在含硅電池中觀察到的各種衰退機制源于循環(huán)膨脹/收縮狀態(tài)。由連續(xù)的體積變化產(chǎn)生的內(nèi)部機械應(yīng)力促使顆粒開裂和粉碎導(dǎo)致活性物質(zhì)的電絕緣、新的固體電解質(zhì)界面層(SEI)在這些斷裂的粒子的形成、電解液和鋰離子的消耗,這些問題在商業(yè)應(yīng)用中尤為重要。膨脹還會引起集流器畸變,并可能導(dǎo)致有機隔膜中的孔閉合而減少離子傳輸。所有這些機制共同導(dǎo)致了硅基陽極容量衰減快、循環(huán)穩(wěn)定性差和庫侖效率低。鋰電池的實際體積能量密度取決于電極的膨脹: 電極膨脹的幅度越大,獲得的能量密度就越低。在設(shè)計硅基陽極電池時,監(jiān)測電極膨脹與電化學(xué)評估同樣重要。
【工作介紹】
有鑒于此,美國阿貢國家實驗室 Daniel P. Abraham教授和伊利諾伊理工 Leon Shaw教授使用原位電化學(xué)膨脹測試法來量化(脫)鋰化誘導(dǎo)的硅基和富石墨電極在電化學(xué)循環(huán)過程中的膨脹/收縮行為。作者評估了電極容量和膨脹之間的關(guān)系,發(fā)現(xiàn)硅含量增加時電極在鋰化時膨脹加劇。對于富硅陽極,電極的膨脹率可以高于300%,其膨脹曲線為低鋰化時緩慢膨脹,高鋰化時加速膨脹。作者還研究了電極的性質(zhì),如孔隙率如何影響電極的膨脹,并量化了電極的不可逆膨脹。最后,作者還提出了一些通過可靠數(shù)據(jù)總結(jié)的實驗方法和技術(shù)要點,用于設(shè)計電化學(xué)膨脹法。該研究成果以 “Electrochemical Dilatometry of Si-Bearing Electrodes: Dimensional Changes and Experiment Design”為題發(fā)表在Journal of The Electrochemical Society (DOI: 10.1149/ 1945-7111/abd465),第一作者為Andressa Y. R. Prado,通訊作者為 Leon Shaw和Daniel P. Abraham。
【內(nèi)容表述】
實驗采用了三種不同類型的電極:富硅/無石墨,富石墨/無硅和硅石墨混合電極。作者先對原始電極的孔隙率,復(fù)合涂層的面積載荷和厚度進行了估算;所有測試均采用含1 M LiFSI的電解質(zhì)。電極的額定容量是在紐扣電池中確定的,其值被用來定義膨脹儀循環(huán)協(xié)議。電化學(xué)測試過程為以C/20速率在100 mV和1 V之間進行3次恒電流循環(huán)。
