7075鋁合金擠壓棒材表面起泡的原因分析
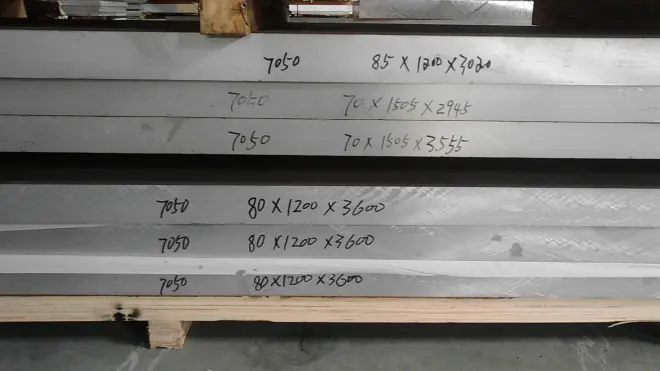
摘要:采用正交試驗對7075鋁合金擠壓棒材表面起泡的原因進行了分析。結果表明:7075鋁合金擠壓棒材表面起泡主要來源于擠壓過程中擠入的氣體和夾雜。另外。固溶熱處理不當會促進表面成層缺陷處產生氣泡。通過優(yōu)化擠壓工藝和模具導流腔設計可消除擠壓棒材的表面起泡,降低固溶加熱爐內水汽含量并采用合理的熱處理工藝可避免淬火后棒材表面起泡。
關鍵詞:7075鋁合金;擠壓棒材;表面起泡;淬火
?
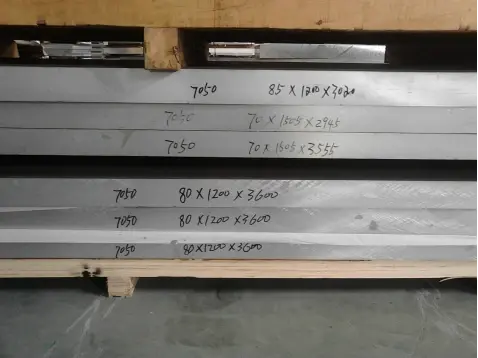
氣泡是高強鋁合金(如7075)擠壓生產中的一個比較常見的缺陷,目前國內外學者對不同擠壓產品表面氣泡的形成有不同觀點,王鳳春將2A14鋁合金棒材表面氣泡分為夾雜氣泡、擠壓分層氣泡和氣體滲透性氣泡三類,認為夾雜氣泡占絕大多數。生產中嚴格控制夾雜物帶入可以防止氣泡的產生。程勇勝等網研究2017鋁合金退火棒材表面起泡的原因時,認為氣泡是起源于成層缺陷的夾雜型表面起泡,合理選擇擠壓工具和模具,提高工模具表面質量可以減少或消除氣泡。PradipKSaha在分析7075薄壁型材氣泡產生的原因時,認為氣泡的形成主要是來自鋁合金內部和外部的氫原子或離子在夾雜物周圍沉淀聚集,形成氫氣泡,熱處理過程能促進氫氣的膨脹,控制合金內、外部氫的來源能夠減少或者消除固溶熱處理過程中形成氣泡的幾率。崔景博等認為成層、高溫氧化或過燒都能引起7A04鋁合金產品起泡.通過分析金相組織可以判定具體的起泡原因。關于7075鋁合金擠壓棒材表面起泡的問題,目前報道較少。本文采用正交試驗的方法,研究不同擠壓工藝參數、模具設計和熱處理工藝對氣泡的影響,找出氣泡形成的工藝因素并提出合理的解決方案,能夠有效避免氣泡的產生,提高棒材成品率。
1、氣泡的形貌和分布
我公司生產的7075鋁合金擠壓棒材。擠壓后出現連續(xù)分布的表面氣泡,主要集中在棒材頭部;淬火后氣泡增多,沿擠壓方向呈連續(xù)分布于整個擠壓長度上。且頭部單位面積氣泡數量比尾部多,大小約1~2mm.其典型照片如圖1所示。
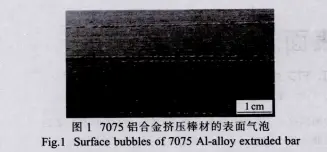
2、試驗方法和結果
在試驗之前,通過初步分析可能導致表面起泡的因素。分別選取了不同的擠壓工藝、模具設計和熱處理工藝進行試驗。所用鑄錠為采用半連續(xù)鑄造法生產的同一批次、同一熱處理爐次的去皮鑄錠,并嚴格控制鑄造前鋁液中H含量低于0.10ml/lO0gAl,其化學成分見表1。根據單位面積表面氣泡的數量和大小。將棒材的表面質量分為l0個等級:1級無氣泡,10級氣泡最嚴重。
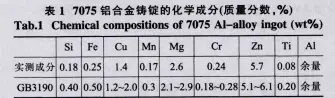
?
