鎳基合金(inconel X-750)化學(xué)成分性能參數(shù)
目前,加工硬化、熱處理?xiàng)l件對X-750合金如抗拉強(qiáng)度、屈服強(qiáng)度、伸長率及硬度等力學(xué)性能的影響已有較多研究[14],γ'相的形態(tài)、數(shù)量、分布和尺寸對X-750合金的強(qiáng)化效果有重要影響[15],但少有冷拉拔減面率對X-750合金絲材γ'相析出影響規(guī)律的研究。因此,本工作通過試驗(yàn),研究冷拉拔減面率及時(shí)效溫度對X-750合金絲材微觀組織特別是γ'相的影響,進(jìn)而探究其強(qiáng)化機(jī)理以及對C形環(huán)密封特性的影響。
1?實(shí)驗(yàn)
1.1?實(shí)驗(yàn)材料
本工作所研究的X-750合金與美國標(biāo)準(zhǔn)ASTM B637-15、SAE AMS 5698G(2007)中牌號為UNS N07750合金的成分相符,雜質(zhì)元素控制更為嚴(yán)格,純凈度更高。實(shí)驗(yàn)合金用工業(yè)純鐵、金屬鉻、電解鎳等配制,采用真空雙聯(lián)冶煉工藝,經(jīng)鍛造→熱軋→固溶處理→冷拉拔→中間熱處理→冷拉拔工序制備出φ1.8 mm的試驗(yàn)用初始絲材,其化學(xué)成分如表1所示。
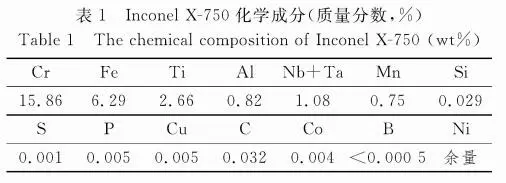
來百度APP暢享高清圖片
1.2?試樣制備
如圖1所示,利用NETZSCH STA 449 F3同步熱分析儀,通過差示掃描量熱法(Differential scanning calorimetry,DSC)與熱重分析法(Thermogravimetricanalysis,TG)聯(lián)用(升溫速率為10℃/min),測定初始絲材的DSC曲線及TG曲線,以確定材料在加熱過程中發(fā)生相變的情況及轉(zhuǎn)變溫度。
由圖1中TG曲線可知,X-750合金絲材在加熱至1500℃過程中質(zhì)量共增加約0.8%,且曲線斜率基本保持恒定,這是高溫氧化導(dǎo)致的增重。由DSC曲線可知,X-750合金升溫過程可以分為4個(gè)階段:第一階段由室溫至650 ℃左右,絲材物理化學(xué)性能穩(wěn)定,未發(fā)生任何相變反應(yīng);第二階段由650℃左右至829.7℃,曲線斜率發(fā)生變化,829.7℃出現(xiàn)拐點(diǎn)但無吸熱峰,這可能是雙峰疊加,根據(jù)文獻(xiàn)[16],該階段過飽和奧氏體發(fā)生調(diào)幅分解,Ti、Al元素富集區(qū)形成γ'相,從γ相基體中均勻析出;第三階段由829.7℃至1338.1℃,在1172.5℃時(shí)出現(xiàn)吸熱峰,隨溫度繼續(xù)升高,該階段擴(kuò)散速率較高,發(fā)生γ'相向η相的轉(zhuǎn)變-8,并伴有γ'相回熔;第四階段由1338.1℃至1500℃,該階段X-750合金發(fā)生熔融,開始溫度為1338.1℃,在1375.3℃出現(xiàn)吸熱峰,熔融完全溫度為1379.6 ℃。
