降低生產(chǎn)批量,推動流線化,精益生產(chǎn)
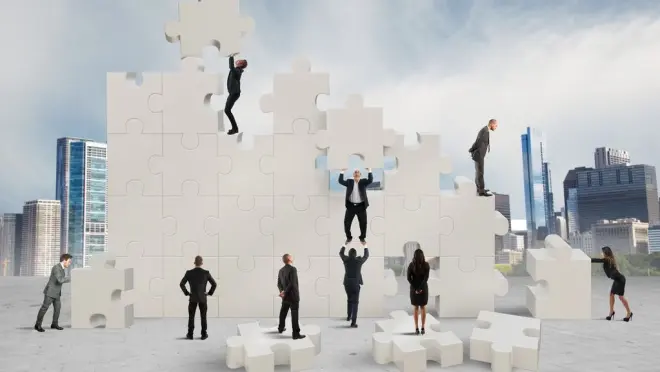
精益生產(chǎn)推動之初,一般都是通過建立標桿線的方式,這樣可以集中精力重點改善,容易取得顯著效果,并通過宣傳示范,起到推廣的作用,進而發(fā)揮全廠自主進行效仿改善的群體效應。
一、標桿線的選擇和運作需要一定的規(guī)范
1.標桿線產(chǎn)品選擇參考原則。
(1)盡量選擇有2條(含)以上生產(chǎn)線生產(chǎn)之產(chǎn)品,使其具可比性;
(2)選擇在生產(chǎn)線正常大量生產(chǎn)2個月(含)以上產(chǎn)品;
(3)產(chǎn)品還可在生產(chǎn)線上生產(chǎn)4個月(含)以上。
2.線體選擇參考原則。在優(yōu)先幾種原則要求的基礎上,對標桿線的選擇還應
考慮以下條件:
(1)人員定崗定位,且新人比例不大于50%(含);
(2)生產(chǎn)線穩(wěn)定生產(chǎn)2個月(含)以上。
3.標桿線管理系統(tǒng)建立。
(1)每日改善計劃及實績收集記錄;
(2)每日改善新聞展示、改善績效管控;
(3)每周總結改善成果。
標桿線改善點及管理機制如下圖所示。
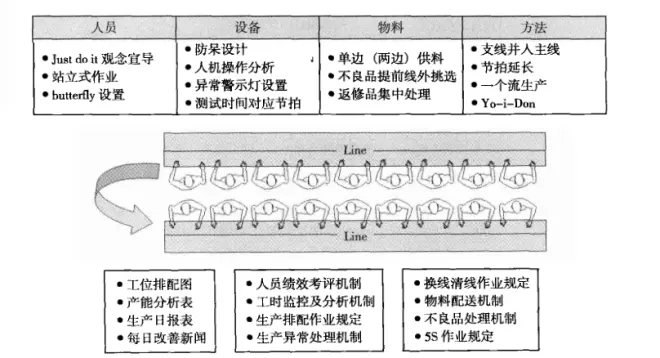
二、標桿線推動的第一階段是無間斷式生產(chǎn)
推行之初,先要求產(chǎn)品能夠進行連續(xù)性的生產(chǎn),過程中的在制品還有一定的堆積,但關鍵是流程盡量不能有中斷及過多搬運的現(xiàn)象,不能有大的堵塞現(xiàn)象,所以需要進行產(chǎn)能的總體平衡分析,并使得不良品不影響正常生產(chǎn)。(天行健精益生產(chǎn))主要推動內(nèi)容有:
1.按流程進行設備布局。改變傳統(tǒng)的按照設備功能進行布局的方式,按照產(chǎn)品的生產(chǎn)流程進行設備及流程布局,使得整體流程的走向呈現(xiàn)“一筆畫”式,減少流程中的交叉、迂回的物流形式。當然,如果流程中需要共享到高精尖的貴重設備或者某工序的加工環(huán)境特別,則可能變成一對多或者孤島式的布局形式。但這不應該影響整體的布局思維。
2.消除次組裝。除非次組裝的設備及加工環(huán)境特殊,否則,應該盡量將次組裝合并到主線之內(nèi),消除孤島式布局,并且消除次組裝的加工過剩的可能。
3.來料檢查及流程中不良品的線外處理。這樣可以保證主線能夠在正常情況下進行生產(chǎn),不受物料品質波動的干擾,防止生產(chǎn)中斷。
4.Andon機制的建立。生產(chǎn)線一旦出現(xiàn)異常,作業(yè)員及時發(fā)出指示,管理及技術人員及時處理,防止處理延誤造成較長時間的生產(chǎn)中斷。
