準時化生產(chǎn)模式:零庫存,快速應對市場變化
JIT(又稱:準時化生產(chǎn)方式)是豐田創(chuàng)始人豐田喜一郎在20世紀30年代提出的。當時二戰(zhàn)前,豐田成立,還很弱。提出這樣的觀點是非常超前的。后來在50年代初由小野先生逐步完善,70年代初達到成熟。JIT是豐田生產(chǎn)模式的核心,所以是我們經(jīng)??吹截S田推出生產(chǎn)模式的原因,也叫JIT生產(chǎn)體系。
JIT的基本思想是:只在需要的時候,根據(jù)需要的數(shù)量,生產(chǎn)需要的產(chǎn)品,所以也叫準時制生產(chǎn)和準時制生產(chǎn)模式。
JIT的核心是:零庫存,快速應對市場變化。
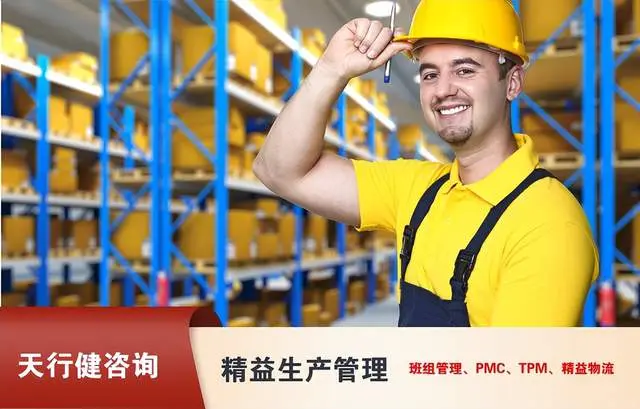
JIT的目標是:徹底消除無效勞動和浪費。具體要做到以下目標:
(1)浪費量最低(零缺陷)。JIT要求消除各種不合理的原因,要求加工過程中的每一道工序都達到最佳水平。
(2)最低庫存(零庫存)。JIT認為庫存是生產(chǎn)制度設(shè)計不合理,生產(chǎn)流程不協(xié)調(diào),生產(chǎn)運營不好的證明。
(3)準備時間最短(零切換)。準備時間的長短與批次選擇有關(guān)。如果準備時間趨于零,準備成本趨于零,就有可能采用極小批量。
(4)生產(chǎn)的提前期最短(零停滯)。該系統(tǒng)提前期短,批量小,適應性強,柔性好。
(5)減少零件搬運,搬運能力低(零搬運)。零件的進給和處理是非增值操作。如果可以減少零件和組件的運輸數(shù)量,減少搬運次數(shù),就可以節(jié)省裝配時間,減少裝配過程中可能出現(xiàn)的問題。
(6)機器損壞率低(零故障)。使用全職裝備管理可以最大限度地降低裝備的傷害,保持裝備的高機動性。
(7)事故減少(零事故)。包括人員事故、設(shè)備事故、安全事故等。
JIT的目標簡稱以上7個零,這7個零最后歸結(jié)為零浪費。
在JIT生產(chǎn)模式下,要用一半的人員和生產(chǎn)的周期,一半的空間和產(chǎn)品研發(fā)時間,一半的投入和少得多的庫存,生產(chǎn)生產(chǎn)出質(zhì)量更高、品種更豐富的產(chǎn)品。
考慮JIT生產(chǎn)模式的方法是把它當成一個理想的生產(chǎn)模式,不斷追求零庫存。零庫存可以無限接近,但永遠達不到。這樣才能不斷降低庫存,改善一些暴露出來的問題。經(jīng)過這樣的反復優(yōu)化,庫存會降到最低,而降低庫存的手段就是減少看板張數(shù)。
精益生產(chǎn)的相關(guān)內(nèi)容:
JIT準時化生產(chǎn)方式:導入準時化生產(chǎn)方式的一般步驟和順序;
JIT準時化生產(chǎn)方式:外部協(xié)作關(guān)系與準時化生產(chǎn)方式;
實施豐田準時化生產(chǎn)方式:全員參加的現(xiàn)場改善活動;
唯品會 JIT模式 應用探討。