如何分析Incoenl601熱擴(kuò)孔過(guò)程中的應(yīng)力狀態(tài)?
鎳基高溫合金等金屬材料歡迎咨詢 上海霆鋼金屬集團(tuán)有限公司
應(yīng)力狀態(tài)分析 為了進(jìn)一步分析熱擴(kuò)孔裂紋產(chǎn)生的原因, 利用有限元軟件對(duì)熱擴(kuò)孔過(guò)程進(jìn)行模擬, 分析熱擴(kuò)孔過(guò)程中的應(yīng)力情況。 圖 6 ( a )為按實(shí)際工藝參數(shù)構(gòu)建的有限元熱擴(kuò)孔模型,坯料直徑 準(zhǔn)320mm , 內(nèi)徑為 準(zhǔn)45mm , 然后加熱至 1180℃ 放置擴(kuò)孔筒中,利用 錐形擴(kuò)孔頭由上而下進(jìn)行擴(kuò)孔,擴(kuò)孔系數(shù)為1.3 。圖 6 ( b )為熱擴(kuò)孔過(guò)程中金屬的流動(dòng)情況。由圖可見, 金屬流動(dòng)速度最快的部位為坯料內(nèi) 孔與擴(kuò)口 頭端部接觸的位置, 內(nèi) 表金屬沿垂直于擴(kuò)口 頭界面向下流動(dòng), 外表層 的金屬則與擴(kuò)孔方向相反的上方流動(dòng)。 從金屬流動(dòng)方向來(lái)看, 在擴(kuò)孔過(guò)程中, 內(nèi)表的金屬流動(dòng)最為劇烈, 因此熱擴(kuò)孔過(guò)程中內(nèi)表也是最容易產(chǎn)生裂紋的部位。另外, 在熱擴(kuò)孔過(guò)程中的最大主應(yīng)力情況如圖6 ( c )所示, 管坯內(nèi) 表層的壓應(yīng)力較大, 而外表面的拉應(yīng)力最高。 外表面由于跟擴(kuò)孔筒的內(nèi) 部接觸, 在向上流動(dòng)的過(guò)程中, 會(huì)形成拉應(yīng)力, 如果材料塑性不夠或者選擇工藝不當(dāng), 容易產(chǎn)生垂直于擴(kuò)孔方向的橫向裂紋。
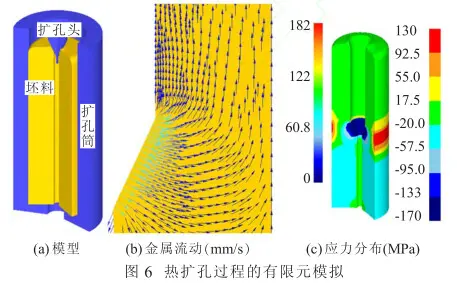
綜合上述對(duì)熱擴(kuò)孔裂紋特征、 Inconel601 合金組織特征、 坯料初始組織及擴(kuò)孔過(guò)程金屬流動(dòng)及應(yīng)力狀態(tài)的分析, 在熱擴(kuò)孔過(guò)程中產(chǎn)生裂紋的主要原因主要有兩方面。首先是原材料的熱塑性, 合金的成分、析出相、晶粒尺寸、夾雜、組織均勻性等均會(huì)影響其熱塑性 。 結(jié)合合金的平衡相圖及組織觀察來(lái)看, Inconel601 合金在熱擴(kuò)孔溫度下( 900~1200℃ )為單一的奧氏體組織, 無(wú)有害相析出, 且原始坯料的夾雜物水平較低, 對(duì)熱塑性影響不大, 化學(xué)成分在合理范圍內(nèi) , 這些均不是熱擴(kuò)孔裂紋形成的主要原因。但是, 原始坯料的組織均勻較差, 混晶嚴(yán)重, 會(huì)導(dǎo)致合金在熱變形過(guò)程中出現(xiàn)變形不協(xié)調(diào)的現(xiàn)象最終降低材料的熱塑性而產(chǎn)生熱裂紋。