芯片產業(yè)鏈系列8半導體材料-半導體基體材料
我們已經通過一系列文章對芯片產業(yè)鏈的橫向環(huán)節(jié)和縱向支撐環(huán)節(jié)進行了介紹。接下來我們將介紹芯片產業(yè)鏈最后一個支撐環(huán)節(jié),即半導體材料。半導體材料雖然在晶圓廠成本中占比較小,但對生產的工藝及良率均起到重要影響,為晶圓制造工藝中不可或缺的原材料,其種類翻多,屬于耗材類產品。作為上游支撐環(huán)節(jié),半導體材料與半導體設備類似,基于芯片產業(yè)鏈制造與封測環(huán)節(jié),通常情況下可被分為制造材料與封裝材料兩類。半導體制造材料是基礎制備材料,細分領域眾多,2021年全球市場規(guī)模為404億美元,其中硅片占比最大(36%) 貫穿制造環(huán)節(jié),其次是電子特氣和掩膜版實現對半導體IC的清洗、蝕刻與氧化。半導體封裝材料的使用貫穿于封測流程始終,存在諸多細分產品,2021年全球市場規(guī)模為239億美元,其中封裝基板占比最大(40%)。
? ? ? ? ?
? ? ? ? ?
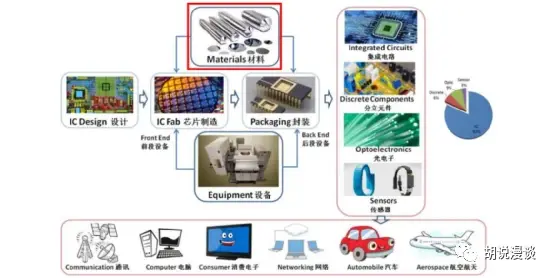
? ? ? ? ?
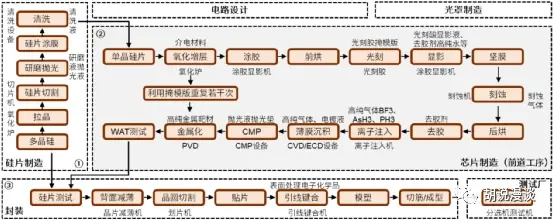
? ? ? ? ?
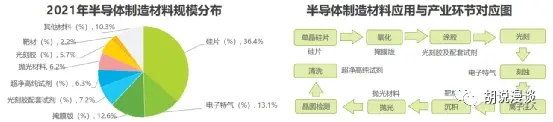
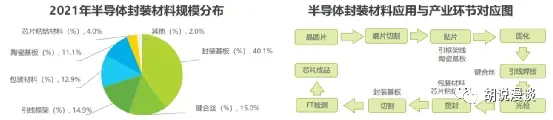
考慮到硅片的重要性以及第三代半導體材料發(fā)展如火如荼,在本文中我們采取更詳細的分法,將半導體制造材料分為基體材料、工藝材料,因此我們將分三個篇章介紹半導體材料,即基體材料、工藝材料和封裝材料。三種材料相輔相成缺一不可,其中基體材料(硅片等)為晶圓基底材料。工藝材料中,掩膜版用于光刻工藝底板;光刻膠用于將掩膜版上的圖案轉移到硅片上;靶材與薄膜工藝前驅體用于薄膜沉積;電子特氣用于氧化/還原/除雜;濕電子化學品用于清洗/刻蝕;拋光材料用于實現平坦化。封裝材料中,封裝基板與引線框架用于保護、支撐芯片及建立芯片與PCB間的連接;鍵合絲用于連接芯片和引線框架;粘合材料用于芯片貼片;陶瓷封裝體用于絕緣打包等。本篇章作為起手篇,我們首先梳理、介紹半導體基體材料。
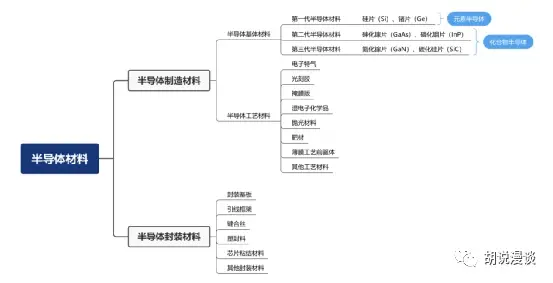
半導體基體材料可以說是參與了從制造到封測的所有流程,是集成電路制造中最為基礎的原材料。在半導體系列4-半導體行業(yè)研究:從分類開始我們講到半導體按照材料組分可分為第一代、第二代、第三代半導體,半導體基體材料則是由這些半導體材料制成的晶片(有時也稱襯底),是半導體器件的主要載體。具體地,第一代半導體基體包括硅片、鍺片;第二代半導體基體主要為砷化鎵片、磷化銦片;第三代半導體基體主要為氮化鎵片、碳化硅片。
接下來我們將對它們做一個簡單的梳理,在此之前我們認為有必要介紹一下三代半導體基體材料的發(fā)展階段和主要區(qū)別。從發(fā)展階段來看,半導體基體材料發(fā)展至今經歷了三個階段:
1、第一階段(代表材料:Si,Ge):20世紀50年代開始,以硅(Si)、鍺(Ge)為代表的第一代半導體材料制成的二極管和晶體管取代了電子管,引發(fā)以集成電路為核心的微電子產業(yè)的迅速發(fā)展,主要應用于低壓、低頻、低功率的部分功率器件、集成電路中,并廣泛應用于手機、電腦、平板、可穿戴、電視、航空航天以及新能源車、光伏等產業(yè)。
2、第二階段(代表材料:GaAs,InP):20世紀90年代開始,隨著半導體產業(yè)的發(fā)展,硅材料的物理瓶頸日益突出,以砷化鎵(GaAs)、磷化銦(InP)、銻化銦(InSb)、部分三元化合物半導體等為代表的第二代化合物半導體材料嶄露頭角。第二代半導體材料主要用于制作高速、高頻、大功率以及發(fā)光電子器件,是制作高性能微波、毫米波器件及發(fā)光器件的優(yōu)良材料,廣泛應用于衛(wèi)星通訊、移動通訊、光通信和GPS導航等領域,代表材料砷化鎵和磷化銦。
3、第三階段(代表材料:SiC、GaN):近年來,以碳化硅(SiC)、氮化鎵(GaN)、氧化鋅(ZnO)、金剛石、氮化鋁(AlN)為代表的寬禁帶(禁帶寬度大于 2.2eV)第三代半導體材料逐漸興起,其介電常數、導熱率及最高工作溫度等等關鍵參數方面具有顯著優(yōu)勢,可以滿足電力電子技術對高溫、高功率、高壓、高頻及抗輻射等惡劣工作條件的新要求。代表材料為碳化硅和氮化鎵,主要應用于電力電子、光電子、射頻電子等領域。
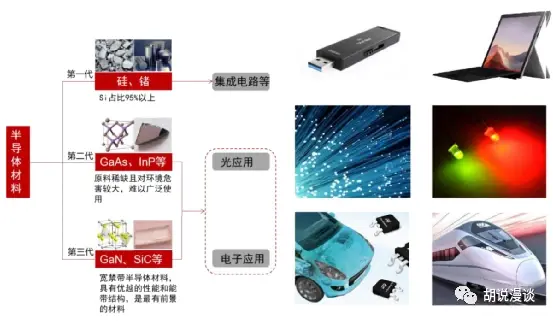
從三代半導體的區(qū)別來看,其物理性質決定了其主要區(qū)別和應用領域。如下表所示,由于第二代、第三代半導體的電子遷移率、飽和電子速度較高,因此適用于高頻應用。同時第三代半導體的禁帶寬度更高,這就使得其有更高的絕緣擊穿場強。以SiC為例,其絕緣擊穿場強是Si的10倍,因此與Si器件相比,能夠以更高的摻雜濃度并且膜厚更薄的漂移層制作出600V~數千V的高壓功率器件。
