AGV車驅動輪打滑情況原因分析與應對措施
AGV車驅動輪打滑情況原因分析與應對措施
前言
對于所有運動的車輛結構來說,減震系統(tǒng)是非常重要的機構。從低端的二八大杠自行車,到轎車卡車,再到特種車輛,都少不了減震系統(tǒng)。
減震系統(tǒng)的主要作用一是保證動力模組和地面的摩擦力,以便提供充足的動力。二是減輕因地面不平時、過溝過坎時、地面突然出現(xiàn)高低落差對車體和貨物的沖擊,保護車體和貨物。
對于AGV車來說,即使沒有減震,也可以跑起來,但是對地面平整度要求很高,而且驅動的電機功率也要足夠大。實際情況設計了減震的AGV車要比沒有減震的AGV車運行狀態(tài)要好,要穩(wěn)定。
在實際的應用當中,我們經常遇到AGV車驅動輪打滑的情況,有的是因為沒有設計減震,有的設計了減震卻仍然出現(xiàn)打滑的情況,在這里我們針對這些情況做一個分析介紹。
AGV車驅動輪打滑主要原因如下:
1.?懸掛減震方面的問題
2.?輪子材質與路面的問題
3.?電機功率小的問題
4.?負載分布不均的問題
一 懸掛減震方面的問題
對于AGV車來說,設計減震懸掛的情況比較多,我們重點討論帶減震的情況進行分析。
AGV減震的設計原則:
1. 減震機構主要作用是保證動力模組和地面的摩擦力,以便提供較大的動力,保證輪子不打滑。
2. 減震機構可以減輕地面不平時、過溝過坎時、地面突然出現(xiàn)高低落差時、裝載貨物時,
輪胎承受的沖擊力,以免損壞齒輪和包膠輪。
3. 減震機構可以減輕貨物在 AGV 運行顛簸時受到的沖擊。
4. 減震機構應該盡量考慮在載貨和空載時 AGV 車體本身上下浮動范圍,越小越好。如果落差太大可能導致平行貨物對接失敗,裝載失敗等
減震的常見結構:
1.?杠桿式
2.?鉸鏈擺動式
3.?直導柱式
4.?四連桿式
5.?舵輪端減震
下面分別詳細介紹常見的減震結構
杠桿式
結構如圖所示:
?
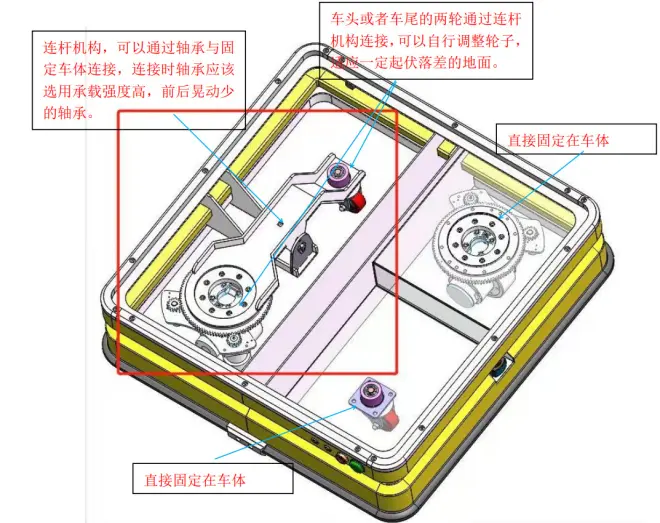
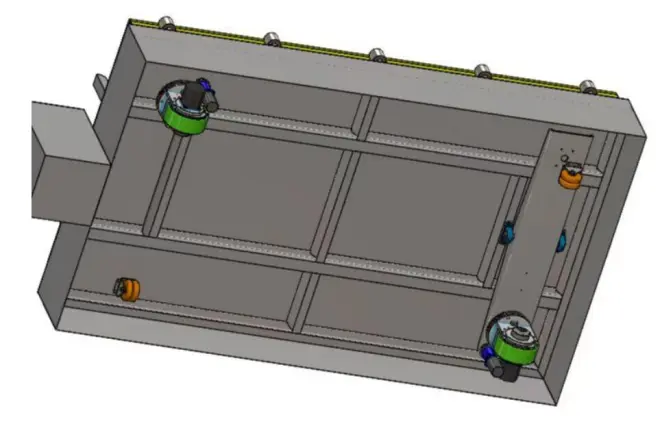
?
