如何減少造粒過程中的粉塵大的問題?
? ?造粒是將乙烯聚合后產(chǎn)生的粉料或熔融樹脂經(jīng)過切粒機(jī)切粒,使粉料或熔融樹脂變成顆粒,便于包裝和輸送。而在切粒過程中必然會(huì)產(chǎn)生碎屑和粉塵,少量的粉塵和碎屑對(duì)工藝和設(shè)備影響不大,但產(chǎn)生大量的粉塵就會(huì)污染環(huán)境,裝置單耗增加,裝置廢水處理量增加等一系列有害因素。因此無論從工藝、設(shè)備還是安全環(huán)保角度考慮,都應(yīng)減少造粒過程中產(chǎn)生的粉塵和碎屑。
一、粉塵和碎屑的產(chǎn)生過程
粉塵和碎屑主要由以下三個(gè)過程產(chǎn)生:
1、造粒過程中由于切刀磨損過度、模板磨損(氣蝕和積屑)、模板加熱不均勻、安裝缺陷(切刀和模板平行度差)和顆粒水溫度低等原因產(chǎn)生的帶尾粒子,這種顆粒通過冷卻水和振動(dòng)篩的作用尾部斷裂分離出絮狀物。
2、顆粒進(jìn)入干燥器和振動(dòng)篩后粒子尚未完全冷卻,顆粒與設(shè)備尖銳的部分碰撞,導(dǎo)致粒子表面拉絲料,后續(xù)的輸送過程中拉絲料斷裂產(chǎn)生的拉絲料。
3、風(fēng)送和摻混過程中粒子與管道之間的摩擦,粒子與粒子之間的摩擦產(chǎn)生的粉塵。
二、影響碎屑產(chǎn)生的因素
1、切刀問題
? ? 切刀的切粒面的平面度、切刀切粒面的粗糙度和切刀的鋒利度都能影響切粒產(chǎn)生的粉塵。切刀平面度較差是由于制造缺陷或磨刀過程中產(chǎn)生,較差的表現(xiàn)是切刀表面有凹凸不平的劃痕,這些劃痕導(dǎo)致切刀面與模板的平行度無法保證,因此會(huì)切出大小不均勻的粒子或尾巴料。切粒面的粗糙度增加,會(huì)增加切刀與熔融樹脂的親和力,切刀刃容易粘結(jié)樹脂,易發(fā)生纏刀、墊刀等問題,從而間接導(dǎo)致切粒效果變差產(chǎn)生更多的尾巴料、小顆粒、粉塵和拉絲料。切刀由于造粒過程中磨損和腐蝕切刀變鈍。
? ? ?如果進(jìn)退刀壓力和切粒機(jī)轉(zhuǎn)速設(shè)置合適,切刀和模板同時(shí)磨損,切刀具有自鋒利功能,但進(jìn)退刀壓力、切粒機(jī)轉(zhuǎn)速設(shè)置不合適,切刀與模板間距過大,僅有物料對(duì)切刀磨損,切刀會(huì)很快變鈍;切刀腐蝕也會(huì)使切刀變鈍。切刀腐蝕主要是由物料本身腐蝕物質(zhì)或添加劑帶入的腐蝕物質(zhì)在循環(huán)的顆粒水集聚造成切刀腐蝕。切刀變鈍后切出的粒子會(huì)產(chǎn)生碎片、尾巴料和長條料等缺陷。
2、模板氣蝕和積屑
