如何利用“精益管理培訓(xùn)”鏟除浙江企業(yè)管理弊?。?/h1>
如何利用“精益管理培訓(xùn)”鏟除浙江企業(yè)管理弊?????
精益管理培訓(xùn)”源于“精益生產(chǎn)”,其核心都在于最大限度地降低消費??逻_首席行政長官白嘉理表示,柯達推行KOS初見成效,企業(yè)浪費明顯減少。在實施KOS(KodakOperationSystem,即柯達運作系統(tǒng))之前,柯達的馬來西亞分公司開設(shè)一家新的柯達沖印店需要7個月;而在實施KOS之后,這個時間縮短為60天,而且成本也大幅降低。??
目標:消除企業(yè)7種浪費??
柯達運作系統(tǒng)的運作思路源自“豐田生產(chǎn)系統(tǒng)”的“精益生產(chǎn)”思想,即使用最少的資源(人力,原材料,設(shè)備)生產(chǎn)出顧客需要的產(chǎn)品,或提供給客戶滿意的服務(wù)。從另一角度而言,就是通過管理手段杜絕各種浪費??逻_認為在企業(yè)內(nèi)部存在著7種浪費,而KOS的目的,就是盡力消除這7種浪費。這7種浪費分別是過度生產(chǎn),殘次品,不必要的庫存量,不適當?shù)倪^程,過多的運輸,等待和不必要的動作,他們消耗了資源但卻沒有生產(chǎn)價值。KOS提倡的是外部導(dǎo)向。簡單說,這套系統(tǒng)就是客戶什么時候需要產(chǎn)品,柯達就什么時候提供;客戶需要多少,柯達就提供多少。外部導(dǎo)向使柯達的每個投入都是有目的,有價值的,這樣既避免了浪費,又提高了客戶的滿意度。??
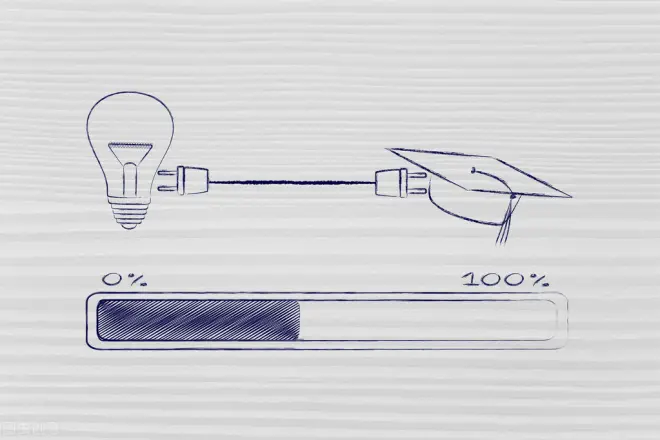
思路:對規(guī)模經(jīng)濟的“反叛”??
任何一種新觀念與實踐結(jié)合都會遇到或多或少的阻力,KOS系統(tǒng)也不例外。柯達剛開始實施KOS的時候,曾經(jīng)面臨巨大的挑戰(zhàn),以前柯達工廠生產(chǎn)膠卷,不管客戶需要的量是多少,每開一次鍋爐就要連續(xù)生產(chǎn)一個星期甚至一個月。而在KOS系統(tǒng)實施后,每開一次鍋爐通常只生產(chǎn)一天。從以往的觀念來看,多開鍋爐肯定多浪費,但在KOS系統(tǒng)所追求的“精益生產(chǎn)”理年中,大規(guī)模的生產(chǎn)需要存儲空間,需要增加管理庫存的人手,而且時間稍長膠卷就會變質(zhì),設(shè)備,場地,人手的投入都遠遠高于使用精益方式的投入。雖然它在生產(chǎn)領(lǐng)域的單位成本較低,但對整個供應(yīng)鏈來說,公司付出的成本卻高于規(guī)模經(jīng)濟所節(jié)約的成本,從而造成了浪費。KOS系統(tǒng)的成效逐漸讓員工心服口服。事實證明,從實施KOS后,柯達的浪費在大幅度降低。譬如在去年,柯達關(guān)閉了其在海外的兩個工廠,大量的生產(chǎn)任務(wù)轉(zhuǎn)移到柯達在廈門的海滄廠。海滄廠由于采用了KOS,在設(shè)有增加生產(chǎn)面積的前提下,結(jié)果完成了相當于以前自身產(chǎn)能1.5倍的工作量。??
執(zhí)行:自下而上,邊做邊學(xué)??
KOS的很多觀念都反傳統(tǒng),這就是意味著在執(zhí)行上,要從管理層開始轉(zhuǎn)變思想并加以推廣。在柯達高層每年都要參加的“全球領(lǐng)導(dǎo)力論壇”,分享,探討全球范圍內(nèi)KOS案例便是一項重要議題,通過這種方式,KOS的思想被灌輸給高層并逐步傳達下去。而與此同時,針對每個具體項目的改善活動則是從下而上進行。KOS系統(tǒng)中有一個非常重要的環(huán)節(jié)叫做“改善”,其基本形式是在為期一周的workshop中,將第一線的員工全部召集起來群策群力,發(fā)現(xiàn)問題,了解問題存在的原因,并最終找到消滅缺陷的辦法。??
與一般生產(chǎn)管理系統(tǒng)不同的是,KOS并不特別注重培訓(xùn),柯達推崇的是邊學(xué)邊做,邊做邊學(xué)。很多好的經(jīng)驗并不是管理層強行推行下去的,而是通過實踐操作者反饋到管理層中在進行推廣的,其中管理層扮演的顯然不是一個命令者的角色。通過KOS的實施,柯達對生產(chǎn)一線員工的信任和授權(quán)也有所提高。因為這種操作方式認為,最了解生產(chǎn)的是第一線的參與者和操作者,一線員工掌握著第一手的資料,因而具有很多創(chuàng)造性的想法,這也與那種認為工人的工作就是執(zhí)行,沒有權(quán)利對生產(chǎn)流程提出意見的傳統(tǒng)觀念劃清了界限。
張馳咨詢提供精益改善周,培訓(xùn)+項目輔導(dǎo)。
精益管理咨詢項目如下:VSM培訓(xùn)、現(xiàn)場改善、精益布局與生產(chǎn)線設(shè)計、單元線生產(chǎn)、標準作業(yè)、TPM、SMED(快速換模)、精益?zhèn)}庫、內(nèi)部物流設(shè)計..