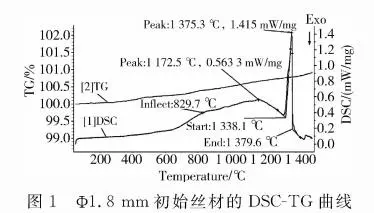
第二階段出現(xiàn)拐點(diǎn)卻無吸熱峰的原因可能是與第三階段出現(xiàn)雙峰疊加,用Origin軟件進(jìn)行雙峰分離擬合,結(jié)果如圖2所示。第一個(gè)吸熱峰出現(xiàn)在849.8℃,第二個(gè)吸熱峰出現(xiàn)在1172.8℃;γ'相析出開始溫度為649℃,η相轉(zhuǎn)變開始溫度為876 ℃。因此選取649~876 ℃作為時(shí)效溫度選區(qū)。
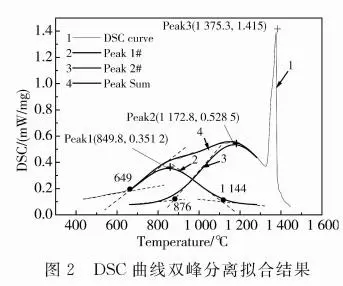
實(shí)驗(yàn)所用試樣制備流程如圖3所示。按照圖3所示方法制備減面率分別為0%、30%、60%的實(shí)驗(yàn)絲材,減面率(Cross section reduction rate,CSRR)的計(jì)算如式(1)所示:
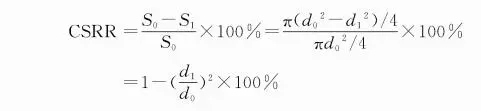
式中:do、d?分別為冷拉拔變形前后絲材的直徑。時(shí)效條件分別為不人工時(shí)效、650℃×16 h、730 ℃×16 h、810 ℃×16 h。
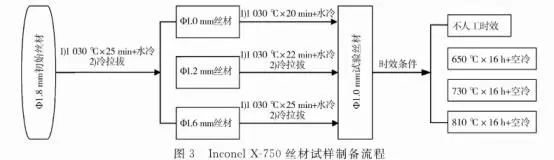
1.3?實(shí)驗(yàn)方法
用于低倍組織檢測的試樣,按國標(biāo)GB/T 14999.1-2012、GB/T 6394-2002進(jìn)行樣品鑲嵌、機(jī)械磨光、拋光,使用1.5gCuSO?+40 mL HCl+20 mLC?H?OH進(jìn)行化學(xué)侵蝕,在OLYMPUS-GX51金相顯微鏡下觀察金相組織并用ImagePro Plus6.0軟件測試平均晶粒尺寸。
用于硬度檢測的試樣,按國標(biāo)GB/T 4340-2009進(jìn)行樣品鑲嵌、機(jī)械磨光、拋光,用HDX-1000型顯微硬度計(jì)進(jìn)行硬度測試。
用于掃描電鏡觀察的試樣,采用20% H?SO?+80%CH?OH溶液對打磨后試樣進(jìn)行電解拋光(電解電壓為15V,時(shí)間為25s),然后在40%C3H?O?+20% HNO?+10% HCl水溶液中對其進(jìn)行電解侵蝕后(電解電壓為6V,時(shí)間為5 s),利用ZEISS SUPRA 55場發(fā)射掃描電子顯微鏡及X射線能譜儀進(jìn)行試樣分析。