杠桿式特點及設計注意事項:
(1) 結構簡單,可靠性高,成本低,體積小,重量輕,車體本體配重小,基本免維護。
(2) 減震主體在 AGV 車體。
(3) 適用路面條件好,起伏落差不大場景。
(4) 缺點是載重量受限動力模組本身的承載限制,最大載荷理論上不超過動力機構最大承載的?4 倍,.實際使用時要考慮到設備沖擊和負載偏載,需要預留一定的安全余量。運動時舵輪承受沖擊力大。
(5) 設計注意:杠桿和車體連接部分承載部要可靠,回差間隙要小,避免運動時晃動??梢栽诟軛U兩頭加小型彈簧,增加一定阻尼,可以加速杠桿回零響應速度和防止維修吊起時,杠桿不受約束的情況下上下晃動,撞擊產生意外破壞和傷害。
?
杠桿式減震機構工作原理:
杠桿原理杠桿?分費?杠桿、省?杠桿和等臂杠桿,杠桿原理也稱為“杠桿平衡條件”。要使杠桿平衡,作?在杠桿上的兩個?矩(?與?臂的乘積)??必須相等。即:動?×動?臂=阻?×阻?臂,?代數式表?為?F1·L1=F2·L2。式中,F(xiàn)1 表?動?,L1 表?動?臂,F(xiàn)2 表?阻?,L2 表?阻?臂。從上式可看出,要使杠桿達到平衡,動?臂是阻?臂的?倍,阻?就是動?的?倍。
?
鉸鏈擺動式
結構如圖所示:
?
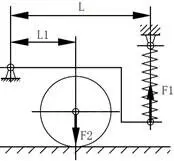
?
受力原理圖:F1*L=L1*F2
?
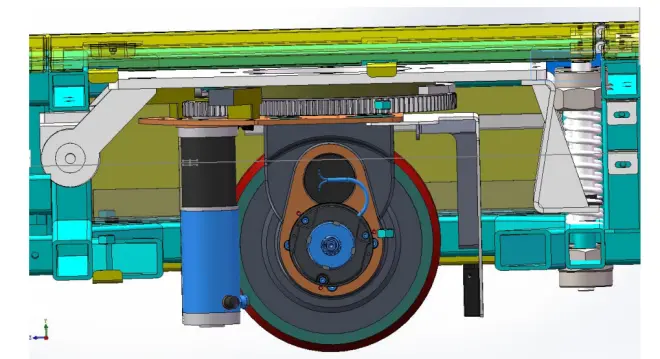
鉸鏈擺動式減震機構特點及設計注意事項:
(1) 結構較簡單,可靠性高,成本低,高度低,水平占地面積大,重量輕,AGV 車體可設計載荷大,壓力可調整,車體本體配重大,基本免維護。
(2) 減震主體在 AGV 車體或者舵輪上。
(3) 適合路面條件好,起伏落差較小場景。
(4) 缺點:舵輪上下浮動時,舵輪沿鉸鏈為圓心旋轉,舵輪觸地點相對安裝垂直中心偏移,布局位置微變,影響控制計算。車體本體需要較大配重,以便空載時將減震彈簧壓制至適合位置,萬向輪輕微觸地。壓力浮動變化較大,在舵輪下沉時,壓力損失較大,容易導致舵輪摩擦力急劇減少,導致舵輪打滑。鉸鏈受側向力時,容易變形,導致晃動加劇,尤其是?AGV 平移時。
(5) 設計注意,鉸鏈結構在側向運行時,鉸鏈受較大的軸向力,會導導致鉸鏈變形,晃動明顯。鉸鏈選用時,材料變形量要小,表面硬度要大,要耐磨,同時直線軸承也要選耐磨產品。
6)減震彈簧在選擇時,勁度系數選的要合適,并且做成行程可調,加防脫調節(jié)螺栓。選擇的原則是,空載時在車體自重的情況下,萬向腳輪能剛接觸到地面,重量大部分都壓載在舵輪上,重載時,舵輪壓力產生的摩擦力?F 大于 AGV 運行時的阻力 F1. 彈簧選擇時,建議可以選一些行程大,彈簧胡克系數較小,在車體在平地時,彈簧有較大的預壓行程?X,這樣在路面起伏時,X 變化較大時,彈簧產生的正壓力 F 變化小,在舵輪下沉時,舵輪摩擦力損失較小,在舵輪上浮時,舵輪所受正壓力不會增加太多,避免超過舵輪最大垂直載荷
?
