特斯拉生產(chǎn)工廠45秒生產(chǎn)一臺車是如何做到的?
北京時間3月2日特斯拉舉辦了2023投資者日,活動同期,第400萬輛特斯拉從得州超級工廠正式下線。根據(jù)規(guī)劃,特斯拉將在2030年達(dá)成2000萬輛年產(chǎn)能目標(biāo),這意味著特斯拉要具備的更強的生產(chǎn)能力。
特斯拉朱曉彤稱:“特斯拉生產(chǎn)工廠,及格線為90%的總體設(shè)備自動化生產(chǎn)效率,以及每45秒生產(chǎn)一輛車?!?/p>
想要實現(xiàn)45秒生產(chǎn)一臺車,除了對技術(shù)需要進(jìn)行再次創(chuàng)新之外,生產(chǎn)方式的改變才是特斯拉未來提高產(chǎn)速的核心。
眾所周知,傳統(tǒng)的汽車制造過程需要把零零碎碎的部件一塊一塊進(jìn)行組裝,整套流程既繁瑣又無法實現(xiàn)高度自動化。而特斯拉現(xiàn)在想要開啟新的“車輛制造方式”,繼續(xù)減少車身零部件數(shù)量,然后通過工人或者機械手對各個部分進(jìn)行同時操作,并實現(xiàn)一體化壓鑄。在新的制造方式中,所有制造完成的零部件都準(zhǔn)備好后,產(chǎn)線才開始進(jìn)行序列組裝和平行組裝,這就好像是在“拼樂高”。在這個過程中,更多人將同時參與裝配工作,整車制造過程中只進(jìn)行一次組裝,生產(chǎn)效率將由此提升30%。
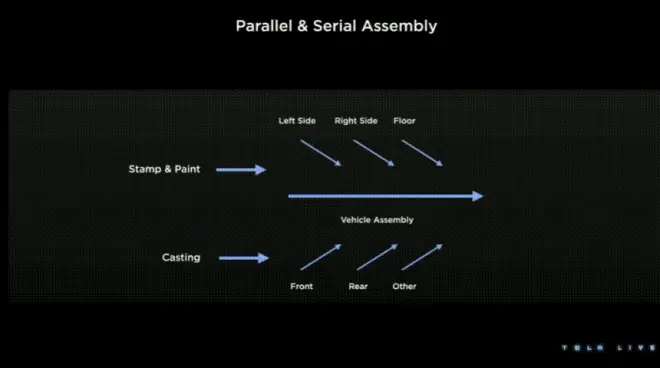
具體來說,特斯拉獨創(chuàng)的一體化壓鑄車身技術(shù),能有效減輕Model Y車身重量,一體式壓鑄后底板總成零件數(shù)量由70個變?yōu)?個,大大簡化了生產(chǎn)制造工藝,并讓車輛性能得以提升。
此外,在特斯拉,整個汽車和工廠是同步實現(xiàn)設(shè)計的,電池專家、化學(xué)專家、機械工程師、自動化工程師、供應(yīng)鏈團隊,程序員等等不同角色在一起工作,共同討論做出決策,從而實現(xiàn)為整輛車提供最優(yōu)的想法和解決方案。
超級工廠也一直是特斯拉引以為傲的產(chǎn)品。目前,特斯拉已在全球建成六座工廠,這也是特斯拉加速生產(chǎn)制造能力的關(guān)鍵所在。
