工廠布局精益化方案,拿走不謝!
精益化是一種管理理念,旨在通過減少浪費(fèi)、提高效率和質(zhì)量來優(yōu)化工廠布局。下面。天行健精益管理咨詢顧問總結(jié)實(shí)現(xiàn)工廠精益化的一般步驟:
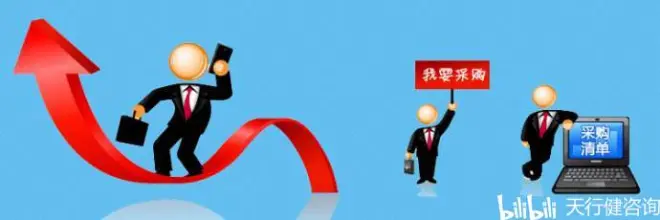
1. 明確價(jià)值流:首先,了解生產(chǎn)過程中的價(jià)值流,包括原材料的進(jìn)入、加工過程和最終產(chǎn)品的交付。通過繪制價(jià)值流圖可以幫助識別不必要的環(huán)節(jié)和浪費(fèi)。
2. 識別浪費(fèi):分析生產(chǎn)過程中可能存在的各種浪費(fèi),如過度生產(chǎn)、庫存積壓、等待時(shí)間、運(yùn)輸成本等。標(biāo)記和識別這些浪費(fèi)是精益化改進(jìn)的關(guān)鍵。
3. 實(shí)施5S:5S是一個基于日本管理模式的工作場所組織方法。它包括整理、整頓、清掃、清潔和自律。通過5S實(shí)施,工廠內(nèi)部可以保持整潔有序,提高工作效率。
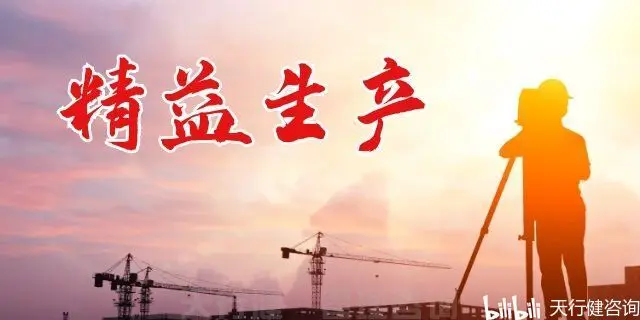
4. 建立小型化生產(chǎn)單元:將生產(chǎn)過程劃分為小型化生產(chǎn)單元,每個單元負(fù)責(zé)完成特定產(chǎn)品或者工藝的加工。這樣可以減少物料和信息的傳遞時(shí)間,提高響應(yīng)速度和靈活性。
5. 實(shí)施持續(xù)改進(jìn):精益化是一個持續(xù)改進(jìn)的過程,需要不斷尋找改進(jìn)的機(jī)會并進(jìn)行實(shí)施??梢圆捎靡恍┕ぞ吆图夹g(shù),如Kaizen活動、價(jià)值流映射、標(biāo)準(zhǔn)化工作等,來促進(jìn)持續(xù)改進(jìn)。
6. 培養(yǎng)員工參與精益化:鼓勵員工參與精益化改進(jìn),培訓(xùn)員工使用精益化工具和方法,使他們能夠主動發(fā)現(xiàn)問題并提出改進(jìn)建議。
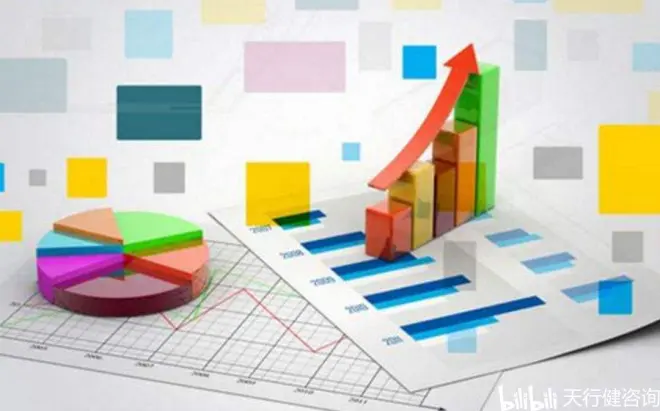
需要注意的是,每個工廠的情況可能不同,具體的步驟和方法可能會有所調(diào)整。但總體來說,通過明確價(jià)值流、識別浪費(fèi)、實(shí)施5S、建立小型化生產(chǎn)單元、持續(xù)改進(jìn)和培養(yǎng)員工參與,可以實(shí)現(xiàn)工廠的精益化布局。