5.產(chǎn)能平衡。根據(jù)生產(chǎn)提前期、生產(chǎn)節(jié)拍和生產(chǎn)能力,合理安排上下流程的對應生產(chǎn)順序及生產(chǎn)數(shù)量,防止生產(chǎn)過多而堵塞,生產(chǎn)過少而斷線的現(xiàn)象。在工序內(nèi)部,進行生產(chǎn)線平衡改善,使得生產(chǎn)線內(nèi)部產(chǎn)能平衡。
6.標桿線驗證。
(1)實際達成效果分析比較;
(2)標桿線第一階段驗證清單。
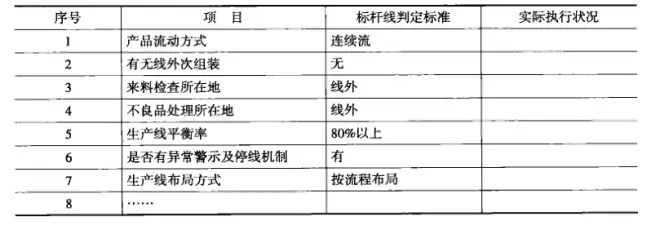
三、以設備為主的流程,主要推動的幾項內(nèi)容
連續(xù)進行一定階段后,再嚴格要求,過渡到能一片一片地進行一個流式生產(chǎn),并對可能的品種多、產(chǎn)品不大、流程相近的一個流生產(chǎn)線改造成Cell模式。以設備為主的流程,則重點開始進行設備的管理,通過快速換模等改善,提高設備的整體效率。(天行健精益生產(chǎn))這時的主要推動內(nèi)容如下表所示。
1.按照節(jié)拍生產(chǎn)。對之前的生產(chǎn)節(jié)拍進行評估,時間較短的,考慮是否進行合并,將節(jié)拍時間適當拉長,降低單線產(chǎn)出速度,減少取放時間占總時間的比重。在生產(chǎn)線上進行畫格,由投料人員控制節(jié)奏,每格放一片產(chǎn)品。
2.設備小型化。評估設備每次同時加工的模穴數(shù),設備加工提前期短的,考慮減少模穴數(shù)甚至只有一個,減小設備體積,設備擺放考慮人因工程,盡量減少作業(yè)者操作時移動的范圍和動作幅度。
3.一個流程生產(chǎn)。要求作業(yè)者單片生產(chǎn),每相鄰工站僅設置一個在制品暫存位置,當來料暫存位置空位時,就停止生產(chǎn)以嚴格執(zhí)行一個流方式,站內(nèi)不積料。
4.Cell生產(chǎn)方式的建立。在產(chǎn)品不算復雜、體積重量適當、品種多但批量小的相似流程產(chǎn)品上,開始嘗試建立Cell線,取消傳送帶,進行U型線布置,進行人機分離作業(yè)。人員進行多種能力訓練。
5.換線、換模改善。內(nèi)部外部作業(yè)的分離,提前準備及同步作業(yè),降低內(nèi)部作業(yè)時間,將換模時間降低到單分鐘以內(nèi),換線甚至無縫切換,降低設備的切換無效時間,提高設備的稼動率。
6.線內(nèi)的物料JIT供應。轉生產(chǎn)線領取物料為倉庫發(fā)放物料,根據(jù)物料的消耗速度,進行定時定量補充,將不同需求物料匯集一臺車,定時對生產(chǎn)線補充。(天行健精益生產(chǎn))各工站原物料設置最低最高水位進行管理,放置物料過多或過少。
7.標準化作業(yè)。按照人機分離圖作業(yè)時間指示,操作安全規(guī)格,操作質量控制點管理規(guī)則,工站布置圖進行有條不紊的生產(chǎn),并且定時檢查生產(chǎn)的進度。
8.此階段的標桿線驗證內(nèi)容。
