影響軸承鋼質(zhì)量的關(guān)鍵成分和夾雜物及其控制-軸承外觀的質(zhì)量要求
影響軸承鋼質(zhì)量的關(guān)鍵成分和夾雜物及其控制
? 氧對軸承鋼質(zhì)量的影響及其控制
? 軸承鋼中的夾雜物及其控制
? 軸承鋼中殘余鋁的控制
? 軸承鋼中殘余鈦的控制
? 硫含量
? 鋼中碳化物缺陷
1 氧對軸承鋼質(zhì)量的影響及其控制
鋼中wT.O=10×10-4%軸承鋼的疲勞壽命比wT.O=40×10-4%提高10倍。wT.O=5×10-4%的疲勞壽命比wT.O=40×10-4%提高30倍。軸承鋼生產(chǎn)的關(guān)鍵在于脫氧。
冶煉過程中應(yīng)注意的問題
? 初煉鋼液實現(xiàn)低氧化和低溫化;
? 強(qiáng)化初煉鋼水的預(yù)脫氧;
? 采用SiC和Al粉進(jìn)行擴(kuò)散脫氧;
? 精煉中期,鋼中氧含量降低,Al也隨之降低,采用喂Al線的方法添加Al;
? 選擇合適的精煉渣系;
? 防止二次氧化;
? 合理的吹氬制度;
? 控制適當(dāng)?shù)臍堜X量;
? 確保足夠的真空度和真空時間。
2 軸承鋼中的夾雜物及其控制
? 鋼中非金屬夾雜物數(shù)量和組分的變化
? 鋼中硫化物夾雜對軸承鋼質(zhì)量的影響
? 工藝參數(shù)對鋼中夾雜物含量的影響
? 澆注過程中夾雜物的控制
鋼中非金屬夾雜物數(shù)量和組分的變化
? 鋼中大于5μm的夾雜物在真空后大部分被去除。夾雜物數(shù)量比真空前少1/3;
? SKF研究發(fā)現(xiàn):出鋼后15min夾雜主要由Al2O3和Al2O3?SiO2?MnO組成,來自電弧爐出鋼的預(yù)脫氧產(chǎn)物;真空前——Al2O3?CaO夾雜,是Al2O3和鐵合金Ca-Si中的鈣的反應(yīng)產(chǎn)物;真空后——夾雜中的Al2O3?CaO往往包著一層MgS,Mg來自真空下的耐材,并與Al2O3生成Al2O3?MgO。
鋼中硫化物夾雜對軸承鋼質(zhì)量的影響
? 有益
? 有害
? 對鋼的疲勞壽命影響不大
工藝參數(shù)對鋼中夾雜物含量的影響
? 電爐出鋼溫度
? 攪拌時間
? 鋁脫氧工藝
Ascometal公司認(rèn)為,對于軸承鋼的精煉,應(yīng)把重點放在:選擇堿性耐材鋼包內(nèi)襯;最大限度地去除爐渣;盡早形成非常低氧勢的脫氧精煉渣;控制氣體攪拌,使夾雜物上浮。
澆注過程中夾雜物的控制
? 模鑄——重點放在避免鋼包和錠模之間鋼水流的二次氧化;最大限度地避免鋼水和耐材的作用;最大限度地避免鋼包渣、保溫劑或澆注保溫渣的卷入;
? 連鑄——檢測鋼包中的下渣量;吹氬保護(hù),防二次氧化;選用優(yōu)質(zhì)的耐材。
