納米反射鏡拋光技術:給予手機光學設計更多的可能
在手機的影像系統(tǒng)中,一般不會看到反射鏡,就算是潛望式長焦鏡頭,也一般會采用三棱鏡而非反射鏡,主要原因就是因為反射鏡的反光率較小,一般在85%(家用鏡)到95%(高端反射鏡)左右,而三棱鏡則可以做到最高98%的反射率。
但是在手機攝像頭中,除了潛望式長焦設計,還依然有很多設計需要用到反射鏡。比如潛望式長焦的三棱鏡可以換成反射鏡,以及上篇專欄提到的折返式長焦鏡。在這些鏡頭設計中,反射鏡的反射率較低,導致在反射過程中存在較多的光損失,從而限制了這類創(chuàng)新光結構在手機模組中的應用。因此,想要實現(xiàn)這些性能更好的模組在手機中的使用,就需要進行材料攻關,以加工出反射率超高的反射鏡來。
反射鏡的反射率和什么有關?
在反射鏡的反射率中,一般和兩個因素有關:反射材料和反射面精度。
在光入射到一種材料上時,光會同時發(fā)生反射和透射。對于透明材料,光的反射率遠小于透射率。對于金屬材料則相反,反射率遠大于透射率。不同的金屬材料反射率不同,一般對于銀材料,目前反射率最高可達99.5%。
而銀的99.5%的反射率也并非隨便鍍層就可以達到,因為家用鍍銀反射鏡的反射率只有85%左右。因此,這其中還涉及到另一個問題——即表面平整度還非常深刻的影響著反射率。對于家用反射鏡而言,表面的玻璃平整度一般為1微米左右的量級。因此,對于1微米平整度的表面,反射率就大為下降。這是因為銀粒子表面有很多凹凸,如圖,光線在其中不斷反射,每次反射都被吸收一點,最終反射射出時,光線的衰減就已經很大了。
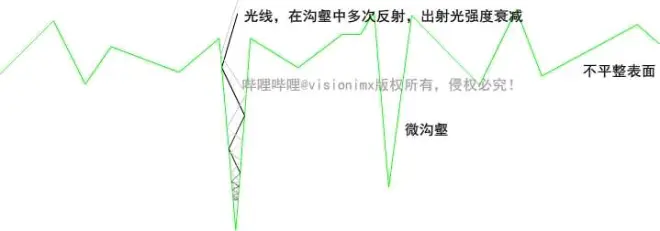
(這里補充一下,雖然在初中物理當中,一般會教我們光線在平滑表面鏡面反射,在粗糙表面漫反射。但是實際上,用10000目砂紙打磨的表面已經可以呈現(xiàn)出鏡面反射效果,此時表面粒度大概是2~3微米。因此就算粗糙表面,當粗糙度小于一定程度時,也可以發(fā)生鏡面反射,但是其中光線卻會在溝槽內不斷被吸收導致?lián)p失,從而導致反射率下降。)
提高反射率——新鍍層技術,以及提高表面平整度
為了提高反射率,讓反射鏡能夠媲美甚至超過三棱鏡的反射效果,科學家們主要從鍍膜技術和提高表面平整度兩個方向進行。這里介紹以下華為10倍潛望模組的反射鏡技術開發(fā)過程中用到的技術。
家用反射鏡反射表面凹凸不平的主要原因除了有玻璃表面的凹凸不平以外,還有鍍銀層的凹凸不平。在液相鍍膜(銀鏡反應)技術中,銀離子會先在溶液中還原,并聚合形成100~500nm直徑的銀粒子,之后通過布朗運動擴散到玻璃表面,被玻璃吸附。因此,這些有大有小的粒子在玻璃表面聚合形成的表面肯定不是光滑的,而是有一定孔洞溝壑,表面粗糙度約為500nm左右。因此,這種銀鏡反應鍍銀的方式雖然在宏觀上表現(xiàn)出反射鏡,但是因為反射率很低,導致實際上不能用在手機光學模組上。
那么,如何讓銀原子規(guī)規(guī)矩矩的在玻璃表面形成一個超級平整的表面呢?