? ?氣蝕是由于切粒刀在高速旋轉(zhuǎn)的刀盤帶動(dòng)下,切粒刀前刀面推動(dòng)冷卻水,造成模板造粒帶內(nèi)環(huán)和刀盤端面的空間壓力低于切粒水室內(nèi)顆粒水壓力。部分顆粒水在模板高溫作用下瞬間發(fā)生汽化向造粒帶和刀盤端面方向瞬間沖擊,極易造成模板造粒帶的汽蝕和物料顆粒的粘結(jié),降低模板的使用壽命和產(chǎn)品合格率,甚至發(fā)生墊刀、纏刀乃至斷刀的事故。積屑瘤是切刀和??自趯?duì)塑料進(jìn)行剪切時(shí),使塑料某處貼近動(dòng)刀前刀面和造粒帶出料孔處,發(fā)生劇烈摩擦變形,產(chǎn)生的高溫將局部塑料融化,其融化的塑料以薄膜狀態(tài)粘結(jié)到切刀、模孔表面,這一狀態(tài)的連續(xù)發(fā)生,形成瘤狀堆積物——積屑瘤。當(dāng)積屑瘤增長到一定高度時(shí)即被動(dòng)刀撞掉,脫落的積屑瘤會(huì)將切粒刀和模板造粒帶出料孔自身的材料粘下一部分,久而久之模板發(fā)生磨損。
3、模板加熱不均勻
? ?擠壓機(jī)模板主要采用電加熱、熱油加熱和蒸汽加熱。大型機(jī)組中應(yīng)用較多的是熱油和蒸汽加熱。熱油加熱的效果要比蒸汽加熱效果好,但熱油加熱建設(shè)投資高,為減低建設(shè)成本許多廠家采用蒸汽加熱。模板溫度高的地方物料流動(dòng)速度快,所切物料顆粒直徑大或較長。溫度低的地方物料流動(dòng)速度慢,所切物料直徑小或成片狀,嚴(yán)重時(shí),甚至不出料等缺陷。
4、顆粒水溫度
? ? 根據(jù)物料熔融指數(shù)和密度,顆粒水溫度一般控制 40-70℃。熔融指數(shù)高的物料顆粒水溫度控制低,熔融指數(shù)低的物料控制的顆粒水溫度高。如果顆粒水溫度溫度控制過低,會(huì)使流出模孔的物料迅速冷卻,切刀切削部分固化的樹脂,固化的樹脂會(huì)從??讕С鲆徊糠治锪?,是粒子產(chǎn)生細(xì)尾巴。如果顆粒水溫度過高,粒子定形時(shí)間變長,粒子移動(dòng)過程中,粒子會(huì)變形,產(chǎn)生粗尾巴粒子??刂坪线m的顆粒水溫度會(huì)減少粉塵和碎屑。
三、減少碎屑產(chǎn)生的措施
1、調(diào)整合適的進(jìn)、退刀壓力和切粒機(jī)轉(zhuǎn)速切粒狀態(tài)下切刀所受到如下力,并達(dá)到平衡狀態(tài):顆粒水給切刀旋轉(zhuǎn)方向相反的方向的阻力和推進(jìn)切刀向模板方向的力;物料對(duì)給切刀旋轉(zhuǎn)方向相反的方向的阻力和推向刀盤方向的力;刀盤對(duì)切刀向模板方向的力(進(jìn)退刀壓差);模板造粒帶對(duì)切刀向刀盤方向的作用反力;切粒機(jī)電機(jī)給切刀旋轉(zhuǎn)方向的扭矩;顆粒水給切刀旋轉(zhuǎn)方向相反的方向的阻力。物料對(duì)給切刀旋轉(zhuǎn)方向相反的方向的阻力和切粒機(jī)電機(jī)給切刀旋轉(zhuǎn)方向的扭矩平衡。