2.1擠壓工藝的影響
? 采用正交試驗方法,分析不同的錠筒溫差、壓余長度和鐓粗排氣壓力對φl00mm棒材擠壓后表面起泡的影響。試驗在75MN(φ460mm擠壓筒)正向擠壓機進行,為了減少試驗過程中其他因素引起的噪聲干擾.除了作為變量的三個因素外,其余擠壓參數相同:鑄錠直徑448mill,長度1000mnl,鑄錠頭部溫度410℃,梯度15℃/m,模具溫度430℃,擠壓速度lm/min,擠壓比21,模具采用小導流設計,每組試驗擠壓3根鑄錠。
? 表2為擠壓工藝因素和試驗結果。表2中,鐓粗壓力54MN和27MN對應的擠壓墊所受壓強分別為325MPa和162.5MPa:錠筒溫差=鑄錠頭部溫度一擠壓筒溫度;壓余長度為上一根鑄錠的設定值。
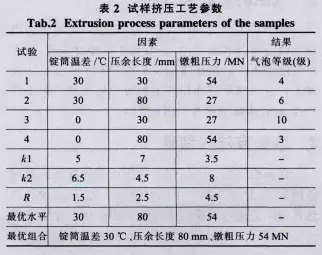
2.2模具設計的影響
? 本試驗同樣在75MN(φ460mm擠壓筒)正向擠壓機進行.模具分別采用大導流、小導流和小導流加防倒槽三種設計方案,模具結構簡圖見圖2,分析不同的模具設計對擠壓后棒材表面起泡的影響。擠壓工藝采用表2中正交試驗結果的最優(yōu)組合,即:錠筒溫差30℃、壓余長度80mm、鐓粗壓力54MN,其余擠壓參數與2.1節(jié)相同,每個試驗擠壓3根棒材,其中22(表3)采用表1中試驗4的結果(條件相同)。
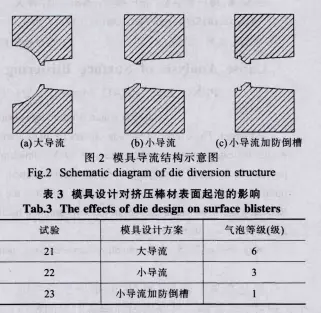
?
?
2.3固溶淬火工藝的影響
本試驗在20m立式淬火爐中進行.采用正交試驗的方法,分析不同加熱溫度、保溫時間和空爐裝料溫度對棒材固溶淬火后表面起泡的影響。試驗樣品采用第22、23號試驗生產的沒有表面起泡的棒材,對淬火樣品進行120℃x24h的人工時效后,用萬能電子試驗機進行拉伸測試。
3分析討論
3.1擠壓工藝的影響
從表2的結果可以看出,擠壓工藝的三個因素對表面氣泡都有影響,其中鐓粗壓力影響最大,其次是壓余長度,錠筒溫差也有一定影響。由于7075鋁合金變形抗力大,如果采用和6XXX系鋁合金同樣的鐓粗壓力(27MN),不足以使金屬完全變形填滿整個擠壓筒,在排氣過程中不能將簡內氣體完全排放,在擠壓過程中氣體被擠入制品表層形成表面氣泡。壓余太短時,接近擠壓終了的金屬紊流階段,金屬死區(qū)的雜質、氧化皮等被擠入制品表面,或被擠入模具內導致擠壓下一根制品時,在制品表面形成成層缺陷,氣體在成層缺陷處聚集形成表面氣泡。筒溫低于錠溫時(錠筒溫差>O),與擠壓筒之間的傳熱效應,鑄錠的內部溫度高于表面溫度,擠壓時鑄錠內部流動性好于表面.表面雜質、氧化皮等不易被擠入模具:當錠筒溫差變小或為負時,鑄錠表面的流動性變好,表面的雜質、氧化皮等容易被擠入模具。但由于擠壓筒內襯的溫度升降速度較慢,在同一批次擠壓過程中改變筒溫對汽泡的影響相對較小。因此,選取合適的鐓粗壓力、壓余長度、錠筒溫度等擠壓參數可以減少或消除擠壓態(tài)棒材的表面氣泡。
3.2模具設計的影響
棒材模具分為有導流和無導流模.有導流模具的優(yōu)點是擠出后棒材連著上一根,可以提高生產效率。但有導流模最大的缺點是上一根鑄錠殘留在導流腔內的金屬,在擠壓時會被擠入下一根產品表面產生成層缺陷,導流越大則缺陷越明顯,因此,減少導流大小可以改善成層缺陷.減少因成層缺陷產生的氣泡。同時,由于7075鋁合金變形抗力大,在切壓余時導流入口上部的金屬容易被拉出而形成空洞(如圖3箭頭所示),在擠壓下一根鑄錠時,空洞處的氣體被擠入下一根產品表面形成氣泡。導流越大則空洞越明顯,在導流入口附近加上一圈防倒槽時.可以減少或避免因切壓余造成空洞引起的棒材表面氣泡。
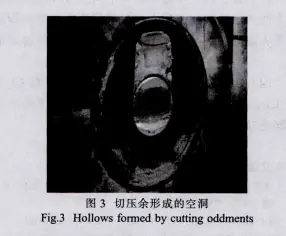
?