3 軸承鋼中殘余鋁的控制
? 金屬鋁及AlN溶于酸,用[Al]S表示。終脫氧用Al是獲得低氧含量的鋼液和保證鋼中有合適[Al]S。[Al]S高——保護(hù)條件不好易二次氧化增加Al2O3夾雜;[Al]S低——Si的二次氧化及鋼液隨溫度降低溶解氧析出,產(chǎn)生含SiO2很高的粗大玻璃質(zhì)硅酸鹽夾雜。如果要使鋼材晶粒細(xì)化,獲得高強(qiáng)韌性,殘余鋁可高些。對滲碳軸承鋼來說,殘余鋁需要控制得高些;對于高碳軸承鋼對此控制要求不太高。
4 軸承鋼中殘余鈦的控制
? 鈦對于高碳鉻軸承鋼有害,在鋼中以Ti(C,N)、TiC、TiN存在呈堅硬的菱角。在相同尺寸下,危害大于Al2O3;
? 實踐證明,wTi超過50×10-4%,軸承疲勞壽命明顯下降。電弧爐生產(chǎn)中,N高——更嚴(yán)格控制殘Ti;
? 國外SKF3標(biāo)準(zhǔn)規(guī)定wTi≤0.003%;
? 大生產(chǎn)軸承鋼鈦含量不高于50×10-4%,對疲勞壽命幾乎無影響,高于此值,TiN與氧化物作用,或簇狀TiN本身之間的作用,導(dǎo)致顯微裂紋發(fā)生率增加,惡化疲勞強(qiáng)度;
? 日本高周波公司開發(fā)低鈦為特色的SUJ2KRF鋼wTi≤18×10-4%,壽命比普通軸承鋼提高2倍;
? 日本住友公司對不同鈦和氧含量的鋼管試驗證明,低氧和低鈦有利于軸承使用壽命的提高。
5 硫含量
? 許多人認(rèn)為硫含量不會影響軸承壽命,甚至能減輕氧化物的有害作用。但隨著純凈鋼的提高,氧化物夾雜含量減少,硫化物的有害作用逐漸表現(xiàn)出來
? 日本一家著名微型軸承企業(yè)要求硫含量不高于0.003%
? 瑞典SKF——0.015%
? 寶鋼——0.008%
6 鋼中碳化物缺陷
? 碳化物缺陷包括液析碳化物、帶狀碳化物和網(wǎng)狀碳化物,其危害相當(dāng)于夾雜物;
? 碳化物缺陷主要起源于鋼在凝固過程中的偏析,控制和減少凝固偏析是控制和減少碳化物缺陷的關(guān)鍵環(huán)節(jié);
? 采用合理的加熱、軋制和熱處理工藝可進(jìn)一步改善碳化物結(jié)構(gòu)和形態(tài),減輕其危害。
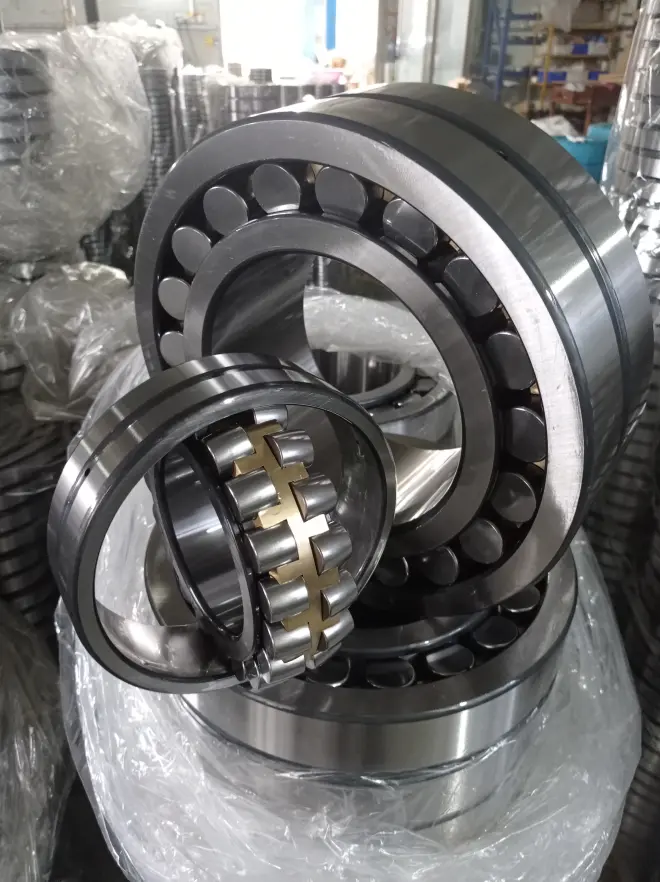
編輯
軸承外觀的質(zhì)量要求
1、軸承零件不允許有裂紋、銳邊、毛刺和銹蝕;滾道不允許有上道工序加工痕跡;內(nèi)外圈、鋼球工作面超精紋路應(yīng)均勻一致,不允許有擦傷、碰傷;
2、軸承零件配合表面磨削紋路應(yīng)規(guī)則一致,不允許有螺旋紋、振紋、陰陽臉及打磨痕跡,不允許出現(xiàn)支承印及明顯的測量痕跡,不允許有磕碰傷和明顯色澤差異。
