長春東獅DXY選擇性催化氧化法轉(zhuǎn)化H2S新技術(shù)
DXY選擇性催化氧化法轉(zhuǎn)化H2S新技術(shù)
1、技術(shù)背景
在煤化工領(lǐng)域,低溫甲醇洗工藝具有舉足輕重的地位。無論是煤的直接液化、間接液化,還是煤氣化制取化工產(chǎn)品的工藝裝置中,大多要有氣體凈化工藝,而低溫甲醇洗工藝無疑是目前最具競爭實力、成熟的氣體凈化技術(shù),已被廣泛應(yīng)用于國內(nèi)外合成氨、合成甲醇和其他羰基合成、城市煤氣、工業(yè)制氫和天然氣脫硫等氣體凈化裝置中。尤其是對煤(水煤漿)或渣(重)油為原料制取合成氣的凈化,采用此方法則效果更佳。在國內(nèi),以煤、渣油為原料建成的大型合成氨、合成甲醇裝置中也大都采用這一技術(shù)。低溫甲醇洗工藝投資較高,但與其它脫硫、脫碳工藝相比具有電耗低、蒸汽消耗低,溶劑價格便宜,操作費用低等優(yōu)點。特別是脫硫的凈化度高,對甲醇及合成氨生產(chǎn)十分有利。
低溫甲醇洗等濕式非氧化法工藝中,硫化氫沒有發(fā)生化學(xué)轉(zhuǎn)化,而是被富集到酸性氣體中,然后采用克勞斯工藝對酸性氣體中的硫化氫進(jìn)行處理。但克勞斯脫硫流程是一種針對高硫含量酸性氣的催化氧化流程,投資高,流程長,對硫含量要求在10%以上,不適合低入口硫含量、高凈化度酸性氣體脫硫。對于有高凈化度要求的酸性氣體脫硫,需要多級克勞斯才能完成,流程長,投資高,在H2S>12%的硫含量時氣體的腐蝕性增強,毒性大,且易燃易爆,低溫甲醇洗裝置中H2S需要反復(fù)吸收解析濃縮,最終勉強達(dá)到12%以上,勉強適合用克勞斯硫磺回收技術(shù),且克勞斯硫磺回收脫硫后的尾氣中H2S或SO2很難達(dá)到國家排放標(biāo)準(zhǔn),常見的含量300~3000ppm,經(jīng)常需要進(jìn)一步處理,克勞斯硫磺回收技術(shù)顯然不是最理想的酸性氣脫硫技術(shù)。
???
長春東獅科技(集團(tuán))有限責(zé)任公司自2012年就開始投入大量人力物力,與相關(guān)院校和研究機構(gòu)合作,研究開發(fā)出了一種新的處理酸性氣體中硫化氫的DXY東獅脫硫新技術(shù)工藝。目前,該工藝的核心技術(shù)——專用催化劑已研制成功,通過了中試和工廠化實驗,并已建成了一套工業(yè)化實驗裝置,經(jīng)過長時間的連續(xù)運行,裝置運行平穩(wěn),各項指標(biāo)都達(dá)到或超過了設(shè)計指標(biāo),標(biāo)志著DXY工藝已具備了全面推廣的條件。
?
2、技術(shù)特點
DXY脫除酸性氣中硫化氫工藝具有公用工程消耗低,凈化度高,催化劑適應(yīng)性廣,設(shè)備投資低,工藝簡單等特點。與克勞斯法相比,本裝置適應(yīng)的H2S含量最低0.3%最高10%,且H2S轉(zhuǎn)化一步即可完成。因反應(yīng)是放熱反應(yīng),H2S含量0.5%以上即可不需要外來熱量,本裝置能耗低,沒有蒸汽消耗,電耗、水耗根據(jù)副產(chǎn)蒸汽需要產(chǎn)生。H2S含量1.0%以上,即可以副產(chǎn)蒸汽。H2S含量3.0%以上 轉(zhuǎn)化爐即可產(chǎn)直接產(chǎn)蒸汽。催化劑一次裝填,可使用3年以上。用在低溫甲醇洗酸性氣脫硫,噸氨催化劑消耗成本為0.1-2元(與原料氣含硫有關(guān))。與傳統(tǒng)克勞斯脫硫相比投資可節(jié)省50%,運行費用可節(jié)省50%。30萬噸/年合成氨NHD或低溫甲醇洗配套的酸性氣,DXY脫硫直接工程投資1500萬左右,低于克勞斯法脫硫投資3000萬。流動資金、技術(shù)費等其他費用根據(jù)投資規(guī)模的運作階段另計。
?