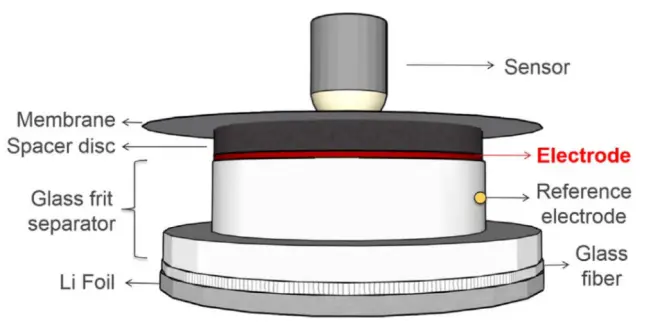
圖1: 電化學(xué)膨脹計電池示意圖。工作電極(紅色)的垂直位移通過薄金屬膜傳遞到傳感器。隔膜是一塊固定的多孔玻璃熔塊,因此,只有工作電極的尺寸變化能被檢測到。
該儀器使用分辨率為5nm的電容位移傳感器。主單元由一個由薄金屬膜密封的三電極電池組成。隔膜為固定在工作電極和鋰箔對電極之間的硬質(zhì)多孔玻璃熔塊;該設(shè)計保證只有工作電極的維度變化可以被檢測。金屬鋰作為參比電極,位于玻璃隔膜的側(cè)面。放置在對電極頂部的玻璃纖維圓盤有助于減少來自鋰箔的背景噪音。位于閥門頂部的隔離閥瓣保證了系統(tǒng)的電接觸。對于硅含量較低的電極,其膨脹值一般可在1 μm內(nèi)重現(xiàn)。然而,對于富硅電極,在高鋰離子含量下,當前集流體涂層偶爾分層會影響數(shù)據(jù)再現(xiàn)性。
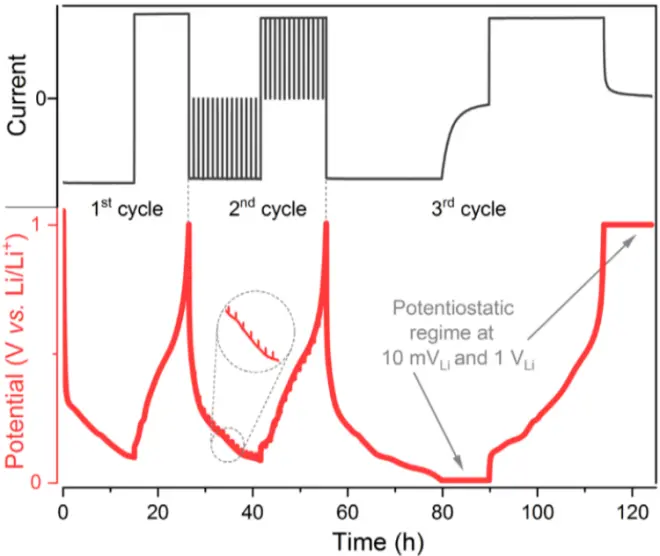
圖2:在膨脹實驗中電極電位(紅色)和電流(黑色)曲線變化。在第二個充放電循環(huán)中產(chǎn)生的電位尖峰(見插圖)是為了估計電池的歐姆極化而設(shè)計的電流中斷的結(jié)果。在第三次鋰化和脫鋰結(jié)束時,采用恒電位以最大限度地增加鋰離子的插入和脫出。
如圖2:在第一和第二次循環(huán)中,電極分別在100 mV 下充電至額定容量的100%和95%。在鋰化過程中,電流經(jīng)過調(diào)整,在15小時內(nèi)達到所需的荷電狀態(tài),在相同的電流下,將脫鋰過程進行到1 V vs Li/Li+。在第二個循環(huán)中,電流每小時中斷30秒,產(chǎn)生由弛緩過程引起的電位峰值(圖2突出顯示)。通過比較30秒前后的電位,可估計并校正電池歐姆極化; 從而得到實際電池電位與電極膨脹的相關(guān)性。在第三個循環(huán)中,電極的鋰化速度較慢,為C/25至10 mV vs Li/Li+,并保持該電位10小時,以確保電極的充分利用。并且最終脫鋰至1 V vs Li/Li+,然后恒電位保持10小時,以確保完全脫鋰。
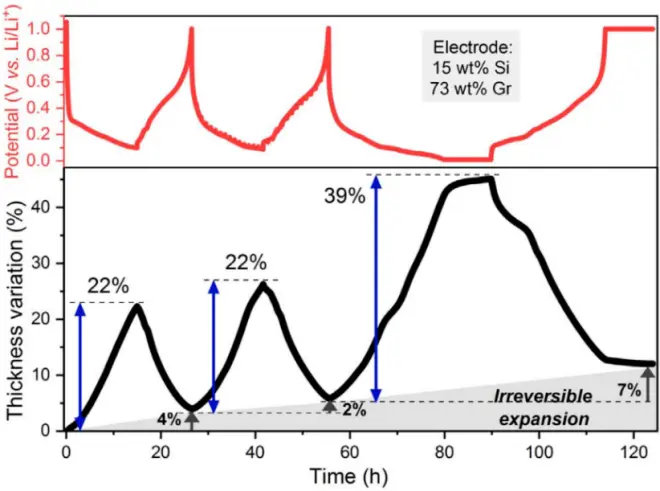
圖3:在三個循環(huán)中,15 wt% 硅 (73 wt% 石墨)電極的電位和相關(guān)厚度隨時間的變化。
