3J53彈簧表面裂紋缺陷原因分析
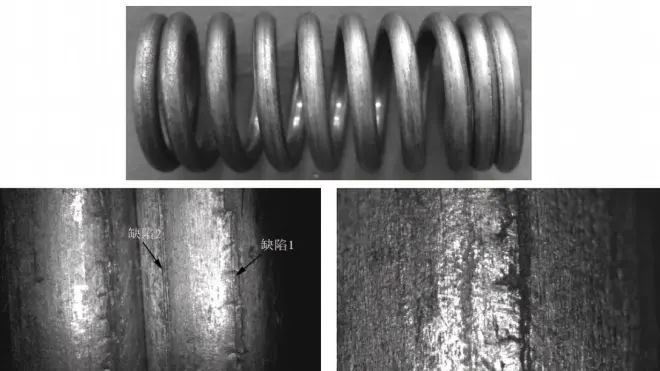
文摘:3J53鋼絲在車間纏繞成彈簧并經熱處理后發(fā)現其表面存在線性缺陷。用掃描電鏡對鋼絲線性缺陷的形貌進行了分析,對線性缺陷區(qū)域進行了能譜分析,并利用金相顯微鏡觀察了線性缺陷的中心部位及其周圍區(qū)域的金相組織。結果表明:鋼絲表面的線性缺陷呈鋸齒狀,沿鋼絲軸向方向,為裂紋型折疊缺陷。折疊缺陷是鋼絲在生產過程中形成,在繞簧和熱處理過程中,裂紋型折疊缺陷發(fā)生擴展和延伸,最終形成線性缺陷。
關鍵詞:3J53,鋼絲,折疊
?
0、引言
彈性合金是金屬功能材料中的一個重要部分,按性能特點,彈性合金可分為高彈性合金和恒彈性合金,3J53屬于恒彈性合金,在一定的溫度范圍(如-60~+100℃)內,其E或G以及可制得元件的共振頻率基本不隨溫度而變化,因此廣泛應用于儀器、儀表、通訊、計量等領域。此合金鋼絲經冷拔(軋)+失效處理后強度較高,具有無磁和耐蝕性,是制造彈簧的良好材料。
彈簧是不可缺少的重要零件,在絕大多數情況下起著控制零部件運動的作用。彈簧在使用過程中常因各種原因導致失效而引起機械故障。導致彈簧失效的因素主要有材料缺陷、加工制造缺陷、熱處理不當、工作環(huán)境等。
直徑為5mm的3J53鋼絲纏繞成彈簧并經熱處理后出現表面裂紋缺陷,本文對缺陷原因進行研究分析,并提出有效的改進措施。
?
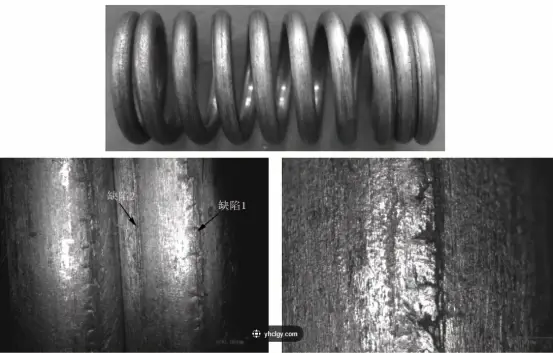
1實驗
由3J53鋼絲纏繞的彈簧熱處理后發(fā)現彈簧表面存在兩條線性似裂紋缺陷。
為確定“裂紋”的性質及成因,采用體式顯微鏡VHX-1000E進行宏觀形貌觀察,并將彈簧缺陷部位置于型號為QuantaFEG650掃描電鏡下進行微觀形貌觀察和能譜分析,從彈簧缺陷部位取樣并制備成金相試樣置于光學顯微鏡下觀察其形貌和組織,顯微鏡型號DM4000M。
?