3、技術(shù)優(yōu)勢
我們開發(fā)的DXY脫硫生產(chǎn)項目,工藝先進(jìn),技術(shù)世界領(lǐng)先,為國家提倡的,符合清潔生產(chǎn)的工藝流程。本工藝優(yōu)勢有:
1、凈化度高,不同含硫量的氣體凈化度可達(dá)10ppm以下。
2、催化劑選擇性好,不與H2、CO等還原性氣體催化反應(yīng),有很好的選擇性,能優(yōu)先轉(zhuǎn)化硫化氫。
3、催化劑適應(yīng)性廣,催化劑比克勞斯催化劑有更好的活性,能適應(yīng)硫化氫含量最小3000ppm,最大100000ppm的氣體脫硫。
4、裝置投資小,操作簡單,因配套設(shè)備數(shù)量少,操作相對克勞斯要簡單。
?
4、工藝簡介
DXY東獅脫硫新技術(shù)脫除酸性氣中硫化氫工藝裝置中核心設(shè)備轉(zhuǎn)化爐為創(chuàng)新型設(shè)備,具有高效,安全,全自動控制的特點,能有效降低運行費用,不同規(guī)模轉(zhuǎn)化爐形式都有不同的創(chuàng)新,是本裝置中的關(guān)鍵設(shè)備。本流程公用工程部分,因規(guī)模的不同,而有較大變化。換熱器的能量回收措施隨能力擴大而有逐步細(xì)化。
1.1預(yù)熱段
酸性氣體首先通過工藝調(diào)整濃度,使其中的H2S濃度降低至1-2%左右,經(jīng)分離器除去液體后,自動控制配比一定的空氣,并用多級換熱加熱到一定的溫度,達(dá)到催化劑所需的活性溫度。
1.2反應(yīng)段
預(yù)熱后的氣體進(jìn)入轉(zhuǎn)化爐,在轉(zhuǎn)化爐中,酸性氣在稍過氧的環(huán)境下硫化氫直接轉(zhuǎn)化成硫磺。反應(yīng)后的氣體通過氣體換熱器和控溫?fù)Q熱器,同時副產(chǎn)0.6MPa(A)和0.3MPa(A)的低壓蒸汽。在轉(zhuǎn)化爐中主要的化學(xué)反應(yīng)是:
COS + H2O→H2S + CO2
2H2S + O2→S + 2H2O
轉(zhuǎn)化爐采用我公司專利設(shè)備——控溫反應(yīng)器。反應(yīng)器中催化劑床層設(shè)置3層,通過等溫?fù)Q熱+DCS冷激控制反應(yīng)溫度,從而得到較高的硫轉(zhuǎn)化率。
反應(yīng)器內(nèi)裝填DXY硫化氫轉(zhuǎn)化催化劑。
1.3硫磺分離段
通過轉(zhuǎn)化爐的氣體,先通過氣體換熱器換熱,再通過控溫?fù)Q熱器嚴(yán)格控制溫度在150℃,氣體135-140℃恒溫進(jìn)入分離器,分離冷凝下來的硫磺,并回收硫磺,尾氣進(jìn)入尾氣處理階段。
1.4尾氣處理段
經(jīng)過硫分離器分離后的尾氣,進(jìn)入過濾吸附塔,過濾并吸附氣體中的硫磺顆粒,然后經(jīng)過換熱回收熱量后達(dá)標(biāo)排放。
1.5硫磺成型段
所有冷凝分離下來的液體硫磺先流入硫回收槽,再流入硫磺鑄模成型。
1.6催化劑
本工藝采用的催化劑
催化劑的物化性質(zhì):化學(xué)組成為粘結(jié)劑助催化劑;物化性質(zhì)外觀為條狀5×(5-15),比表面積大于100m/g,孔容大于等于0.2mL/g,平均壓碎強度大于80N/顆,堆積密度0.95~1.05kg/L磨損率小于1.0%(m/m)。
DXY脫除酸性氣中硫化氫工藝是一種全新的脫除含硫氣體中硫化氫的新工藝:無污染,無能耗,低物耗,低強度等特點,本工藝已經(jīng)十分成熟??芍苯舆x擇使用。我們公司可提供全套的工藝設(shè)計工藝包及核心設(shè)備,DXY催化劑,指導(dǎo)開車及售后服務(wù)等相關(guān)工作。
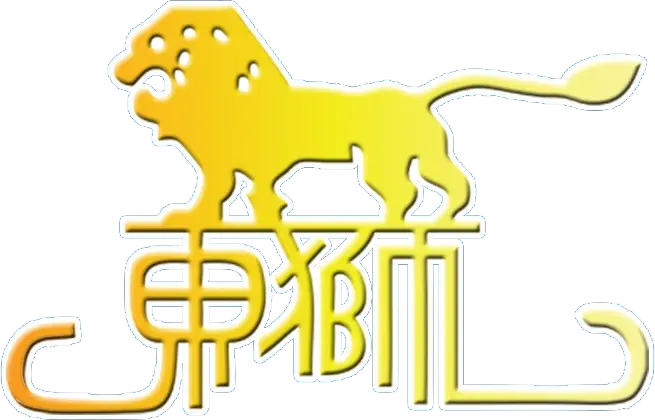
?