從事后解決變事前預防——自工序完結
自工程完結的衍生是從豐田佐吉翁所開發(fā)的G型自動織機開始的,豐田G型自動紡織機實現(xiàn)了自動檢測功能,當紡織機出現(xiàn)短線的情況,紡織機會自動停止,當時豐田的理念就是只生產(chǎn)合格的產(chǎn)品,而且在不需要檢測的情況下制造出合格的產(chǎn)品。當時的自動化只解決了影響質量的設備因素,不能實現(xiàn)真正在不需要檢測的的情況下,制造出合格的產(chǎn)品,但是自工序完結的理念已經(jīng)形成了一顆種子。
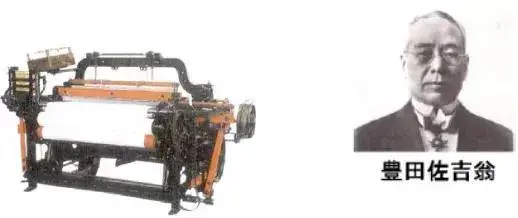
產(chǎn)品檢測對于產(chǎn)品本身而言沒有任何附加價值,它只是確保產(chǎn)品是否符合要求,如果我們能夠確保產(chǎn)品滿足所有要求,那就可以不需要檢測這項作業(yè)。只有每一個參加產(chǎn)品生產(chǎn)的員工都能保證自己的作業(yè)是合格的,才能保證產(chǎn)品合格。
基于這個理念,1962年豐田汽車內部下達了“在工序內創(chuàng)造品質”指定,并傳遞給公司的每一位員工,標志著自工序完結的理念的誕生。自工序完結就是自己做到工序完結,自己判斷工作的好壞,不制造不良品,不流出不良品到后工序。
自工序完結的優(yōu)勢
—1—
實現(xiàn)零檢測
自工序完結是一種全新的質量管理方法,整個質量管理方法從最原始的沒有質量管理意識,對于產(chǎn)品只有最終的質量檢測,發(fā)展到開始有質量管理意識,不斷增加檢測點,通過細分的節(jié)點來管理產(chǎn)品質量,這種方式只能防止不良品流出,不能從根本上解決問題,不生產(chǎn)出不良品。然而,自工序完結是從只生產(chǎn)合格產(chǎn)品入手,徹底顛覆了以往的質量管理模式,最終接近零檢測的目標。
—2—
降低成本
原來的檢測是防止不良品的流出,事后解決這種模式存在三大成本:第一是生產(chǎn)不良品的材料成本、人工成本、設備等成本。第二是檢測所花費的人工成本。第三是發(fā)現(xiàn)問題后的對策成本,自工序完結屬于事前問題預防,不會產(chǎn)生這三大成本,只需要事前分析和對策的成本,故可以在穩(wěn)定產(chǎn)品質量的同時,幫助企業(yè)降低生產(chǎn)成本。
—3—
員工技能提升
目前的質量管理方法是質量部門制定檢測項目和檢測標準,然后由相關的檢驗人員對產(chǎn)品進行檢測。作業(yè)人員一直處于被動檢查的狀態(tài)。使用自工序完結的理念,生產(chǎn)作業(yè)人員可以化被動變主動,積極理解整個工序和自己負責工序的良品條件,通過設定自己工序內的良品確認條件,改善自己工序內的作業(yè)狀況,一方面可以降低工序的不良品率,同時可以提升自己對工序的理解和自身技能,帶動員工的積極性。
—4—
實現(xiàn)改善,沉淀改善文化
自工序完結概念里,每一位員工都是自己工序的負責人,為了實現(xiàn)自己工序不生產(chǎn)不良品,每位員工都需要積極參與自主改善,形成公司的持續(xù)改善體系,最終構建成公司的持續(xù)改善文化。
以往的質量管理側重于事后檢測,通過檢測來防止不良品的流出,由于采用的是節(jié)點檢測,在此之前經(jīng)歷了較多的作業(yè)工序,會造成很多不必要的返工返修,也增加了找出不良品產(chǎn)生的原因的難度,降低了問題解決的效率。
然而自工序完結更注重事前工序的分解,通過對良品條件和作業(yè)標準不斷完善,讓每道工序中影響品質的因素處于受控,最終確保工序的產(chǎn)品品質滿足顧客需求。自工序完結把質量管理從防止不良品流出,轉變?yōu)榭刂屏计飞a(chǎn),從源頭杜絕不良品的產(chǎn)生。