2實驗結果
2.1宏觀形貌
由鋼絲纏繞的彈簧熱處理后發(fā)現彈簧表面存在兩條平行且連續(xù)分布的線性缺陷,并伴有起皮現象,未見明顯的機械損傷和腐蝕痕跡。宏觀形貌如圖1所示。
?
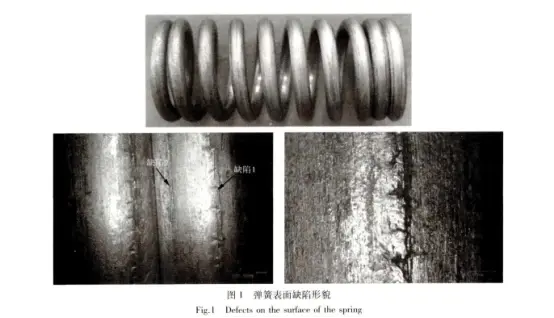
2.2微觀形貌
將彈簧置于描電鏡下觀察,缺陷處存在張口,呈現層疊和鋸齒形貌,見圖2。部分域存在剝落,暴露表面呈氧化形貌,見圖3。層疊和鋸齒形貌符合折需的形貌特征,而折疊缺陷往往由于凸出產品表面而在經歷熱工藝成型后常常會伴有明顯的氧化脫象。
?
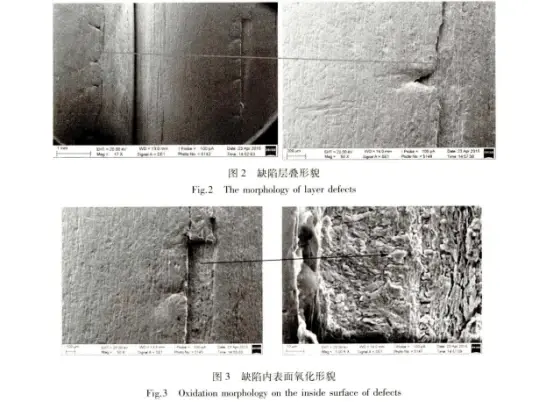
2.3能譜成分分析
主要含有Fe(主)、Ni(40.1%)、Cr(6.4%)、Ti(3.0%)、Si(1.0%)、AI(1.0%)元素,主合金元素及含量與3J53牌號相符,主成分正常,但缺陷內表面除基體元素外還含有較高的O元素,EDS能譜圖見圖4。
?
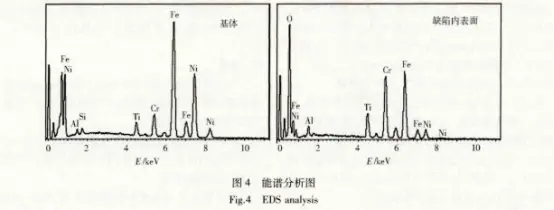
2.4金相分析
從存在缺陷的區(qū)域截取部分試樣進行金相分析,兩處缺陷剖面形態(tài)較為相似:缺陷深度分別約為0.4、0.2mm,存在較多分又微裂紋,缺陷內部存在較多聚集態(tài)顆粒狀氧化物,近表面處缺陷開口較大,氧化物存在脫落,形貌見圖5。顯微組織為正常的奧氏體組織,缺陷附近組織存在變形痕跡,見圖6,說明缺陷在纏繞制成彈簧前已經存在,是鋼絲的本質缺陷,鋼絲纏繞成彈簧后經受力表面缺陷呈現開口形貌。
?
