優(yōu)思學(xué)院|如何系統(tǒng)地學(xué)習(xí)精益管理(CLMP)?
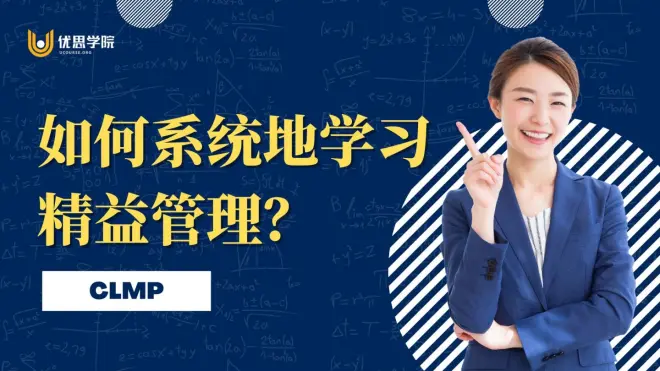
豐田生產(chǎn)模式經(jīng)過詹姆斯·P·沃麥克和丹尼爾·T·瓊斯多年的努力研究和在他們的著作《改變世界的機(jī)器》、《精益思想》等作出深入的闡述之后,已經(jīng)成為了一個(gè)相當(dāng)完整的知識(shí)體系。
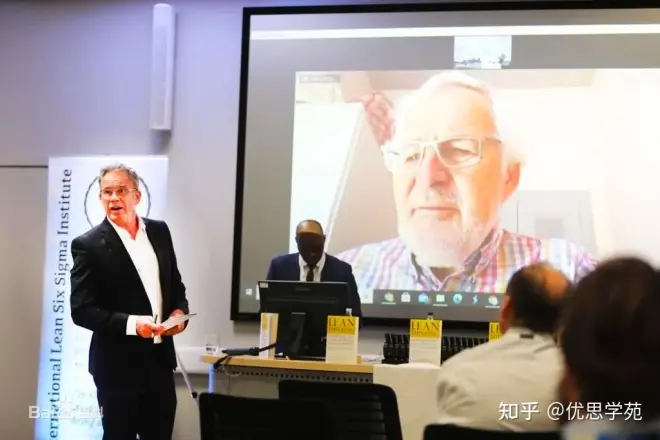
最常用來解釋這個(gè)體系的就是精益之屋。
精益之屋是將豐田精益生產(chǎn)方式的各個(gè)要素系統(tǒng)化圖示的一種形式,由于其形狀像一間屋,因而稱為精益之屋,如下圖就是密歇根大學(xué)工業(yè)和運(yùn)營(yíng)工程教授,Jeffrey K. Liker所制定的豐田精益之屋,首先是來自他的著作《豐田生產(chǎn)模式》一書。

我們可以把精益之屋理解為一整套適用于本企業(yè)運(yùn)營(yíng)的精益方法的組成。
精益之屋亦有眾多不同的版本。企業(yè)可以根據(jù)自身的情況自己制定自己的精益之屋,當(dāng)然這也不是必需要的,不過精益之屋的確可以直觀地展示了在組織中實(shí)施精益的結(jié)構(gòu),讓大家對(duì)精益管理理論的結(jié)構(gòu)有一個(gè)初步的印象。
即使精益之屋有多種版本,但核心原則都一樣,它始于達(dá)成質(zhì)量最優(yōu)、成本最低與最短交付時(shí)間等目標(biāo),作為——屋頂。
然后,是兩個(gè)大支柱——準(zhǔn)時(shí)生產(chǎn)和自働化。
屋的中心是尊重人員、消除浪費(fèi)。
地基則是由幾項(xiàng)要素構(gòu)成,其中包括平準(zhǔn)化、標(biāo)準(zhǔn)化作業(yè)、目視化管理,以及精益管理的14個(gè)原則。
另外,你亦可以透過不同機(jī)構(gòu)的培訓(xùn)大綱,了解他們的思路,不同的機(jī)構(gòu)可能會(huì)有不同的側(cè)重點(diǎn)和思路,你也可以從中了解他們的思維方法。
當(dāng)然,學(xué)習(xí)的順序其實(shí)并不是非常重要,你可以從精益管理的原則開始,然后從浪費(fèi)的界定入手,也可以從價(jià)值流動(dòng)的管理開始入手,因?yàn)榫婀芾淼母拍詈凸ぞ叨际腔ハ嚓P(guān)聯(lián)的,不論你從哪里開始下手,最后都會(huì)發(fā)現(xiàn)很容易理解和輕易地融會(huì)貫通。
以下,分享一下優(yōu)思學(xué)院?精益管理學(xué)會(huì)的精益管理專業(yè)人員認(rèn)證課程(CLMP)作為參考。
第一部 精益思想基礎(chǔ)
1.00 歡迎和學(xué)習(xí)方式介紹
1.01 精益管理的源起
1.02 精益管理的前世今生
1.03 精益管理的獲利思維模式
1·04 精益管理的思想
1.05 精益之屋
第二部 發(fā)掘隱藏的價(jià)值
2.01 隱藏的價(jià)值
2.02 增值活動(dòng)和非增值活動(dòng)
2.03 認(rèn)識(shí)價(jià)值流
2.04 精益管理的五個(gè)原則
第三部 消除浪費(fèi)和3M 原理
3.01 七種浪費(fèi)(運(yùn)輸、庫(kù)存、動(dòng)作)
3.02 七種浪費(fèi)(等待、生產(chǎn)過剩、過度處理、缺陷)
3.03 第八種浪費(fèi)
3.04 精益思想中的三個(gè)M
第四部 價(jià)值流動(dòng)管理和拉動(dòng)模式
4.01 交付時(shí)間 Lead Time (L/T)
4.02 批量生產(chǎn)和單件流
4.03 平準(zhǔn)化生產(chǎn)
4.04 節(jié)拍時(shí)間 Takt Time (T/T)
4.05 周期時(shí)間 Cycle Time (C/T)
4.06 分析瓶頸和優(yōu)化流程
4.07 拉動(dòng)模式的概述
4.08 看板系統(tǒng)
4.09 看板在項(xiàng)目管理中的應(yīng)用
第五部 精益管理工具
5.01 5S 游戲
5.021 5S方法重點(diǎn)剖析(上)
5.022 5S方法重點(diǎn)剖析(下)
5.03 5S方法在辦公室的應(yīng)用
5.04 目視化管理
5.05 標(biāo)準(zhǔn)化作業(yè)簡(jiǎn)介
5.06 標(biāo)準(zhǔn)化作業(yè) – 標(biāo)準(zhǔn)化作業(yè)圖
5.07 標(biāo)準(zhǔn)化作業(yè) – 標(biāo)準(zhǔn)化作業(yè)結(jié)合表
5.08 標(biāo)準(zhǔn)化作業(yè) – 產(chǎn)能表
5.09 SMED 快速切換原理
5.10 如何使用SMED方法?