按國標(biāo)GB/T 18876.1-2002采用Photoshop CS6及軟件對試樣顯微照片中y'相粒子進(jìn)行圖像分析及體視學(xué)測定。每個(gè)樣品隨機(jī)選取20個(gè)不同視場,用掃描電鏡獲得對應(yīng)顯微照片,通過Photoshop處理獲得黑白、暗亮分明的圖片,利用圖像分析軟件測量γ'相粒子的面積、直徑及數(shù)量。將每個(gè)試樣所有視場下的尺寸求平均值即為γ'相粒子的平均直徑,按照式(2)、式(3)分別計(jì)算單個(gè)視場下γ'相粒子的體積分?jǐn)?shù)及單位面積數(shù)量,再通過數(shù)學(xué)計(jì)算求得所有視場的平均值即為γ相的體積分?jǐn)?shù)及密度。
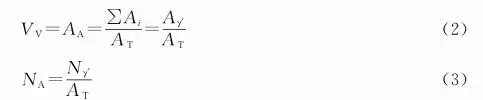
式中:Vv、A、N?分別為單個(gè)視場γ'相的體積分?jǐn)?shù)、面積分 片數(shù)及單位面積上γ'相粒子的數(shù)目,A;、A,、A、N,分別為單顆γ'相粒子的面積、γ'相的總面積、測量面積(視場面積)、單個(gè)視場中y'相粒子的數(shù)量。將經(jīng)過730℃時(shí)效處理16h后的X-750合金絲材繞制成外徑為φ11.3mm的彈簧,以Inconel600合金作為中間包覆層,純銀作為密封層,制成φ318 mm的C形環(huán),利用5000 kN的壓縮試驗(yàn)機(jī)、氦質(zhì)譜檢漏儀進(jìn)行壓縮回彈試驗(yàn),并用計(jì)算機(jī)進(jìn)行控制和數(shù)據(jù)處理。
2?結(jié)果與討論
2.1?冷拉減面率及時(shí)效溫度對微觀組織的影響
實(shí)驗(yàn)用初始絲材的金相組織照片如圖4所示,材料由等軸晶粒組成,奧氏體基體上分布有最大直徑約為4μm的MC型碳化物,小尺寸顆粒碳化物呈球形或橢球形,大顆粒則呈較規(guī)則多邊形,并伴有大量退火、形變孿晶及滑移帶。
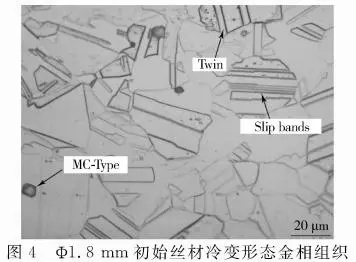
圖5為不同減面率及時(shí)效溫度下絲材樣品的晶粒尺寸測量結(jié)果,可知隨減面率增加,晶粒尺寸均有減小趨勢,減面率由0%增加至30%時(shí)晶粒尺寸減小約6~9μm,減面率由30%增加至60%時(shí)晶粒尺寸減小約3~5μm。增大減面率可增強(qiáng)晶粒細(xì)化效果,晶界面積越大,對位錯(cuò)滑移的阻礙作用越大。更大的減面率使得絲材在強(qiáng)烈的三向應(yīng)力作用下產(chǎn)生高的變形度,從而增加了位錯(cuò)密度,這會增加再結(jié)晶形核位置,使晶粒細(xì)化程度提高[],而時(shí)效溫度對晶粒尺寸沒有明顯影響。