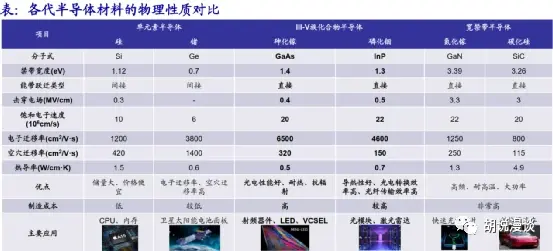
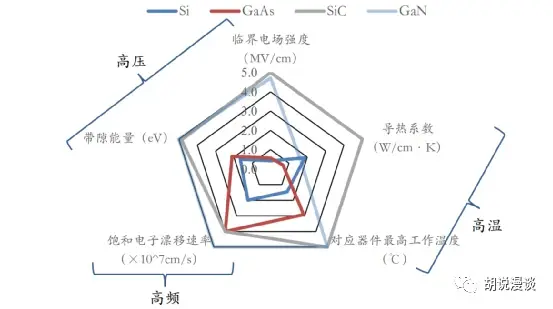
總之,晶圓材料經歷了60余年的技術演進和產業(yè)發(fā)展,形成了當今以硅為主、新型半導體材料為補充的產業(yè)局面。Si的物理性質限制了其在光電子和高頻、高功率器件上的應用,于是發(fā)展出了SiC、GaN 等化合物半導體滿足了電子技術對高溫、高功率、高壓、高頻以及抗輻射等惡劣條件的新要求?;衔锇雽w多用于射頻器件、光電器件、功率器件等制造,具有很大發(fā)展?jié)摿?;硅器件則多用于邏輯器件、存儲器等,相互之間具有不可替代性質。
硅的儲量豐富、成本低、具經濟規(guī)模,且在8寸及以上晶圓中,Si相比第三代半導體材料更為成熟、可靠性更高。此外,第三代半導體材料的寬禁帶、耐高溫高壓、開關頻率高優(yōu)勢在邏輯芯片上并不突出(寬禁帶的優(yōu)勢在于功率而非速度,使用硅材料才可做高速)。因此二者在未來很長一段時間中, 仍會根據各自特性不同,以共存的形式存在。目前硅片仍將維持主流半導體材料的地位。從半導體器件產值來看,全球95%以上的半導體器件采用硅作為襯底材料。
? ? ? ? ?
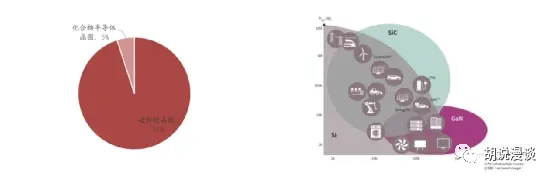
另一方面,在兩代化合物半導體材料中,GaAs、InP等化合材料的原料稀缺,需通過合成形成,價格相對較高,并且材料本身有毒,以及可能造成環(huán)境污染,使得其難以被更廣泛應用,局限性較大,逐漸被第三代半導體材料取代。根據 Yole 數據顯示,第三代半導體滲透率逐年上升,SiC滲透率在2023年有望達到3.75%,GaN滲透率在2023年達到1.0%,第三代半導體滲透率總計4.75%。
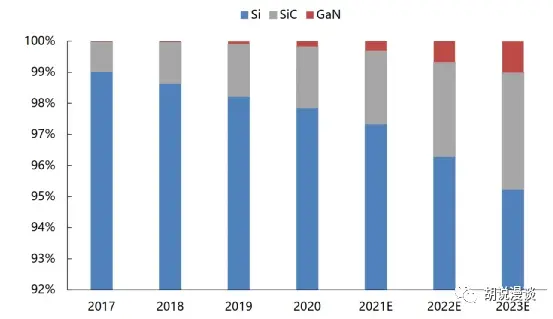
主要半導體材料滲透率及預測
1、第一代半導體材料:主要包括硅片和鍺片。
(1)硅片:主流基體材料。
硅片主要應用于半導體和光伏領域,其中半導體硅片的制造技術要求更高,下游應用也更廣泛,市場價值也更高。半導體和光伏領域使用的硅片差異主要體現在類型、純度和表現性質上。從類型來看,半導體硅片均為單晶硅結構,而光伏硅片多晶硅和單晶硅結構都有(目前單晶硅也已逐漸占據主流)。從純度來看,半導體硅片的純度要求達9N以上(99.9999999%),區(qū)熔單晶硅片純度要求在11N(99.999999999%)以上,而光伏硅片對純度要求較低,在6N( 99.9999%)以上。從表面性質來看,半導體硅片表面的平整度、光滑度以及潔凈程度要比光伏硅片高,需要經過后續(xù)的研磨倒角、拋光、清洗等環(huán)節(jié)。因此半導體硅片較光伏硅片的加工難度更高、附加值也更高。
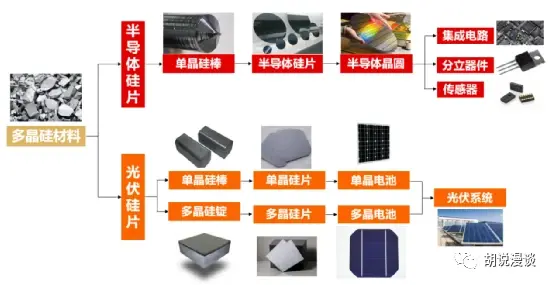
我們在芯片產業(yè)鏈系列3-超級長文解析芯片制造全流程中已簡要介紹過硅片的制造流程,即單晶生長和后端加工(切片、倒角、研磨等)。在此我們補充一下單晶生長即拉單晶的內容。拉晶工藝是硅片制作核心工藝之一,主要流程為將電子級高純度多晶硅拉制成單晶硅錠,單晶生長技術的重點在于保證拉制出的硅錠保持高純度水平的同時,有效控制晶體缺陷的密度,單晶的生長過程決定了硅材料的直徑、晶向、摻雜導電類型、電阻率范圍及分布、氧碳濃度、少子壽命、晶格缺陷等技術參數。單晶的生長方法主要可分為直拉法和區(qū)熔法兩種。
直拉法(CZ法)是當今制備單晶硅的主流技術,市場占比約為85%,且12英寸硅片只能用直拉法生產,適用于邏輯、存儲芯片的制造。直拉法的制備在單晶爐中進行,主要流程是在石英坩堝中放入多晶硅,在高純惰性氣體的保護下加熱熔化,再將單晶硅籽晶插入熔體表面,待籽晶與熔體找尋到熔化點后,隨著籽晶的提拉晶體逐漸生長形成單晶硅棒。晶體的摻雜也是通過直接在坩堝中加入摻雜劑,使摻雜元素在拉制單晶的過程中直接溶入單晶之中。直拉法優(yōu)點是工藝成熟,更容易得到大直徑的單晶硅棒、設備簡單、可大規(guī)模生產;缺點則是由于在長晶過程中使用到坩堝,會形成碳和氧雜質,導致純度低、電阻率不均勻。
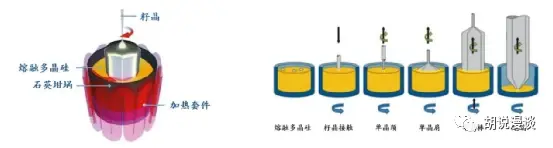
區(qū)區(qū)熔法制作的硅片主要用于功率器件的制備,適用于8英寸及以下的硅片制作。區(qū)熔法制備單晶硅在區(qū)熔爐中進行,具體流程如下:首先在真空或稀有氣體環(huán)境下的爐室中, 利用電場給多晶硅棒加熱,直至被加熱區(qū)域的多晶硅融化,形成熔融區(qū);而后用籽晶接觸熔融區(qū)融化;最后使多晶硅上的熔融區(qū)不斷上移,同時籽晶緩慢旋轉并向下拉伸,逐漸形成單晶硅棒。區(qū)熔法中不使用石英坩堝,避免了很多污染源,但由于其工藝繁瑣,生產成本較高,難以大規(guī)模生產。
