萃余液除油方法和萃余液回收鎳鈷
背景技術:
萃取法富集和提純鎳(鈷)一般是在萃取之前先將萃取劑(主要為磷酸酯類萃取劑,如2-乙基己基磷酸單-2-乙基己酯)P507/P204等,用磺化煤油等溶劑稀釋[1],然后用氨水和液堿等堿性溶液皂化,皂化后有機相用于萃取。萃取反應結束后,通過機械澄清獲得水相和富鈷有機相,萃余液(水相)成分多為鈉鹽或銨鹽,通常進行蒸發(fā)結晶制備鹽類產(chǎn)品;富鈷有機相用酸液反萃,獲得空白有機相和富鈷水相??瞻子袡C相返回萃取工藝;富鈷水相主要成分為硫酸鎳(鈷)或氯化鎳(鈷),用于生產(chǎn)三元鋰電池前驅(qū)體材料、金屬鎳(鈷)以及其他鎳鈷產(chǎn)品。
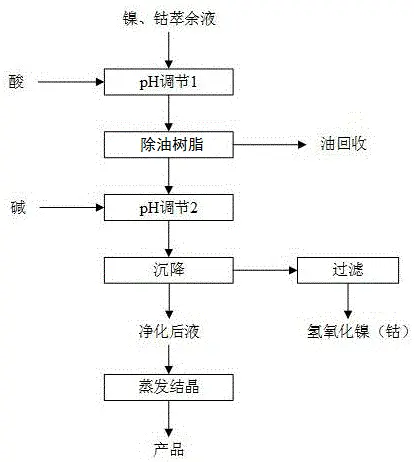
在工業(yè)實際生產(chǎn)中,鎳、鈷萃取率很難達到100%,萃余液中往往會殘留少量未被萃取的游離鎳(鈷)離子,另外,由于鎳(鈷)金屬萃合物溶解度等原因,萃余液中還會攜帶一部分以金屬萃合物形式存在的鎳或鈷,總鎳(鈷)含量在20~100mg/L。這些萃余液中的鎳(鈷)如果不去除,會影響蒸發(fā)結晶的產(chǎn)品純度。
目前大部分企業(yè)是先用杜笙特種離子交換樹脂(CH-90)除鎳或鈷,然后活性炭除油,最后進行蒸發(fā)結晶。因為離子交換無法完全去除以金屬萃合物形式存在的鎳或鈷,活性炭除油也不徹底,出水油含量仍在7mg/L以上,也影響了鎳(鈷)的二次去除。由于鎳(鈷)去除的不徹底,繼而影響了最終產(chǎn)品的純度,也會大大增加蒸發(fā)結晶母液的處理難度。另外,含油的料液進入杜笙特種離子交換樹脂(CH-90),會造成樹脂污染,繼而嚴重縮短了樹脂的使用壽命,投資成本和樹脂折舊成本大大增加。
技術實現(xiàn)要素:
針對上述問題,科海思提供了一種鎳(鈷)萃余液的深度去除鎳、鈷的方法,該方法通過除油樹脂深度除油和沉降相結合,實現(xiàn)了鎳(鈷)萃余液中鎳(鈷)的去除,通過蒸發(fā)結晶得到鎳(鈷)產(chǎn)品,通過過濾得到氫氧化鎳(鈷)產(chǎn)品。
為達此目的,本發(fā)明采用以下技術方案:
一種鎳(鈷)萃余液的深度去除鎳、鈷的方法,將所述廢水進行pH調(diào)節(jié)后,通過除油樹脂深度除油,出水進一步調(diào)節(jié)pH后進行沉降,得到出水凈化后液和沉淀漿液;
所述出水凈化后液經(jīng)蒸發(fā)結晶得到鎳(鈷)產(chǎn)品;
所述沉淀漿液經(jīng)過濾得到氫氧化鎳(鈷)產(chǎn)品。
最終得到的氫氧化鎳(鈷)產(chǎn)品,鎳(鈷)回收率超過99.99%。
出水凈化后液經(jīng)蒸發(fā)結晶得到鎳(鈷)產(chǎn)品,產(chǎn)品純度超過99.95%。
將所述廢水pH調(diào)節(jié)至2~3后,進入樹脂除油。
除油樹脂深度除油出水進一步調(diào)節(jié)pH至7~7.5,出水進入沉降池。
沉降池出水得到凈化后液和沉淀漿液。
調(diào)節(jié)pH用鹽酸溶液或硫酸溶液。
調(diào)節(jié)pH用氨水或氫氧化鈉溶液。
凈化后液Ni(Co)含量小于0.001mg/L。
一種利用上述方法進行處理的廢水為鎳、鈷萃取工藝的鎳、鈷萃余液,其pH為5~7.5,主要成分為氯化銨或氯化鈉或硫酸銨或硫酸鈉,Ni(Co)含量為20~100mg/L,油含量為60~300mg/L。
與現(xiàn)有技術相比,具有以下有益效果:
(1)提供了一種鎳(鈷)萃余液的深度去除鎳、鈷的方法,該方法實現(xiàn)了出水鎳(鈷)含量小于0.001mg/L;
(2)本工藝方法實現(xiàn)了鎳、鈷以氫氧化鎳(鈷)形式回收,回收率超過99.99%;(3)全流程不向系統(tǒng)引入雜質(zhì),產(chǎn)品純度超過99.95%。
科海思作為行業(yè)前沿技術推行者,2011年與美國Thermax集團(Tulsimer)、德國Watch集團合作成為其中國區(qū)總代理,將“特種離子交換樹脂”首次引進國內(nèi),基于國情進行工藝創(chuàng)新,添補行業(yè)空缺,完成技術升級。在推廣實踐中,倡導“環(huán)保治理價值化”新理念,運用國際先進技術在治理的同時進行資源再生,將企業(yè)環(huán)保建設從單純投入轉為開源投資。
主營產(chǎn)品:氨氮吸附樹脂,硝酸鹽吸附樹脂,COD吸附樹脂,除鎳螯合樹脂,除氟樹脂,回收銅螯合樹脂,除磷樹脂,拋光樹脂,除鉻樹脂,除溴酸鹽樹脂,吸附金銀鉑鈀銠貴金屬樹脂,除汞樹脂,除鋁樹脂,除鐵樹脂,除砷樹脂,鉬錸回收樹脂,酸回收樹脂,高鹽除鈣鎂樹脂,德國無鹽軟化濾料,等各種特種離子交換樹脂。