導入MES系統(tǒng)后,首先可以解決哪些問題?
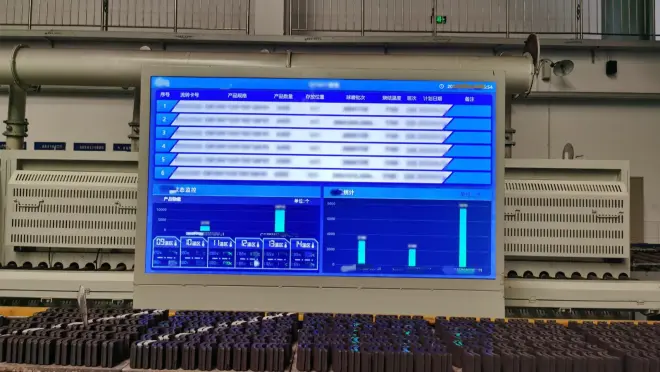
在這里跟大家講述一個真實的案例,在導入MES系統(tǒng)之前,一家日資企業(yè)也按照TPS標準,推進了車間5S、可視化看板、多技能工培養(yǎng)機制、TPM等等精益管理工作,表面上來看也是取得了很好的效果。
但是在MES系統(tǒng)導入并實現(xiàn)與ERP系統(tǒng)數(shù)據(jù)交互以后,在最初的一個月,就發(fā)現(xiàn)之前推出的精益,只是表面光鮮。由于數(shù)據(jù)的精確和信息反饋的及時,很多問題都浮出了表面。
比如,人員技能培訓,覺得人員技能培訓體系做的已經(jīng)很不錯的了,最起碼從月度操作節(jié)拍工時與BOM標準工時比數(shù)據(jù)來看,基本上都在95%~99%之間波動。
但在導入MES系統(tǒng)以后,可以在第二天快速的拉出來個工作崗位員工操作節(jié)拍工時與BOM標準工時精準的對比數(shù)據(jù),經(jīng)過一周的數(shù)據(jù)分析。
老員工的節(jié)拍工時達成率可以達到130%,而入職一個月的不到員工的節(jié)拍工時達成率只在85%左右,入職三個月到半年的員工節(jié)拍工時達成率最高可以提升到95%左右。
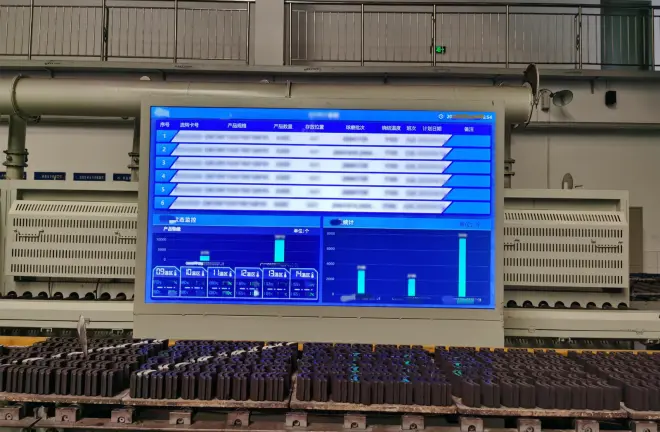
這是因為以前的培訓工作主要集中在產(chǎn)品裝配的標準動作,無論老員工還是新員工,在產(chǎn)品裝配上的標準動作上是沒有太多區(qū)別的,但是在裝配之外。
比如備料的放置和拿取、完成品的放置、品質(zhì)自檢方法等等存在太多的差異,特別是在這次的觀察中,發(fā)現(xiàn)老員工普遍在使用一種簡易、自制的品質(zhì)自檢工裝,通過這個工裝,可以將自檢時間縮短將近20%。
之所以沒有按照改善提案制度進行上報,主要是當時的改善提案制度都需要提案人自己提出、自己驗證、自己聯(lián)系生產(chǎn)部門和品質(zhì)部門進行聯(lián)合審核、再上報申請獎勵。
提案人要做的事情太多、責任太大、周期太長、還需要自己解決跨部門驗證的問題,作為普通作業(yè)人員根本沒有時間和精力做這些事情,所以還不如直接由班組長確認沒有質(zhì)量風險后,就可以悶聲大發(fā)財了。
那么
(1)現(xiàn)有的BOM是否正確?
(2)現(xiàn)有的培訓工具是否正確?
(3)現(xiàn)有的改善提案制度是否正確?
除了這個問題以外,還有很多設備維修及時性、物料領料退料管控、品質(zhì)不良判定流程等等問題也被暴露出來。
在沒有MES系統(tǒng)的時候,手動輸入時間太長,往往只能得到一個大概的、不及時的平均數(shù)據(jù)、比例數(shù)據(jù)。到了月初匯報的時候,很多問題就被平均或比例掉了。
有了MES系統(tǒng),很多精準到工位和個人的數(shù)據(jù)會很快的呈現(xiàn)出來,以這些準確的數(shù)據(jù)為導向,重新界定目前的標準、流程和制度,再建立各個項目組進一步推動精益改善和優(yōu)化,更加的精準、有效,更能淬煉和選拔具有精益思維的管理人員。有了這批具有精益思維的管理人員,加上MES系統(tǒng),將會加速車間機械工裝化、少人化、自動化、數(shù)字化進程。
問題是管理人員最好的磨刀石,用MES系統(tǒng)來準確、快速的呈現(xiàn)問題,再用這些問題不斷打磨自己的管理團隊,再用自己的管理團隊不斷提升MES系統(tǒng)數(shù)據(jù)顆粒度,再用更細的數(shù)據(jù)顆粒度呈現(xiàn)更細節(jié)的問題。
如果您的企業(yè)在生產(chǎn)管理上也存在管理不透明、生產(chǎn)效率差、紙質(zhì)文件多等問題,可以上慧都網(wǎng)咨詢客服或直接撥打主頁電話,我們將安排專業(yè)數(shù)字化專家為您介紹mes解決方案,并發(fā)送相關案例資料!