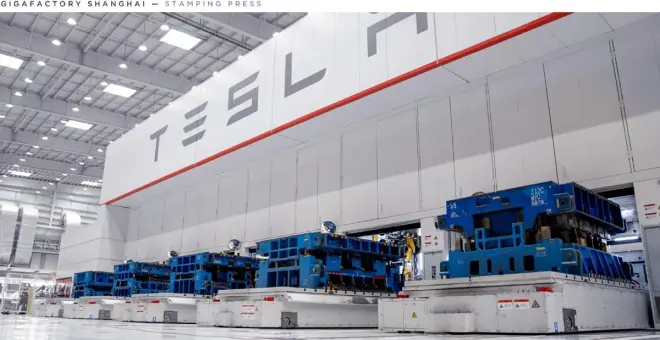
其中,上海超級工廠作為特斯拉的核心工廠,一直以優(yōu)異的成績?yōu)樾袠I(yè)所熟知。
特斯拉在上海超級工廠的設(shè)計過程中,挑戰(zhàn)了很多傳統(tǒng)汽車工程的經(jīng)驗,如采用了直線型設(shè)計,大幅減少上下、轉(zhuǎn)彎次數(shù),并取消緩沖區(qū)冗余設(shè)計,制造效率大幅提升。自動化方面,上海超級工廠也是名副其實的全球榜樣。傳統(tǒng)汽車制造中,面漆和周圍結(jié)構(gòu)漆無法同時完成噴烤,但特斯拉創(chuàng)新性地將這兩個過程相結(jié)合起來,不僅節(jié)省時間,還降低了9%的能源消耗、9%的二氧化碳二次排放量。全自動生產(chǎn)線讓特斯拉生產(chǎn)效率極大提升,以往數(shù)千人才能完成的傳統(tǒng)生產(chǎn)線工作效率,如今特斯拉只需要幾十人即可完成。
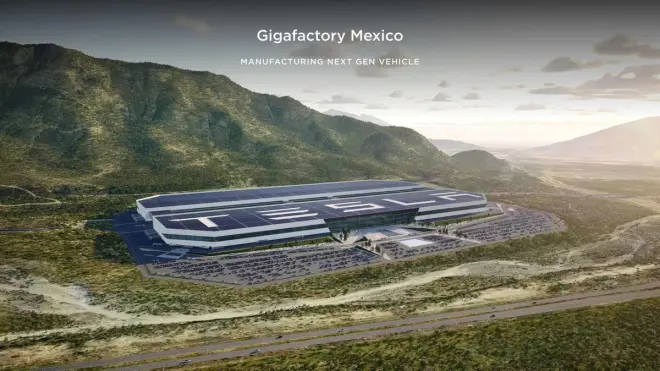
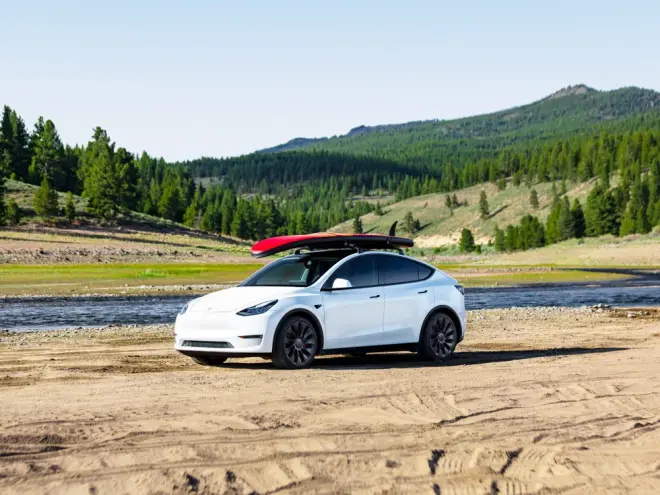
此外,弗里蒙特工廠在大量創(chuàng)新改進(jìn)后,生產(chǎn)節(jié)拍提速10%;柏林和得州超級工廠目前也具備了每周生產(chǎn)4000臺Model Y的能力。
持續(xù)提高生產(chǎn)制造效率的特斯拉,首次實現(xiàn)100萬輛汽車下線花了12年時間,第二個100萬輛只花費了18個月,而到第三個100萬輛時,僅用時11個月。7個月之后,特斯拉全球產(chǎn)量已經(jīng)突破400萬大關(guān),達(dá)成又一里程碑。
投資者日上,馬斯克也宣布又一座超級工廠——墨西哥蒙特利超級工廠即將誕生。該工廠將采用“拼樂高”式的制造方式,即讓汽車部件分為六部分各自分開裝配,然后再組裝在一起,并且只組裝一次。這將讓操作空間密度提升44%的同時,空間利用效率提升30%,最終實現(xiàn)生產(chǎn)線占地面積減少40%以上,對比Model Y生產(chǎn)成本減少50%。
墨西哥超級工廠的建立,也將繼續(xù)為提升全球產(chǎn)能、達(dá)成2030年交付2000萬輛電動車增長的目標(biāo)而努力。