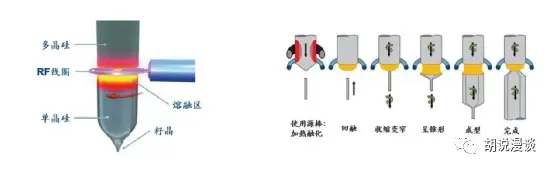
拉單晶之后再經過一系列的后端加工工藝就可以得到基礎的硅片產品了。從耗材端來看,硅片生產所需主要原材料包括多晶硅、石墨制品、石英制品、切磨耗材、包裝耗材、化學試劑、氣體、拋光耗材、備品備件等。參考滬硅產業(yè)及立昂微披露的數據,其中多晶硅占比最高,約占總成本的20%~30%,石英坩鍋約占10%~15%,拋光耗材成本占比10%~15%,包裝材料占5%~20%不等。
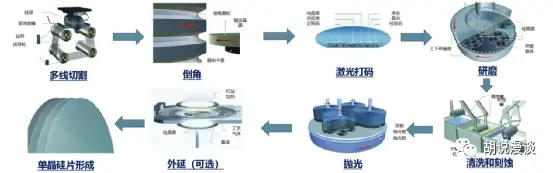
硅片的種類較多,不同種類的硅片應用領域也不同。具體來說,硅片可以根據工藝、應用場景、摻雜程度、尺寸等進行分類。
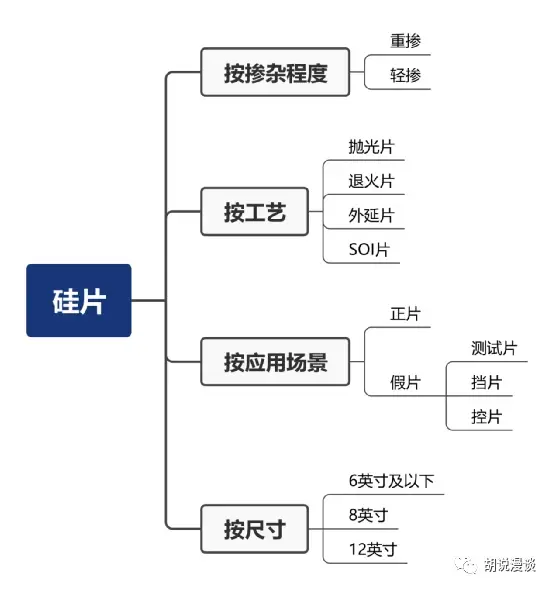
根據摻雜濃度,硅片可以分為重摻和輕摻。一般而言摻雜元素量越大,電阻率也越低。重摻硅片的摻雜元素摻入量大,電阻率低,在保證器件反向擊穿電壓的同時又能有效降低器件的正向功耗,一般用于模擬器件、功率器件等領域產品;輕摻硅片摻雜濃度低,通過生長高質量的外延層,可以提高CMOS柵氧化層完整性、改善溝道漏電、提高集成電路可靠性,一般用于集成電路領域,技術難度和產品質量要求更高。由于集成電路在全球半導體市場中占比超過80%,全球對輕摻硅片需求更大。
根據工藝,硅片可分為拋光片(Polish Wafer)、退火片(Anneal Wafer)、外延片(Epitaxy Wafer)、SOI(Silicon-On-Insulator,絕緣體上硅),其中最基礎和常見的種類為拋光片,占比達到70%,退火片,外延片和SOI硅片則是經對拋光片的二次加工而來。SOI硅片價格遠高于同尺寸外延片和拋光片,8英寸外延片主要是功率器件用重摻外延片,外延層較厚,相比拋光片價格更高。12英寸的外延片的外延層較薄,通常在3um以內,主要用于改善硅片的表面性能,價格是同尺寸拋光片的1.2倍左右。
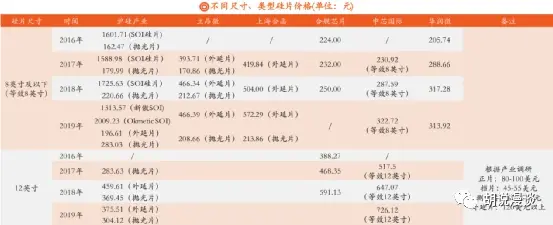
具體地,拋光片是經過邊緣或雙面拋光形成的具有原子級平坦度的硅片,8寸拋光片主要用于邏輯芯片、傳感器,12寸拋光片主要應用于NAND、DRAM等存儲器領域。退火片是將拋光片置于氫氣或氬氣中,進行升溫、降溫過程制得,可以消除氧對硅片電阻率影響,提高芯片良率,主要用于高性能CMOS工藝中。外延片是拋光片經外延生長后形成,外延層能夠在低阻襯底上形成高電阻層,并提供與襯底晶圓不同的物理特性,8寸外延片主要用于PMIC、功率芯片、CIS等,12寸外延片主要用于MPU、CIS、邏輯芯片等。
SOI硅片則是一種三明治結構的硅片,底層拋光片經氧化、鍵合或離子注入等工藝處理后形成,通過在頂層硅和支撐襯底之間加入一層氧化物絕緣埋層(又稱BOX)。BOX使得硅片可實現IC中元器件的介質隔離,大幅減少寄生電容以及漏電現象,主要用于射頻前端芯片、功率器件、傳感器及硅光子器件等。
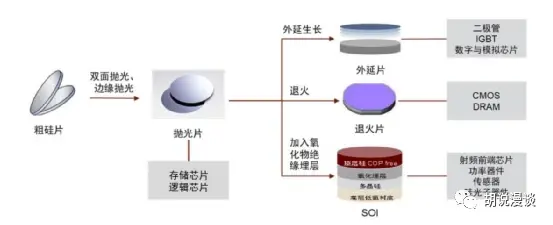
根據應用場景,硅片可分為正片,假片(又稱陪片)。其中正片指的是用于正式生產的、最終形成晶圓成品的硅片,一般使用單晶硅棒中間較好的部分來制作。正片具體又包括拋光片、外延片、退火片、SOI片等。假片則用來暖機、填充空缺、測試生產設備的工藝狀態(tài)或某一工藝的質量狀況,一般由晶棒兩側品質較差部分切割而來。假片按功能又可分為測試片(Test Wafer)、擋片(Dummy Wafer)和控片(Monitor Wafer)。一般而言,假片占正片的比例在10%左右。
測試片主要用于實驗及檢查等用途,也用于制造設備投入使用初期以提高設備穩(wěn)定性;擋片用于新產線調試以及晶圓生產控制中對正片的保護;控片多用于正式生產前對新工藝測試、監(jiān)控良率,同時為監(jiān)控正式生產過程中的工藝精度及良率,需要在晶圓正片生產過程中插入控片增加監(jiān)控頻率。另外,部分擋控片可重復使用。由于擋控片作為輔助生產使用且用量巨大,晶圓廠通常會回收用過的擋片,經研磨拋光,重復使用數次;而控片則需具體情況具體對待,用在某些特殊制程的控片無法回收使用,可以回收重復利用的擋控片又被稱為可再生硅片(Reclaimed Wafer)。
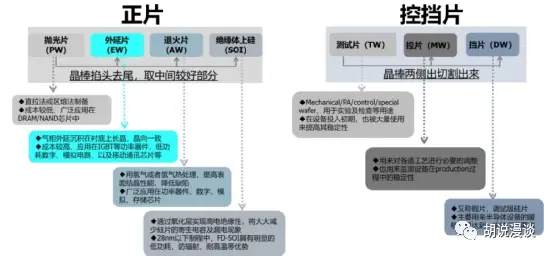
按照尺寸分類, 半導體硅片的尺寸(以直徑計算)主要包括23mm、25mm、28mm、50mm(2英寸)、75mm(3英寸)、100mm(4英寸)、125mm(5英寸)、150mm(6英寸)、200mm(8英寸)與300mm(12英寸)等規(guī)格。自 1960 年生產出 23mm 的硅片之后, 硅片尺寸就越來越大,到2002年已經可以量產300mm(12英寸)硅片,厚度則達到了歷史新高775μm。簡單起見,我們將之劃分為6英寸及以下,8英寸及12英寸三類。
? ? ? ? ?