首先,我們需要一個極致平整的玻璃表面??梢钥吹剑退闶清冦y原子極致平滑,假設玻璃表面凹凸不平,實際鍍膜效果依然會大打折扣。因此,我們需要研磨一個超級光滑的表面。在日常生活中打磨一般會用砂紙,再高級一點的會用研磨液,但是這些模組廠商所采用的研磨方法都不滿足精度需要,這些研磨方式最高只能研磨表面到100nm的精度,這也是手機光學模組廠對模組打磨精度的上限,一般手機潛望鏡當中的三棱鏡會用到這種精度。但是,由于反射面是鏡面而非全反射面,采用反射鏡需要更高的精度。如何做到這種精度呢?在華為和反射玻璃的供應商豪雅光學進行技術攻關的過程中,芯片(晶圓)的表面打磨拋光技術得到了關注。
在7nm以上的制程中,一般要求晶圓表面的精度要小于1nm。因此,晶圓表面拋光用到的方法雖然也是研磨,但是是特殊的CMP工藝(化學機械拋光,chemical-mechanical polishing)。CMP工藝采用化學蝕刻和機械研磨結合,對于玻璃來說,蝕刻液一般是熟悉的氫氟酸,但是為了獲得更平整的表面精度,氫氟酸的濃度很低。之后,研磨顆粒則是超細金剛石研磨顆粒,一般是化學方式形成的超小粒度金剛石,粒徑在20nm左右。這套借鑒了晶圓拋光方法的拋光方式,可以將玻璃表面最高做到30nm的拋光精度,雖然和真正晶圓1nm的表面精度沒法比,但是已經能夠顯著提升反射率,為下一步的銀原子鍍膜提供基礎了。
如下是當年有關于這項技術的報道:
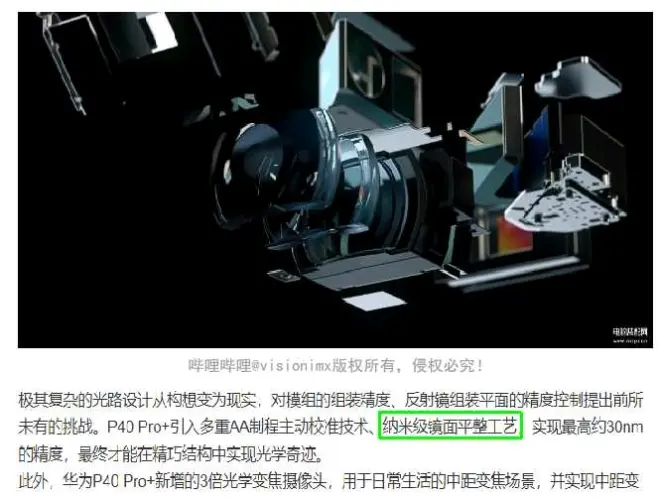
在實現(xiàn)這樣夢幻般平滑的表面以后,下面就是鍍膜了。
鍍膜技術也不會采用液相聚合法(銀鏡反應),讓銀原子先在溶液中聚合成幾百納米直徑的銀粒子,之后吸附到玻璃表面形成銀薄膜。這種方式導致表面形成幾百納米深度的溝壑,不夠平整。因此,為了避免這個缺陷,豪雅和華為共同開發(fā)了濺射鍍膜技術,通過將銀靶材解離成單原子,在電場和磁場的控制下到已經平整過的玻璃表面聚合,聚合形成的薄膜表面精度控制大概也是30nm量級。
此時已經形成了超高反射率的表面。但是為了讓這個表面能夠耐久,因為銀原子會和周圍空氣中的硫元素發(fā)生反應,形成多溝壑的硫化銀(銀飾戴久了光澤度下降也是因為硫化銀),因此,在形成這個表面之后,還需要在銀原子表面在鍍一層玻璃薄膜,形成帶反射的夾層。最后形成的即是超高反射率的反射鏡組件,這種反射鏡反射率可以達到99%,和潛望式長焦的三棱鏡差不多。
寫在結尾
