中小企業(yè)原來可以做到精益化管理|張馳咨詢
中小企業(yè)原來可以做到精益化管理|張馳咨詢??
精益化管理JITTPMIE生老板叫住了我,指著產(chǎn)線上一個精益生產(chǎn)作業(yè)員,說,你看看,他這樣作業(yè)有什么問題?我順著他的手望去,那個員工似乎在將絕緣粒套進晶體的螺絲孔里面。我一看就驚呆了,原來那個作業(yè)員正在用一支圓珠筆將絕緣粒套進晶??
精益生產(chǎn)精益化管理JITTPMIE生老板叫住了我,指著產(chǎn)線上一個精益生產(chǎn)作業(yè)員,說,你看看,他這樣作業(yè)有什么問題?我順著他的手望去,那個員工似乎在將絕緣粒套進晶體的螺絲孔里面。我一看就驚呆了,原來那個作業(yè)員正在用一支圓珠筆將絕緣粒套進晶體的螺絲孔里面,要知道,這條生產(chǎn)線是無鉛線??!圓珠筆芯是含有鉛的!??
我知道,產(chǎn)線員工這樣做不完全是他們的錯,我們有責任。絕緣粒是一個小小的塑料圓環(huán),是為了將螺絲和晶體絕緣的。圓環(huán)的內(nèi)徑剛好和圓珠筆芯的直徑差不多,所以員工下意識的使用了圓珠筆作為作業(yè)的工具。??
后來我找IE做了幾個亞克體零件安裝部位的需要,時而和地面移動平臺緊挨,時而和人身高等齊。時而從空中轉(zhuǎn)到另外一個區(qū)域,充分的利用了空間,節(jié)省了地面面積。完全沒有國內(nèi)企業(yè)全無立體感,空中一片空蕩蕩的景象。??
最開始看到的區(qū)域,是他們的訓練道場,有簡易的組工位和基本的組裝工具,白板上貼滿了員工的訓練成績,所有的新入職工人都需要在這里進行嚴格的培訓,直到達到工廠所需要的操作技能和操作時間為止。豐田JIT非常注重員工的培訓和鼓勵員工自動自發(fā)的進行改善。平均每人每月都至少有一件改善案,實施后的改善獎勵高者上千,但如果僅僅只是一個提議,沒有實施,也積極鼓勵,以10元進行表示。??
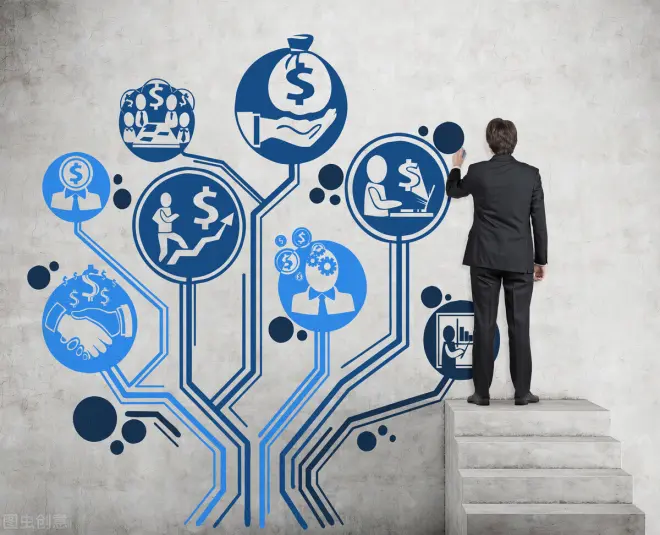
豐田的生產(chǎn)完全采用混流式精益生產(chǎn)方式,雅力士、凱美瑞等不同車型完全共線裝配TPM,剛才還是輛紅色的雅力士,接下來組裝的,就是一臺黑色的凱美瑞了。這種生產(chǎn)方式對員工技能要求比較高,尤其對物料的精密配送,時間的無縫銜接要求更為精細化管理。??
廣汽豐田員工8000余人,其中間接人力1300人,直接人力近7000人。5.3的直間比,似乎不是一個很好看的,數(shù)字,但也正是有了這些算龐大的間則是通過空中鏈軌方式進行轉(zhuǎn)送到對應的工站。大零件按照定量,小零件按照定時的方式進行備貨。為了防止可能的異常,同時也盡量減少在制品的庫存,SPS區(qū)域僅儲備了30分鐘的備品。??
當然,混流生產(chǎn)的前提,也需要穩(wěn)定的生產(chǎn)效率提升計劃,豐田公司生產(chǎn)多少,都是提前一個月進行下單確定。不會隨意更改計劃。為了保證精益供應鏈盡量小的庫存,豐田僅保留了2小時的配送量。??