垂直導柱式
結構如圖所示:
?
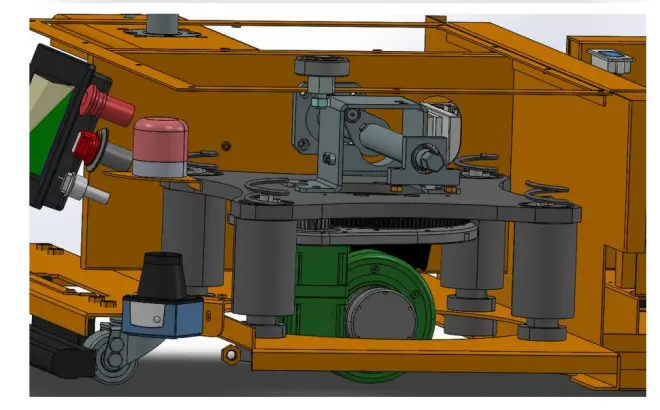
導柱減震機構設計于車體之上
?
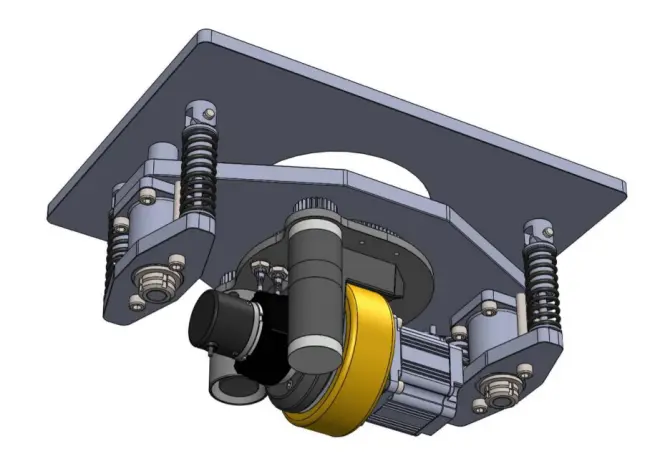
導柱減震機構設計于舵輪端
垂直導柱減震機構特點及設計注意事項:
(1) 結構較為復雜,可靠性高低主要取決于設計合理性和加工裝配工藝。成本高,水平面積小,高度高,重量適中,AGV 車體可設計載荷大,壓力可調整,車體本體配重大,需要定期維護清理和加潤滑劑。
(2) 減震主體在 AGV 車體或者舵輪上。
(3) 適合路面條件不好,起伏落差較大場景。
(4) 缺點是成本高,車體本體需要較大配重,空載時將減震彈簧壓制至適合位置,萬向輪輕觸地。壓力浮動變化較大,在舵輪下沉時,壓力損失較大,容易導致舵輪摩擦力急劇減少,導致舵輪打滑。導向柱受側向力時,容易變形,導致上下卡頓,失去減震作用。
(6) 設計注意:垂直導柱住數量不易過多,由于 AGV 車運動時,導向柱受較大的徑向力,會導致導向柱變形,卡頓,導向柱越多,卡頓現(xiàn)象越明顯。
導向柱要做的較為粗壯,材料變形量要小,表面硬度要大,要耐磨,同時直線軸承也要選耐磨產品。
減震彈簧在選擇時,勁度系數選的要合適減震彈簧在選擇時,勁度系數選的要合適,并且做成行程可調,加防脫調節(jié)螺栓。選擇原則是,空載時在車體自重的情況下,萬向腳輪能剛接觸到地面,重量大部分都壓載在舵輪上,重載時,舵輪壓力產生的摩擦力?F 大于 AGV 運行時的阻力 F1. 彈簧選擇時,建議可以選一些行程大,彈簧勁度系數較小,車體在平地時,彈簧有較大的預壓行程?X,這樣在路面起伏時,X 變化較大時,彈簧產生的正壓力 F 變化小,在舵輪下沉時,舵輪摩擦力損失較小,在舵輪上浮時,舵輪所受正壓力不會增加太多,避免超過舵輪最大垂直載荷。
?