3、零件表面不允許有氧化皮。套圈倒角、內(nèi)外徑、外內(nèi)徑要求亮化處理。
4、軸承套圈零件經(jīng)酸洗后,工作表面不應(yīng)有燒傷,配合表面不應(yīng)有未經(jīng)酸洗可見的燒傷痕跡且不影響硬度檢測。
5、裝配倒角。
a.裝配倒角尺寸、倒角形狀應(yīng)符合我方產(chǎn)品圖紙規(guī)定。
b.倒角表面無銹蝕和磕碰傷。
6、鋼球
鋼球外觀質(zhì)量標(biāo)準(zhǔn)應(yīng)符合JB/T10861 標(biāo)準(zhǔn)要求。
7、保持架
外觀表面應(yīng)平整、光滑、無毛刺、無碰傷、無銹蝕和明顯色差,不允許有壓傷、挫傷、變形及砂眼等外觀缺陷。
(運(yùn)轉(zhuǎn)世界大國龍騰 龍出東方 騰達(dá)天下 龍騰三類調(diào)心滾子軸承 劉興邦CA CC E MB MA)
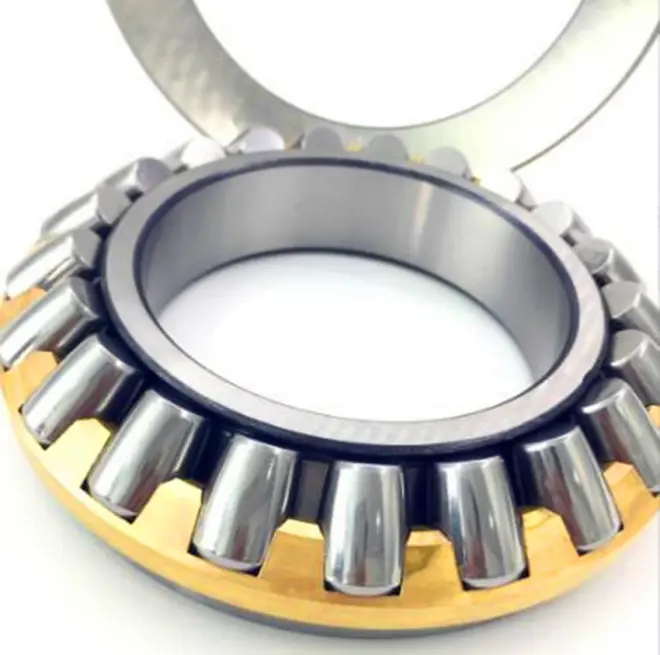
編輯
磨削加工質(zhì)量分析和判斷
1. 寬度尺寸偏差在大
由于寬度尺寸偏差超出工藝要求應(yīng)判為廢品(在實際生產(chǎn)中寬度尺寸過小,只得報廢,寬度尺寸大,可進(jìn)行返修加工成合格品)。造成廢品的原因,主要是操作不當(dāng),如儀表沒對好,跑表,進(jìn)刀量太大或進(jìn)刀太猛等,這都會產(chǎn)生本工序廢品。另一種情況是操作工按工藝要求磨非基準(zhǔn)端面,然后又按工藝要求磨完基準(zhǔn)端面后,套圈已到了工藝要求尺寸,但端面仍有:“黑皮”存在,這應(yīng)判為廢品。這廢品屬于上工序廢品。
寬度尺寸偏差大對下工序磨加工溝道產(chǎn)生位置偏差和影響軸承成品高度。
2. 寬度變動量大
寬度變動量超過了工藝要求應(yīng)判為廢品。造成本工序產(chǎn)生廢品原因有砂輪主軸與擋圈不垂直,工件不清潔或有毛刺等都會造成寬度變動量大。
寬度變動量超差對下工序有一定影響,如磨削外徑時,外徑表面母線對基準(zhǔn)端面傾斜度的變動量產(chǎn)生誤差。磨削溝道時,溝道對基準(zhǔn)端面的平行度產(chǎn)生誤差。
3. 單一外(內(nèi))徑偏差大
由于 外徑偏差超過了工藝要求應(yīng)判為廢品。造成本工序廢品原因有“合溫”沒掌握好,磨削深度過大,砂輪已磨損或修整不好,操作或調(diào)整失誤等等。外(內(nèi))徑偏差大直接影響軸承與主機(jī)(機(jī)械設(shè)備)的配合,磨削溝道時影響“R”形狀。
4. 單一徑向平面外徑變動量大
由于此項超出工藝要求應(yīng)判為廢品。其產(chǎn)生原因有導(dǎo)輪沒修圓,導(dǎo)輪徑向擺過大,工件中心低于導(dǎo)輪中心,砂輪磨鈍,砂輪軸振擺,毛坯橢圓過大,縱向進(jìn)給太快等。