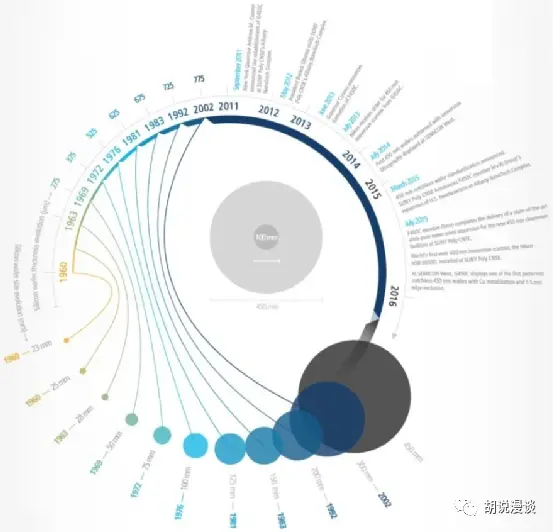
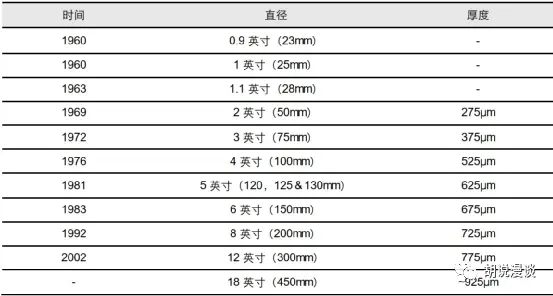
硅片尺寸的擴大和芯片制程的減小是集成電路行業(yè)技術進步的兩條主線。由于硅片尺寸越大,單位面積產出的芯片數量也會隨之增加,如8英寸到12英寸,直徑增加了1.5倍,產出面積增加了2.64倍,分攤的生產成本、設備廠房等固定資產后單位面積生產成本更低,硅片邊緣的損失也越少,在同等工藝條件下,尺寸越大的硅片可使用率越高,因此單位成本也會降低。
不同尺寸硅片下游應用也有所不同,12英寸硅片主要應用于邏輯芯片及存儲器中,如MCU、ROM、Nand Flash、SoC等,尤其是28nm制程以下芯片;8英寸則主要用于功率器件及特色工藝產品,如MOSFET/SBD、傳感器、電源管理芯片、指紋識別芯片等。由于 8 英寸產線建廠時間較早,產線基本已折舊完畢,且技術較為成熟,在部分制程要求不高的芯片上成本較低,而 12 英寸對代工企業(yè)廠房潔凈室及設備的設計精密度要求都較高,初期投資及后續(xù)研發(fā)投入較大,因此一般用于制造難度較高的邏輯芯片。
根據SEMI統(tǒng)計,2020年12英寸硅片占比約67.2%,8英寸硅片占比25.5%,6英寸及以下占比7.3%,12英寸硅片為更大尺寸(18 英寸,450mm)商業(yè)化量產前的主流應用。
從市場規(guī)模來看,伴隨5G、物聯(lián)網、新能源汽車、人工智能等新興領域的高速成長,社會含硅量快速提升。2021年全球硅片出貨量總計141.65億平方英寸(MSI),YoY+14%,市場規(guī)模達126億美元,YOY+13%,受益于下游晶圓廠擴建帶來的產能增長,硅片行業(yè)需求持續(xù)保持旺盛,2022年SEMI預計全球硅片出貨量達146.94億平方英寸(MSI),YoY+4.8%,2023年受到整體需求下滑所致,預計環(huán)比略有下滑,2024~2025年保持持續(xù)增長。出貨量機構方面,截至4Q22 8寸硅片出貨量達約600萬片/月,12寸硅片出貨量達約800萬片/月,SUMCO預計至2026年有望超1000萬片/月需求量,CAGR達8%。
從競爭格局來看,全球硅片市場高度集中,日本企業(yè)一直在半導體硅片領域處于領先地位,信越化學(Shin-Etsu)和勝高(Sumco)合計市場份額超過50%。2016年12月,環(huán)球晶圓(Global Wafers)以6.83億美元收購當時排名全球第四的美國SunEdison Semiconductor (SEMI)。收購案完成后,環(huán)球晶圓成為中國臺灣最大、全球第三大的半導體硅片供應商。SK Siltron與存儲大廠海力士同屬SK集團, 隨著存儲市場的快速發(fā)展市場,SK Siltron占有率持續(xù)提升。截至2021年,硅片市場仍由海外公司所占據,根據Omdia統(tǒng)計,信越化學、SUMCO、環(huán)球晶圓、德國世創(chuàng)及SK Siltron合計占據約95%以上的市場,市場集中度較高,由于2021年開始半導體景氣度上行,海外硅片公司均做出擴產規(guī)劃,并計劃于2023~2025年分別投產。
? ? ? ? ?