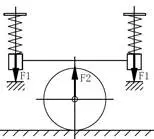
設計工作原理:可以做如下假設,驅動輪正壓力完全由減震彈簧提供(前提車體要做配重),車體總重全部分攤于輔助腳輪,按照經驗數值驅動輪不打滑的條件是正壓力不小0.3-0.5的驅動輪額定載荷,計算之后要保證車子加了負載后彈簧還有一定的壓縮行程。
?
四連桿式
結構如圖所示:
?
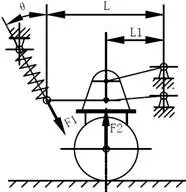
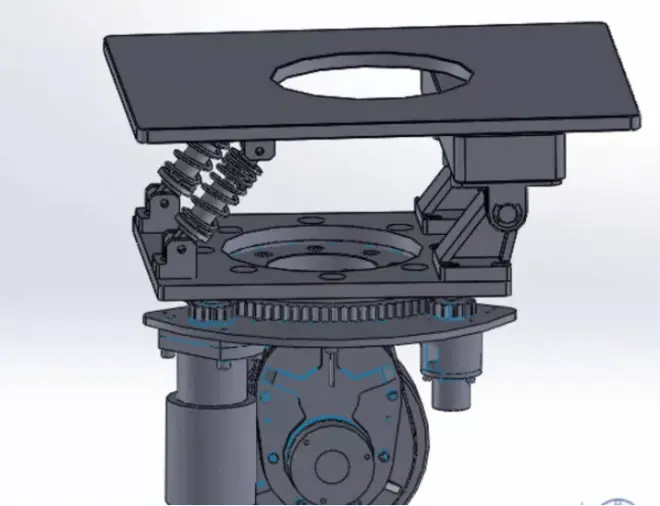
?
四連桿式減震特點及設計注意事項:
(1) 結構復雜,可靠性高,成本高,高度適中,AGV 車體可設計載荷大適用于大載荷車體,壓力可調整,車體本體配重大,
(2) 減震主體在 AGV 車體
(3) 提供更大的地面貼緊力,減震適應性較好。
?
舵輪端減震
結構如圖所示:
?
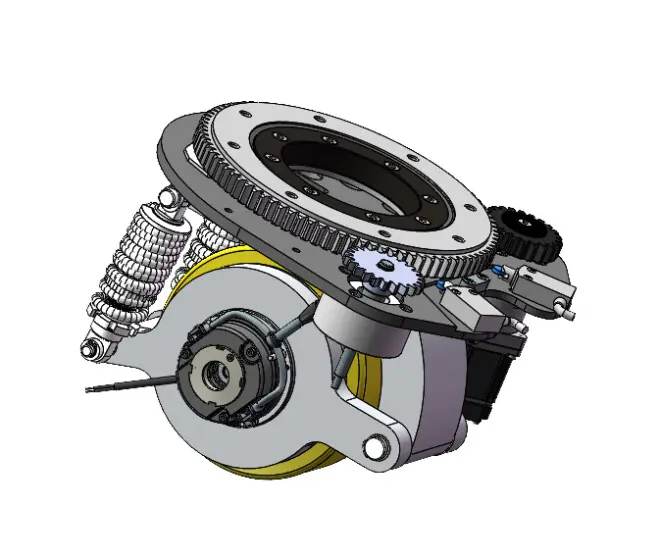
舵輪端減震特點及設計注意事項:
(1) 車體設計簡單,但是需要做配重
(2) 減震主體在 驅動輪上面
(3) 減震行程較小,調節(jié)空間小,一般彈簧不能自由調節(jié)
4)驅動輪定位精度不高,無法應用于定位精度要求高的場合
?
