模流分析(CFD)軟件在鋁泡沫成型工藝上的應(yīng)用-馬路科技
本應(yīng)用簡報由Erlangen-Nuremberg大學金屬科學與技術(shù)系主任,材料科學系Johannes Hartmann和VeraJüchter提供
鋁泡沫顯示出優(yōu)異的性能,如良好的阻尼,高能量吸收和質(zhì)量比彎曲剛度[1]。剛度使其在承重和同時使用輕質(zhì)結(jié)構(gòu)時尤其具有吸引力。為了提高這種重量比剛度和更好的載荷傳遞,需要一個緊湊的外殼[2],如在鋁泡沫三明治(AFS)中實現(xiàn)的那樣。
Erlangen-Nuremberg大學金屬科學與技術(shù)系主任研制了改進的壓鑄工藝“整體泡沫成型(IFM)”,以生產(chǎn)具有完整實心表皮,發(fā)泡芯和漸變的鋁泡沫過渡區(qū)之間(見圖1)。該工藝是由聚合物的發(fā)泡注塑成型開發(fā)的,因此適用于具有緊湊層的復雜泡沫部件的成本有效的一步式大規(guī)模生產(chǎn)。本說明中描述的CFD軟件Flow-3D模擬技術(shù)已被用于對此過程進行建模,作為選擇過程參數(shù)的輔助手段。
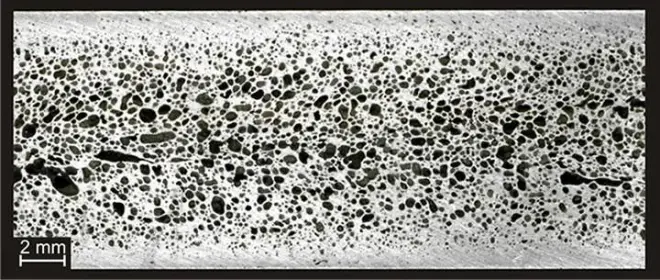
鋁泡沫整體式成型技術(shù)
因此,一定量的發(fā)泡劑(氫化鎂,MgH2)被放置在流道系統(tǒng)中,并且噴射室充滿鋁熔體(示意性工藝循環(huán)如圖2所示;該過程在[3]中詳細描述) 。隨著活塞前進,粉末以紊流方式夾帶到模具中。在技術(shù)變型“高壓一體式泡沫成型(HP-IFM)”的情況下,該零件在標準壓鑄工藝中已知的高環(huán)境壓力下完全填充,從而確保出色的表面質(zhì)量。從模具的回火表面開始,熔體開始凝固成完整的固體表皮。幾毫秒后 – 即所謂的延遲時間 – 模具在抽芯系統(tǒng)上打開,體積局部增加(并減小壓力),由于熱分解和氫釋放,在內(nèi)部半靜態(tài)區(qū)域開始孔的生長的氫化鎂顆粒。