(2)鍺片:初始基體材料。
鍺片是制作半導體器件,紅外光學器件的材料,是初始的半導體基體材料。半導體材料最初以鍺為主,世界上第一只晶體管就是由鍺材料制成,但由于硅在自然界的儲量非常豐富、價格更低,且鍺基半導體雖然電子能級更好,導電性能更強,但熱導能力較弱,發(fā)熱現象較為明顯,所以硅片成為了第一代半導體材料的核心。全球鍺的資源比較貧乏,全球已探明的鍺保有儲量僅為8600金屬噸,且非常分散,是一種典型的稀有分散元素。鍺資源在全球分布非常集中,主要分布在中國、美國和俄羅斯,其中鍺資源分布最多的國家是美國,保有儲量3870噸,占全球含量的45%,其次是中國占全球41%
鍺產業(yè)鏈包括上游的資源提煉、中游的提純和深加工以及下游紅外、光纖等方面的高端應用。鍺具備多方面的特殊性質,在半導體、航空航天測控、核物理探測、光纖通訊、紅外光學、太陽能電池、化學催化劑、生物醫(yī)學等領域都有廣泛而重要的應用。在電子工業(yè)中,在合金預處理中,在光學工業(yè)上,還可以作為催化劑,是一種重要的戰(zhàn)略資源。
鍺片在半導體行業(yè)中是一種重要的材料。它被用于制造高速電子器件和光電器件,如高純度鍺晶片用于太陽能電池和紅外探測器的制造。具體來說,鍺器件二極管、晶體三極管及復合晶體管等,鍺光電器件等,廣泛用于彩電、電腦、電話及高頻設備中。此外,鍺管特別適用于高頻大功率器件中,且在強輻射與-40℃下可正常運轉。
太陽能鍺晶片
2、第二代半導體材料:主要包括砷化鎵片和磷化銦片。
在進行砷化鎵片和磷化銦片之前,對第二代半導體的產業(yè)鏈進行一個概覽是有必要的。與第一代半導體類似,二代半導體產業(yè)鏈包括上游的襯底制造、外延加工,以及中游的IC設計、制造、封測和下游應用等環(huán)節(jié)。其中砷化鎵襯底材料主要由Freiberger、Sumitomo等行業(yè)龍頭供應,磷化銦村底材料則由Sumitomo、日本JX等供應;外延加工市場則是由IQE、全新光電等少數寡頭占據,但一些IDM廠商自己也生產外延片;中游的IC設計、制造、封測等環(huán)節(jié),存在IDM和代工兩種主流模式;下游應用包括射頻、光電子、LED和光伏等板塊。
(1)砷化鎵片:按工藝可分為襯底和外延(根據電阻的不同,襯底又可以進一步分為半導體型和半絕緣型),按尺寸分可以分為4英寸及以下、6英寸、8英寸晶片。
砷化鎵產業(yè)鏈最上游為砷化鎵晶體生長和襯底生產加工環(huán)節(jié)。襯底是外延層半導體材料生長的基礎,在芯片中起到承載和固定的關鍵作用。生產砷化鎵襯底的原材料包括金屬鎵、砷等,先通過人工合成砷化鎵多晶,再利用生長技術制備砷化鎵單晶,最終經過切割、磨邊、研磨、拋光、清洗等工藝得到砷化鎵襯底,整個過程生產設備主要涉及晶體生長爐、研磨機、拋光機、切割機、檢測與測試設備等。
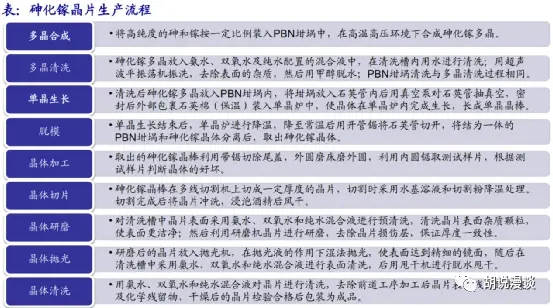
多晶合成和單晶生長是襯底制備過程中的核心技術。由于自然界中不存在天然的砷化鎵多晶,因此首先需要通過人工合成制備多晶。單晶生長方面,從20世紀50年代開始,就已經開發(fā)出多種砷化鎵單晶生長方法,目前主流的工業(yè)化生長工藝包括液封直拉法 (Liquid Encapsulated Czochralski,LEC)、水平布里奇曼法 (Horizontal?Bridgman,HB)、垂直布里奇曼法 (Vertical Bridgman,VB)以及垂直梯度凝固法 (Vertical Gradient Freeze,VGF) 等。

砷化鎵襯底可進一步分為半絕緣型和半導體型。較純砷化鎵晶體中摻入VI族元素Te、Se、S等或IV族元素Si,可獲得N型半導體; 摻入II族元素Be、Zn等可制得P型半導體; 摻入Cr或提高純度可制成高電阻率的半絕緣材料。半絕緣型砷化鎵襯底主要用于高頻通信器件, 半導體型則主要應用與LED和VCSEL(垂直腔面發(fā)射激光器)等光電子器件。
與硅片類似,砷化鎵襯底材料的發(fā)展趨勢是大尺寸化,尺寸越大,在單片村底上可制造的芯片數量越多,襯底邊緣的損失也會越小,有利于進一步降低芯片的成本。砷化鎵襯底向大直徑發(fā)展的同時,單晶體的生長長度也需要不斷提升。根據北京通美招股書,目前全球砷化鎵襯底以4-6英寸為主流直徑,但Freiberger等龍頭襯底廠商均已具備8英寸襯底生產能力。
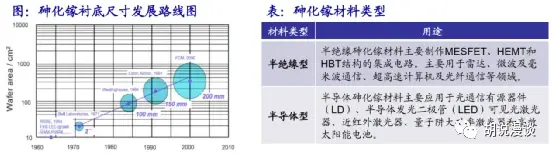
從市場規(guī)模來看,根據Yole數據,2019年全球折合二英寸砷化鎵襯底市場銷量約為2000萬片,預計到2025年將超3500萬片,2019-2025年CAGR為9.72%;2019年全球砷化鎵襯底市場規(guī)模約為2億美元,預計到2025年將達3.48億美元,2019-2025年CAGR為9.67%。分應用來看,2025年全球射頻器件砷化鎵襯底(折合二英寸) 的銷量和規(guī)模將達965.70萬片、9800萬美元;LED器件襯底(折合二英寸) 的銷量和規(guī)模將達1333.80萬片、9600萬美元;激光器確化襯底(折合二英寸) 的銷量和規(guī)模將達330.30萬片、6100萬美元。
