inconel600鎳鉻鐵鎳基合金成分性能
產(chǎn)品簡介
inconel600簡介:
inconel600合金是鎳-鉻-鐵基固溶強(qiáng)化合金,inconel600具有良好的耐高溫腐蝕和抗氧化性能、優(yōu)良的冷熱加工和焊接工藝性能,inconel600在700℃以下具有滿意的熱強(qiáng)性和高的塑性。inconel600合金可以通過冷加工得到強(qiáng)化,也可以用電阻焊、熔焊或釬焊連接。
Inconel 600國內(nèi)外對(duì)應(yīng)牌號(hào):
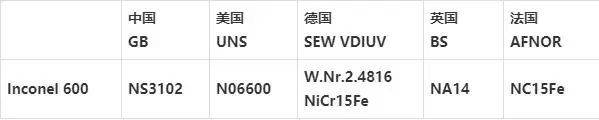
Inconel 600化學(xué)成分:

Inconel 600物理性能:
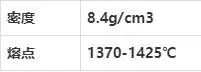
Inconel 600在常溫下合金的機(jī)械性能的MIX:
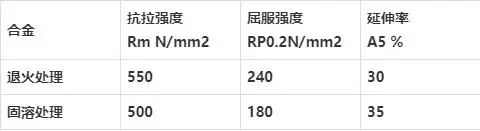
Inconel600力學(xué)性能(室溫)
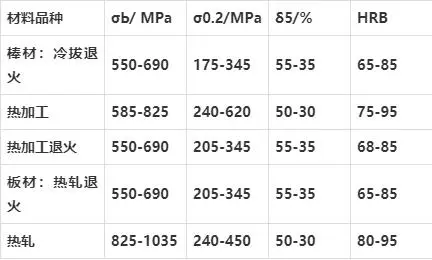
Inconel 600具有以下特性:
1. 具有很好的耐還原、氧化、氮化介質(zhì)腐蝕的性能
2. 在室溫及高溫時(shí)都具有很好的耐應(yīng)力腐蝕開裂性能
3. 具有很好的耐干燥氯氣和氯化氫氣體腐蝕的性能
4. 在零下、室溫及高溫時(shí)都具有很好的機(jī)械性能
5. 具有很好的抗蠕變斷裂強(qiáng)度,推薦用在700℃以上的工作環(huán)境。
Inconel 600應(yīng)用范圍應(yīng)用領(lǐng)域有:
1.侵蝕氣氛中的熱電偶套管
2.氯乙烯單體生產(chǎn):抗氯氣、氯化氫、氧化和碳化腐蝕
3.鈾氧化轉(zhuǎn)換為六氟化物:抗氟化氫腐蝕
4.腐蝕性堿金屬的生產(chǎn)和使用領(lǐng)域,特別是使用硫化物的環(huán)境
5.用氯氣法制二氧化鈦
6.有機(jī)或無機(jī)氯化物和氟化物的生產(chǎn):7.核反應(yīng)堆
8.熱處理爐中曲頸瓶及部件,尤其是在碳化和氮化氣氛中
9.石油化工生產(chǎn)中的催化再生器在700℃以上的應(yīng)用中推薦使用合金600以獲得較長的使用壽命。
1?前言?
