徐進的信念:明知精益生產(chǎn)有用,有些服裝企業(yè)為什么遲遲不行動?
現(xiàn)實中,下面的人想搞點改善、推下精益生產(chǎn),就會碰到上級或者老板的不理解,以為那玩意就是搞搞6S、整點目視化給客戶看的,跟我們經(jīng)常說的搞體系應付客戶沒兩樣。講到這里,可能很多朋友都會有同感,這是什么原因造成的?服裝精益智能制造俱樂部分析如下:
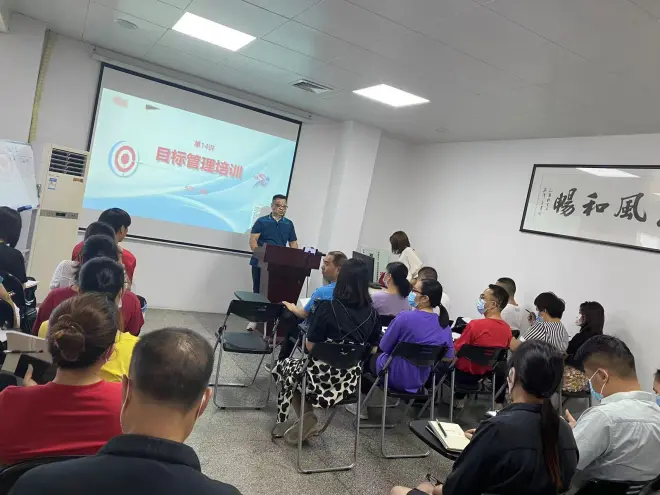
有的服裝企業(yè)目前面臨的競爭相對較小,企業(yè)市場和利潤沒有太大影響。這樣的企業(yè)多數(shù)是因為行業(yè)較小,產(chǎn)品特殊,或者受到某種利益保護,所以他相對與外界隔絕。
這樣企業(yè)的老板,多數(shù)選擇差不多就好,不想讓企業(yè)折騰,不要讓自己辛苦。這是他們的認知,也是人的本性(追求安逸)。但本質上來講,這是他還沒有遇見真正的“痛苦”,所以他也不會愿意去思考如何改變,更不會有行動。
2、缺少認知
精益源于豐田,傳到中國也有近30年。要說這個時間也不短,但仍然有很多人不了解精益,甚至有絕大多數(shù)人根本沒有聽說過精益。比如在零售行業(yè)、服務行業(yè)、金融和互聯(lián)網(wǎng),因為豐田精益的應用更廣泛在于制造領域。
所以,很多老板不了解精益也很正常,這是精益?zhèn)鞑バ枰訌姷牡胤?,需要更多精益的愛好者和實踐者不斷來傳播這么好的東西。起碼在我來看,精益的思想和理念無處不可用,最重要的是它成體系、很落地,這是很多管理體系欠缺的,同時也是企業(yè)最關注的。
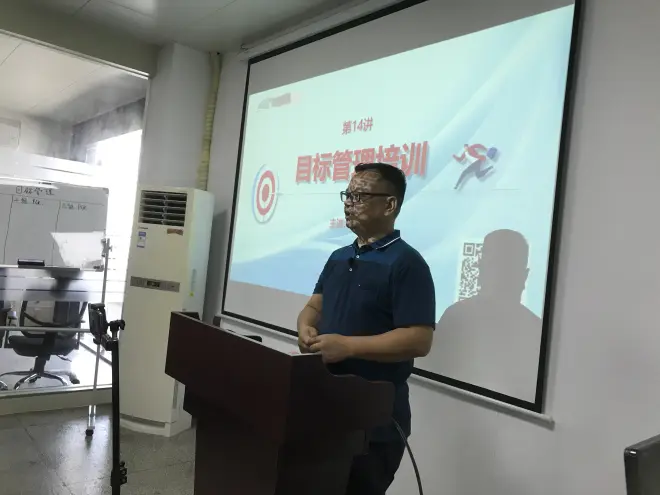
對于少部分企業(yè)老板,他們知道精益的重要性,也想推精益,但沒有找到合適的人。不管是企業(yè)內(nèi)部還是企業(yè)外部,合適的精益變革者很關鍵。關鍵在于讓精益推行達到效果,真正改善企業(yè)的QCD(質量、成本、交期),真正解決企業(yè)的核心問題。
所以,多數(shù)企業(yè)老板會選擇尋覓精益人才,或者請外部專業(yè)的精益咨詢機構(如服裝精益智能制造俱樂部)來幫助企業(yè)。這里不得不提的是,內(nèi)部推行精益和外部精益咨詢有一個本質的區(qū)別在于角度和立場會完全不一樣。