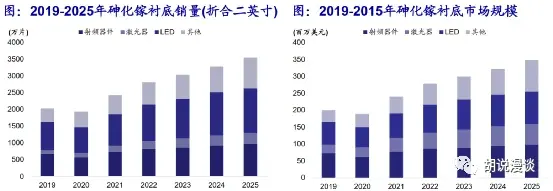
從競爭格局來看,全球砷化鎵襯底市場集中度較高。根據Yole數據,2019年全球砷化鎵襯底市場主要生產商包括Freiberger、Sumitomo和北京通美,其中Freiberger市占率為28%、Sumitomo為21%、北京通美為13%。
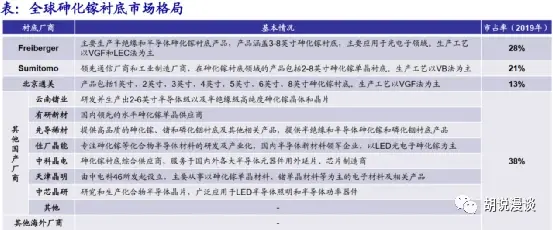
砷化鎵外延片是產業(yè)鏈的關鍵材料。器件制作在外延層上為正外延,若器件制作在襯底上則稱為反外延,此時外延層只起支撐作用。外延生長的新單晶層可在導電類型、電阻率等方面與襯底不同,還可以生長不同厚度和不同要求的多層單晶,從而大大提高器件設計的靈活性和器件的性能。外延制備有MOCVD和MBE(Molecular Beam Epitaxy,分子束外延法)兩種方法。MOCVD成長薄膜時,主要將載流氣體通過有機金屬反應源的容器時,將反應源的飽和蒸氣帶至反應腔中與其它反應氣體混合,然后在被加熱的襯底上面發(fā)生化學反應促成薄膜的成長。MBE成長條件則透過元素加熱方式,借由超高真空環(huán)境的腔體,將所需外延元素加熱升華形成分子束,當分子束接觸村底后,就可形成所需外延結構。
從量產速率看,MOCVD速度較MBE快1.5倍 (MBE需時間加熱形成分子束);但以外延質量來說,由于MBE可精準控制分子束外延成長,因此質量更好。
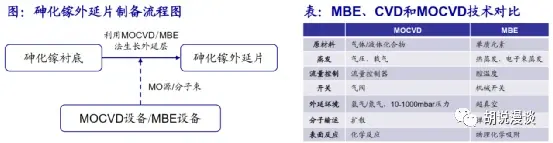
從市場規(guī)???,根據前瞻產業(yè)研究院數據,2018年全球GaAs外延片市場規(guī)模為11億美元,GaAs外延IDM廠商多采用MOCVD工藝,廣泛應用于數通、功率和LED等領域。
從競爭格局看,頭部外延廠商中IQE、全新光電、Hitachi Cable多采用MOCVD法;MBE技術生成的外延材料質量好,但生長的速度較慢,全球僅有IQE和英特磊兩家專業(yè)外延代工廠采用此工藝 (IQE掌握MOCVD和MBE兩種制程技術)。分應用市場來看,GaAs射頻市場約90%采用外延生產外包模式,2019年IQE和全新光電合計占據市場份額80%以上;LED市場幾乎由IDM廠商Osram、三安光電、晶元光電、乾照光電等占據;光電子市場商業(yè)模式取決于應用:數據通信市場主要由Finisar、Avago、IVI等IDM廠商主導,智能手機3D傳感和VCSEL市場則以外包為主,2019年IQE在光電子市場市場份額仍達61%。
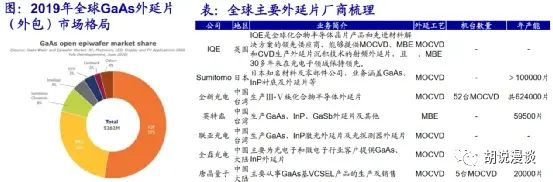
(2)磷化銦片:同樣可按工藝分為襯底和外延(襯底可進一步分為半導體型和半絕緣型),按尺寸可分為2英寸、3英寸、4英寸、6英寸晶片。
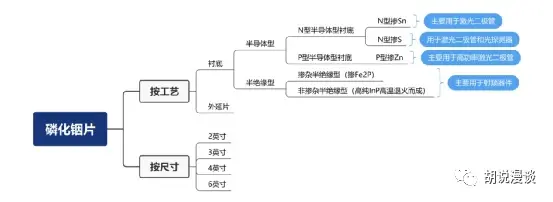
與砷化鎵襯底類似,磷化銦襯底生產也需要經過多晶合成、單晶生長后再經過切割、磨邊、研磨、拋光、清洗等多道工藝后真空封裝成品,其中多晶合成、單晶晶體生長是核心工藝。在多晶合成方面,自然界中不存在天然的磷化銦多晶,因此需要通過人工合成制備磷化銦多晶,將兩種高純度的單質元素按一定比例裝入PBN坩堝中,在高溫高壓環(huán)境下合成磷化銦多晶;合成方法主要有水平梯度凝固法 (Horizontal Gradient Freezing,HGF)、水平布里奇曼法 (HB)、溶質擴散法 (Synthesis Solute Diffusiod,SSD)和直接合成法(In-situ Synthesis)等。目前,改進后的HB/HGF法是工業(yè)合成InP多晶的主要方法。
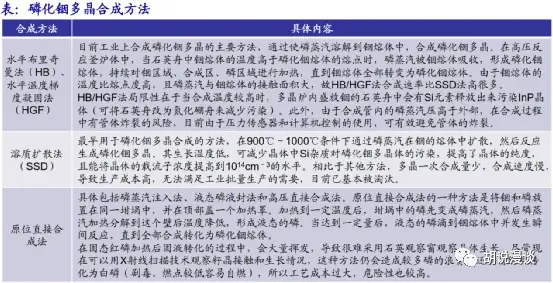
在單晶生長方面,磷化銦的單晶生長方法分為兩大類:?垂直生長和水平生長,目前主要的生長方法包括液封直拉法?(LEC)、改進LEC法、HB法和HGF法、VGF法和VB法,其制備技術存在較高壁壘。
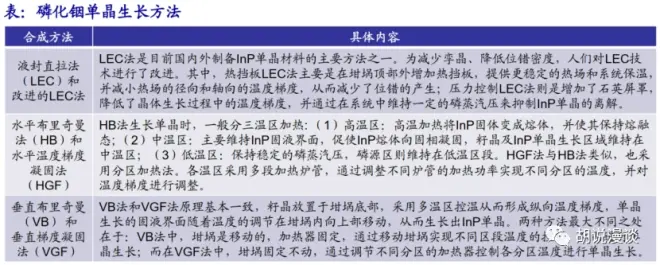
按導電性能,InP襯底可進一步分為半導體型和半絕緣型。半導體型又分為N型和P型,N型襯底通常選用Sn和In2S3作為摻雜劑,P型襯底則選用ZnP2作為摻雜劑。各種摻雜劑的使用,目的是為器件制造提供不同導電類型的襯底。其中,N型摻Sn的InP主要用于激光二極管,N型摻S的InP用于激光二極管和光探測器,P型摻Zn的lnP主要用于高功率激光二極管。半絕緣型按是否摻雜分為摻雜半絕緣襯底和非摻雜半絕緣村底,摻雜半絕緣襯底通常采用Fe2P作為摻雜劑而非摻雜半絕緣襯底是將高純InP單晶襯底通過高溫退火而成,主要用于制作射頻器件。
按晶片尺寸,為了降低成本,InP單晶的總體發(fā)展趨勢是向大尺寸、低位錯、工業(yè)化大規(guī)模生產發(fā)展。目前,其主流尺寸是2-4英寸,最大商用尺寸是6英寸。根據北京通美招股書,Sumitomo和北京通美分別使用VB和VGF技術可以生長出直徑6英寸的InP單晶,日本JX使用LEC技術可以生長出直徑4英寸的InP單晶。
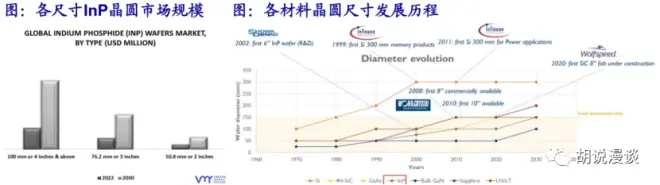