另一方面, 熱擴(kuò)孔過(guò)程中表層金屬受到的拉應(yīng)力較大, 如果擴(kuò)延系數(shù)過(guò)大或者坯料表層的潤(rùn)滑選擇不當(dāng)亦會(huì)導(dǎo)致熱裂紋的產(chǎn)生。 由于擴(kuò)延系數(shù)過(guò)大或潤(rùn)滑不當(dāng)造成的熱裂紋通常為垂直于擴(kuò)孔方向的橫向裂紋, 而根據(jù)上述對(duì)該合金的裂紋特征來(lái)看, 裂紋首先在表層混晶區(qū)域處形成橫向裂紋, 然后再沿著粗晶和細(xì)晶的界面處擴(kuò)展。因此, 解決 Inconel601 合金的熱擴(kuò)孔裂紋最有效的方式是控制坯料的晶粒尺寸均勻性, 另外當(dāng)坯料存在晶粒不均勻的情況可嘗試降低熱擴(kuò)孔的擴(kuò)延系數(shù)以減少表層的應(yīng)力水平, 進(jìn)而緩解裂紋的產(chǎn)生。
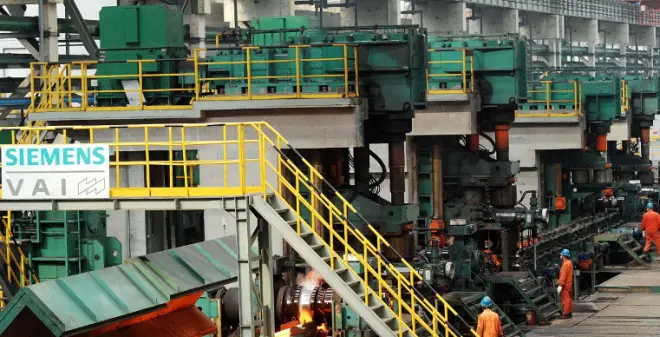
圖 7 ( a )為晶粒均勻分布、平均尺寸為 40μm 的Inconel601 合金坯料經(jīng)過(guò)同樣熱擴(kuò)孔工藝擴(kuò)孔后的表面質(zhì)量, 可以觀察到, 表面質(zhì)量較好, 無(wú)裂紋存在。再者, 對(duì)晶粒尺寸不均勻的坯料, 將擴(kuò)延系數(shù)從 1.3降低到 1.15 , 熱擴(kuò)孔溫度不變, 經(jīng)過(guò)擴(kuò)孔后的表面質(zhì)量如圖 7 ( b )所示。 外表裂紋已經(jīng)得到消除, 但可以觀察到表面相對(duì)晶粒均勻的坯料要粗糙多, 這是由于晶粒粗大且不均勻在熱擴(kuò)孔過(guò)程中變形不協(xié)調(diào)而造成的。 這兩種改進(jìn)方式的結(jié)果也進(jìn)一步證實(shí)以上的分析和推理。
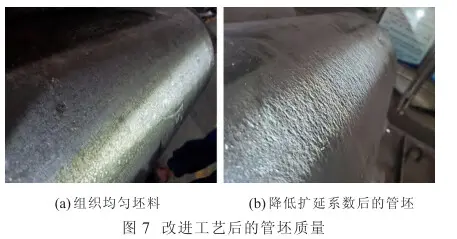
本文針對(duì) Inconel601 合金熱擴(kuò)) 孔裂紋形成的原因, 從裂紋形貌、組織特征以及熱擴(kuò)孔過(guò)程中的金屬流動(dòng)和應(yīng)力狀態(tài)幾方面進(jìn)行了深入分析, 得出以下主要結(jié)論: ( 1 ) 熱擴(kuò)孔裂紋附近為混晶組織, 在粗晶和細(xì)晶的界面處并沿著晶界擴(kuò)展, 裂紋附近無(wú)有害析出相存在, Inconel601 合金在熱擴(kuò)孔的溫度范圍內(nèi) , 為單一的奧氏體組織。 ( 2 ) 在熱擴(kuò)孔過(guò)程中, 金屬流動(dòng)速度最快的部位為坯料內(nèi)孔與擴(kuò)口 頭端部接觸的位置, 內(nèi) 表金屬沿垂直于擴(kuò)口 頭界面向下流動(dòng), 表層金屬則沿與擴(kuò)孔方向相反的上方流動(dòng), 且外表面的拉應(yīng)力較高, 徑向上金屬流動(dòng)及應(yīng)力分布不均勻。 ( 3 ) 初始組織的不均勻性是熱擴(kuò)孔裂紋產(chǎn)生的主要原因, 改善坯料組織均勻性及降低擴(kuò)延比均能避免熱擴(kuò)孔裂紋的產(chǎn)生。