優(yōu)思學(xué)院|為什么搞精益管理的企業(yè)最后都死掉了?
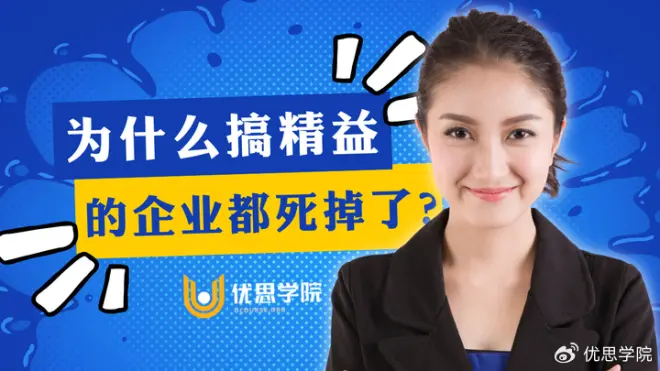
最近看到一些討論關(guān)于"為什么搞精益管理的企業(yè)最后都死掉了?"然而這個(gè)問題包含了很多預(yù)設(shè),令人以為搞精益會(huì)對(duì)公司不利。事實(shí)上聲稱自己是搞精益的和實(shí)際上在搞精益的是兩回事,可是除非我們是他們的員工,否則很難區(qū)分,所以說"為什么搞精益管理的企業(yè)最后都死掉了?"這個(gè)問題的前設(shè)已經(jīng)是難以成立的。
就如六西格瑪一樣,很多人問摩托羅拉為什么沒落了?六西格瑪為什么沒拯救摩托?老實(shí)說,流行的東西總是有人會(huì)吐槽,天下惟庸人無(wú)咎無(wú)譽(yù)?—— 這可能反而反映了它們的價(jià)值。
新鄉(xiāng)重夫(Shingo)曾經(jīng)說豐田生產(chǎn)系統(tǒng)的成功實(shí)施,不超過30-40%是來(lái)自于工具,而60-70%的成功來(lái)自于人,30年后的今天,一切都沒有改變!
精益項(xiàng)目失敗的原因
30年前美國(guó)哈佛大學(xué)的一項(xiàng)研究結(jié)果,涵蓋了400家不同的公司,分析了為什么這些公司的大多數(shù)項(xiàng)目會(huì)失敗,結(jié)論是失敗的四大原因如下:
1. 經(jīng)營(yíng)項(xiàng)目時(shí)缺乏方向和愿景
2. 缺乏分配給項(xiàng)目的時(shí)間
3. 缺少資源
4. 缺少公司員工的堅(jiān)持
所以,不要把公司的失敗簡(jiǎn)單地歸咎于單一工具,很多時(shí)候公司的失敗是難以預(yù)知的,管理層一個(gè)決策上的失誤就可以把公司推向死亡。
此外,有很多公司試圖仿效精益生產(chǎn)和六西格瑪管理等方法,希望能提升質(zhì)量工具套用于公司執(zhí)行改善方法中,但卻忽略了執(zhí)行這些精益營(yíng)運(yùn)方法背后的企業(yè)文化和制度,它們同時(shí)也忽略了,精益生產(chǎn)方法的綜合運(yùn)用,而無(wú)法仿制出另一個(gè)具有競(jìng)爭(zhēng)優(yōu)勢(shì)的豐田公司。
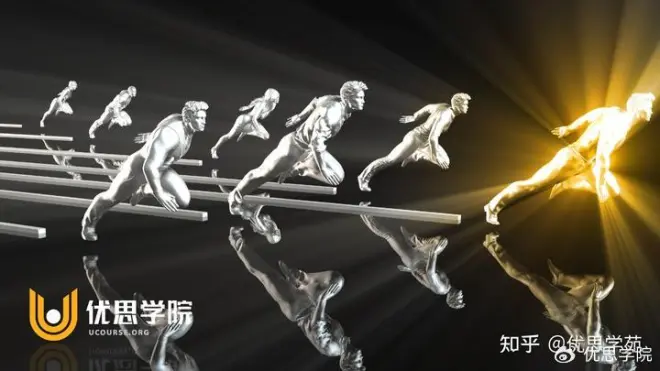
導(dǎo)入精益生產(chǎn)的建議
優(yōu)思學(xué)院對(duì)中小型企業(yè)導(dǎo)入精益生產(chǎn)的建議是:
1. 建議已逐項(xiàng)導(dǎo)入改善項(xiàng)目的方式,避免一次全面性導(dǎo)入,進(jìn)而造成資源不足而效果打折的情況。
2. 導(dǎo)入精益生產(chǎn)前,借由宣達(dá)或是教育培訓(xùn),不斷鼓勵(lì)人員培養(yǎng)創(chuàng)新,同時(shí)打破墨守成規(guī)之規(guī)定。
3. 導(dǎo)入精益生產(chǎn)前,首先先了解企業(yè)文化與制度,再草擬出最適合公司之改善方法,逐步予以導(dǎo)入。
4. 公司全體人員均須參與,從改善的過程中學(xué)習(xí)改善。
5. 導(dǎo)入前,一定要具備強(qiáng)而有力的改善決心,并找出問題點(diǎn),徹底解決根本原因。
6. 設(shè)立出最具公司特有之優(yōu)良文化,努力培養(yǎng)團(tuán)隊(duì)及專業(yè)人員,提升公司競(jìng)爭(zhēng)能力。
在開展精益生產(chǎn)前,如何確保每一個(gè)員工都能夠參與其中?最重要的是人員的培訓(xùn),優(yōu)思學(xué)院設(shè)計(jì)的精益管理(CLMP)課程可以讓大量員工獲得足夠的精益知識(shí)和認(rèn)可考核,員工甚至可以不用放棄日常工作的時(shí)間,只要每天花一小時(shí)左右自主學(xué)習(xí)即可。
?
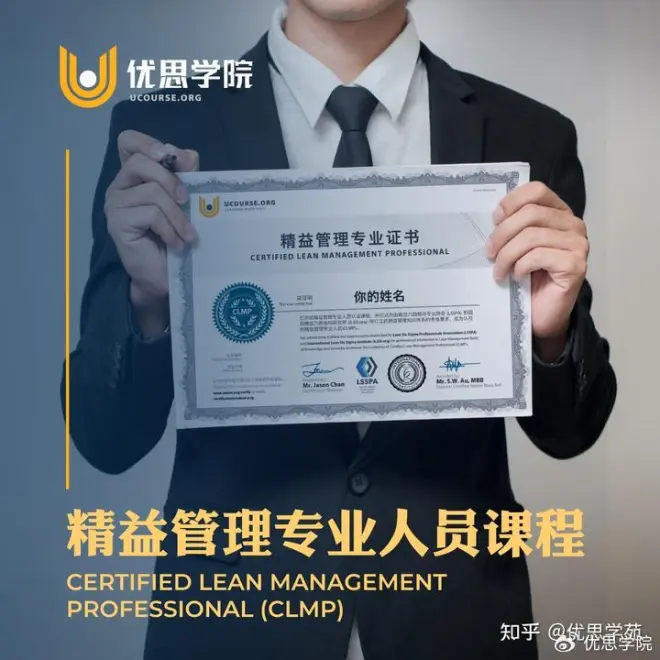