寧夏某化肥廠采用天然氣通過爐內(nèi)高壓注氧產(chǎn)生?CO、CO2和?H2,為尿素裝置制造原料。輸氧管道為?Inconel600?高合金材?料。Inconel600?鋼無磁性且焊接性較好,但工藝不當(dāng),易在焊接?熱影響區(qū)(包括多層焊的前一道焊縫熱影響區(qū))產(chǎn)生熱裂紋,焊?縫返修表現(xiàn)的尤為突出。細(xì)小且無方向的裂紋需采取熒光劑滲?透措施顯示,部分裂紋會(huì)隨焊接應(yīng)力擴(kuò)展成可目測的粗大裂紋。
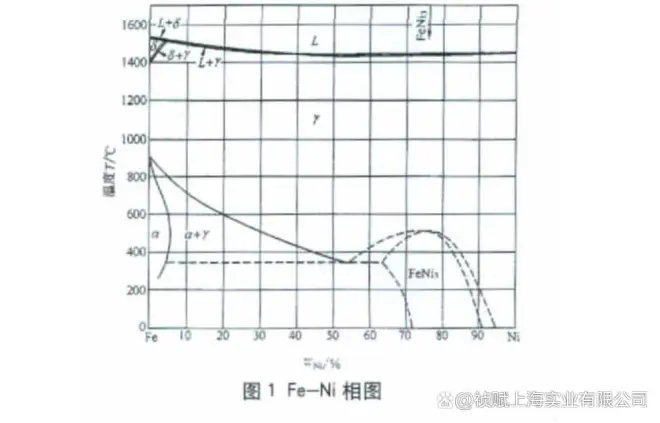
2?材料焊接冶金和力學(xué)因素分析
Inconel600?鋼為鎳合金耐高溫材料(美國牌號(hào)),主要應(yīng)用?于抗腐蝕領(lǐng)域。高鎳含量使材料在腐蝕環(huán)境和氯化物腐蝕裂變?中具有特別的耐受性,合金中的鉻增加材料在弱氧化環(huán)境下的?抗腐蝕特性。材料化學(xué)成份及力學(xué)性能詳見表?1[1]。

Inconel600?鋼焊接熱裂紋主要是由材料冶金因素和力學(xué)因?素相互作用形成的: (1)?鎳含量高,材料一次結(jié)晶并保持至室溫的組織為奧氏?體,易形成方向性強(qiáng)的柱狀晶和樹枝狀晶,促使?S,P?等有害雜質(zhì)?偏析或因溶解度下降而形成低熔共晶物;
(2)?材料熱導(dǎo)率小、熱膨脹系數(shù)大,焊接局部加熱和冷卻條?件下,材料塑性儲(chǔ)備及收縮產(chǎn)生的拉應(yīng)力隨著溫度的下降而變?化,存在的低熔點(diǎn)相減少了塑性儲(chǔ)備量,促使熱裂紋產(chǎn)生。
2. 1?一次結(jié)晶組織對(duì)焊縫金屬熱裂行為的影響
Inconel600?鋼中?Ni?元素含量高達(dá)?72%。Ni?是強(qiáng)奧氏體形成?元素(γ?相),鐵?-?鎳相圖中(圖?1)和鐵?-?鉻?-?鎳三元相圖(圖2)中,可以看出合金由液相凝固后直接形成γ?奧氏體組織并保?持至室溫[2]。
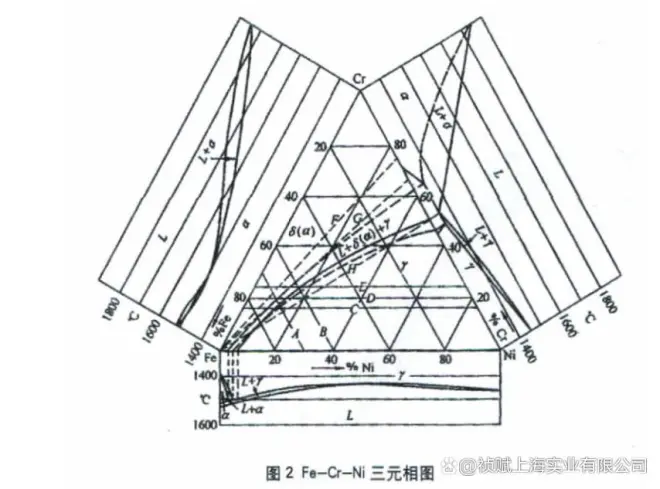
焊接熱循環(huán)作用下,焊縫和熱影響區(qū)金屬發(fā)生再結(jié)晶現(xiàn)象(多層焊使再結(jié)晶現(xiàn)象加強(qiáng))。奧氏體組織再結(jié)晶過程中不發(fā)生相變所以無法細(xì)化,且偏析方向的一致性,使新晶粒邊界易富集低熔點(diǎn)相。由于焊縫金屬具有良好的抗熱裂性,所以裂紋易出現(xiàn)在母材熱影響區(qū)或多層焊前一道焊縫的熱影響區(qū)內(nèi)。?