圖3顯示了使用15% wt% 硅 (73 wt% 石墨)電極的膨脹實驗。紅色表示電壓曲線,黑色表示厚度變化與時間的關(guān)系。與第三循環(huán)相比,前兩次循環(huán)的電極鋰化至~100 mV vs Li/Li+,會導(dǎo)致一個較低程度的膨脹,在這個過程中,慢速充電速率及隨后的10 mV vs Li/Li+恒電位,陽極被完全鋰話。該硅電極在第一次和第二次循環(huán)中膨脹約22%,在最后一次循環(huán)中膨脹39%。脫鋰后的膨脹并沒有完全消除,電極在脫鋰狀態(tài)下的厚度隨著時間的推移永久增加,三次循環(huán)后的不可逆膨脹率為13%(4%、2%和7%)。
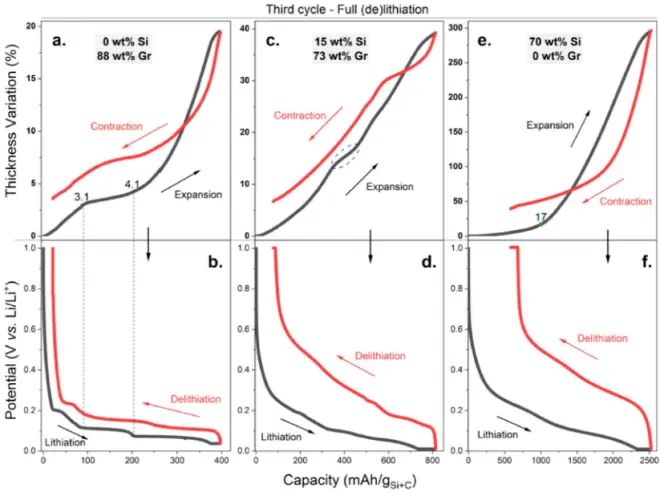
圖4: (a)(b)富石墨/無硅電極; (c)(d) 15% wt% 硅(73 wt% 石墨)電極; (e)(f) 70 wt%硅電極的第三個循環(huán)的厚度變化和電壓變化與比容量的關(guān)系。
圖4顯示了三種不同電極在第三個充放電循環(huán)過程中的厚度和電壓變化對電池容量的相關(guān)性曲線。黑色和紅色分別為鋰化和脫鋰過程中的電位演化曲線以及電極膨脹或者收縮。對于所有測試的電極,隨著更多的鋰離子到達活性材料和晶格重排,膨脹率隨容量增加。電位分布顯示了滯后效應(yīng),尤其是70%硅電極是非常顯著的。
對于富石墨/無硅電極(圖4a和4b),電壓曲線是由不同鋰化階段所產(chǎn)生的特征相變平臺所定義的。膨脹曲線與原位XRD及其他石墨膨脹學(xué)研究中檢測到的石墨單元電池電荷誘導(dǎo)體積變化曲線一致。如圖4a所示在階段3,電位高于120 mV,對應(yīng)Lix<0.25C6插層化合物的形成,膨脹曲線呈線性,達到約3.1%。在這之后,從第3到第2階段發(fā)生相變產(chǎn)物為LixC6(0.25<X<0.5),此時晶體有序度越高,膨脹曲線的斜率就越小,僅增加1%的電極厚度,總增加到4.1%。在 80 mV 時,另一個電壓平臺形成,第2階段相變完成, LiC12開始轉(zhuǎn)變?yōu)楦咪嚮腖iC6化合物。隨著鋰離子在每層間的插入,伴隨著電極膨脹的快速增加,導(dǎo)致完全鋰化時的總膨脹約為19%。與鋰化過程一樣,當鋰離子從石墨晶格層脫出時,電極的收縮曲線與相變過程一致,脫鋰初期體積快速收縮,當完全過渡到LiC12相時(145 mV處)速度放緩。當脫鋰完成后,電極的厚度永久增加3.5%。
當硅與石墨一起加入電極時,兩種活性材料的鋰化都會導(dǎo)致電極膨脹,因此膨脹曲線發(fā)生變化。由于石墨和硅的工作電位相似,兩種材料的電荷誘發(fā)膨脹疊加在圖中。對于硅-石墨 (15:73 w/w) 混合電極,通過比較圖4a和圖4c,作者觀察到硅的存在減弱了石墨相關(guān)的相變特征。然而,形成LiC12相過程的電位平臺,以及膨脹曲線上相關(guān)的電位平臺仍然存在,如圖4c中的藍色虛線圈所示。