按市場規(guī)模來看,根據Yole數據,2026年全球磷化銦村底市場預計銷量為128.19萬片(折合二英寸)?,2019-2026年CAGR為14.40%;2026年全球磷化鋼村底市場預計規(guī)模為2.02億美元,2019-2026年CAGR為12.42%。分應用來看,2026年全球光模塊器件磷化銦村底(折合二英寸)?的銷量和規(guī)模將達100.03萬片、1.57億美元;傳感器件磷化銦襯底(折合二英寸)的銷量和規(guī)模將達20.54萬片、3200萬美元;射頻器件碎化鋼村底(折合二英寸)的銷量和規(guī)模預計約為7.63萬片、1300萬美元。
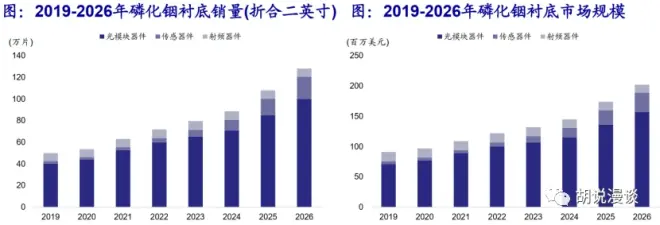
按競爭格局來看,全球磷化銦襯底市場集中度高。目前主要供應商包括Sumitomo、日太JX、法國InPact、英國WaferTech等。根據Yole數據,2020年全球前三大廣商占據磷化鋼襯底市場90%以上的市場份額,Sumitomo、北京通美、日本JX分別占比42%、36%、13%。
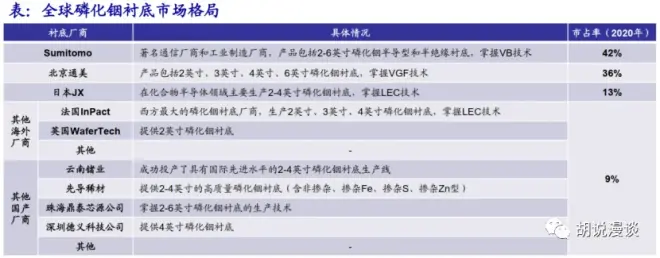
對于不同的材料和應用,外延技術主要包括MBE、MOCVD、氫化物氣相外延(Hydride Vapor Phase Epitaxy,HVPE)和液相外延(Liquid-Phase Epitaxy,LPE)等。液相外延、氯化物氣相外延和氫化物氣相外延因簡便快速而適合厚層外延,但在多層、多元組分、摻雜、界面質量等方面具有很大的局限性,MOCVD和MBE方法可實現厚度、組分、摻雜和界面的精確控制,是磷化銦外延的主要方法。
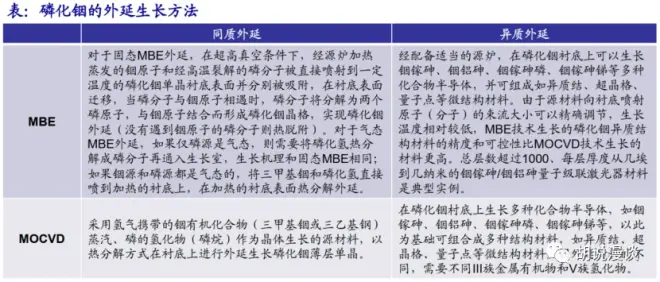
從市場規(guī)模來看,根據恒州博智QYR百家號數據,2021年全球磷化銦外延片市場銷售額為1.04億美元,預計2028年將達到1.62億美元,年復合增長率為6.30%。
從競爭格局來看,磷化銦外延片市場集中。全球磷化鋼外延片主要有兩種來源:一種是大型的IDM制造商,包括美國II-VI、Lumentum、Broadcom和日本Sumitomo、Mitsubishi等公司;另外一種是專業(yè)的外延廠,包括中國臺灣聯(lián)亞光電、全新光電、英特磊以及英國IQE等公司,根據Yole,2020年聯(lián)亞光電占磷化銦外延片市場份額約67%。我國大陸磷化銦外延片廠包括全磊光電、華興激光等。此外,長光華芯、仕佳光子、源杰科技、中科光芯等IDM公司也具備自主磷化銦外延生長能力。
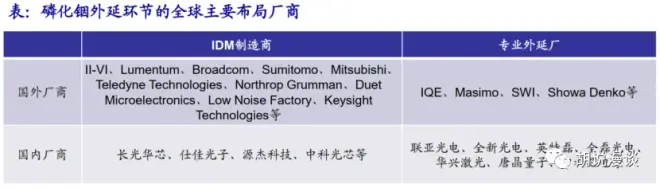
3、第三代半導體材料:主要包括碳化硅片和氮化鎵片。
在具體介紹碳化硅片和氮化鎵片之前,我們同樣首先對兩者的產業(yè)鏈進行一個概覽,這樣比較有利于我們后續(xù)的理解。與二代半導體材料類似,碳化硅和氮化鎵的產業(yè)鏈同樣包含襯底、外延、設計、制造和IDM。產業(yè)鏈整體上看,SiC的商用更成熟,GaN市場則處于起步階段。
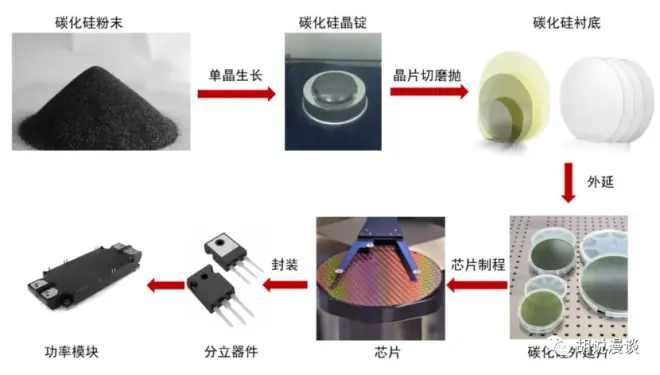
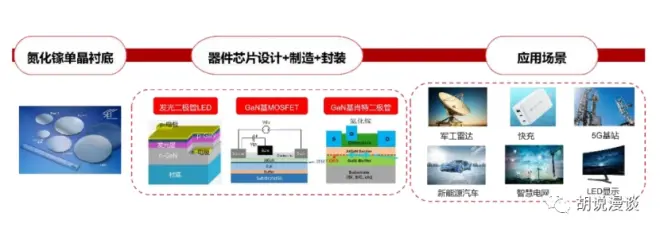
(1)碳化硅片:按工藝可分為襯底和外延(根據電阻率的不同,襯底又可以進一步分為導電型和半絕緣型),按尺寸分可以分為4英、6英寸、8英寸晶片。
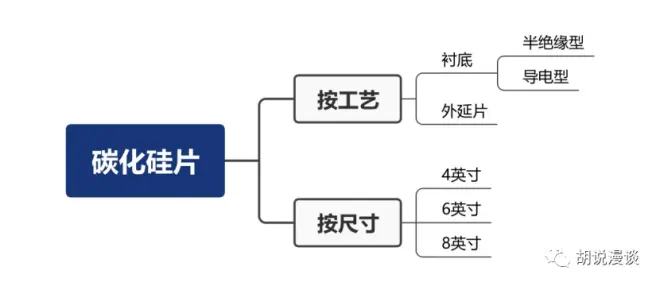
從最上游的碳粉、硅粉制備成碳化硅圓晶,在進行外延,最后制備成?SBD、?MOSFET、?IGBT?等器件,碳化硅襯底及外延是整個環(huán)節(jié)最關鍵的一環(huán)。他決定著上游原材料制備的方式及相關參數,同時也決定著下游器件的性能。與二代半導體晶片相似,碳化硅片的生產過程同樣包括了多晶合成、單晶生長以及后端加工的步驟。
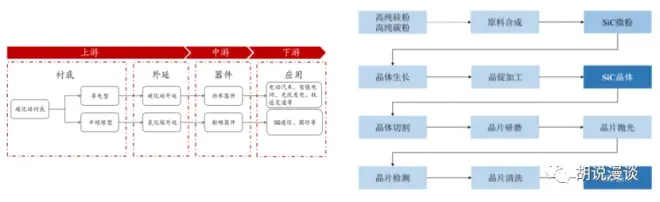
在晶體生長和晶體加工環(huán)節(jié)均存在技術難點。晶體生長環(huán)節(jié),條件控制嚴、長晶速度慢和晶型要求高為主要技術難點。碳化硅晶體的生長溫度在?2300°C?以上,對溫度和壓力的控制要求高;此外,碳化硅有250多種同分異構體,其中4H-SiC為主流,因此需要嚴格控制硅碳比、生長溫度梯度及氣流氣壓等參數才能生長出理想晶體。晶體生長主要有物理氣相傳輸法(PVT)、高溫化學氣相沉積法(HT-CVD)、頂部籽晶溶液生長法(TSSG法)等,其中PVT法是現階段商業(yè)化生長SiC襯底的主流方法,技術成熟度最高、工程化應用最廣。
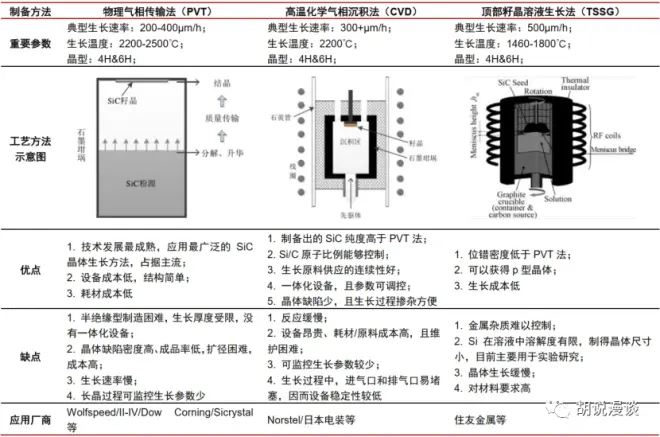
與二代半導體所不同的是,碳化硅長晶速度緩慢。同時由于碳化硅晶體高硬、高脆、耐磨性好、化學性質極其穩(wěn)定,使得襯底加工非常困難,碳化硅襯底的加工過程(主要分為切片、薄化和拋光)中的切片和薄化為主要技術難點,加工難度更高。此外碳化硅的缺陷密度相較二代半導體也更大,這都是碳化硅成本的居高不下的原因。