5.11 設(shè)備綜合效率 OEE 原理
5.12 設(shè)備綜合效率 OEE 計(jì)算方法
5.13 OEE 計(jì)算實(shí)例
5.14 制作 OEE 試算表
5.15 OEE和六大損失
5.16 整體人力資源效率 OLE
第六部 精益價(jià)值流改革
6.01 利特爾法則
6.02 價(jià)值流圖簡(jiǎn)介
6.03 價(jià)值流圖 – 選擇產(chǎn)品系列
6.04 價(jià)值流圖 – 繪制現(xiàn)狀圖
6.05 價(jià)值流圖 – 繪制未來圖
6.06 價(jià)值流圖 – 實(shí)現(xiàn)未來圖
第七部 持續(xù)改善和質(zhì)量改進(jìn)工具
7.01 自働化
7.02 防錯(cuò)方法的三個(gè)層次
7.03 防錯(cuò)方法的十個(gè)基本原理
7.04 A3 和 PDCA 問題解決
7.041 PDCA 和 DMAIC 的區(qū)別
7.05 5W1H 問題描述
7.06 尋找可能原因的工具 – 魚骨圖
7.07 根本原因分析和5-Why
7.08 相關(guān)性及散布圖
7.09 數(shù)據(jù)收集方法 – 檢查表
7.10 數(shù)據(jù)分析方法 – 帕累托圖
7.11 過程質(zhì)量風(fēng)險(xiǎn)分析 – FMEA
7.12 過程能力指標(biāo)
7.13 其他質(zhì)量常用指標(biāo)
7.14 現(xiàn)場(chǎng)主義
第八部 精益戰(zhàn)略和方針管理
8.01 精益管理的戰(zhàn)略地圖
8.02 方針管理七個(gè)步驟(第一至四步)
8.03 方針管理(X-矩陣方法)
8.04 方針管理七個(gè)步驟(第五至七步)
8.05 團(tuán)隊(duì)動(dòng)力與常用團(tuán)隊(duì)工具
8.06 力場(chǎng)分析
8.07 領(lǐng)導(dǎo)者與管理者的差異
8.08 領(lǐng)導(dǎo)者和變革管理
8.09 沖突管理
8.10 領(lǐng)導(dǎo)者的5個(gè)特質(zhì)
8.11 精益管理的十四個(gè)原則
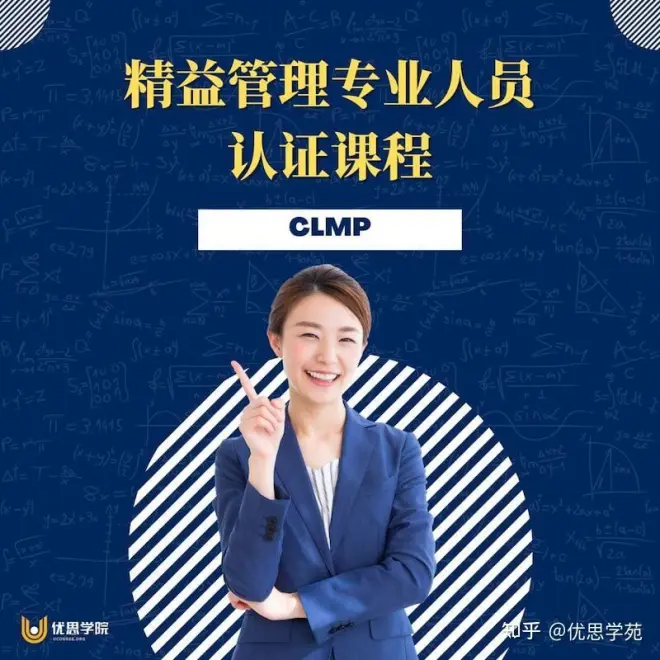