本工序的廢品對下工序有影響,在磨削溝道時產(chǎn)生溝道直徑變動量超差,影響溝道圓度誤差等。
5. 圓度誤差過大
圓度誤差超過了工藝要求應(yīng)判為廢品,產(chǎn)生廢品原因有工件中心過低或過高(過低或過高產(chǎn)生棱圓面),毛壞圓度誤差,砂輪推動過大,貫穿磨削次數(shù)小,導(dǎo)輪旋轉(zhuǎn)速度不合適,磨削淡化度過大和縱向進(jìn)給過快,托板太薄或已磨損。
圓度誤差大對下工序加工有影響,在磨削溝道時,影響溝道圓度誤差,單一徑向平面內(nèi)溝道直徑變動量等。
6. 外圓表面母線對基準(zhǔn)端面傾斜度變動量大
該誤差超過了工藝要求后應(yīng)判為廢品,產(chǎn)生廢品原因有毛坯本身誤差大、磨削“火花”調(diào)整得不好而造成工件“離縫”、縱向送料不均勻、工件端面有碰傷或端面過窄、磨削深度過大或貫穿磨削次數(shù)過小等。
本工序廢品對下工序加工有影響,在磨削溝道時影響外圈溝道對端面的平行度,溝道圓度誤差,單一徑向平面內(nèi)溝道直徑變動量等。
7. 內(nèi)圈基準(zhǔn)端面對內(nèi)孔的跳動大
由于該誤差超過了工藝要求應(yīng)判為廢品。廢品產(chǎn)生的原因有主軸旋轉(zhuǎn)精度低,工件端面有碰傷或污物,毛坯本身有誤差,無心夾具的磁力不足,無心夾具調(diào)整不當(dāng)?shù)取?/p>
本工序產(chǎn)生的廢品對下工序的溝道磨削會產(chǎn)生溝道對端面平行度誤差、以及會產(chǎn)生單一徑向平面內(nèi)溝道直徑變動量誤差等。
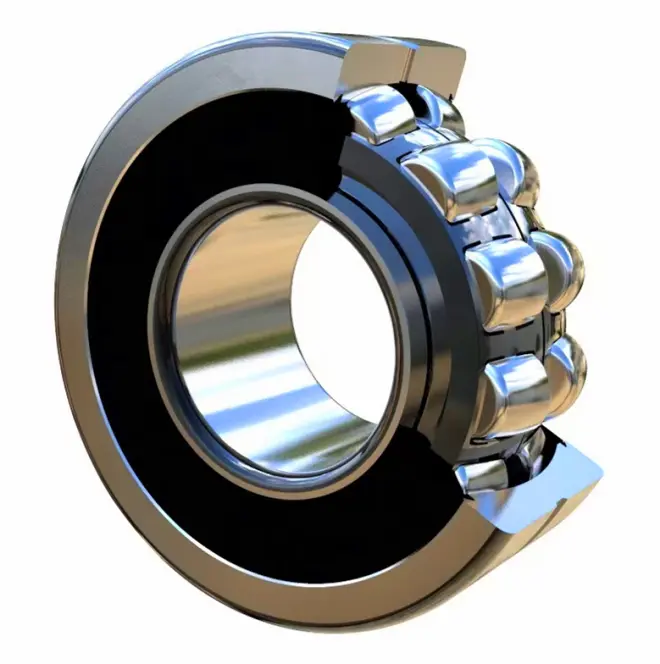
編輯
軸承裝配后質(zhì)量分析與判斷
一.?尺寸精度超差
內(nèi)徑、外徑尺寸在成品檢查中有超差可能,主要原因:
1.?前工序的產(chǎn)品漏檢。
2.?裝配檢查環(huán)境溫差變化大。
3.標(biāo)準(zhǔn)件與套圈恒溫不夠。
4.磨加工與成品檢查使用標(biāo)準(zhǔn)件不合格。
軸承內(nèi)徑尺寸過大,應(yīng)判為不合格產(chǎn)品,內(nèi)圈報廢。內(nèi)徑尺寸過小,應(yīng)判為不合格產(chǎn)品,但可以返工修磨,使其成為合格品。軸承外徑尺寸過大,可通過重新修磨,使其成為合格。但外徑尺寸過小,應(yīng)判為不合格軸承,外圈報廢。
二.?? 旋轉(zhuǎn)精度超差
產(chǎn)生旋轉(zhuǎn)精度超差的原因有:
1.?套圈在磨加工時,溝道中心平面對基準(zhǔn)端面平等度已超差。
2.?內(nèi)外溝道表面有傷、有臟物。
3.?內(nèi)外套圈基準(zhǔn)面有傷。