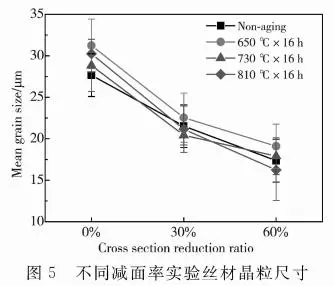
2.2?冷拉減面率及時(shí)效溫度對析出相和力學(xué)性能的影響
圖6為60%減面率絲材730℃時(shí)效16 h后的SEM照片,及位置1、2、3、4對應(yīng)的EDS定量分析結(jié)果,在晶內(nèi)和晶界(特別是三角晶界處)分布有粒徑約2~4μm較大顆粒的一次碳化物,由表2可知其為(Nb,Ti)C;沿晶界、孿晶及亞晶處呈半連續(xù)析出有長度約0.3μm長條狀的二次碳化物,由表2可知其為CrCs。可見大的減面率會使時(shí)效后二次碳化物析出位置由晶界拓展至孿晶及亞晶界,并且更高的位錯(cuò)密度還會增加碳化物形核及長大的擴(kuò)散通道,因此會形成彌散析出的細(xì)小顆粒,增加對位錯(cuò)的釘扎作用[20]。
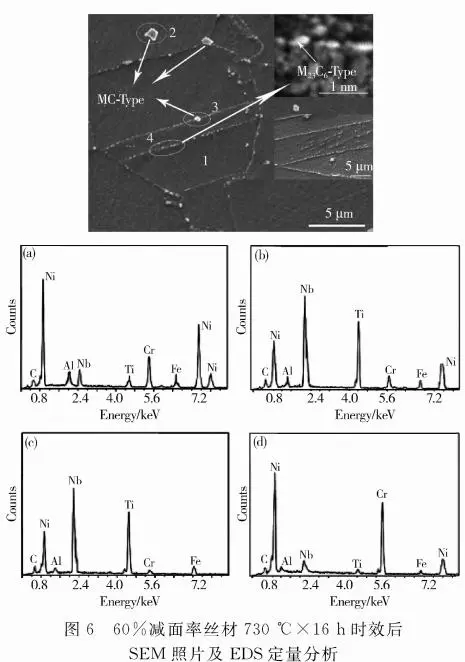
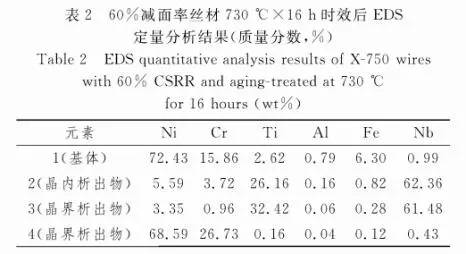
圖7給出了不同減面率及不同時(shí)效溫度下實(shí)驗(yàn)絲材的維氏硬度值,圖中每個(gè)點(diǎn)由一個(gè)試樣的5個(gè)隨機(jī)位置的硬度求平均值得出??芍唤?jīng)時(shí)效處理的絲材的硬度值最低,經(jīng)650 ℃、730℃、810℃時(shí)效處理的絲材由于沉淀強(qiáng)化硬度顯著提高,硬度值隨減面率的增加而增加。與未時(shí)效處理的絲材相比,經(jīng)時(shí)效的絲材硬度值提高約100HV~150HV;時(shí)效溫度由650℃升高至730℃,絲材硬度提高約40HV~80HV;時(shí)效溫度升至810℃,硬度降低60HV~120HV。因此時(shí)效溫度對材料硬度也有明顯的影響,時(shí)效過程中從基體γ相中析出γ'相,兩者點(diǎn)陣常數(shù)相近,界面共格,從而達(dá)到沉淀強(qiáng)化的效果,冷拉減面率及時(shí)效溫度對γ'相析出的影響如圖8所示。
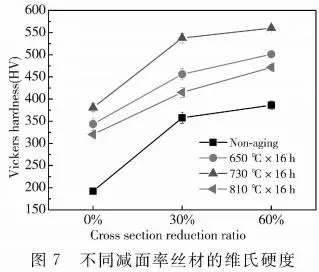
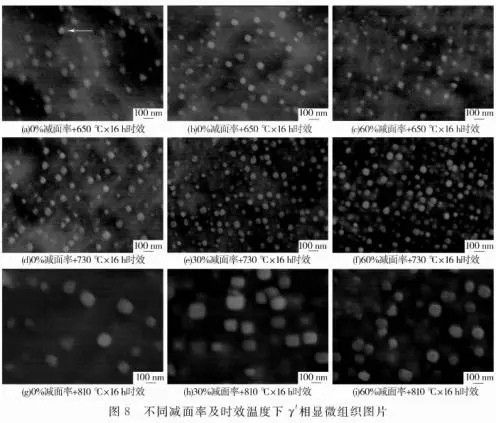
由圖8可知,實(shí)驗(yàn)絲材基體上彌散均勻地分布著γ'相顆粒,當(dāng)時(shí)效溫度為650℃時(shí),γ'相直徑較小,且尺寸均勻,約為40~60nm,形狀呈球形。當(dāng)時(shí)效溫度為730 ℃時(shí),γ'相直徑有微小長大,且尺寸較均勻,約為60~80nm,大部分呈球形,少數(shù)較大顆粒呈立方形。