這10個精益生產(chǎn)管理工具,你必須要會!
精益生產(chǎn)是當前工業(yè)界最佳的一種生產(chǎn)組織體系和方式,這里分享10個精益生產(chǎn)管理必備工具,希望對大家有所幫助!
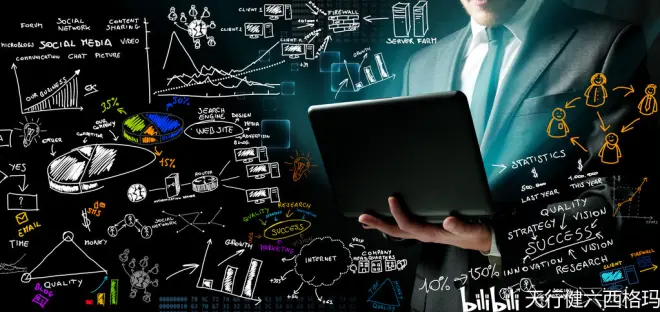
1.OEE設(shè)備綜合效率
衡量一個制造過程損失的綜合指標只需要將以下三個指標進行相乘即可:設(shè)備利用率(停機問題);設(shè)備效率(節(jié)拍問題);質(zhì)量率(缺陷問題)。100%的OEE則意味著完美的生產(chǎn):無停機,高節(jié)拍和無缺陷。
2.防錯
通過預(yù)防和探測缺陷以便實現(xiàn)最終(客戶端)的零缺陷。
3.根本原因分析
找到問題的根本原因,而非表面現(xiàn)象:比如5-Why方法。通過糾正措施消除問題的根本原因,使得問題更好更徹底地解決。
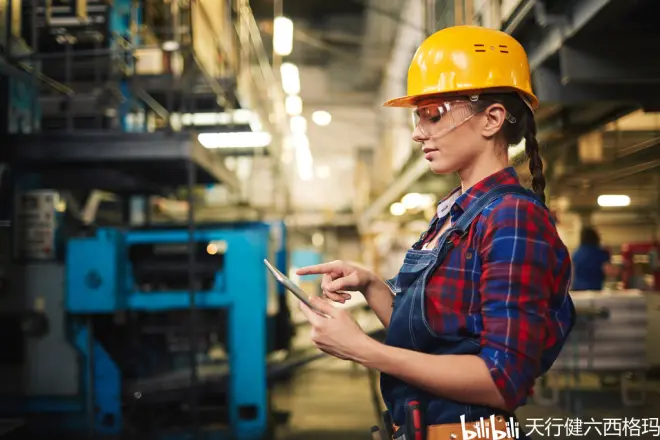
4.標準化作業(yè)
基于最佳實踐的,細化到每一個步驟的,可以歸檔的作業(yè)流程,可以用動態(tài)文件來支持必要時的更新。
5.SMART目標
設(shè)定以下目標:Specific具體化的,Measurable可衡量性的,Attainable可達成的,Relevant與戰(zhàn)略相關(guān)的,Time-Specific與時間期限相關(guān)的。
6.Takt Time節(jié)拍時間
基于顧客需求的生產(chǎn)節(jié)拍:節(jié)拍時間=計劃生產(chǎn)時間(有效時間)/顧客需求數(shù)量。如果按照顧客節(jié)拍進行生產(chǎn),既能夠滿足顧客又可以減少浪費。
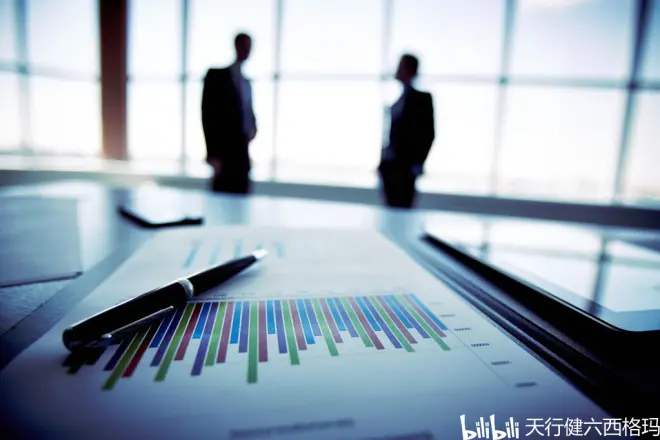
7.可視化工廠
通過使用電子看板,控制器,物理看板等裝置來實現(xiàn)工廠的可視化,透明化,并且還可以增強信息的溝通。如果將制造過程的狀態(tài)快速有效的展現(xiàn)給大家,可以減少不必要的浪費。
8.價值流圖
將當前和未來的生產(chǎn)流進行可視化的對比,以便可以尋找改進空間的方法。能夠解決暴露當前過程的浪費,同時以便繪制出未來改善路線圖。
9.六大損失
在制造過程中往往會存在六大生產(chǎn)率損失:機器故障,計劃外停工,需要換線,損壞,速度降低,質(zhì)量缺陷。
10.SMED快速換模
一種可以將換模時間減少到10分鐘以下的技術(shù)??焖贀Q模使得小批量在生產(chǎn)時,大大減少了換模時間的損失,降低了庫存,加大了客戶響應(yīng)。