這一特性在無石墨電極中是觀察不到的,如圖4e所示。除了鋰化的開始和相變階段,15 wt%硅電極的膨脹曲線是成線性的,達到39%。關(guān)于脫鋰過程,觀察也為多步過程,鋰離子先后從石墨和硅中完全脫出。因此,收縮曲線的初始部分,也就是10-230 mV 的電位區(qū)域,與富石墨電極相似,因為在這個電壓范圍內(nèi),大部分鋰離子是從石墨相中脫出。從230 mV到1 V這一階段以后,硅開始脫鋰,其收縮速率幾乎保持不變。正如前面提到的,第三個循環(huán)導(dǎo)致了7%的不可逆膨脹。
當硅含量增加到70 wt%時,在沒有石墨的情況下,電極膨脹完全由硅納米顆??刂?,電極膨脹輪廓呈s形,如圖4e所示。該曲線包括在低荷電狀態(tài)下緩慢膨脹,隨后加速,然后在10 mV恒電位保持期間放緩。這導(dǎo)致在電極容量為40%時(1000mAh/gSi+C)有17%的膨脹,在滿容量時(2500 mAh/gSi+C)有300%的膨脹,如圖4e所示。由于電極孔隙率對顆粒膨脹的調(diào)節(jié)作用,在低鋰化狀態(tài)下觀察到的厚度變化緩慢。此外,原子尺度改變優(yōu)先于粒子級膨脹,因此在低鋰濃度下,鋰離子被插入到硅的粒子間隙,對原始結(jié)構(gòu)的影響很小。隨著進一步的鋰化,Si-Si鍵被破壞,結(jié)構(gòu)逐漸重新排列以適應(yīng)Si - Li合金化,這導(dǎo)致了相當大的結(jié)構(gòu)重組。在一定濃度的鋰離子下,當電極的孔隙度不再足以容納粒子的膨脹,粒子-粒子相互作用增強,電極膨脹急劇增大。在最初的脫鋰期,電極快速收縮(見圖4e),收縮率高于相應(yīng)的擴張率。在曲線的拐點處,收縮開始加速,盡管有70%的脫鋰容量還未完成,電極此時已經(jīng)收縮了73%。這表明,電極內(nèi)部的大多數(shù)結(jié)構(gòu)變化發(fā)生在鋰脫出的早期階段。脫鋰結(jié)束時,可觀察到厚度永久增加39%。
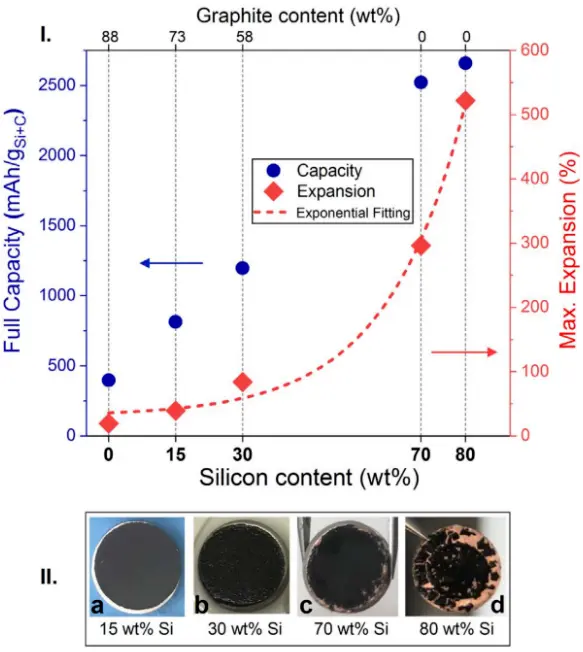
圖5:(I)各種測試電極完全鋰化后的最大膨脹(紅色)和比容量(藍色)作為硅含量的函數(shù)變化。(II)硅-石墨復(fù)合材料測試后的涂層:(a) 15:73 w/w (b) 30:58 w/w;(c) 70% wt% 硅和(d) 80% wt% 硅。
圖5總結(jié)了所有測試電極成分在完全鋰化過程中觀察到的最大膨脹和相應(yīng)的比容量。循環(huán)后電極表面形貌也給予展示( 注意,在70% wt%和80% wt% 硅電極上觀察到的分層可能發(fā)生在電池拆卸過程中)。