根據電阻率,襯底可以進一步細分為導電型和半絕緣型兩大類。不同于傳統(tǒng)硅基器件,碳化硅器件不可直接制作于襯底上,需先使用化學氣相沉積法在襯底表面生成所需薄膜材料,即形成外延片,再進一步制成器件。其中,導電型襯底即在碳化硅襯底上生長碳化硅外延層,適用于做功率器件,下游應用包括新能源車、光伏發(fā)電等。半絕緣型襯底即在碳化硅襯底上生長氮化硅外延層,適用于射頻器件,下游應用包括5G通信、衛(wèi)星等。
從尺寸來看,對于降低成本,主要有擴大晶圓尺寸、改進碳化硅長晶工藝及改進切片工藝等三個方向。根據Wolfspeed最新資料,從6寸轉向8寸晶圓,碳化硅芯片數量有望從448顆增加到845顆,增加了75%。8英寸SiC襯底的基面和螺紋螺釘密度分別為684cm-2和289cm-2。化學機械拋光后,表面質量得到改善,有66個缺陷。碳化硅外延可以實現略高于1%的厚度和摻雜均勻性。根據GTAT公司的預估,相對于6寸晶圓平臺,預計8寸襯底的引入將使整體碳化硅器件成本降低20-35%。而且,6寸SiC晶體厚度為350微米,而最初投放市場的8寸SiC襯底厚度為500微米。盡管晶體成本會略微上漲,但是由于更厚的晶體可以切除更多的襯底片,預計也有望進一步降低器件生產成本。
從市場規(guī)模來看,根據Yole數據,2020年半絕緣型SiC襯底市場規(guī)模為10.62億美元,預計2025年將增長至28.39億美元,CAGR約21.7%。2020年導電型SiC襯底市場規(guī)模為7.31億美元,預計2025年將增長至44.67億美元,CAGR約43.6%。由于目前襯底制備的成本較高,襯底在SiC晶圓中價值量最高,據TrendForce數據,在6寸SiC晶圓中,襯底價值量最高,占比達到46%;外延占比23%,芯片器件22%,封測9%。
從市場格局來看,市場集中度高,兩類襯底CR3均高達90%以上。半絕緣型SiC襯底市場集中度CR3為98%,Wolfspeed、II-VI、山東天岳三足鼎立;導電型SiC襯底市場集中度CR3為90%,其中Wolfspeed(原名Cree公司)占比超50%。國外廠商在兩類襯底市場中均占有主要份額,國內廠商在半絕緣襯底全球市場具有一定優(yōu)勢,但在導電型襯底全球市場占比較小。半絕緣型襯底市場中山東天岳占比30%;導電型天科合達和山東天岳占比1.7%和0.5%。
(2)氮化鎵片:同樣可根據工藝分為襯底和外延,也可根據尺寸分為2-4英寸、6英寸、8英寸晶片。
GaN產業(yè)范疇大致包括GaN單晶襯底(以GaN、SiC、Si、藍寶石為襯底)、GaN?材料外延、器件設計以及器件制造。國內氮化鎵企業(yè)以IDM模式為主,充分挖掘行業(yè)技術潛力,且有條件率先實驗并推行新技術。隨著行業(yè)規(guī)模不斷拓展, 設計與制造環(huán)節(jié)已經開始出現分工,如傳統(tǒng)硅晶圓代工廠臺積電已經開始提供GaN制程的代工服務。
氮化鎵產業(yè)鏈上游主要包括襯底與外延片的制備。?在GaN器件中,襯底的選擇對于器件性能起關鍵作用,襯底也占據了大部分成本,因而襯底是GaN器件降低成本的突破口。由于GaN單晶襯底生長尺寸受限,通常在異質襯底(藍寶石、SiC和Si)上生長外延片。目前GaN器件主要采用藍寶石、SiC、Si等襯底,但外延層GaN和異質襯底之間存在晶格失配和熱失配問題,效率降低,研究者們正著力突破GaN單晶襯底的制備技術。
目前GaN單晶襯底以2-4英寸為主,4英寸已實現商用,6英寸樣本正開發(fā)。GaN體單晶襯底的主要方法有HVPE、氨熱法,以及助熔劑法。HVPE方法生長速率快、易得到大尺寸晶體,是目前商業(yè)上提供氮化鎵單晶襯底的主要方法;其缺點是成本高、晶體位錯密度高、曲率半徑小以及會造成環(huán)境污染。氨熱法生長技術結晶質量高,可以在多個籽晶上生長,易規(guī)?;a,可以顯著降低成本;缺點是生長壓力較高,生長速率低。助熔劑法生長條件相對溫和,對生長裝備要求低,可以生長出大尺寸的氮化鎵單晶;其缺點是易于自發(fā)成核形成多晶,難以生長出較厚的氮化鎵晶體。
GaN外延片方面,由于GaN的熔點很高,且飽和蒸汽壓較高,在自然界中無法以單晶形式存在,必須采用外延法進行制備。MOCVD、MBE、HVPE等是比較傳統(tǒng)的GaN薄膜制備方法。因此GaN基本是以外延片形式存在的。從市場規(guī)模來看,2021年全球氮化鎵(GaN)外延片市場銷售額達到了4.2億美元,預計2028年將達到15億美元,年復合增長率為21.2%。
從競爭格局來看,GaN襯底市場主要由日本廠商主導。據半導體產業(yè)網,2020年住友電工、三菱化學、住友化學等三家日商合計占據GaN襯底市場份額超過85%。GaN外延片市場中,歐、美、日廠商占據領先位置。據QYResearch,2020年全球GaN外延片市場CR5為53%,核心廠商包括NTT AT、Wolfspeed、住友化學、EpiGaN(Soitec)等。
至此我們已經把半導體材料中價值量最大的一環(huán)硅片,以及化合物半導體材料都進行了簡單的梳理。下次我們將繼續(xù)介紹半導體的工藝材料,讓我們下次再見吧。
? ? ? ? ?