內(nèi)部精益更多只看到自己身上局部的問題,外部咨詢則會看到整個鏈條上的問題,這就是身在其中和站在外部的不同視角。就拿每個人來講,你對自己看得見的部位很清楚有沒有問題,比如臉、手和腳,但你對自己看不見的地方就必須去醫(yī)院診斷檢查,比如我們的五脹六腑。
那如果拒絕精益生產(chǎn),企業(yè)會出現(xiàn)哪些問題?說白了,一個企業(yè)如果不經(jīng)過精益的洗禮和重塑,就會有生存的壓力,也一定會面臨發(fā)展的挑戰(zhàn),因為企業(yè)已經(jīng)病入膏肓了。
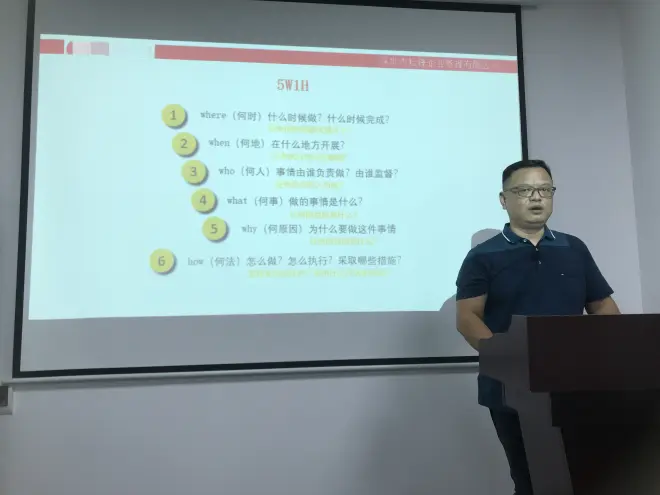
外傷是可以直接看到的疤痕或傷口。企業(yè)的材料、工具、人員隨意擺放,整個現(xiàn)場凌亂不堪,安全、質量沒有保障,效率低下,士氣低落。這樣的企業(yè),客戶一看就沒信心,股東一看就不想合作,員工一看就不想加入。這是企業(yè)一眼就能看出來的創(chuàng)傷。
根治方法并不復雜,就是精益5S,可視化,換場景換人物。讓現(xiàn)場耳目一新,讓員工方便,讓客戶滿意。
5、內(nèi)傷
既然是內(nèi)傷,那就是我們一眼看不出來的內(nèi)傷。你需要透過現(xiàn)象看本質,即使是專業(yè)的老師也能現(xiàn)場診斷。比如工廠質量問題很多,質量過程不良率高,返工率高,報廢率高,客戶投訴多。比如交貨不及時,可能包括原材料定盤率低,生產(chǎn)計劃達成率低,客戶交貨率低;比如再成本高,包括勞動效率低,設備OEE低,材料成本高等。甚至還有組織架構和企業(yè)文化的問題,這些都是企業(yè)隱形的內(nèi)傷,需要找到根源,根除。
治療內(nèi)傷,可以開出精益藥方,比如布局改善、生產(chǎn)線平衡、看板拉動、單件流、TPM、TQM等。
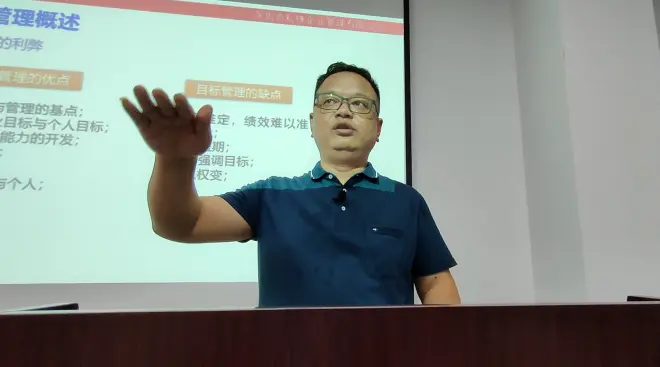
看名字就知道很嚴重,要么影響企業(yè)生存,要么好折騰。比如,由于管理松散粗放,各種浪費嚴重,經(jīng)營成本居高不下,企業(yè)不賺錢甚至虧損。我們做什么呢比如質量問題嚴重,導致大量車輛召回,奶粉違禁成分超標賣不出去。怎么做?比如因為總是出現(xiàn)嚴重的發(fā)貨問題,客戶直接轉到第二家供應商,就沒有訂單了。怎么會?