當然,這個反射鏡本身成本相比反射三棱鏡肯定要高得多,因為畢竟反射三棱鏡加工表面最高做到100nm久夠了,但是反射鏡需要三個精度30nm的表面,以及復雜的拋光工藝和濺射真空鍍膜工藝,看似似乎得不償失。但是,當踏入無人區(qū)之時,新技術的攻關往往需要這樣的投入和勇氣。如果廠商一直待在研發(fā)的“舒適區(qū)”,只想著拿到供應鏈最厲害的技術就可以了,那么它永遠做不到第一,要做到第一就需要有創(chuàng)造這種人無我有的技術的勇氣。
超高反射率反射鏡制造技術本來并非特別需要攻關的技術,但是一旦攻關,就能形成很大的技術優(yōu)勢。比如華為的10倍長焦,通過反射鏡設計,減少了防抖模塊的重量,最終可以把光圈做到f/4.4(實際上由于特殊的光路設計,第一片鏡片直徑8.5MM),你看隔壁傳統(tǒng)三棱鏡防抖方案的三星最高就只能做到f/4.9的光圈,進光量輸了華為很多。并且由于反射鏡設計可以折疊光路,因此10倍模組雖然有這驚人的28.5MM物理焦距,但是體積卻并不是很大——和三星的對比一下就明白了。在之前并未向工程師了解過反射鏡的技術細節(jié)的時候,我一直覺得華為在鏡頭形態(tài),對焦,以及10倍體積控制的思路上非常具有創(chuàng)造性,但是現(xiàn)在看來,最不起眼的反射鏡,竟然是背后最高科技的技術。
而且,我認為10倍長焦可能只是該反射鏡技術的小試牛刀的場所,雖然這顆10倍模組已經在鏡頭形態(tài)上做了創(chuàng)新,但是顯然,有了這項技術的加持,就能馳騁更廣闊的天地——折返鏡頭,以及種種特殊形態(tài)的鏡頭就可以實現(xiàn)了,而假如把這項鍍膜技術獨占,不對供應鏈開放,那就意味著其他高度依賴供應鏈技術的廠商就會因為小小反射鏡被“卡脖子”——就是造不出來。因此,以折返鏡頭技術為例,在15*15*9MM的體積下,就可以塞下f/1.8光圈,等效140MM的1/2.5寸大底長焦;而同樣的,其他廠商想實現(xiàn)f/1.8,140MM,1/2.5寸,如果沒有超高反射率反射鏡技術,要用潛望式鏡頭做,需要40*15*11的超大體積,因此,就可以在更纖薄的機身內實現(xiàn)同樣效果。
因此,有些技術的投入可能看不到收獲,但是只要投入,終有一天它會得到用的地方,用上便可以實現(xiàn)更大的技術領先。因此,這也是我建議越來越多的廠商跳出供應鏈技術的舒適圈的原因——雖然現(xiàn)在暫時因為制裁,華為這種高度技術儲備的廠商拿不到豪雅的光學組件,ois,以及相關可以實現(xiàn)它的技術儲備的供應鏈,導致現(xiàn)在華為又站在同一起跑線上和各廠商拼供應鏈技術;但是,僅僅2年,華為就靠著p60Pro的長焦鏡組形態(tài)創(chuàng)新,在更纖薄的機身內實現(xiàn)了同樣乃至更好的效果,倘若未來國產元件效果成熟,華為把一些更小體積卻能達到相同甚至更好效果的模組用起來,那便是巨大的技術代差。