每個發(fā)泡劑顆粒代表孔生長開始的孔核,直到它被同時膨脹的相鄰孔的反壓停止為止。由此形成的單元壁通過主要凝固的鋁合金顆粒穩(wěn)定化,所謂的內(nèi)源穩(wěn)定[4]。每個發(fā)泡劑顆粒代表孔生長開始的孔核,直到它被同時膨脹的相鄰孔的反壓停止為止。由此形成的單元壁通過主要凝固的鋁合金顆粒穩(wěn)定化,所謂的內(nèi)源穩(wěn)定[4]。每個發(fā)泡劑顆粒代表孔生長開始的孔核,直到它被同時膨脹的相鄰孔的反壓停止為止。由此形成的單元壁通過主要凝固的鋁合金顆粒穩(wěn)定化,所謂的內(nèi)源穩(wěn)定[4]。
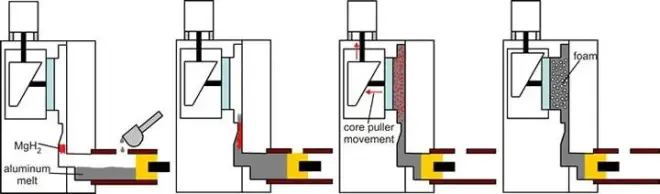
在鑄造部件的整個體積中均勻泡沫形態(tài)的先決條件是在分解開始時顆粒的良好分布。此外,發(fā)泡劑夾帶期間熔體的溫度一方面決定氫化鎂的分解動力學(參見圖3),另一方面決定發(fā)泡過程中固相的量。由于毛細作用力引起的熔體排液導致毛孔粗化,固化的α-晶粒不足導致形成相鄰孔之間的非穩(wěn)定支柱。然而,大量的固相增加了基體的剛性,并通過阻礙發(fā)育孔的球化導致結(jié)構(gòu)破壞[2]。
微孔鋁泡沫整體工藝 – 接近工藝限制
Flow-3D是一個強大的模流分析工具,能模擬泡沫整體成型過程,不僅有助于調(diào)查新零件設(shè)計的模具填充性能,還可以預測顆粒夾帶并確定泡沫演變條件,從而節(jié)省成本密集型試驗系列。目前研究的目標是在保持孔隙度水平不變的同時減小孔徑。Flow-3D計算流體動力學(CFD)仿真將有助于盡可能接近當前的流程限制或甚至進一步推動它們。泡沫形態(tài)的改進不僅會導致更均勻的結(jié)構(gòu),而且機械性能的分散性更小,而且還會允許生產(chǎn)更薄的部件,其機械性能可能由有限元件確定。
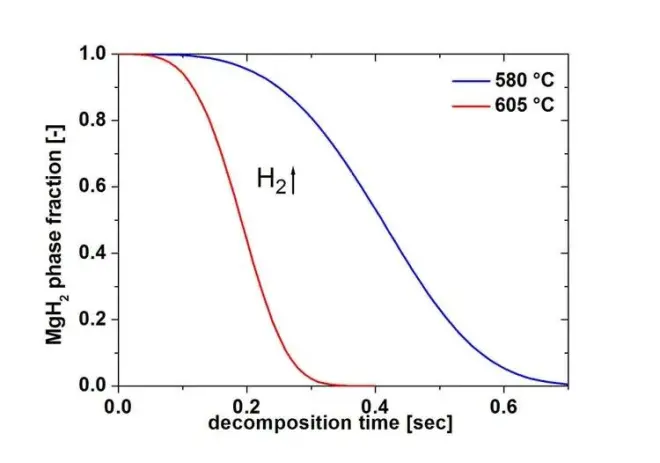
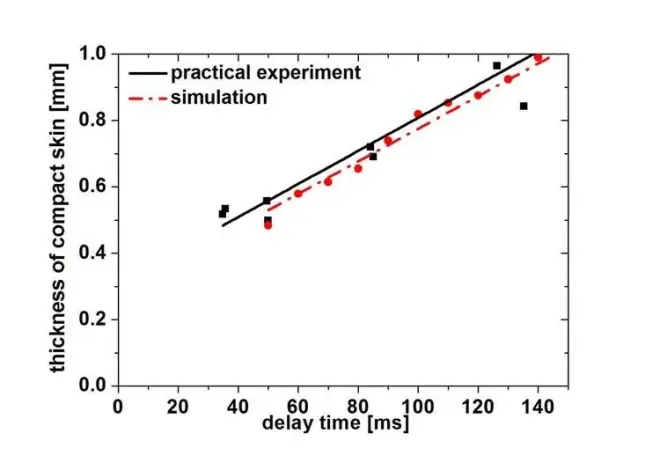
將仿真參數(shù)調(diào)整為實用的整體泡沫成型實驗
為了能夠使用?Flow-3D 的 CFD模擬來預測顆粒行為或溫度場的可靠性,必須通過調(diào)整這些參數(shù)以匹配實際實驗來確定不同的模擬參數(shù)。為此,整體式泡沫部件的生產(chǎn)延遲時間大約介于5秒之內(nèi)。30和130ms導致不同的致密的表皮厚度,其中由于固相分數(shù)超過一定百分比而不可能形成泡沫在模膨脹和孔生長開始的時刻。這導致了一個特征性的所謂的凝固曲線,其軸截距和斜率取決于模具溫度和其他選擇的工藝參數(shù)(見圖4)。