魯西化工事故反思:以先進工藝提升本質安全
5月1日上午,中化集團魯西化工雙氧水生產區(qū)發(fā)生爆炸火災事故。根據5月3日聊城高新區(qū)管委會的通報,事故造成9人死亡、1人受傷,1人失聯(lián)。
另據應急管理部危化監(jiān)管一司事故警示,事故原因初步分析為,雙氧水裝置工作液配置釜回收工作液時,吸入大量70%濃度雙氧水,釜內可能存在的雜質造成雙氧水劇烈分解,引發(fā)配置釜超壓爆炸。
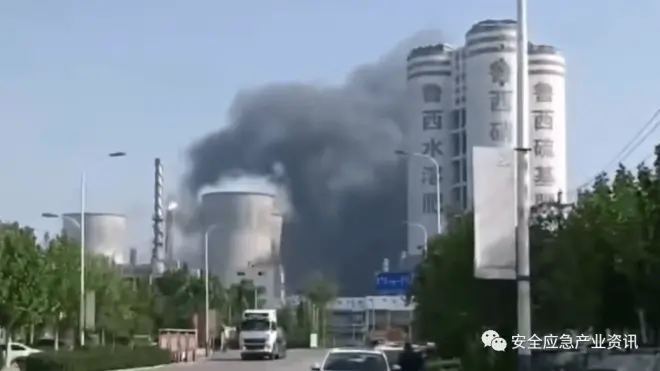
在雙氧水生產過程中,過氧化氫的分解爆炸是最大的生產安全風險。一方面,這是由過氧化氫本身極易分解爆炸的特性所決定的。另一方面,也和我國目前所采用的主流生產工藝有關。
目前,國內生產雙氧水主要采用蒽醌法酸堿混合生產工藝。在這種生產工藝中,工作液是循環(huán)的,而工作液每循環(huán)一次,就要經歷一個由堿性體系到酸性體系的轉變。
其中,氫化過程是在堿性體系的氫化塔中進行,而氫化液進入氧化塔前必須加磷酸中和至酸性,而在氧化塔中經過氧化反應產生過氧化氫后,后續(xù)的體系又必須處于酸性環(huán)境,包括過氧化過程也必須要在酸性環(huán)境下。同時還要求,整個生產過程必須是在不含金屬離子等雜質的環(huán)境下進行。
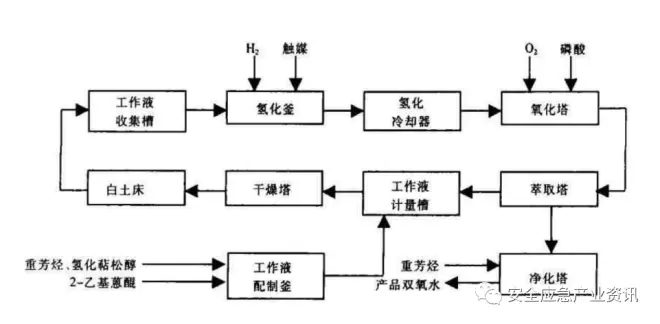
由于工作液是循環(huán)使用,這種酸、堿交替的變化,一方面對雙氧水的安全生產提出了極高的要求,另一方面也提升了整個生產工藝的復雜程度,造成工藝設備總量增多,裝置建設固定資產投資增加,以及日常運行成本的增加。
而全酸性工藝可以避免酸、堿交替帶來的串料可能,從而大大降低生產安全風險。
不過,由于國外對雙氧水生產技術的嚴格控制,尋求具有自主知識產權的生產工藝與設備突破勢在必行。得益于科研院所與企業(yè)的積極探索,我國雙氧水全酸性生產工藝近兩年也到了一定的發(fā)展。以湖南化工設計院的全酸性雙氧水生產工藝為例,除了工藝上高氫效、高產品品質以外,這項工藝還可以通過工作液少量體外自動堿洗方式有效避免裝置串堿;同時避免氧化鋁粉末污染觸媒,提高觸媒使用周期,形成了工藝裝置本質安全上的獨特領先優(yōu)勢,因此獲得中國石油與勘察設計協(xié)會授予“新工藝—全酸性工作液條件下雙氧水制備工程設計”專有技術。湖南化工設計院目前已落成29套雙氧水裝置工程設計。
總體而言,以全酸性生產工藝替代傳統(tǒng)酸堿工藝,是雙氧水行業(yè)發(fā)展的趨勢。也只有通過生產工藝的發(fā)展與進步,才能幫助雙氧水生產行業(yè)真正實現本質安全。(撰稿/洪楊)