操作現(xiàn)場生產(chǎn)效率提升做得非常好,是他們的操作平臺,一臺車由吊裝平臺吊著,和工人操作所站立的地面移動平臺同步,工人站在地面移動平臺上操作,和車輛同步移動,每完成一車輛的組裝,就推動零件及工具小推車,轉(zhuǎn)回到下一個車輛。所以看起來工人隨著車輛移動到下一個工位,完成了,他又推車回到他原來的為止,然后繼續(xù)隨車安裝,周而復始。??
每輛車左右兩邊各有一個工人,并配備隨車工具車。一位負責安裝零件,一位負責緊固。負責緊固的工人在安裝不同車型時,使用不同的啟動緊固工具,緊固工具連接有扭力和計數(shù)傳感器,當少打一顆螺絲,或者扭力不夠時,工具車上的燈號就亮起,提示有問題——一種很實用的防呆技術!??
車間不時有吊裝汽車玻璃、吊裝座椅等重物安裝,但都是使用吸盤、磁力吊及其他的專用吊裝工具進行吊裝,方便快捷,也節(jié)省體力。豐田有規(guī)定,超過12KG的零件,都需要借助機械來進行。對于需要在車底安裝的零件的區(qū)域,吊裝平臺會高過人頭,或者在車底挖一專門下沉平臺,讓人站立就可操作,現(xiàn)場絕對看不到任何體力活或者鉆到車底、身體變形才能安裝的現(xiàn)象。豐田現(xiàn)場對人因的考慮可見一斑。??
豐田JIT獨特的異常處理機制,體現(xiàn)在其andon系統(tǒng)上,現(xiàn)場任何工位的員工,只要發(fā)生問題,立即拉動一根水平懸掛的拉繩,就會在班組長所在區(qū)域的燈號顯示屏上紅燈閃爍,班組長迅速趕赴現(xiàn)場,停線立即進行問題處理。這在一般的企業(yè)里面絕對做不到,一般都認為,都停下來的損失該多大啊,沒問題的工站可以繼續(xù)做啊,這樣不是可以減小損失嗎?殊不知,第一,這樣會產(chǎn)生產(chǎn)品堆積,在制品增加。??
第二,不停線,班組長、工程人員(IE部門)就不會重視,處理的速度,處理的質(zhì)量就會大打折扣,從而造成可能相同問題的第二、第三次停線。豐田這種做法,即是典型的短痛換取根除長痛。第一次停線處理可能很久,但是第二次,第三次,后續(xù)的停線自然越來越少,越來越短。??
小小拉線,更體現(xiàn)在現(xiàn)場的記錄上。在測試線上。操作人員用傳統(tǒng)的紙筆記錄,每檢驗完成一到工序,工人就拉動標有測試名稱的對應拉環(huán),傳感到控制器終端進行系統(tǒng)自動記錄。縮短了時間,且減少了可能的筆誤。??
關注自身特有的精益生產(chǎn)方式,關注對人的尊重,豐田同時也非常的關注安全。在隨后稍微開闊的區(qū)域,都有安全最優(yōu)先的標語,提示安全第一的作業(yè)環(huán)境。??
廣汽豐田沒有專門的精益生產(chǎn)推進組織,不過有近60人的龐大的人才培訓中心,其特有的精益生產(chǎn)方式不是通過專人進行專案改善,而是通過教育,通過提案,灌輸?shù)矫總€人的腦子中,執(zhí)行到每個崗位上,真正實現(xiàn)全員精益的方式,這點值得許多通過專門的精益管理機構(gòu)來專業(yè)推動精益生產(chǎn)的公司參考。??
參觀只有短短的一個小時的時間,但很有震撼力。常有人說,臨去豐田前非常激動——盼望著早點領略到超一流企業(yè)的模樣;看到豐田TPM的現(xiàn)場,又非常的感動——企業(yè)原來可以做到這么精益管理;但是回到原來的崗位上,一種激動的固有思潮又襲上心頭——現(xiàn)實總有這樣那樣的障礙。??
對于我們來說,更多的需要有持續(xù)改善、精益求精的決心,精益生產(chǎn)的方法,同心協(xié)力,立志追求卓越,這樣才能讓自己的企業(yè)立足于世界強者之林。??
張馳咨詢提供精益改善周,培訓+項目輔導。
精益管理咨詢項目如下:VSM培訓、現(xiàn)場改善、精益布局與生產(chǎn)線設計、單元線生產(chǎn)、標準作業(yè)、TPM、SMED(快速換模)、精益?zhèn)}庫、內(nèi)部物流設計..