盡管重量容量(藍色)幾乎隨硅含量的增加呈線性增加,但膨脹(紅色)呈現(xiàn)指數(shù)增長:從15 wt%硅電極的39%到30 wt%硅陽極的84%,進一步到80 wt%硅電極的520%。當硅含量從70 wt%增加到80 wt%時,重量容量增益僅為140 mAh/gSi+C,然而,電極將受到額外的120%的膨脹。關(guān)于富硅電極的研究,盡管復(fù)雜的電極體系具有部分調(diào)節(jié)膨脹的機制,但電極的膨脹可能比理論顆粒尺度的膨脹大的多。這種行為是由于硅顆粒在鋰化和脫鋰過程中發(fā)生了大量不可逆的形態(tài)變化,而理論中沒有考慮到這些計算。如圖5c和6d所示,富硅電極的大量電極膨脹通常會導(dǎo)致活性物質(zhì)分層。
作者還總結(jié)了影響膨脹實驗結(jié)果的一些因素,包括:
電解液的選擇
測試是使用基于LiFSI的電解液進行的。當使用含LiPF6的電解質(zhì)進行膨脹測量時,在第一次鋰化過程中,在2.25 V 附近始終觀察到電壓平臺,這一高電位平臺與水的減少有關(guān),使用LiFSI電解質(zhì)時未檢測到這種情況。
極化
膨脹計電池包含一個厚的玻璃熔塊分離器,會導(dǎo)致電池阻抗增加,電極極化加強。由于這種極化,在高倍率下進行的膨脹實驗由于對容量的利用較小而低估了電極的實際膨脹。
電極孔隙度
電極孔隙可以部分容納單個粒子的膨脹。在低電荷狀態(tài)下,該部分緩沖區(qū)可以最大限度地減少電極膨脹。
傳感器漂移,施加壓力和滯留氣體
傳感器漂移、施加在電池堆上的負載和電池內(nèi)捕獲的氣體。漂移是一種低頻噪聲,它導(dǎo)致傳感器背景在整個實驗過程中緩慢變化。該效果受測試時間的影響,根據(jù)制造商介紹,對于膨脹電容式傳感器,漂移幅度為?20 nm h?1。對于長期測試,傳感器漂移會影響結(jié)果,特別是累積的不可逆膨脹數(shù)據(jù)
Andressa Y. R. Prado, Marco-Tulio F. Rodrigues, Stephen E. Trask, Leon Shaw,* and Daniel P. Abraham*, Electrochemical Dilatometry of Si-Bearing Electrodes: Dimensional Changes and Experiment Design,?Journal of The Electrochemical Society, 2020, DOI:10.1149/ 1945-7111/abd465
MatCloud+ |?計算?數(shù)據(jù)?AI,僅需網(wǎng)頁瀏覽器
文章來源于能源學(xué)人,作者Energist