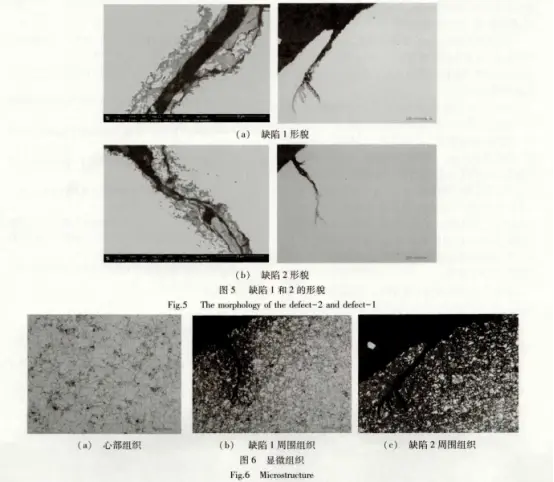
3、分析討論
彈簧所用材料主成分未見異常,缺陷內部含有較高的O元素,呈氧化形貌,缺陷附近未見損傷及腐蝕痕跡。彈簧表面的兩處缺陷均呈鋸齒狀,走向沿鋼絲軸向方向,且在橫斷面上與表面呈20°左右斜交,向內部延伸,并在內部呈現小的Y型微裂現象。
從缺陷形貌特征判定此次失效故障應為折疊,折疊缺陷一般呈直線狀,也有的呈鋸齒狀,分布于鋼材的全長或斷續(xù)狀局部分布,深淺不一,其周圍伴有脫碳現象,一般夾有氧化鐵皮。折疊缺陷通常是由于材料表面在前一道鍛、軋中所產生的尖角或耳子,在隨后的鍛、軋時壓入金屬本身而形成的。
折疊缺陷是熱軋材不可避免的缺陷,主要形成的兩大因素:
(1)?由于鋼坯表面本身存在較嚴重的凹坑、結疤等缺陷,或者鋼坯存在過大的V型修磨痕跡,在上游機架產生了局部的飛邊或耳子,經下游機架多道次軋制后形成了局部折疊,后經拉拔工序形成了似裂紋缺陷,此類折疊一般底部較粗糙。
(2)?在軋制過程中,由于如上游機架來料過大或料型不正,導衛(wèi)導槽安裝不正,有可能使軋件單邊或雙邊充盈,經下游軋機軋制后形成折疊,此類折疊一般底部較圓鈍、光滑。
生產廠家復查,此批鋼絲的生產工藝流程為:熔煉一鍛造方坯一方坯修磨一方坯熱軋盤圓一熱處理一酸洗一盤條修磨一掛潤滑劑(石墨粉)一排摸冷拔一成品表面檢驗一性能取樣檢測一入庫。折疊缺陷應在方坯熱軋盤圓階段產生,如果方坯的表面質量不好(如存在較嚴重的凹坑、凸塊或邊部、角部裂紋等)或者修磨的V形銳度過大都會導致在熱軋階段形成折疊。而本次失效故障呈現出的折疊形貌為底部呈現較多分叉,且缺陷內部夾雜物僅為氧化鐵,因此折疊應是鋼坯表面的缺陷導致的在軋制過程中形成的“裂紋型”折疊。
折疊突出的表面由于氧化的作用,周圍常伴有氧化物夾雜,夾雜物的存在破壞了基體的均勻連續(xù)性,易造成應力集中,往往會成為疲勞裂紋的發(fā)源地,同時它對鋼材的工藝性能也有不利影響,容易引起冷變形時開裂,因此折疊缺陷不允許帶到產品生產中。
4、結論
(1)?彈簧表面裂紋應是由于鋼坯表面缺陷導致在軋制過程產生的折疊缺陷,鋼絲在拉拔后呈現出了沿變形方向的“裂紋”。
(2)?在后期的彈簧纏繞和熱處理工序中,折疊缺陷在剪切力及扭轉力的作用下得以擴展和延伸形成了表面的線性缺陷。
(3)?鋼絲采用石墨粉潤滑的方法,導致表面顏色發(fā)暗,表面缺陷不易被檢出。
5、改進措施
(1)?加強坯料表面缺陷的修磨與檢查,防止修磨深坑及V形角的出現。
(2)鋼絲冷拔時采用油類潤滑劑,形成光亮的表面,以便于進行表面檢查。