2. 2?合金元素和雜質(zhì)的影響
合金元素對(duì)金屬材料的組織、性能產(chǎn)生影響。Cr?是強(qiáng)碳化物形成元素,主要提高鋼的高溫強(qiáng)度和耐蝕性;Ni?是強(qiáng)奧氏體形成元素,提高抗電化學(xué)腐蝕的效果,但?γ?相易形成偏析;C?有強(qiáng)的奧氏體化作用,易與?Cr?形成?M23C6?混合碳化物,?但固態(tài)奧氏體對(duì)碳的溶解度急劇下降,易產(chǎn)生晶間腐蝕;Mn?是奧氏體形成元素,Mn?與?S?易形成熔點(diǎn)為?1580℃的硫化錳共晶物;S?是雜質(zhì)元素,硫以?FeS?的形態(tài)存在于鋼中。FeS?與?Fe?可在奧氏體晶界上形成低熔點(diǎn)(985℃)的共晶體,鋼加熱到約?1200℃時(shí),晶粒間結(jié)合被破壞[3]。
增加熱裂敏感性的主要元素是?S、P、B、Nb、Si?和?Ti。通常情況下,奧氏體對(duì)這些元素的溶解度比鐵素體低,材料含鎳更高時(shí),溶解度會(huì)進(jìn)一步減少。
2. 3?偏析的影響
多元合金的結(jié)晶是在一個(gè)溫度范圍,合金凝固后會(huì)形成成分不平衡的不穩(wěn)定狀態(tài),試圖通過擴(kuò)散變?yōu)槠胶鈶B(tài)。一次結(jié)晶為
γ?相的區(qū)域會(huì)產(chǎn)生較大的偏析傾向,很多元素在奧氏體中的擴(kuò)散能力相當(dāng)差,析出相難于通過擴(kuò)散而達(dá)到均勻化,即使元素含量很低,低熔點(diǎn)相也可以發(fā)生析出。S、P?元素在奧氏體中的溶解
度小,并且由于偏析使溶解度進(jìn)一步減小,這種現(xiàn)象使剩余溶液中的有害元素的不利作用加劇。
2. 4?焊接工藝的影響
高溫合金焊后,過熱區(qū)有顯著的晶粒粗化現(xiàn)象,且焊接接頭具有較大的拘束應(yīng)力,使粗晶部位液化裂紋傾向增加。故焊接工藝盡可能選用能量集中和小線能量。
TIG?是較好的焊接方法,具有焊接熱量集中、熔池小、焊速快、熱影響區(qū)小和焊縫金屬純凈的優(yōu)點(diǎn),能夠獲得優(yōu)質(zhì)焊縫并降低結(jié)晶粗大的傾向。
2. 5?結(jié)構(gòu)設(shè)計(jì)的影響
焊接過程,熱影響區(qū)由初期承受壓應(yīng)力轉(zhuǎn)變?yōu)槔瓚?yīng)力,轉(zhuǎn)折點(diǎn)的時(shí)間和溫度對(duì)液化裂紋的產(chǎn)生起決定作用。如果在轉(zhuǎn)折點(diǎn)時(shí),熱影響區(qū)晶界處的低熔點(diǎn)物質(zhì)仍然以液相存在,晶界處液態(tài)薄膜就會(huì)擴(kuò)展,形成熱裂紋。
若轉(zhuǎn)折點(diǎn)溫度較低,低熔點(diǎn)液相已經(jīng)凝固,結(jié)晶組織不會(huì)被液態(tài)薄膜分割,也就不會(huì)擴(kuò)展為熱裂紋。厚件焊接冷卻速度快,低熔點(diǎn)相更容易被排擠到晶粒邊界,同時(shí),應(yīng)力轉(zhuǎn)折點(diǎn)的溫度很高,焊縫和熱影響區(qū)在高溫時(shí)更早地承受拉應(yīng)力,