這個(gè)過程中,剛析出的γ'相與基體共格且呈球形,隨著γ'相逐漸長大,彈性應(yīng)變能會增大,其增大到一定程度時(shí)γ'相由球形轉(zhuǎn)變成立方形,與基體間的界面為半共格或非共格。因而晶界和晶內(nèi)碳化物周圍的y'相尺寸較小且呈球形,而碳化物較遠(yuǎn)處的γ'相繼續(xù)長大成立方形,直至回熔分裂成為二隅體或八隅體形狀。此時(shí)γ'相的尺寸由兩方面因素決定:(1)γ'相的長大受擴(kuò)散控制,其動力學(xué)過程主要由溫度決定,時(shí)效溫度升高,擴(kuò)散加快,促進(jìn)γ'相長大;(2)晶界和晶內(nèi)一次碳化物均含Nb、Ti,這必然會使其周圍基體中Nb、Ti的含量降低,它們的貧化必然會推遲γ'相的析出和長大[]。時(shí)效溫度升高至810 ℃時(shí),γ'相直徑明顯增大且不均勻長大趨勢明顯,約為0.08~0.2μm,同時(shí)γ'相顆粒數(shù)量明顯減少,呈立方形。還可以看出,當(dāng)γ'相顆粒尺寸在80~100 nm以上時(shí),其形狀由球形開始轉(zhuǎn)變?yōu)榱⒎叫巍?/p>
由圖8可知,同一時(shí)效溫度下,減面率增大時(shí),γ相顆粒數(shù)量有所增加,根據(jù)體視學(xué)原理進(jìn)一步進(jìn)行定量分析,測量γ相的數(shù)量、尺寸及體積分?jǐn)?shù),結(jié)果如圖9所示。從圖9(a)可以看出,在各時(shí)效溫度下,隨減面率增大,γ'相尺寸均有減小趨勢,但810℃時(shí)效情況下,當(dāng)減面率為30%時(shí),γ'相尺寸反而增大,這可能是因?yàn)榇藭r(shí)雖然晶內(nèi)位錯(cuò)密度較高,形核較多,但由于溫度較高,擴(kuò)散加強(qiáng),使一些形核位置的γ'相來不及長大,Nb、Ti、Al元素就擴(kuò)散至其他位置,使該處的γ'相長大明顯加快,尺寸較大。
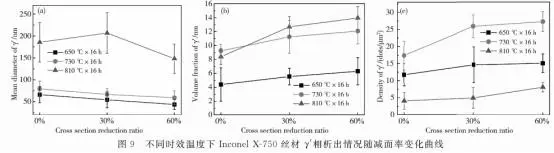
總地來講,γ'相尺寸隨減面率增大而減小,這是因?yàn)椋?1)減面率越大,材料內(nèi)部殘余應(yīng)力越大,因而γ'相在長大過程中受到應(yīng)力場的作用就越強(qiáng),其長大受阻;(2)由圖9(c)可知,減面率越大,γ'相顆粒數(shù)量越多,在有限的Nb、Ti、Al含量及一定的擴(kuò)散速率情況下,其尺寸越小。
從圖9(b)可知,相同時(shí)效溫度下,增大減面率在一定程度上有利于γ'相的析出,提高其體積分?jǐn)?shù)。從圖9(c)可知,γ'相顆粒的數(shù)量隨減面率增大而略有變多,時(shí)效溫度為730℃時(shí),γ'相顆粒的數(shù)量最多,密度約為17~27個(gè)/μm2,結(jié)合圖7中絲材的維氏硬度值,這解釋了其硬度最高的原因。