很多工程師雖然設計了減震機構,仍然出現(xiàn)驅動輪打滑的情況,那么需要考慮減震的彈簧壓力不夠,配重是否足夠,然后需要進行受力分析和計算,彈簧施加于驅動輪的壓力不能小于0.3-0.5倍的驅動輪額定載荷,受力計算方面沒有什么問題,則需要考慮其他方面的問題
二、輪子材質與路面
AGV驅動輪的材質一般是聚氨酯和橡膠。
聚氨酯材質的特點硬度高,彈性變形小,承載重量大,耐磨,應用的場合主要是室內平整地面,地面要求無油無水
?
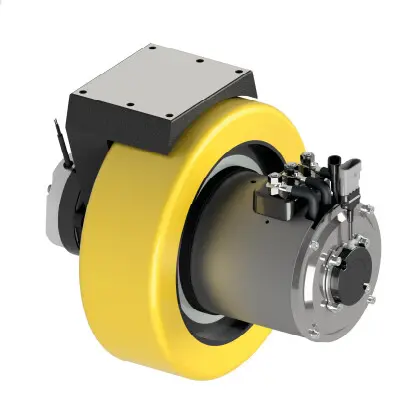
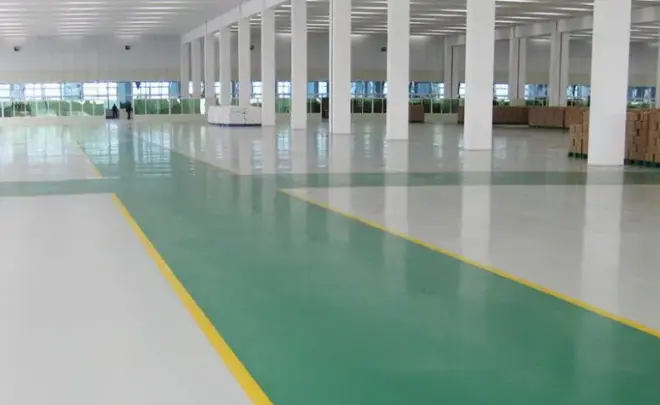
橡膠材質特點,硬度軟,彈性變形大,承載重量小,耐磨性較低,主要應用于戶外路況,路面有水有油污也可以使用
?
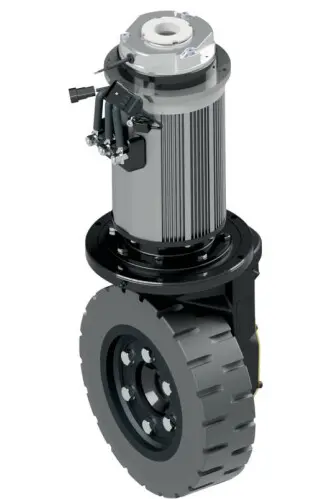
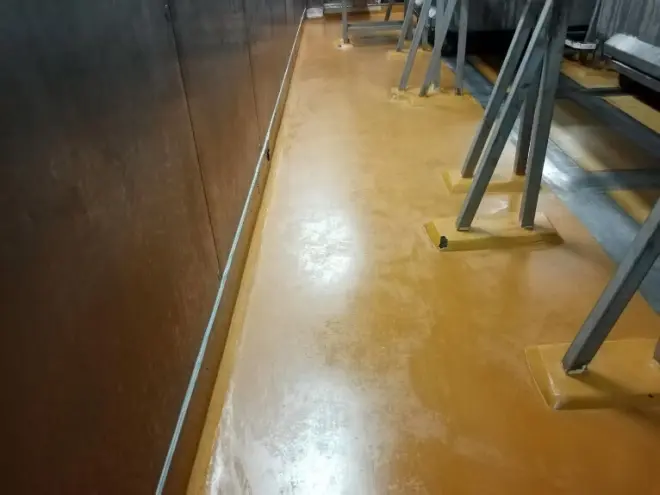
根據不同的路面環(huán)境選擇不同材質的輪子,也可以避免因為環(huán)境地面導致的輪子打滑情況
三、電機功率小
電機功率小導致舵輪打滑的情況分兩種,一種情況是電機的實際功率選小了,另一種情況,電機實際功率足夠,驅動器設置輸出功率小導致電機的實際輸出功率小了了。
第一種情況在設計選型階段對于電機的功率選擇過小,要么是選型階段計算錯誤,要么是沒有考慮到啟動與爬坡階段電機需要過載輸出
?