從而增加熱裂紋的傾向。
3?焊接工藝措施
通過對(duì)?Inconel600?鋼材料冶金和力學(xué)因素的分析,我們可以看出,降低?γ?奧氏體相焊縫金屬再結(jié)晶傾向、成分偏析及焊接應(yīng)力,是預(yù)防焊接液化裂紋的有效措施。
3. 1?焊接方法選擇
為了獲得高質(zhì)量的焊接接頭,選用了能量集中的?TIG?焊。
3. 2?焊接材料
確保焊接接頭的高溫強(qiáng)度,焊材力求與母材合金成分相當(dāng),以保證焊材與母材有同一熔點(diǎn)、同一結(jié)晶溫度、同一熱脹(收縮)率等;同時(shí),考慮到合金元素過渡期間的燒損,選擇?ERNiCr - 3
焊絲[1],?材料化學(xué)成分見表?2。
3. 3?焊接設(shè)備
采用直流脈沖手工鎢極氬弧焊機(jī),具有高頻起弧、提前送氣、延時(shí)斷氣等功能,滿足施工要求。
3. 4?坡口加工及組對(duì)
構(gòu)件的坡口寬高比保持在?1. 5:1~2:1?之間,減少熔合比。
錯(cuò)邊量嚴(yán)格控制在?0. 5mm?以內(nèi),且嚴(yán)禁強(qiáng)力組對(duì)。
3. 5?坡口及焊材的清理
工件(焊絲)表面的污物(比如水、銹、油污、油漆等)會(huì)影響焊接接頭性能,高溫合金的表面常存在難熔氧化膜——NiO(熔點(diǎn)為?2090℃),易在焊縫中形成夾雜物。污物的清洗可采用丙酮

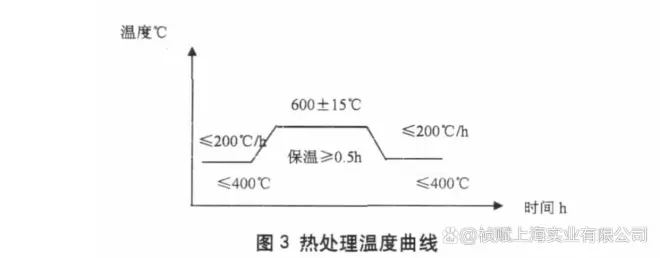
(2) 地線應(yīng)于焊件接觸牢固,焊接時(shí)在坡口內(nèi)引弧,焊件表面不得有電弧擦傷等缺陷。
(3) 焊接時(shí)應(yīng)嚴(yán)格控制接線能量,在保證焊透及熔合良好的條件下,應(yīng)選用小工藝規(guī)范,即小電流、短電弧、較快焊接速度和多層多道焊,層間溫度不應(yīng)超過?200℃。
(4) 每道焊縫要盡量一次焊完,如因故中斷應(yīng)按工藝要求進(jìn)行緩冷措施,重新焊接時(shí)應(yīng)進(jìn)行檢查,確認(rèn)無缺陷后方可按原工藝焊接。
(5) 焊接收弧時(shí)應(yīng)將弧坑填滿,并用砂輪磨去弧坑缺陷。多層焊時(shí)層間接頭應(yīng)錯(cuò)開?30~50mm。
(6) 焊接時(shí)選用焊條直徑不宜過大,焊接初層焊道焊條直徑一般不超過?3. 2mm,填充和蓋面直徑一般不超過?4mm。
(7) 卡具、臨時(shí)支架與母材接觸部分材質(zhì)應(yīng)和母材相同或相近,夾具拆除應(yīng)用砂輪磨除,嚴(yán)禁敲打。
(8) 管道采用鎢極氬弧焊打底手工電弧焊蓋面。鎢極氬弧焊打底時(shí)應(yīng)在管內(nèi)充氬保護(hù)。
(9) 為防止線能量超標(biāo),使焊工便于掌握,規(guī)定?φ3. 2?焊條 , 每 根 焊 接 長 度 應(yīng)?> 150mm,φ4?焊 條 每 根 焊 接 長 度 應(yīng)
> 220mm,每層焊縫每次焊接的厚度應(yīng)≤3mm。