當(dāng)時(shí)效溫度為810℃時(shí),γ相顆粒的數(shù)量最少,雖然此時(shí)其體積分?jǐn)?shù)最高,但由于擴(kuò)散作用加強(qiáng),γ相長大速度較快,這符合Ostwald熟化理論,y'相長大過程中,有部分γ'相小顆粒回熔,Nb、Ti、Al元素?cái)U(kuò)散至另外的顆粒,使其繼續(xù)長大,因而γ'相顆粒尺寸大,且顆粒數(shù)量少。
2.3 C形環(huán)壓縮回彈試驗(yàn)
如圖10所示,C形環(huán)由三部分組成:外部密封層和中間包覆層組成外殼,外殼內(nèi)包裹螺旋形圓柱彈簧。密封層為純銀材料,包覆層為Inconel 600合金材料,?彈簧材料為文章所研究的Inconel X-750合金。該結(jié)構(gòu)依靠彈簧獲得良好的回彈性和必要的密封比壓,依靠軟金屬包覆套管獲得良好的密封接觸表面,達(dá)到密封效果。當(dāng)壓縮該密封環(huán)時(shí),螺旋形彈簧的每一圈對金屬外殼產(chǎn)生附加的反作用力,使外部密封層發(fā)生塑性變形,填實(shí)法蘭密封表面的微觀粗糙不平和局部表觀缺陷[8]。
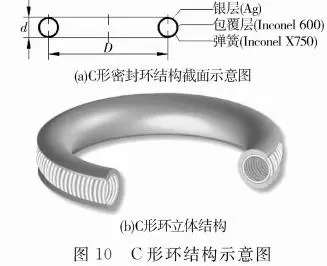
其中純銀材料為退火態(tài),抗拉強(qiáng)度為175 MPa,硬度為50HV,彈性模量為64 GPa。Inconel 600合金材料為退火態(tài),抗拉強(qiáng)度為610 MPa,屈服強(qiáng)度為243 MPa,延伸率為43%,硬度為144HV。本研究中X-750合金絲材減面率越大其強(qiáng)度越高,但塑性及韌性下降,因此C形環(huán)用X-750絲材減面率為30%,并經(jīng)730℃時(shí)效處理16 h,其抗拉強(qiáng)度為1423~1530 MPa,屈服強(qiáng)度為1255~1260 MPa,延伸率為18%~25%,斷面收縮率為40%~45%。
分別經(jīng)0.9 mm、1.1 mm、1.4 mm、1.7 mm壓縮量下的壓縮回彈試驗(yàn)檢測結(jié)果如圖11所示。
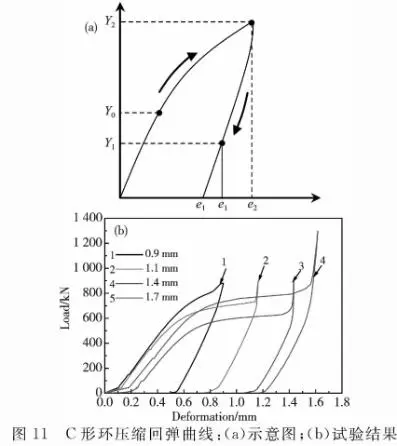
圖11(a)為載荷-變形曲線示意圖。其中Y。為達(dá)到規(guī)定泄漏率水平時(shí)的壓縮載荷,Y。為達(dá)到規(guī)定壓縮量e2時(shí)的壓縮載荷,當(dāng)壓縮載荷從Y。卸載到Y(jié)?,壓縮量從e回彈至e,要求泄漏率不高于1.33×10?9Pa·m3/s(氦氣,△P=0.1 MPa)。e2-e1稱為有效回彈量,應(yīng)不小于0.2 mm,當(dāng)壓縮載荷完全卸除后,壓縮量回彈至e',e:-e'稱為總回彈量,應(yīng)不小于0.25 mm]。從圖11(b)可知,加載曲線具有明顯的彈性段和塑性段,當(dāng)壓縮達(dá)到一定量時(shí),螺旋彈簧開始出現(xiàn)塑性變形,