4.?內(nèi)外溝道直徑變動量較大。
5.?裝最后一球時,會使外圈變形,或使鋼球表面卡傷。
6.?可能裝有混球,鋼球直徑差過大。
7.?保持架變形。
8.?溝形狀變形。
Kia和Kea超差而報廢較少,即使有是由于單個套圈的溝道對內(nèi)徑或外徑厚
度變動量超差。但是Sia和Sea超差而報廢較多。為了減少損失,往往通過拆零件重新組合裝配可得到一定改善。Sd和SD超差只能報廢。
三.?? 軸承靈活性不好
軸承靈活性不好,其主要原因有:
1.?鉚合時軸承內(nèi)部進(jìn)入污物。
2.?鉚合時壓力太重,使保持架變形。
3.?模具受力不均,使保持架受壓不均,產(chǎn)生變形。
4.?鉚釘直徑超差,長度超差,使鉚合時,同一保持架鉚釘變形量不等,使保持架變形。
5.?保持架球窩尺寸超差,使鋼球轉(zhuǎn)動無足夠的徑向間隙。
6.?合套時徑向游隙太小。
7.?個別出現(xiàn)混入大球,不能轉(zhuǎn)動等。
四.?? 徑向游隙超差
??? 按徑向游隙要求進(jìn)行合套,出現(xiàn)徑向游隙超差,主要原因有:
1.?套圈尺寸分選的數(shù)值不準(zhǔn)確,由于分選中的偶然誤差,測量系統(tǒng)誤差等造成。
2.?套圈尺寸分選的數(shù)值不準(zhǔn)確,由于分選中的偶然誤差,測量系統(tǒng)誤差等造成。
3.?套圈溝道曲率半徑超差。
4.?測量軸向游隙、鋼球等分不均、位置不正確、手推力不一致。
5.?軸承清潔度不夠。
6.?套圈溝道幾何尺寸偏差過大。
7.?保持架中心圓超差過大。
游隙過大和過小均為不合格產(chǎn)品。但可以返工,重新配套來達(dá)到合格的游
五.軸承銹蝕
軸承銹蝕為外觀質(zhì)量不合格。其產(chǎn)生原因是軸承零件保存不當(dāng)產(chǎn)生銹蝕;裝配過程中防銹工藝執(zhí)行不嚴(yán);特別是梅雨季節(jié)操作者不帶手套作業(yè);裝配作業(yè)間空氣相對濕度過大;清潔度較差等。
??? 產(chǎn)生銹蝕的產(chǎn)品可進(jìn)行擦銹處理,使其成合格品。銹蝕太大只得報廢或降低精度等級。
附表二
測量軸承Kia?和Sia時施加的中心軸向載荷
軸承公稱內(nèi)徑??d(mm)
載荷 (N)
超過
到
最小
3
6
2
6
10
3
10
30
10
30
50
20
50
80
25
80
100
25
?
?
附表三
測量軸承Kea?和Sea時施加的中心軸向載荷
軸承公稱外徑?D(mm)
載荷(N)
超過
到
最小
6
10
3
10
18
5
18
30
10
30
50
15
50
—
20
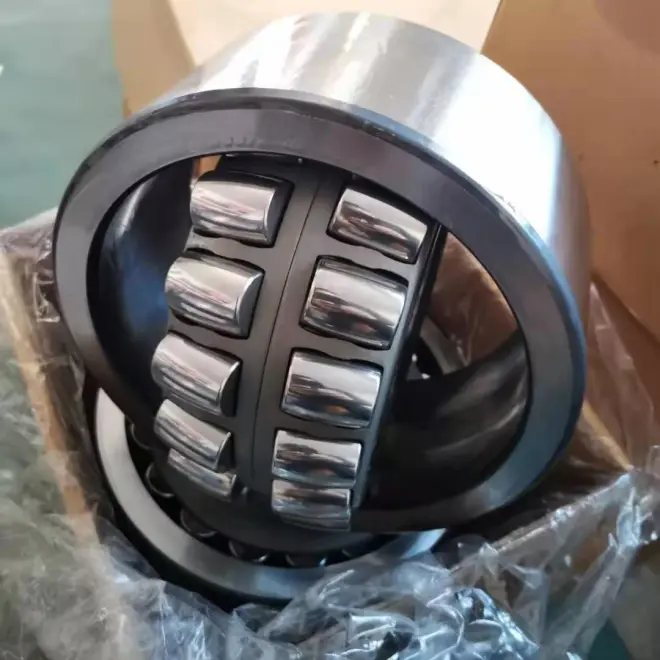
編輯