(10) 焊縫背面清根可采用碳弧氣刨,但必須用砂輪唐出金屬光澤,清根后坡口要寬窄一致,盡量呈?U?形,杜絕出現(xiàn)窄而深的不良狀況;焊縫背面清根后,應(yīng)進(jìn)行?PT?檢查,當(dāng)確認(rèn)無缺陷時(shí)再進(jìn)行焊接。
8?小結(jié)
在近幾年的施工中?3. 5Ni?鋼的焊接,由于焊接工藝合理、管理措施得當(dāng),焊接質(zhì)量較高,焊接探傷一次合格率達(dá)?98. 6%以上。通過產(chǎn)品試板試管的檢驗(yàn),焊縫低溫韌性(低溫沖擊值)與母材相近,得到了用戶和監(jiān)理部門的一致好評(píng)?,F(xiàn)將幾點(diǎn)特殊的管理措施總結(jié)以下:
(1) 為防止線能量超標(biāo),記錄員應(yīng)詳細(xì)測定、記錄焊接電流、電壓、焊接速度(每人、每道焊縫每層檢測?1~2?點(diǎn)),并及時(shí)計(jì)算出焊接線能量,發(fā)現(xiàn)接近上限時(shí)及時(shí)通知焊工調(diào)整。
(2) 焊接施工中規(guī)定?φ3. 2?焊條,每根焊接長度應(yīng)大于
150mm,φ4?焊條每根焊接長度應(yīng)大于?220mm,量化了焊接線能量,使焊工便于掌握,是控制焊接線能量行之有效的措施。
(3) 設(shè)備和厚壁管道焊縫完成后,最好在焊縫熔合區(qū)焊接一道?ACI?整容焊道,以消除咬邊和改善熔合區(qū)韌性,如圖?4?所示。
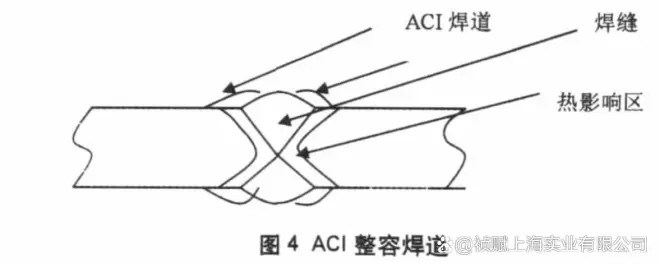
3. 6?焊接參數(shù)
焊接采用小線能量,減少晶粒粗大形成的偏析及熱裂傾向。
電弧長度盡可能短,易于控制熔透和窄焊道。構(gòu)件背部充氬保護(hù),防止根部焊縫氧化。
3. 7?焊縫檢查
焊接引弧、收弧處的打磨工作很重要,可消除存在的微裂紋。條件許可的情況下,對(duì)坡口、打底層、蓋面層焊縫進(jìn)行?100%
滲透檢查,確保焊接接頭表面的缺陷全部清除。
3. 8?層間溫度
焊接層間溫度嚴(yán)格限制在?100℃,降低焊件總的熱輸入可減少熱裂敏感性。
3. 9?結(jié)構(gòu)設(shè)計(jì)
材料的厚度和剛度都對(duì)熱裂紋的形成有重要影響,應(yīng)避免坡口及材料厚度的急劇變化而產(chǎn)生的焊接應(yīng)力增加熱裂傾向。
3. 10?焊縫返修
提高焊接一次合格率,避免焊接缺陷,減少返修。焊后對(duì)缺陷的修補(bǔ)會(huì)引起新的裂紋,如果需要清除缺陷應(yīng)盡量減小開口面積,降低熱裂傾向。
3. 11?人員因素。
焊接應(yīng)由有奧氏體鋼焊接經(jīng)驗(yàn)的且受過良好培訓(xùn)的焊工完成,對(duì)作業(yè)流程的了解和熟悉,有利于工藝紀(jì)律的執(zhí)行。監(jiān)督和控制人員也必須有相關(guān)的專業(yè)知識(shí)。
4?結(jié)論
焊接實(shí)踐證明,通過合理的工藝措施和嚴(yán)格的過程控制,可有效地防止焊接液化裂紋的產(chǎn)生,能獲得良好質(zhì)量效果和經(jīng)濟(jì)效益。