彈簧的剛度下降。卸載時(shí),隨著載荷減小,C形環(huán)產(chǎn)生彈性回彈,壓縮量逐漸減小,當(dāng)載荷減小至0時(shí),C形環(huán)仍存在殘余變形。并且隨著壓縮量增加,殘余變形增大,曲線整體位置右移,當(dāng)壓縮量為0.9mm、1.1mm、1.4mm時(shí),Y2點(diǎn)載荷相差不大,約為880~900kN,壓縮量為1.7mm時(shí),Y2點(diǎn)載荷增大,約為1200 kN。
不同壓縮量下,壓縮回彈試驗(yàn)過程密封特性曲線如圖12所示。密封特性曲線有關(guān)參數(shù)如表3所示。
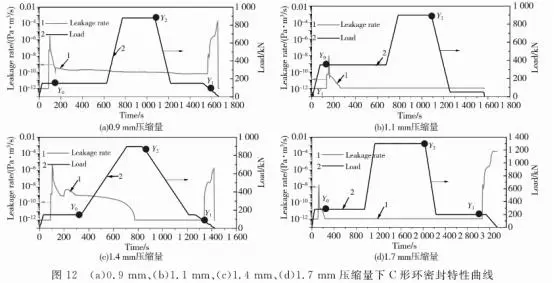
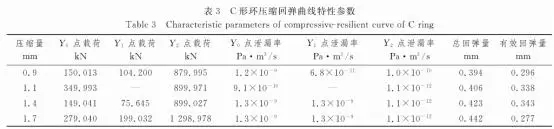
由表3可看出,壓縮量越大,回彈量越大,即使壓縮量小于1.4mm,泄漏率仍能達(dá)到要求(≤1.33×10-9Pa·m3/s),并且泄漏率數(shù)值與較大壓縮量下相當(dāng)??偟幕貜椓考s為0.4mm,完全滿足不小于0.25 mm的要求,有效回彈量為0.277~0.343 mm,也滿足不小于0.2mm的要求。因此,實(shí)驗(yàn)絲材滿足C形環(huán)彈簧用材料的各項(xiàng)性能要求,由其制成的C形環(huán)在壓縮回彈試驗(yàn)條件下表現(xiàn)出良好的密封性能。
3?結(jié)論
(1)?增大冷拉減面率,在一定程度上可使X-750合金中起主要強(qiáng)化作用的γ'相尺寸更細(xì)小,體積分?jǐn)?shù)增大,顆粒數(shù)量變多,沉淀強(qiáng)化效果提高,材料強(qiáng)度提高。
(2)?與減面率相比,時(shí)效溫度對X-750合金晶粒尺寸的影響不大,主要是從γ'相的數(shù)量、形狀及尺寸來影響材料強(qiáng)度。欠時(shí)效及峰時(shí)效狀態(tài)下,時(shí)效溫度越高,γ'相體積分?jǐn)?shù)越大,y'相顆粒數(shù)量越多;但過時(shí)效狀態(tài)下,由于γ'相顆粒Ostwald熟化長大,其尺寸劇烈長大,數(shù)量明顯減少。隨時(shí)效溫度升高,γ'相形狀由球形向立方形轉(zhuǎn)變,轉(zhuǎn)變開始尺寸約80~100 nm。
(3)增大冷拉減面率雖然能減小γ相尺寸,增大其數(shù)量及體積分?jǐn)?shù),但時(shí)效溫度對γ'相數(shù)量、形狀、體積分?jǐn)?shù)及大小的影響較減面率更強(qiáng)烈。