? 進(jìn)退刀壓差和推進(jìn)切刀向模板方向的力這兩個(gè)力決定模板對(duì)切刀的反作用力,如果作用力過大切刀磨損嚴(yán)重。如果作用力過小稍有負(fù)荷波動(dòng)就會(huì)造成切刀與模板之間距離改變。推進(jìn)切刀向模板方向的力由顆粒水流量和切粒機(jī)轉(zhuǎn)速確定,切粒機(jī)轉(zhuǎn)速根據(jù)粒子長度調(diào)節(jié)至一個(gè)固定轉(zhuǎn)速。造粒過程中能調(diào)節(jié)的只有進(jìn)退刀壓差。實(shí)際操作可以給進(jìn)退刀壓差一個(gè)偏大的值,根據(jù)現(xiàn)場千分表檢測(cè)情況每天減小壓差 0.01MPa(G),直至千分表檢測(cè)千分表磨損量小于0.02mm 每天。該進(jìn)退刀壓差值作為該負(fù)荷下進(jìn)退刀壓差的經(jīng)驗(yàn)值。造粒過程中進(jìn)退刀壓差盡量往經(jīng)驗(yàn)值靠近可以有效減少粉塵量并且盡可能減少切刀磨損。
2、調(diào)整模板加熱
造粒過程中模板溫度保持在 180-220℃之間。除模板加熱介質(zhì)對(duì)模板溫度有影響外,顆粒水流量也會(huì)影響模板溫度。顆粒水流量大則帶走模板的熱量越多,模板溫度就低。正常生產(chǎn)應(yīng)保持顆粒水流量穩(wěn)定。模板加熱介質(zhì)溫度、壓力穩(wěn)定,盡量減少模板加熱不均勻,減少造粒過程中粉料產(chǎn)生。
3、校正安裝偏差
國內(nèi)大型造粒機(jī)都采用撓性刀盤,撓性刀盤雖然解決了設(shè)備沉降不一、調(diào)整困難的問題,但如果切刀和模板安裝偏差過大,將會(huì)導(dǎo)致,切刀與模板間隙不均勻,容易引發(fā)碎屑,粒子大小不一等問題。每次檢修完畢后應(yīng)該校準(zhǔn)安裝偏差,如果偏差超出廠家規(guī)定的范圍,應(yīng)予以校正。即使偏差在廠家規(guī)定的范圍內(nèi),安裝完切刀和模板后應(yīng)至少磨刀 30 分鐘,磨刀時(shí)的進(jìn)退刀壓差調(diào)至正常造粒進(jìn)退刀壓差的80%。磨刀結(jié)束后,應(yīng)檢查每把切刀均有磨過的痕跡,否則重新磨刀。
4、調(diào)整顆粒水溫度至合適
有粉塵產(chǎn)生的原因可知,顆粒水溫度過低會(huì)造成粉塵增加,所以生產(chǎn)中應(yīng)嚴(yán)格控制顆粒水溫度。根據(jù)生產(chǎn)經(jīng)驗(yàn)得出各個(gè)牌號(hào)的最佳顆粒水溫度后,應(yīng)保證生產(chǎn)時(shí)該溫度波動(dòng)不能超過 5℃。發(fā)現(xiàn)由于顆粒水換熱器堵塞等原因?qū)е骂w粒水溫度無法控制時(shí),應(yīng)立刻切至備用換熱器。
5 結(jié)語
粉塵和碎屑產(chǎn)生的原因十分復(fù)雜,不可能完全消除碎屑和粉塵。但減少粉塵和碎屑的量對(duì)裝置經(jīng)濟(jì)效益有十分顯著的影響。實(shí)際操作中,微調(diào)一個(gè)變量,觀察顆粒外形及粉塵和碎屑產(chǎn)量,逐步總結(jié)出最優(yōu)參數(shù)組合。若通過調(diào)整參數(shù)無法控制粉塵和碎屑生產(chǎn)量至合適,則更換切刀或模板。
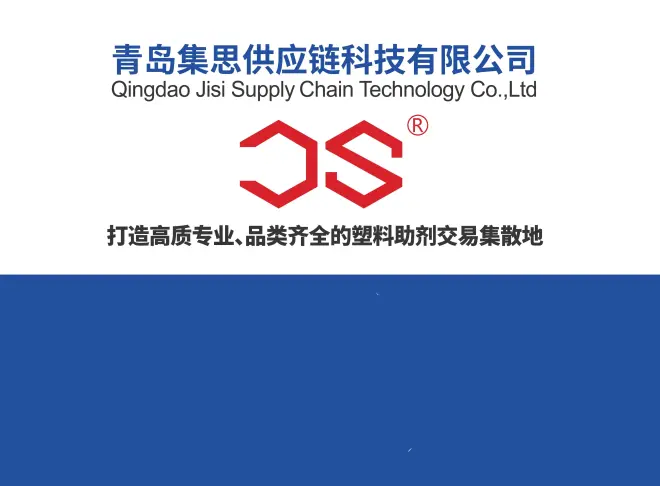