3.3固溶淬火工藝的影響
從表4可知,空爐裝料溫度對氣泡影響最大,其次是保溫時間,加熱溫度對氣泡無影響。熱處理過程產生的表面氣泡與鋁合金內部或外部的氫有關,內部的氫為鋁合金在鑄造過程中所吸收,外部的氫為鋁合金在高溫、高濕的環(huán)境下與水分子反應所釋放出。內部的氫在擠壓過程的高壓作用下遷移到成層缺陷的夾雜物內部.外部的氫則以離子或者原子形式擴散到棒材夾雜物周圍沉淀聚集。在熱處理過程中氫離子或原子隨著夾雜物繼續(xù)遷移,當晶格畸變能減到最小時.沉淀聚集的氫原子在夾雜物中重組成氫氣而不能溢出.同時氫氣受熱膨脹.擴大所在夾雜物的空腔而形成表面氣泡。由于在熔鑄過程中嚴格控制了氫含量.因此氫主要來源于外部。爐內濕度越大則越容易反應產生氫,表面氣泡也越嚴重,而熱爐裝料能保證爐內干燥,因此空爐溫度對氣泡影響最大。氫的擴散速度主要受溫度、時間的影響,試驗中兩組溫度相差較小,對氣泡的影響并未體現出來,保溫時間相差較大,對氣泡的影響也相對較大。因此,不合適的固溶處理能夠促進表面成層缺陷處產生氣泡。
?
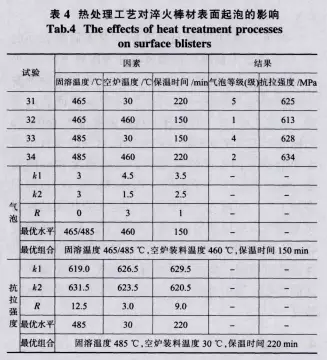
從表4還可看出,對力學性能的影響程度依次為固溶溫度、保溫時間和空爐裝料溫度。在過燒溫度以下保溫溫度越高、保溫時間越長則固溶程度越高,時效后的抗拉強度越大。試驗中的溫度為爐氣溫度,熱爐裝料對應的爐內總時間比冷爐裝料少了爐氣升溫時間,即金屬實際保溫時間變短,因此也對力學性能有一定影響,在實際生產中熱爐裝料時要進行相應的爐氣保溫時間補償。采用熱爐裝料、高溫短時間的固溶淬火工藝可以有效防止表面氣泡的產生。由于當前7075棒材存在的主要矛盾是表面起泡,抗拉強度方面則因性能過剩降為次要矛盾,如果表面氣泡和抗拉強度出現相對立時,可以在標準要求范圍內適當犧牲一定的抗拉強度以保證表面質量。從表4可知,所有試樣的抗拉強度都比560MPa的標準要求高出9.5%~13.2%.而對氣泡和抗拉強度影響最大的因素分別是空爐裝料溫度和固溶溫度,因此,實際生產中應優(yōu)先選擇熱爐裝料、高溫固溶的工藝,而對氣泡和抗拉強度起次要作用的保溫時間則可以相應縮短。即最優(yōu)組合工藝為:固溶溫度485℃,空爐裝料溫度460℃,保溫時間150min,可保證在抗拉強度滿足標準要求的前提下避免表面氣泡的產生,該組合在后續(xù)的批量化生產中也得到了驗證。
4結論
(1)7075鋁合金擠壓棒材的表面氣泡起源于擠壓過程帶入的氣體或雜質.不合適的固溶處理能夠促進表面成層缺陷處產生氣泡。
(2)避免擠壓棒材表面氣泡的關鍵是減少氣體或雜質被擠入。采用小導流加防倒槽的模具設計,同時選取合適的鐓粗壓力、壓余長度、錠筒溫度等擠壓參數可以減少或消除擠壓態(tài)棒材的表面氣泡。
(3)淬火后表面起泡與爐內氣氛和熱處理參數有關,采用熱爐裝料、高溫短時間的固溶淬火工藝可以有效防止表面氣泡的產生。