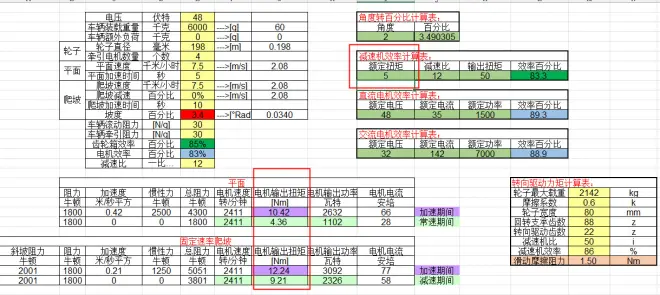
舵輪設計選型的時候建議先咨詢研發(fā)技術能力強的舵輪廠家,他們有豐富的選型經驗和科學的計算工具,例如我們江蘇億控智能裝備有限公司。
另外一種情況是電機的實際功率足夠,驅動器調試的時候輸出的電流過于保守過小,導致電機輸出功率不足導致輪子打滑
?
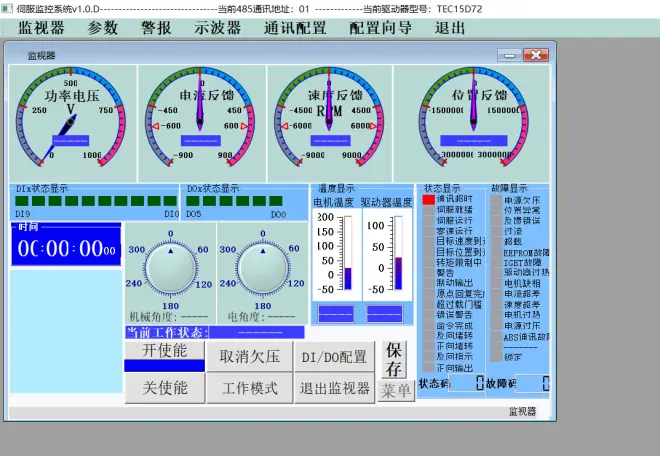
驅動器重新調試將輸出功率上限調高滿足要求,按照我們的驅動器選型與調試的經驗,驅動器一般最大可以做到3倍的過載輸出,但是需要根據驅動器的過載電流上限和過載時間,合理設置輸出上限述數值。
四、負載分布不均
雙舵輪車體如果出現(xiàn)負載不均勻,負載輕的一端舵輪也可能出現(xiàn)打滑情況,出現(xiàn)這種情況需要重新調整負載位置
總結:AGV車出現(xiàn)舵輪打滑的情況,首先進行問題分析,分析出原因,針對原因進行整改。一般我們優(yōu)先分析輪子材質與地面的問題這是最容易看到的問題,然后在分析減震方面的問題,分析減震結構是否合理,減震彈簧力是否足夠,行程是否足夠,以及車體配重是否足夠。減震問題排除了,我們就考慮電機的功率以及實際輸出功率,最后再考慮負載是否均衡。