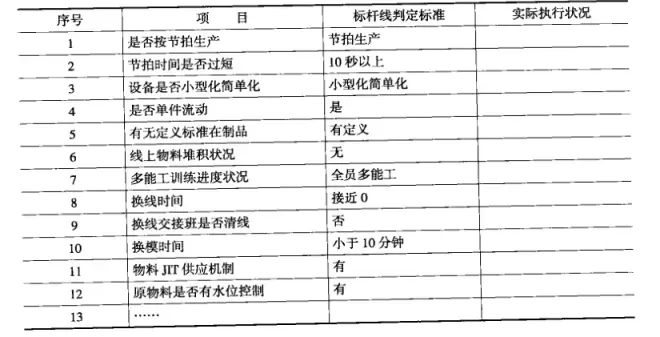
四、工序間的改善整合
工序內(nèi)部改善基本完畢,現(xiàn)在開始要進行工序間的配合改善了,這包含生產(chǎn)排配的配合、倉庫的管理及物料供應。
精益生產(chǎn)總體的思想是為了符合現(xiàn)代社會,產(chǎn)品批量較小、品種繁多的生產(chǎn)模式。在如今“山寨”橫行的年代,多數(shù)產(chǎn)品、多數(shù)中小廠商確實是這種生產(chǎn)模式,市場迫使它們不得不頻繁地換線,不得不開立更小的生產(chǎn)工單,不得不進行簡單的一個工(例如Cell)式樣的生產(chǎn),不得不使用通用小型的設備……但一些大廠,或者生產(chǎn)的產(chǎn)品是普通耐用消費品,往往批量很大,如何引導這類公司工廠進行轉型,往往至關重要,是從中樞機構----生產(chǎn)計劃制訂和管理部門先入手,引導他們有意識地、逐步地增加內(nèi)部生產(chǎn)工單的種類,減少每個工單生產(chǎn)的數(shù)量,以源頭逼迫式的方式使得各流程單位不得不按照新方向、新思維,尋找各自的新方法來應對新問題。
例如,某廠生產(chǎn)一國際品牌的產(chǎn)品,批量都很大,主管意識到精益生產(chǎn)的好處,希望進行局部的改善,尤其突出進行快速換模的改善,借以減少換模造成的無效工時損失。改善團隊經(jīng)過精心研究和設計,可以從2小時減少到10分鐘,并進行標桿機器實驗,效果良好。但推廣過程中,卻遇到了難題,實際統(tǒng)計得到的換模時間總是停留在40分鐘上下。(天行健精益生產(chǎn))為什么呢?通過分析發(fā)現(xiàn),有兩方面的原因。一是快速換模雖然進行了許多的改善,技術的改進不會走回頭路,實際都在按新設備新參數(shù)等進行,但更多的是管理的改善,一些并行作業(yè),內(nèi)部時間向外部時間轉化的執(zhí)行,內(nèi)部時間的嚴格管理及降低等,需要制度的規(guī)范和通過獎懲來嚴格執(zhí)行,這些往往不能堅持。二是其生產(chǎn)排配方式并沒有相應改變,因為批量大,模具幾乎是幾天才換一次,40分鐘的換模分攤到每天,實際損失工時的比例并不太大,也不會對實際產(chǎn)出造成太大影響,所以實際執(zhí)行人員難以體會為何需要這么嚴格地執(zhí)行改進,有所降低就好了,從而導致執(zhí)行不徹底,勉強降低到40分鐘即被他們認為已經(jīng)不錯了而躑躅不前。
倉庫的管理也是一個重要環(huán)節(jié)。倉庫一般需要人員工作負荷管理板、出貨進度管理板、物料在庫狀況、倉庫布置圖、物料儲存水位狀況等信息。通過降低批量和生產(chǎn)提前期的有效控制,各工序間的物料數(shù)量、暫存?zhèn)}面積可以有效地降低,各倉庫進行有效的觸發(fā)機制,設置合理的最小安全庫存和最大庫存。