通過改變傳熱系數(shù)(完全液態(tài)熔體的值以及完全固化的熔體)來模擬合金AlSi9Cu3(Fe)的鑄造周期,可以擬合實驗?zāi)糖€。為了實現(xiàn)這一目標,有必要將模擬延伸到射流室中的熔體計量,以描繪活塞運動開始之前的實際溫度分布。通過放置熱電偶在射擊室局部測量溫度,并且可以成功描繪與模擬內(nèi)的真實數(shù)據(jù)非常吻合的溫度。
在第二步中,使用Flow-3D定義熔體流動行為(例如表面張力或凝固阻力系數(shù))的其他參數(shù) 通過將不同設(shè)置的模擬與在填充模具之前活塞停止的實驗研究(參見圖5)進行比較來調(diào)整。一旦模擬內(nèi)的熔體流動與實際測試一致,就設(shè)定參數(shù)。
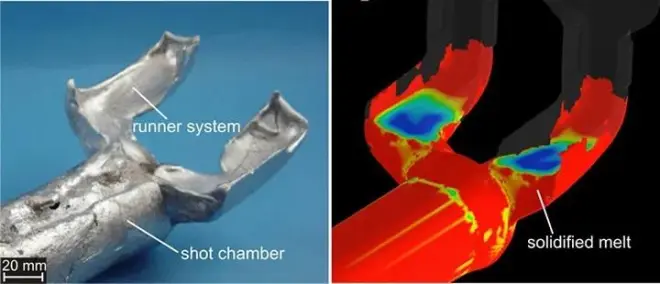
在確定冷卻以及熔體的流動特性之后,模擬顆粒的夾帶。為了調(diào)整正確的顆粒/流體相互作用的模擬, 通過比較X射線樣品來擬合顆粒阻力的顆粒定義參數(shù) 系數(shù),其中在X射線表征中具有比氫化鎂高的對比度的替代顆粒是鋁夾帶,例如銅或鐵顆粒(見圖6)。模擬結(jié)果與實驗非常吻合,因此可以推斷粒子分布的可靠預測作為過程參數(shù)的函數(shù)。
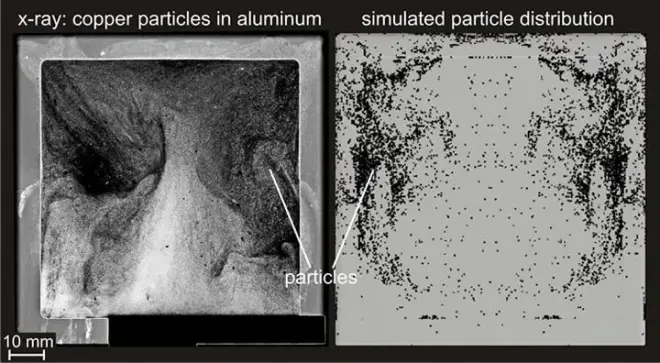
結(jié)論
總之,可以證明?FLOW-3D 模流分析軟件可以成為找尋在實際生產(chǎn)之前制造新整體泡沫部件的潛在弱點的重要工具。這樣就可以保證無冷流或死區(qū)的成功填充和發(fā)泡劑分布。此外,由于預期的溫度場的正確描述,可以推斷形成致密的表皮和氫化鎂的分解性質(zhì)(以及因此孔形成條件)。這提供了定義工藝參數(shù)以滿足客戶對整體泡沫結(jié)構(gòu)的要求的潛力。
1 標準是固體相部分,其中剪切強度和因此孔隙演變的阻力急劇增加。
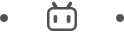
馬路科技作為FLOW-3D中國公司授權(quán)經(jīng)銷商,我們會提供了各種學習途徑,比如定期的培訓計劃、線上/線下的研討會和相關(guān)的鑄造展覽會,為用戶以及想了解和學習的人們提供專業(yè)的持續(xù)教育。