對于受了重傷的企業(yè),迅速止血,然后包扎傷口進行治療。這時候如果時間不夠,精益只能緩解,上帝也很難拯救。
就像一個人平時不運動不保養(yǎng),小病不重視,大病不治療。當他病重時,他用一生來挽救他的生命。就算是大醫(yī)院,好專家,也來不及回天。
對于很多服裝企業(yè)老板來講,精益生產(chǎn)是個棘手的存在,尤其中小服裝企業(yè)更加突出。當然,萬事皆有其緣由,如果我們細細分析下就會發(fā)現(xiàn),大多民營企業(yè)老板都是白手起家,甚至是從一線慢慢上來,最后積累了一定的技術和資源,加上一身膽識就創(chuàng)業(yè)了,所以,他們對精益生產(chǎn)的認識是不夠的,所以也就出現(xiàn)了以下問題:
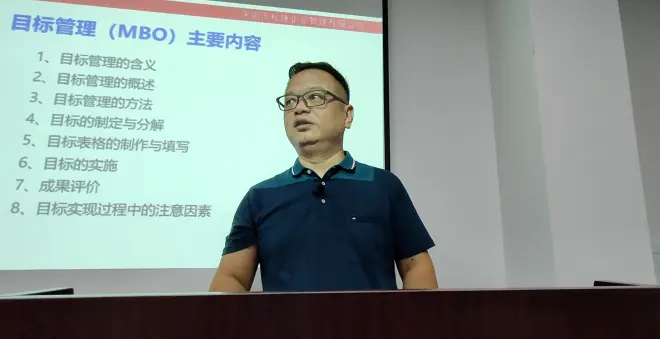
多數(shù)民營企業(yè)的精益改善確實是點對點的改善,相當缺乏系統(tǒng)。在今天的課堂上,很多小伙伴也提到自己企業(yè)里面的改善,都是某個部門在推,并非全員參與,甚至老板都未參與,這樣的精益推行注定失敗,甚至可以說是勞命傷財,還不如不搞。
比如設備部門來推個TPM,生產(chǎn)部門搞個5S,質量部門來個TQM,都是自己搞得鬧熱,并沒有真正解決問題,也沒有真正帶來價值,最后都只能偃旗息鼓。
8、人才培養(yǎng)不夠重視
說到人才培養(yǎng),不得不又拿豐田舉例,豐田推崇“造車先育人”。我在廣汽工作多年,對隔壁的電裝和豐田都有不少了解,在人才招聘和培養(yǎng)上,它們是認真的。多數(shù)是校招,從學校招過來直接培養(yǎng),1年,2年,3年,就這樣不斷給他們培訓、鍛煉,很多一線員工也送到日本總部工廠培訓學習,工廠內(nèi)部還有很多的改善活動,甚至全球比拼......這才是在“育人”,這也真實體現(xiàn)了“以人為本”的核心文化,你也可以對比下自己的企業(yè)。
很多民營企業(yè)不重視人才培養(yǎng)的原因在于,老板認為底下的員工就那點水平,很難提高,不想投入時間和金錢。但我想說,企業(yè)的成長是源于員工成長的紅利,當一個企業(yè)的員工沒有成長,老板也不幫助員工成長,那么企業(yè)面臨的最大瓶頸一定是管理,包含生產(chǎn)管理、供應鏈管理、質量管理、設備管理、工程管理等等一切管理,而這些管理直接決定了企業(yè)運營的QCD(即質量、成本、交期)水平。